How to Edit and draw up Warranty General Conditions - Foundation And Concrete Service Online
Read the following instructions to use CocoDoc to start editing and filling in your Warranty General Conditions - Foundation And Concrete Service:
- At first, find the “Get Form” button and tap it.
- Wait until Warranty General Conditions - Foundation And Concrete Service is shown.
- Customize your document by using the toolbar on the top.
- Download your finished form and share it as you needed.
The Easiest Editing Tool for Modifying Warranty General Conditions - Foundation And Concrete Service on Your Way
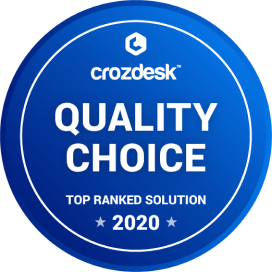
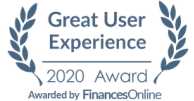
Open Your Warranty General Conditions - Foundation And Concrete Service Right Now
Get FormHow to Edit Your PDF Warranty General Conditions - Foundation And Concrete Service Online
Editing your form online is quite effortless. You don't have to get any software via your computer or phone to use this feature. CocoDoc offers an easy software to edit your document directly through any web browser you use. The entire interface is well-organized.
Follow the step-by-step guide below to eidt your PDF files online:
- Browse CocoDoc official website on your device where you have your file.
- Seek the ‘Edit PDF Online’ icon and tap it.
- Then you will open this free tool page. Just drag and drop the document, or append the file through the ‘Choose File’ option.
- Once the document is uploaded, you can edit it using the toolbar as you needed.
- When the modification is completed, tap the ‘Download’ icon to save the file.
How to Edit Warranty General Conditions - Foundation And Concrete Service on Windows
Windows is the most conventional operating system. However, Windows does not contain any default application that can directly edit document. In this case, you can get CocoDoc's desktop software for Windows, which can help you to work on documents effectively.
All you have to do is follow the steps below:
- Install CocoDoc software from your Windows Store.
- Open the software and then select your PDF document.
- You can also upload the PDF file from Dropbox.
- After that, edit the document as you needed by using the diverse tools on the top.
- Once done, you can now save the finished PDF to your computer. You can also check more details about how to edit on PDF.
How to Edit Warranty General Conditions - Foundation And Concrete Service on Mac
macOS comes with a default feature - Preview, to open PDF files. Although Mac users can view PDF files and even mark text on it, it does not support editing. Through CocoDoc, you can edit your document on Mac instantly.
Follow the effortless guidelines below to start editing:
- To begin with, install CocoDoc desktop app on your Mac computer.
- Then, select your PDF file through the app.
- You can upload the document from any cloud storage, such as Dropbox, Google Drive, or OneDrive.
- Edit, fill and sign your template by utilizing several tools.
- Lastly, download the document to save it on your device.
How to Edit PDF Warranty General Conditions - Foundation And Concrete Service on G Suite
G Suite is a conventional Google's suite of intelligent apps, which is designed to make your workforce more productive and increase collaboration with each other. Integrating CocoDoc's PDF document editor with G Suite can help to accomplish work handily.
Here are the steps to do it:
- Open Google WorkPlace Marketplace on your laptop.
- Look for CocoDoc PDF Editor and get the add-on.
- Upload the document that you want to edit and find CocoDoc PDF Editor by clicking "Open with" in Drive.
- Edit and sign your template using the toolbar.
- Save the finished PDF file on your device.
PDF Editor FAQ
Is a construction manager's responsibilities over once a project is completed? If for some reason the concrete floors were not mixed correctly and started cracking 5 years later, would the crew that made the error have to go back and fix it?
In Texas, there is an implied one-year workmanship warranty on construction jobs you contract out to others. This is a very good reason why you should use a reputable contractor who has an office and about whom you have a reasonable expectation that they will still be able to be found in one year or five.On one occasion, I literally had a woman call me and see if we could come out and give her an estimate on a project. When I got into the problem, she told me that her house was hanging off the edge of the foundation by an inch or two. She had a concrete house slab; on one side, she could measure concrete that was covered by nothing. On the other, she could measure the house hanging out over no concrete foundation. — I was aghast.I told her that such a thing was unheard of, and anything I could do to help her would be ridiculously expensive. Since this had been done recently, she was still covered by the implied workmanship warranty, so why did she not just call the contractor who made the mistake?Her reply: She couldn’t remember his name.Don’t be that customer. Yes, construction contractors have responsibilities that continue on past when the job is finished.Even more than that, reputable contractors will carry commercial general liability (GL) insurance. The standard level of coverage for that is $1,000,000 per inicident/$2,000,000 per policy period (usually a year); the insurance terminology for that is “$1MM/$2MM aggregate”.Imagine a scenario where a construction company carried this GL insurance for the policy period 1/1/2011 to 12/31/2011. It is now the middle of the year 2021, and the construction company went out of business a couple of years ago.Is the insurance company that wrote the company’s 2011 GL insurance policy still liable for mistakes the now-defunct company made in the products and services it sold during the year 2011?You bet they are! — This is why you need to keep your contracts, invoices, plans, payment receipts, and everything else necessary to explain what the contractor did for you; that you were a recipient of their goods and services; and, that you did receive them during the time the company was carrying the GL insurance (which might’ve been just 2011, or it might have been for many years) with the particular insurance company with whom you’re now trying to file a claim.So long as the company did not exhaust its policy maximum (e.g., $2MM) during that policy period, there is a good likelihood that you will be able to recover some or all of your money, plus the money required to fix the problem in 2021, from the now-defunct company’s GL insurance carrier for the year 2011.This prevents you from having to try to find all of these now-broke jokers in order to sue them. If you know how to find the owner(s) or principal(s) of the company/corporation, today, then nothing stops you from suing them; but, if you can stay out of court, you’re better off, because whom the judge decides has to pay the attorneys fees is difficult to predict. All of their personal property may be related to their homestead(s). The company/corporation may have filed for bankruptcy. And, if they carried GL insurance back then, their response to your summons will be, first, to file an insurance claim, which is what I suggested you do to begin with.This is already a long answer, and the issue of the cracking concrete may be just as long. I happen to have worked simultaneously, for half a decade, estimating general construction (contracting) jobs, and being the general manager of a ready-mix concrete plant, so I know how to answer your question, but I’m not sure if I know how to be brief!You have a few distinct scenarios:The general contractor acted as the concrete contractor and owned the ready-mix concrete plant that manufactured and delivered your concrete;The general contractor hired (contracted with) a concrete contractor, and either the general contractor or concrete contractor placed the order for the concrete from the ready-mix plant;You acted as your own general contractor and hired a concrete contractor, who ordered the concrete;You acted as your own general contractor and hired the concrete contractor and called the ready-mix concrete plant and placed the order yourself.I can’t list all the different combinations with any hope of brevity, but you can see the patterns.Concrete that is batched on-demand, just for you, and delivered immediately thereafter based on when you or your contractor specified it would be needed on your job site is known as ready-mix concrete; the plant adds a specific amount of water per “unit” (aka cubic yard [CY]) of concrete, which may be based on instructions given by the customer; or, using experience and the guidelines of the concrete mix design you are using.Water (specifically, the water-to-cement ratio) is very important, and adding too much water is an almost certain way to reduce the end strength of your concrete.Also notice that I’ve made a distinction between concrete and cement. Cement (i.e., Portland cement) is a component of concrete; you do not have “cement floors”; you have concrete floors, sidewalks, driveways, foundations, slabs, etc.Significant cracking in concrete, over time, may be due to improper dirt work and packing of the ground underneath the concrete to be poured. Nice, sandy topsoil is appropriate. Do not build concrete applications on clay. — So, there is a potential person to blame. Who did the dirt work? Was improper dirt work, prior to the concrete pour, the cause of your current problem?Next, water:Did the concrete arrive extremely wet directly from the plant? If so, why? Did you or the contractor order it this way, or did the plant send you super-wet concrete?Did the contractor instruct the concrete mixer truck driver to add too much water on-site? This is common when the concrete contractor did not bring enough men to help pull the concrete into place; watering down the concrete makes the job easier. As I said before, it also significantly reduces the strength you reasonably can expect the concrete to reach in the end (end strength).Was your concrete poured in extreme weather conditions?If concrete is allowed to freeze, then the chemical process that causes concrete to get harder and harder over time — stops.If the ambient temperature is very high, then the exothermic reaction of cement + water, going on inside the mixer drum, added to 100+ degree (F) temperatures outside, may cause water to evaporate too quickly. You are advised to put oscillating water sprinklers (yeah, the kind you use to water your lawn or garden) on the concrete, as soon as it is cured enough to be strong enough to walk on, creating a moisture barrier, which promotes the continued creation of more and more internal crystalline structures, which is what makes concrete so durable and strong. This also reduces the temperature of the still-curing concrete. If it gets too hot, you are likely, as well, to lose end strength.This is why it’s smart to hire experienced concrete contractors, or to hire general contractors who know such people or businesses. You can always call a local concrete plant manager, but the topic is significant enough that civil engineers study it, and you’re not going to be able to get all the information you need from a short phone call — if the company’s executives even allow their operations personnel to give out advice like this.—Make sure that you retain copies of all concrete load tickets for your records. Each load of concrete will come with a load ticket that someone has to sign to prove they received the amount of concrete stated on the ticket, because that’s what the plant will bill them for! These are usually in triplicate or quadruplicate, so the end user (like the homeowner), the general contractor, the concrete contractor, and the concrete plant itself will get a copy for their records.In our modern times, this ticket may show the concrete mix design template and then the actual results of what went into the concrete you were delivered.Some of these tickets give a reference range, set by the plant’s concrete mix designers, for what an allowable range of water to be added on-site should be.What all of these tickets will show is how much water was actually added on-site. That is something filled in by the driver, and the driver (who works for the plant) should be the only person operating the truck's controls that allow additional water to flow into the mixer drum. — Mixer trucks carry about 100 to 150 gallons of extra water with them. The real purpose of this is to allow a driver the water needed to clean off his chutes and the back of the mixer drum after his portion of the concrete pour is finished. Otherwise, he’d be breaking windshields all the way from your job site back to our plant.In reality, customers often need extra water, and we allow them the use of some of the water we carry — as a courtesy. But, some customers will call for 20, or 30, or 50, or 80 gallons of extra water to be added before they even take a first look at what the concrete the plant sent to them looks like already. As I hope I’ve drilled into your heads by now, this is a horrible practice. — When customers/contractors make horrible decisions, we notate that on the concrete load tickets before the customer signs, that way these extraordinary amounts of extra water added show up on all triplicate or quadruplicate copies of the yet-to-be-signed load ticket. So everybody knows it happened.Did the contractors (or you) use the appropriate size and type of rebar, wire re-mesh, or any other form of steel reinforcement?Following these scenarios I’ve presented, you can see that who is liable for concrete’s failure is not obvious.If the plant sent concrete that was extremely wet, you or the contractor should have refused it and sent that truck back to the plant and called the dispatcher and asked for another truck with the correct “wetness” (jargon term: slump) that was requested. — If you don’t, then you take possession of the concrete, and you are then responsible for it. You have absolved the plant of its mistake. Even if it fails, you still have to pay for it.The same thing goes for improper mix designs and inaccurate/imprecise batching of the concrete. This one is more difficult. Sometimes, even for a concrete plant manager, it’s difficult to tell if the concrete someone else batched has something wrong with it. If I could not identify the problem based on visual inspection, then I would have to research any contemporaneous notes or papers, supplier (incoming materials’) load tickets, and the mix design my batch person used. — Still, if you sign that load ticket, then you take possession of the product. This is true if your contractor signs it for you; he or she signs it as your agent.I’m an honest person, and I knew and know much about the manufacture of concrete. Your contractor should know more about how to pour, place, and finish concrete than I do, but when it comes down to the science of it, surely the manufacturer has the trump cards.All I mean by that is that you may have used a bunch of different contractors, or a bunch of different people who work for the same contracting company, but for my part, I’m just coining the same product, the same way, day-in and day-out.While not universally true, your problem likely originated with work your contractor(s) did. Despite that, people always want to blame the concrete plant.I’m not sure who would have to back out and fix your problem after five years, but within this answer, I hope I’ve been comprehensive in describing to you where to look and who to look for.Also remember that hairline cracking is what strong concrete does; that’s the type of concrete you want. An old concrete contractor told me one that, when he was learning his trade, he asked his boss: “What happens if my concrete cracks?”Response: If your concrete doesn’t crack, then I’ll come over with my sledgehammer and put some cracks in it for you.—A good, usually handy way to judge if you have hairline cracking, or something more serious, is to pull out a credit card and see if the edge of that card will fit into the crack. — If it can, then continue investigating what the problem is. If it can’t, then that’s just what concrete does.—If you literally have crumbling concrete, then call a reputable concrete contractor and have him tell you what he thinks is going on. Estimates are free.
What is the terminology used by architects during a home renovation/construction?
There are many more, especially for material names, construction systems, components, but still these are some of the words we use daily:All risk insuranceAgencyAuthority Having Jurisdiction - AHJAgreementAccessibilityArbitrationASTMAwardAddendaBarrierBid BondBidBoring LogBudgetBuilding CodeCertifyConstruction Change DirectiveChange OrderClaimConstruction ManagerCommissioningConstruction DocumentsConstruction AdministrationConcreteCostsConsultantContractDamageDecisionDeliverablesDemolitionDesignDesign-BuildDetailDisputeDeveloperDraftDocumentationDrawingElevationEngineerEntitlementEnvironmentalEquipmentErectionEvaluationExistingExteriorFacilityFast TrackFeesFinal (Inspection)FoundationFormFurnitureFloor AreaGeneral Liability InsuranceGuarantyGuaranteed Maximum PriceHazardous MaterialHVACHold Harmless agreementIndemnificationInformation (Request for)InstallationInsuranceISO 9000JurisdictionKeynotesLaborLEEDLiabilityLicenseLump sumMaintenanceManufacturerMaterialMechanicalMilestoneMobilizationNon binding (agreement)NFPANegociateOccurrence (Basis Insurance)ObservationOSHAOverheadOwnerPass offPaymentPenal ClausePerformance bondPerilPlanPDPP Parallel Design Permitting ProcessPricePrime contractProcurement DocumentsProduct dataProject ManagerProgressProject Delivery MethodProposalPropertyPunch ListQuality AssuranceQuality ControlRated (Fire)Record DocumentsRegulationsRequest for Proposal (RFP)RetainageReviewRFISafetySampleScaleScheduleStructureSchematic DesignScope of workSequencingServicesSetbackStandardSiteShop drawingsSpecificationsSubmittalSubstantial completionSubstitutionSupplementary conditionsSuretySupplierSurveySustainabilityTenantTestingTechnologyToleranceToolsTimeTracking listUnionUtilityUnit priceValue engineeringWarrantiesWaste managementWeldWorkers compensationWorking daysZoning
What is Kya Hota Hai?
Introduction-Weighbridge and its types-A weighbridge or a truck scale is fixed of scale that's used to weigh bulk items. These are electronic pit type or pit less, digital pit type or pit less, rail weighbridge, portable weighbridge, RCC weighbridge, mechanical weighbridges, etc. Each weighbridge is built to last with a rugged design, robust weight sensors, and high-quality manufacturing – all backed by industry-leading warranty options. Weighbridge helps you to calculate the number of products incoming and outgoing in your warehouse. The profit of weighbridges may be higher understood from the perspective of a business in which there's a regular bulk activity of large & heavy goods.Some companies or individual businesses find it difficult to keep a track of the goods that they are sending outwards and the number of goods/raw materials coming their way. Weighbridges help solve this purpose. To keep a track of your business on-goings especially when your business calls for sending & receiving of goods to & fro, weighbridges serve here a great purpose.An electronic weighbridge is a protracted-time period of funding that requires the right assessment and in-depth consideration earlier than making the final buying desire. Cost is an important factor but choosing only on price can divert you to certain problems.Choice - Choosing the appropriate type, size, and capacity of your weighbridge is a significant part of the decision making process. Seeking expert advice can save huge costs, changes, or upgrades in the future.Production of key units - Weighbridge overall performance and long time reliability is related to the exceptional of the key units. The important components are load cells, junction boxes, etc.Cost of Ownership - This may seem like an outdated term but is still very relevant when it comes to weighbridges. The initial low-cost weighbridge solutions will soon turn into expensive problems of replacement, downtime, and unwanted repairs making it important to consider all the important factors.Software and database management - this is any other very essential part of a weighbridge system and maybe a vulnerable point if now not defined sufficient.Type of weighbridgesAbove ground weighbridgesAbove-ground weighbridges are the most not unusual, due to their fee-effectiveness plus. They require the least amount of website online training. However, they do require the maximum floor place. Get right of entry to and go out ramps ought to be at the least 5m in period and the ‘easy-regions’ alongside each element of the weighbridge deck need to be as a minimum a meter.This type of weighbridge can be supplied in a single deck, twin deck, or multi-deck configuration depending on the length of the vehicles that need to be weighed.Semi-pit weighbridgeSemi-pit weighbridges are available standard and custom configurations and can be a multi-deck, dual deck, or unmarried deck, depending on the precise desires. No ramps are required which makes them a value-effective alternative, however, a few civil works are compulsory (excavation, drainage pipes or sumps, etc). Semi-pit weighbridges have sidewalls that act as maintaining partitions and those have to be positioned as a minimum a meter from the facet of the deck. Extra reinforcement of the retaining walls may be required.Custom semi-pit weighbridgeThese weighbridges are generally mounted wherein obstacles are an aspect (width constraints, cutting-edge homes adjacent to one or each factor of the weighbridge, pass roads adjoining to one or each factor). This layout is basically a version of the everyday semi-pit design wherein the adjustments are required to house them scale barriers. Where the width of 1 or both of the aspect partitions is decreased and where get right of entry to a few loading cells is restrained or prevented, access holes need to be installed inside the deck or the aspect wall adjacent to the affected loading cells to facilitate servicing and preservation.In-ground weighbridgeThis type has the smallest footprint of all of the options and is ideal for sites wherein there are mandatory space restrictions. They’re also best for shared weighing and site visitors areas and wherein vehicles are weighed in the course of loading by using forklifts. However, they require great website coaching, excavation, and reinforcing, making them the most highly-priced choice. The weighing floor of absolutely in-ground weighbridges is completely degree with the encircling ground and access to the burden cells is holes in the deck or side of the deck. They're commonly categorized as ‘constrained areas’ and as such, require specialist intervention for preservation and servicing. A couple of deck weighbridge these may be built as above-ground, semi-pit, or absolutely in-floor weighbridges, so they may be definitely extra of a variation of a design than a particular type. The quantity and duration of decks rely upon necessities and decks may be varying lengths. With more than one deck weighbridges, person axles or axle organizations may be weighed simultaneously, making them ideal for use in stations where the number one characteristic is to document axle breakdown weights.Portable weighbridges are a fee-powerful choice, in particular for both non-trade operations and for the one's sites so that it will handiest be used briefly (much less than years). They’re essentially a variant on the design of an above-floor weighbridge and use square concrete slabs for the burden-bearing places and a detachable frame as a rigid guide base for the loading cells and deck. The deck can both be made entirely from metal (the lightweight construction is ideal for relocation purposes) or from the extra common aggregate of metallic and concrete.Cars get access to the deck thru ramps constituted of the earth. If the transportable weighbridge is to be used for exchange purposes, concrete stop walls should be built.Why do we need weighbridge and its Importance-Think about it like this that you are a doctor & run a clinic and your stethoscope doesn’t work or you have a manufacturing unit and one of the machines have stopped working.Similar is the case with a Weighbridge. A weighbridge helps a business to remain informed about the accurate measures of incoming & outgoing goods. However, if there’s some error in the weighbridge, the performance of a weighbridge would highly be affected. There could be imbalances in the incoming & outgoing goods that can further relate to the imbalance in the profits.So, the proper functioning of a weighbridge is highly important for such a business for its successful operation. Although, it is more important to choose a weighbridge wisely because that will decide the viability of it in the longer run.Some of the amazing benefits include cost savings, reduced bottlenecks, improved traffic flow, and improved workplace safety. Maybe you have been wondering about how a weighbridge will improve your business, here are five real reasons for you.The importance of weighbridge to several businesses cannot be over-emphasized. Some of the key reasons why they are significant are listed below.1. Cost savingsIf a vehicle is not fully loaded, it can cost the company a lot of money; that is, part of what should have boosted the company’s revenue will be lost. However, when a weighbridge is used, the space in the vehicle will be used to its optimal level.As you could already understand, overloading speeds up the damage and tear of an automobile and shortens its lifespan. With a weighbridge, overloading can be prevented. Considering the truth that overloaded vehicles and trailers make organizations spend extra on gas and renovation, it way businesses will keep a whole lot of cash with the aid of warding off overloading.2. Compliance penalties and fines-Overloaded cars or trucks are a total waste of money. You don’t want to repay such charges. A weighbridge will ensure that your vehicle is legally compliant particularly with respect to the payloads.3. Safety firstNo person must ever sense risky within the place of business if they are going to paintings optimally. A weighbridge gives drivers a warranty that the vehicle they're coping with is in general compliant and in shape for the purpose for which it is being used. Also, heading off overloading of the vehicle promotes the safety of different street customers and decrease the harm that might be accomplished the road surfaces, overpasses, and bridge.4. Increased productivityProductivity and efficiency are what guarantees a profit in any business. By installing a weighbridge, the vehicles will be optimally loaded at all times. Therefore, you won’t waste any time and effort trying to reload a truck’s freight.5. Enhanced vehicle managementThis may be a surprise but it’s true. A weighbridge can serve as a comprehensive vehicle management system that will interface with other software in the company to produce detailed analysis and reports. The company’s fleet management operations can then be optimized using such analysis and reports.Why do you buy from us –We are into weighing business in India from many years. Also we known as the leading weighbridge manufacturer having a wide range of weighbridges, that is also commonly known as (Dharam Kanta), available in various sizes and capacities. With extra than a variety of operational installations throughout India, our weighbridges are area-confirmed for dependability and accuracy in hard industrial environments.Avery weighbridges contain innovatively designed modular deck systems that might be fabricated in-residence at our ISO certified manufacturing facility, Using top best steel from reputed metallic makers like JINDAL, TATA, ESSAR. These rugged structures are complemented by means of original synthetic, extraordinarily accurate (OIML c5/c6 licensed) and strong (stainless-steel, ip69k) load cells and artwork ‘ZM series’ indicators to offer ‘built to ultimate’ weighbridges to fit your desires.Our superior product nice is firmly supported by way of a Pan India community of trained and skilled carrier engineers. Our purchaser-targeted service delivery machine deploys a globally reputed “Service now” platform to make certain that your weighbridges function with the best up-time, supplying the nice go back on investment to you in terms of cash & trust.We are producing all types of weighbridges & weighing scales. We also offer ISO certified products with OIML/ NTP standards. All of our products are also having CE certification. We are having a Weighbridge production unit with a complete-fledged manufacturing facility. We're having the ability and enough manpower to cater to the production of weighbridge as consistent with the buyer’s requirement and its miles having a base of greater than 12,000 happy customers in India and abroad.All products offer whole custom-designed solutions with the simple person necessities standardized. We offer the maximum advanced technology to the marketplace at extremely competitive expenses. Our emphasis has been on the utility of load cell era and technique instrumentation to deal with various procedure problems that are so regular in addition to rare for every enterprise. Our relentless efforts in this direction have earned us the knowledge in these areas.All of our products offer on-line documentation with easy computer compatibility. Also, the software provided for automation is programmed within a wide range of packages to make it compatible with the current working system of the user organization. The returned-cease used gives easy garage and manipulation of the database whereas the front-give up provides appealing displays for graphical person interface to go into and manage numerous parameters.How does Weighbridge work -Almost all weighbridges have common components, which work collectively to degree weight. It's far important for a buyer to understand these components well to determine the truck scale exceptional applicable to meet their needs. There are some concepts which you must recognize earlier than deciding on a weighbridge in your enterprise:Gross weight: the burden of the truck while loadedTare: the weight of the truck whilst emptyNet weight = gross weight – tareMaximum load: It is so critical to make certain that the total weight of the truck and/or the load on a set of axles is in the range of felony values for street motors in a given location. Whether or not you're a client or dealer of goods, whether or not you need to matter stocks or test their conformity, the facts provided through the truck scale is crucial.This fact has an essential role in placing fees, earnings margins, nice control, inventory control, compliance with regulatory requirements, among others. The vicinity of the weighbridge has to be thoroughly idea. Before achieving a decision, solution the subsequent questions:Will the truck scale handle traffic in one direction or both?Does the site have enough space for Trucks to without problems exercise to go into or exit the dimensions?Is there a ready area for trucks in line now not to be blockading the street?Is the website Equalize and does it has enough capability to face up to cycles of ice and thaw?Does the website permit enough evacuation to accommodate rainwater and melt water?Does the website permit, if necessary, the set up of a brand new truck scale?For using the weighbridge, a weighing cabin for the operator is also required. He may make weighing records and verify the dispatch and/or reception notes, in addition, to be the man or woman of contact for truck drivers. Now and again, the cabin works additionally because of the authority that orders entry and exit aiming to keep order and protection of the region. In a few conditions, the weighing cabin may be changed via self-carrier terminals, permitting the truck motive force to deal with his private transactions, streamlining operations with excessive repeatability or restrained variables.How to install a weighbridgeA defective weighbridge a waste recycling site in Portsmouth had a weighbridge that malfunctioned. The website’s present weighbridge underwent prognosis and restore, but it was hooked up to be beyond restore-crowning glory after it failed re-qualification checking out. The selection to update the weighbridge become no longer one that became taken gently, but, a completely functioning and compliant weighbridge is essential to the commercial enterprise’s everyday operations, so it needed to get replaced without query, and rapid.Putting in a brand new weighbridge that allows you to avoid huge downtime to the enterprise, a new weighbridge had to be installed as a priority. So, with the co-operation of three groups, of which Solent scales become one, the vintage weighbridge changed into capable of being absolutely eliminated and brought away for scrap. This left the gap for a brand new weighbridge to be installed. Firstly, new foundations had to be prepared to contain some of the present foundations. This part of the task is vital as a sturdy, degree basis is important for the weighbridge to feature properly.But, the relevant groups pulled collectively to get this part of the task completed without any delays, and to the high preferred that turned into required. The new weighbridge was introduced and established with knowledge, professionalism, and precision. After testing, calibration, and verification have been achieved, the brand new weighbridge turned into prepared for use and the enterprise become operational another time.A -week turnaround, from start to complete, for a task of this value is pretty splendid. However, this case-examine highlights that once a goal is in sight, and with tremendous teamwork, a venture which may additionally seem not possible can be accomplished, and executed to a completely high popular of delivery. We are a company that believes in customer support and satisfaction, so we are adding some points you should know about Weighbridge measurement software too.Vehicle scale management softwareAutomobile scale management or Vehicle scale management software program can give customers control of scale functions on their laptop, and save an in-intensity record of every weighing transaction. From standard capabilities like producing reviews and tickets to advanced options including unattended terminal controls, invoicing, and image size, this exceedingly configurable bundle gives your enterprise a powerful device for taking pictures and analyzing facts. What is the weighbridge software program?Management software can give users manipulate of scale features on their laptop, and keep an in-depth file of each weighing transaction. From trendy capabilities like generating reports and tickets to advanced alternatives such as unattended terminal controls, invoicing, and image size, this especially configurable package gives your organization an effective device for shooting and studying data. What styles of the weighbridge software program are to be had?There's a large type of weighbridge software program available for purchase. It's miles crucial to are searching for a company that has a solution that could match your genuine requirements, or write a custom answer if no longer. This guarantees overall performance for your weighbridge software program. The maximum commonplace weighbridge software program is software used for transaction management, or shopping for and selling over the scale in criminal-for-exchange packages. This software allows us to do away with guide ticketing, which comes with many benefits.
- Home >
- Catalog >
- Business >
- Letter Template >
- Welcome Letter >
- Welcome Letter For New Members Sample >
- welcome message for group members >
- Warranty General Conditions - Foundation And Concrete Service