A Comprehensive Guide to Editing The Tria Form Pdf
Below you can get an idea about how to edit and complete a Tria Form Pdf step by step. Get started now.
- Push the“Get Form” Button below . Here you would be transferred into a splasher making it possible for you to make edits on the document.
- Choose a tool you require from the toolbar that shows up in the dashboard.
- After editing, double check and press the button Download.
- Don't hesistate to contact us via [email protected] regarding any issue.
The Most Powerful Tool to Edit and Complete The Tria Form Pdf
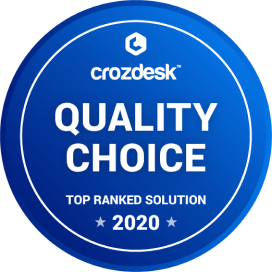
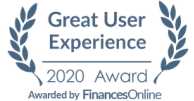
A Simple Manual to Edit Tria Form Pdf Online
Are you seeking to edit forms online? CocoDoc is ready to give a helping hand with its useful PDF toolset. You can make full use of it simply by opening any web brower. The whole process is easy and quick. Check below to find out
- go to the free PDF Editor Page of CocoDoc.
- Upload a document you want to edit by clicking Choose File or simply dragging or dropping.
- Conduct the desired edits on your document with the toolbar on the top of the dashboard.
- Download the file once it is finalized .
Steps in Editing Tria Form Pdf on Windows
It's to find a default application that can help make edits to a PDF document. Yet CocoDoc has come to your rescue. Examine the Manual below to find out possible approaches to edit PDF on your Windows system.
- Begin by obtaining CocoDoc application into your PC.
- Upload your PDF in the dashboard and make modifications on it with the toolbar listed above
- After double checking, download or save the document.
- There area also many other methods to edit PDF, you can go to this post
A Comprehensive Guide in Editing a Tria Form Pdf on Mac
Thinking about how to edit PDF documents with your Mac? CocoDoc offers a wonderful solution for you.. It makes it possible for you you to edit documents in multiple ways. Get started now
- Install CocoDoc onto your Mac device or go to the CocoDoc website with a Mac browser. Select PDF paper from your Mac device. You can do so by pressing the tab Choose File, or by dropping or dragging. Edit the PDF document in the new dashboard which includes a full set of PDF tools. Save the file by downloading.
A Complete Instructions in Editing Tria Form Pdf on G Suite
Intergating G Suite with PDF services is marvellous progess in technology, with the power to streamline your PDF editing process, making it faster and more cost-effective. Make use of CocoDoc's G Suite integration now.
Editing PDF on G Suite is as easy as it can be
- Visit Google WorkPlace Marketplace and get CocoDoc
- install the CocoDoc add-on into your Google account. Now you can edit documents.
- Select a file desired by hitting the tab Choose File and start editing.
- After making all necessary edits, download it into your device.
PDF Editor FAQ
Which is the smallest Android PDF library to open PDF files?
If you’re looking for a great PDF Library and SDK, I recommend trying an SDK built on top of one of the best PDF Readers on the iOS and Android app stores. I’m part of the Kdan team, and I recommend that you try Kdan’s PDF SDK. It contains many examples of code snippets which you can try and launch your app today. With efficient code in C#, Java, and Objective-C, you can create an app for whatever platform you want. The PDF SDK leverages experience for over 10 years with the Kdan PDF Reader, incorporating many of the most popular features for you to develop in the SDK. It contains features like to/from PDF converter, page editor, annotations, and a robust viewer engine. There is even a signature system based on DottedSign, so your users can create legally enforceable document signatures. See for yourself why Kdan’s PDF SDK is the one to use, download for a free tria ltoday, and see what you can create.
I am using Hypermesh as a preprocessor for finite element analysis. How do I decide which element to use and on what basis is this decided?
Hypermesh is indeed a good preprocessor for FEM as it supports exporting the mesh in different formats for many different solvers.Fig.1 - Hypermesh GUI with labels.Now, coming to meshing, there are some golden rules for meshing mostly irrespective of type of analysis and problems.- The mesh should be finer and accurately represent the geometry in the critical areas i.e. the areas where stress, strain, deformation and loading is going to be important.Fig.2 - Mesh 3 represents the geometry better than all others.- A part with all the three dimensions (x, y, z in a cartesian coordinate) comparable are usually meshed with solid elements. Any feature or part having thickness more than 10 mm should be meshed with solid elements provides any of the other two dimensions are not greater than 100 mm.Fig.3 - A circular cylinder meshed with solid tetrahedron elements.- A part with two dimensions comparable and the remaining one atleast 10 times less than both of the other two is meshed with shell elements. As a rule of thumb, any feature or part having thickness less than 10 mm should be meshed with shell elements provided both of the other two dimensions exceed 100 mm. The mesh should be in mid-surface and then the thickness and section properties should be assigned accordingly.Fig. 4 - Midsurface meshing and visualization of thickness- A part with two dimensions comparable and the remaining one at-least 10 times bigger than both of the other two is meshed with beam elements.Any long feature like a rod/bar/beam having circular cross section with diameter less than 10 mm or rectangular cross section less than 10 mm X 10 mm should be meshed as beam. The type of beam to be used will depend on the loading on the part, whether it is purely axial or bending and twisting is also involved.Fig. 5 - A circular rod is meshed with beam elements and shell elements.These four rules will take care of the mesh for the most part, though there's more depending on type of analysis, computational cost, accuracy and other modeling considerations.The last three rules work on the definition of aspect ratio of the geometric shape. In general, an aspect ratio more than 10 invites the necessity of using shell or beam elements.Preference of elements (only first order elements considered) :- While using solid elements 8 noded hexahedron elements are preferred to 6 noded pentahedron elements and the later preferred to 4 noded tetrahedron elements.Fig. 6 - Shell and solid elements- While using shell elements, 4 noded quad elements are preferred over 3 noded tria elements.The elements in the picture with more nodes than mentioned in my points are second order elements and in general they perform better than their first order counterparts.Element Quality:The elements interpolate the value of field variables from the later's value at the nodes and the intepolation happens according to the element formulations. The element formulation is derived for the ideal topology of elements, say an equilateral triangle or a square rectangle in case of tria and quad elements respectively. Deviation in the topology degrades the quality of mesh i.e. how accurate the interpolation will be and hence the accuracy of your result.The elements of the mesh must satisfy some quality criteria like- Minimum and maximum angles in tria and quad elements. For tria, they may be within 30-120 degrees and for quad, within 45-135 degrees.- Jacobian, a measure of how close the elements to the ideal ones. In Hypermesh, they should be more than 0.6.- Warpage, a measure of how much a quad element deviates from being in a single plane. The warpage angle should be less than 15.- Being within an appropriate length range defined by you, a minimum length of 3mm with most of the elements within the range of 5 mm - 10 mm is ideal for most of the cases.- Within a specified aspect ratio, likely range is 4-6.Mesh quality check is available in Hypermesh, and the menu shortcut is F10.Fig. 7 - Element quality checking panel in Hypermesh.Special Features:- Meshing circular holes: A hole is meshed in different manners according to its diameter.0 mm < D < 3 mm, the hole is ignored.3 mm < D < 5 mm, the hole is meshed as a rectangular hole5 mm < D < 10 mm, the hole is meshed with 6 elementsD> 12 mm, the hole is meshed with 8 elements or more.Fig. 8 - Mesh around a hole- Fillets: Like holes, a fillet is meshed in different manners according to its radius.R < 2 mm, the fillet is ignored.2 mm < R < 8 mm, the fillet is meshed with one element with an edge forming a chord along the circumference.R > 8 mm, the fillet is split with more than one element and the geometry is represented as accurately as possible.Fig. 9 - Accurate representation of a fillet.- Small parts: If any protruding part is present, there should be atleast two lines of element representing the geometry.Of course, for holes and fillets, ignoring the feature will depend on the importance of the same in your analysis. Look at the first golden rule.Automesh:Hypermesh has an automesh feature, where the software automatically meshes a part and decide the optimum meshing for the part. But, automesh doesn't perform well in case of complex geometries. Only for a conventional geometry automesh is sufficient. The best process here is taking out chunks of domain which is rectangular and simple and apply automesh to speed up the process of meshing.Automesh command can be invoked by pressing F12 in Hypermesh. In the 2D panel, there is another command "smooth" which will optimize mesh over a domain you select to make it better. The idea is to use all these commands together to achieve mesh flow.Mesh Flow and Symmetry:Mesh flow is a really important concept. In a complex assembly of parts, the mesh size and density changes from one region to another. When the mesh has to change its form, the transition should be smooth and the flow of mesh should conform with the transition.When the mesh size changes from big to small, it should happen gradually and not instantly in a row or two. The image at the top has a better mesh flow than the one at the bottom. The rule of thumb is, given all other things are right, the mesh is better when it looks good.Also, symmetry plays an important role in meshing. If a part is symmetric, the mesh should also be symmetric. This rule actually follows from the first golden rule, though in a non-obvious way, that the mesh should accurately follow the geometry. The rule of thumb for this is that when there is a symmetric part, the meshing is done only on the half the part and is reflected to maintain the symmetry as it is in the geometry.For example, in the above part the meshing can be done only in the left part and then reflect it to maintain symmetry of the mesh.Hypermesh Shortcuts:Here goes most of the shortcuts for Hypermesh.F1 - HelpShift+F1 - ColorCtrl+F1 - Print fileF2 - DeleteShift+F2 - Temp NodesCtrl+F2 - BMP fileF3 - ReplaceShift+F3 - EdgesF4 - DistanceShift+F4 - TranslateF5 - MaskShift+F5 - FindF6 - Edit elementShift+F6 - SplitCtrl+F6 - JPEG fileF7 - Align nodeShift+F7 - ProjectCtrl+F7 - Full screenF8 - NodesShift+F8 - Node editF9 - Line editShift+F9 - Surface editF10 - Check elementsShift+F10 - NormalsF11 - Quick editShift+F11 - OrganizeF12 - AutomeshShift+F12 - SmoothThere is a nice PDF of the shortcuts which can be printed and kept for ready reference. It can be downloaded from Hypermesh Shortcuts on altairuniversity.comDISCLAIMER:1. This answer is not everything one need to know about meshing in Hypermesh. To learn more about meshing, look at the below answers and links and consult the references mentioned there. This is just a primer.Mukunda Madhava Nath's answer to ANSYS Inc: How should I decide which mesh to use in ansys?Mukunda Madhava Nath's answer to What are some good books to learn finite element analysis?Top 5 misunderstandings on (good) mesh.Accuracy, Convergence and Mesh QualityMeshing Considerations for Linear Static ProblemsMeshing your Geometry: When to Use the Various Element Types2. The measurements and lengths given here are not absolute. They are values usually used by FE analysts and should be considered carefully with guidance.3. The images are taken from internet and I don't own any of them. I will remove them in case of any dispute.Hope this helps.PS: This answer will need a little bit of editing and clarifications. If you have any comments or find any mistakes, please let me know.Things to update: computational cost/memory consumption, references, a few links and of course, grammar.Interested in FEA, check my blog at Practical FEA
How should I decide which mesh to use in ansys?
Mesh type and size depends on many factors including:Type of Analysis required.For CFD other than thermal, trias/tetra mesh is used, and for crash mixed mesh of quads and trias is used.Geometry.Min. Element size should equal to length of least sized fillet, if perfect capture is not required it can be altered.Time and available computing resources.Time is also important to decide how to mesh and computing resources also plays role to decide mesh size/no.of elements.There is a book which gives an idea about Meshing and Analysis, if you read it, it will definitely help you.Practical Finite Element Analysis by Nitin S. Gokhle. Online free PDF versions also available.
- Home >
- Catalog >
- Legal >
- Business Law >
- Hold Harmless Agreement >
- Hold Harmless And Insurance Agreement >
- hold harmless agreement real estate >
- Tria Form Pdf