A Complete Guide to Editing The Navigation-Inspection Guide For Commercial Vessels
Below you can get an idea about how to edit and complete a Navigation-Inspection Guide For Commercial Vessels in detail. Get started now.
- Push the“Get Form” Button below . Here you would be transferred into a page allowing you to conduct edits on the document.
- Select a tool you like from the toolbar that emerge in the dashboard.
- After editing, double check and press the button Download.
- Don't hesistate to contact us via [email protected] For any concerns.
The Most Powerful Tool to Edit and Complete The Navigation-Inspection Guide For Commercial Vessels
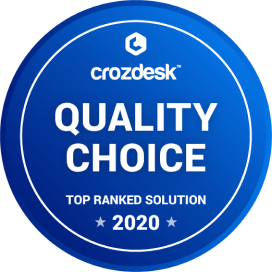
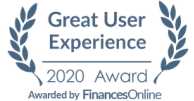
A Simple Manual to Edit Navigation-Inspection Guide For Commercial Vessels Online
Are you seeking to edit forms online? CocoDoc can be of great assistance with its Complete PDF toolset. You can quickly put it to use simply by opening any web brower. The whole process is easy and quick. Check below to find out
- go to the PDF Editor Page of CocoDoc.
- Import a document you want to edit by clicking Choose File or simply dragging or dropping.
- Conduct the desired edits on your document with the toolbar on the top of the dashboard.
- Download the file once it is finalized .
Steps in Editing Navigation-Inspection Guide For Commercial Vessels on Windows
It's to find a default application that can help make edits to a PDF document. However, CocoDoc has come to your rescue. Take a look at the Manual below to know possible approaches to edit PDF on your Windows system.
- Begin by obtaining CocoDoc application into your PC.
- Import your PDF in the dashboard and make modifications on it with the toolbar listed above
- After double checking, download or save the document.
- There area also many other methods to edit PDF text, you can check it out here
A Complete Handbook in Editing a Navigation-Inspection Guide For Commercial Vessels on Mac
Thinking about how to edit PDF documents with your Mac? CocoDoc can help.. It allows you to edit documents in multiple ways. Get started now
- Install CocoDoc onto your Mac device or go to the CocoDoc website with a Mac browser. Select PDF sample from your Mac device. You can do so by clicking the tab Choose File, or by dropping or dragging. Edit the PDF document in the new dashboard which encampasses a full set of PDF tools. Save the content by downloading.
A Complete Advices in Editing Navigation-Inspection Guide For Commercial Vessels on G Suite
Intergating G Suite with PDF services is marvellous progess in technology, with the power to reduce your PDF editing process, making it troublefree and more cost-effective. Make use of CocoDoc's G Suite integration now.
Editing PDF on G Suite is as easy as it can be
- Visit Google WorkPlace Marketplace and locate CocoDoc
- establish the CocoDoc add-on into your Google account. Now you are in a good position to edit documents.
- Select a file desired by pressing the tab Choose File and start editing.
- After making all necessary edits, download it into your device.
PDF Editor FAQ
How does US Coast Guard personnel inspect ships and what do they look for?
The U.S. Coast Guard inspects domestic and foreign flag vessels in accordance with U.S. law, international treaty, and agency policy. Specifically, Title 46 Code of Federal Regulation, the Safety of Life at Sea conventions, and Commandant's Instructions are the principal guiding authorities Coast Guard marine inspectors use when conducting commercial vessel inspections.Vessels are inspected at recurring intervals determined principally by the class of vessel, cargo type, and operating environment: e.g. Passenger, tankship, or general cargo ship, salt water or fresh water.Inspection types include: Inspection for Certification, annual or quarterly reinspections, hull examinations, cargo tank internal inspections, internal structural examination, and for foreign vessels: port state control examinations.A typical inspection includes an examination of required vessel documents, logs, and crew licenses and credentials, examination of navigation, lifesaving, firefighting, pollution prevention, and engineering systems. Firefighting, man overboard, and abandon ship drills are conducted. Any deficiencies noted during the inspection are documented and requirements for correction are stated. A timeframe for correction of each deficiency is established as appropriate for the specific deficiency. For example lifesaving and firefighting deficiencies might require correction prior to getting underway whereas deficiencies in the logging of drills might be given a period of days for correction. After the inspection is complete, the marine inspector enters the inspection and inspection results into a computerized database and updates next inspection due dates and any requirements for any follow up activity.
Did Great Britain sink an Argentinian submarine during the Falklands war? Is it still there?
OPERATION “HOKEHAMTON” Georgia Islands (1984/1985)During the latter part of 1984 and the first weeks of 1985, the Directorate of Marine Services of the British Ministry of Defense undertook the largest shipwreck removal operation in the South Georgia Islands.Refloating Operation of the Argentine Submarine ARA "SANTA FE"During the latter part of 1984 and the first weeks of 1985, the Directorate of Marine Services of the British Ministry of Defense undertook the largest shipwreck removal operation in the South Georgia Islands.This unique Operation due to its remoteness and lack of support bases, was mounted to remove the Argentine Submarine "SANTA FE" (Former USS CATFISH), sunk in the only truly sheltered anchorage on the Island.The SANTA FE was sunk in 21 m .deep, still containing a load of munitions of war and seriously obstructing the free international use of the anchorage.Operation "HOKEHAMPTON" was directed by the Chief of Rescue of the Navy and supported by the personnel embarked on the Salvage Vessel RMAS GOOSANDER and the commercial tugboat SALVAGEMAN, owned by the United Towing Co. of Hull.It was known that the submarine was totally flooded and had all the watertight ports of the transverse bulkheads open.There was no information on the condition of the external tanks, but I knew that the stern was partly buried in a bed of mud.To set up this operation in such a remote location, careful planning and having the equipment required to solve all the expected problems and unforeseen problems was largely required.Obviously, it would be necessary to excavate the mud bed to gain access under the side of the external tanks, but with little or no tidal current to carry the mud out, a traditional air compressor would not be practical.GENFLO SUBSEA Ltd, offered a power eductor pump, which not only gave good digging performance, but was also capable of discharging debris through a 500 m submerged pipe.to a point outside KING EDWARD Cove, where it did not interfere with normal navigation.This equipment was leased.As it was clear that a considerable amount of underwater cutting operations would be required using a large amount of oxygen, this meant that large and heavy storage cylinders were required for their provision.The transportable concentrated oxygen, originally purchased from RIMERALCO for an earlier planned recovery operation in the South Atlantic, was reconditioned by the manufacturer and formed a vital part of the prepared equipment.The water around South Georgia is very cold, therefore a special thick, bespoke neoprene drysuit was tailored for each diver to reduce the effects of the low seawater temperature.After nearly five weeks of travel from GREAT BRITAIN, the expedition arrived at KING EDWARD's Cove at dawn on November 4, 1984, finding several inches of snow on land and half a cove with a thin layer of snow-covered ice.The first four days were spent unloading the equipment at the GRYTVIKEN dock, the laying of an anchor field around the Submarine by GOOSANDER and the recovery, by the SALVAGEMAN, of an abandoned barge, to be used as a work platform.SALVATION BEGINS.On November 9, the GOOSANDER secured the moorings on the submarines and was thus placed, so that it was possible to move throughout the total of 94 m.length of the submarine, without adjusting the position of the anchors.It remained in that mooring position for 94 days, being supplied with food, equipment, fuel and fresh water by SALVAGEMAN.The preliminary inspection dive, using an underwater television camera, showed that the submarine was at approximately 25 gdos.Heel to starboard, buried about 5 m.in the mud aft and with only the turret hatch open.It was also confirmed that the submarine had connections to drain the hull compartments with high and low pressure air.Subsequent work proved that six of the eight discharge pipes were operable, of which fortunately some were not located in compartments with access hatches through the rugged hull.At the appropriate time, these hatches were tightly fitted, fitting taps, control valves, and a flexible discharge pipe.To avoid the control problems associated with air-only refloating of a totally submerged vessel, it was decided to regain as much buoyancy as possible in the interior of the resistant hull and in the external tanks, progressively decreasing the weight with pressurized air, until that the submerged weight be reduced from almost 1800 tons to a value between 100 and 200 tons approximately.The final weight would then be lifted by two 100-ton GOOSANDER rigs, breaking most of the mud suction and the bow would be re-floated with its own buoyancy.Work was started on the forward port side, in the fuel tank. N ° 1.As the excavation approached the keel, it found a manhole cover that was reasonably easy to remove.No fuel was found in this tank and when it was prepared to introduce air into it, this fuel tank was found to have no longitudinal bulkhead, being attached around the hull.This allowed it to be blown from either side, or both sides, but needed to be vented from both sides to be able to flood.The lack of longitudinal subdivision also reduced the tank's effectiveness in lateral stability control.Subsequently the other three fuel tanks were found in similar construction condition.Diesel Oil was found in the two rear fuel tanks.The buoyancy of these tanks was important, so some method had to be imagined to recover the fuel, without polluting the waters.The circumference shape of the tanks was used to effect the recovery of the fuel, by means of convenient air pressure from the lower part of the starboard side of the tank by placing a 38 mm flange.Discharge on the upper port side of the tank.A hole was made in the inside of the flange to allow the fuel to escape and a hose was adapted in the upper part, to transfer the fuel to the 3-ton capacity reception tank of the barge, moored to the side of the GOOSANDER.The plugged tank manhole cover was then removed, allowing water to enter and pressurize the tank to ambient sea pressure.By carefully blowing from the starboard side of the tank to a maximum of 4 square inches of pressure, above ambient sea pressure, the fuel was displaced from the starboard side, around the rugged hull, above the level of the water inlet hole. and through the recovery hose, to the receiving tank on the barge.From this tank it was pumped into the SALVAGEMAN, to be passed through its purifiers and stored for future use.When air began to come out of the recovery hose, indicating that all the fuel had been displaced from the starboard side, the blowing stopped and the air allowed the tank to vent.This caused seawater to enter the tank, pulling the remaining fuel on the port side up and through the hose to the surface.The difference between the specific gravity of the fuel and the seawater, combined with a less siphoning effect, ensured the complete removal of the fuel from the tanks.A similar operation was executed on both next tanks, resulting in the recovery of almost 90 tons of fuel and a similar volume of buoyancy.Some difficulty was experienced in the insertion of pressurized air in the external tanks, due to the lack of documentation and the considerable variations in the thickness of the tank plate, being the ends of 9.5 mm, in the main tanks of ballast and 22 mm in the safety and auxiliary tanks.Similar problems were found in cutting openings for tank flooding without valves or manhole covers.The underwater cutting was carried out using a powerful electric arc, as in welding, with oxygen supplied through an electrode with a cutting effect similar to casting.The arc of current required to achieve the underwater cut varies with the thickness of the steel, with a maximum of 640 amres and 200 square inches of oxygen pressure being used for the thickness of the make in this operation.A large number of projectile holes had to be repaired in the plates of the ballast tanks and in the vent and blow pipes.This was accomplished using a variety of techniques, including underwater welding, small patching, attaching headstocks, direct welding of cracks, hook-tight patches, patch fitting with explosive riveting equipment.The renovation of a bad perforated pipe and canceling the rest of the openings that were left.The use of compressed air to vent the hull of the submarine is restricted by the feasibility that all hatches, valves and gaskets are designed to withstand external pressure.A very careful application of internal pressure is necessary to avoid breaking the seal, which once established, will normally be maintained, but if a leak occurs, it is extremely difficult to contain.ENTERING THE HELMETIt was necessary to enter the submarine to close as many watertight ports as could be accomplished, to reduce the effect of longitudinal free surfaces and to divide the hull pressure within manageable blowing values.The first few entries were made with some fear and required a great deal of courage on the part of the divers.With the progress of the work, a routine was developed, thus the working distance from the access point was extended until the divers were working at 18 m.from the access hatch, having traversed the length of both engine rooms, passing through an intermediate watertight porthole on the way, with zero visibility.During these entries, the divers took with them a handheld underwater television camera, with lighting lamps, the brightness of which was controlled from the position of the supervisor's dive monitor.The resolution of the camera was 6 times greater than the human eye, so the dive supervisor and the rescue officer on the surface could often see enough to guide and inform the diver on their tasks.This increased the morale of the divers and relieved the supervisor of many concerns, since he could maintain visual contact with the task that the diver was developing, as well as verbal communication.During the tests carried out on the outer tank, it had been agreed that apparently some tanks were common, and could probably be blown by means of high pressure air lines, through control valves that were open, in the air control panel of the tank. high pressure.A diver inside the control room, was dedicated in an intensive way to locate the high pressure air control panel and close the valves.This solved the ballast tank problems.When the blowing test of the rugged hull was started, it was discovered that there were two more problems.These were, air leakage from the resistant hull inside certain fuel tanks and an action of deterioration of the tightness, due to a leak in the lip of the main induction valves.Despite the valiant efforts of the divers to locate and close the valves of the fuel and water compensation lines, the loss of air from the hull to the tanks was never properly canceled and had to be taken into account when the survey began. blowing program.It turned out to be quite a task trying to stall the induction valve leak, with no guarantee of success, this having been decided rather than locating and stalling the three or four inlet valves in the hull.This particular vessel was found to have two 635mm and one 400mm check valves.In diameter which were located in the engine room.Some difficulties were experienced in finding these controls, as only a vague idea of their shapes was had.Once found, he encountered the additional difficulty of learning their operation.Eventually, by having the outer valve with the covers removed, a diver could observe the opening and closing movement and verify its operation, proceeding to close the three valves.However, this did not mean that the way the valves locked in the closed position had been discovered, therefore, jaws with extension screws were constructed to hold them and the valves were then secured against the lip of the inlet pipe.To complete the sealing 1680 pounds of concrete were mixed by hand by the divers and poured into each of the valve distribution boxes, ensuring their effectiveness.Heavy plates of steel with secured discharge hoses and valves were placed over the open hatch in front of the torpedo room and after the engine room to replace the broken discharge pipes in those compartments.A heavy 18mm cable sling was passed under the hull with the shackle eyes together on top of the deck to close aft, in front of the depth planes.Ten inflatable parachutes were attached to this strap, each with a lifting capacity of 5 tons, five with a 6 m cable.in length and five with 3 meter long cables.These parachutes were inflated as they were placed, to prevent them from tangling later.The 50 tons of capacity that were applied to the lower part of the stern of the submarine, would help to break the initial suction of the mud and then be progressively reduced, taking care of the parachutes break the surface and the submarine floats by its own means.In this way it was tried to mitigate the acceleration effect after it took off from the bottom and then to reduce the blowing air from the outer tanks on the surface and allow more time to reduce the pressure in the internal compartment on the watertight hatch.The GOOSANDER, moved aft, along the submarine, stringing the 31 hoses to the tanks and hull spaces and the divers secured the openings on the deck.Meanwhile the SALVAGEMAN was laying moorings at the chosen beach and some of the GOOSANDER men were settling on the shore with clamps for the bow moorings of the submarine.With its stem over the stern of the SANTA FE, the GOOSANDER and the divers passed the 210mm cable.For the subsequent hoisting around the hull, on the axis of the propellers and placed the 100-ton tackle.The carefully planned blowing began at 10:50 a.m. on February 8, 1985, and the submarine was on the surface at 11:17 a.m. on February 11.After checking and consolidating the buoyancy, the movement towards the beach was started.At 15:15 the submarine was stranded with a heavy list to starboard and having lost some buoyancy along the way.Eight days of work were required to secure the vessel and prepare it for towing.On February 20 after careful conditioning he was towed out of King's Cove.EDWARD to be sunk in deep water.The operation lasted 120 days, during which 868 separate dives were made, including 42 entries in the resistant case.There were no accidents, diving incidents or decompression sickness, speed was sacrificed for safety throughout the entire operation.This operation could not have been carried out without the cooperation of the Commander of the British Falklands Forces, the Commander-in-Chief of the Fleet and the Royal Auxiliary Fleet, which together made logistical support possible, maintaining the appropriate units in the area. .SOURCE: JANE´S DEFENCE WEEKLY - VOLUME 4 - N ° 12 - SEPTEMBER 21, 1985.Original Article: SALVING THE SANTA FE - By MD WALKER
What is the person in The Crows Nest called?
A Barrelman is the person who would be stationed in the barrel of the foremast or crow's nest of an oceangoing vessel as a navigational aid. In early ships the crow's nest was simply a barrel or a basket lashed to the tallest mast. Since ships no longer have a crows nest to speak of, here is a part of how maritime vessels have evolved from the crows nest to our modern radar systems. The old wind driven sailing ships of early periods included a small observation deck nicknamed the crow’s nest, located high above the deck and built on to one of the masts. One of the sailors would climb to the crow’s nest with a telescope to gain a long range view of the surroundings from higher elevation. During the early 20th century, some naval ships towed a balloon that carried a gondola from where crew members could gain a long range view. Evolving maritime technology could create new application for an airborne micro technology that can provide a long range view.IntroductionThe development of early vessels coincided with advances in astronomy that assisted night time navigation. Navigation by stars provided an accurate idea of latitude, allowing early maritime traders to discover that a spice trading city in southwestern India shared the same latitude as the southern entrance to the Red Sea. The increasing size of wind driven ships built with multiple masts made possible the installation of an observation platform on one of the masts, high above the deck. The elevated vantage point increased the range of vision for mariners and especially when approaching land.The introduction of steam power led to the development of much larger ships, built to mush greater length, width and height. Following the era of the towed balloon, the invention of radar technology allowed the remotely located terrain observation technology to be installed high on a ship. Radar and sonar technology served the maritime sector well, given the low to moderate sailing speed of most commercial civilian vessels. The possible introduction of high-speed winged boats to oceanic travel would require the installation of observation technology high above ocean surface.Vessel Speed and ObservationThe high rate of speed of which winged boats are capable requires that the navigation crew have a view of marine traffic conditions perhaps as much as 50 or 60 miles ahead of the speeding vessel. If the winged vessel were to tow an airborne observation technology that would fly at an elevation of 2,600 feet (800 meters) above water level, it could provide information about the seascape up to 100 kilometers (60 miles) ahead of the speeding winged vessel. Winged vessel crew would know the location, speed and sailing direction of other vessels and have one to two minutes to undertake corrective action.As the winged vessel leaves port, either from land-based coastal runway or from a seaplane runway, winged observation technology would be launched by reeling out a tether installed on top of the winged vessel. As the vessel accelerates to greater speed, a tether would be further reeled out until the “eye-in-the-sky” reaches the required elevation flight. It would carry aeronautical lights to alert other aircraft of its presence. The tether may include both power cable and optical cable to supply the flying observation unit with aviation lighting and operate the observation/transmission technology.Scale Model Flight TechnologyThe observation vehicle would be the equivalent of a towed scale model glider carrying observation technology such as radar and television, except built to greatly more rugged structural standards. For operation in winter weather, the flight unit may need to be built with electric heaters under the upper surface of its wings, to melt ice that could otherwise build up on top of the wings and impair flight. The tethered flight unit could include a turbine that drives an electrical generator to provide electric power for aviation lights and to operate the high-elevation observation unit.To assure ruggedness and longevity, the small flight unit could be built from any of several modern lightweight, high-strength materials such as carbon fiber or other super material. Advances in optical lens technology would allow for development and installation of a light weight camera along with modern radar technology that would collect data from the terrain ahead and provide on a screen, the equivalent of a daytime high-elevation view of the terrain so as to improve night time navigation. The technology would be applicable on the ocean as well as along navigable waterways with unlimited overhead clearance.Arrival at DestinationAs the winged vessel slows on approach to a destination port, the airborne observation unit would be retracted through reeling in the cable. If the airborne unit receives electric power from the winged vessel, it could be built with the rotors of a drone helicopter or quadcopter to allow it to remain aloft so as to provide the navigation crew with a high elevation view of the terminal area. The high elevation view could help guide the crew to navigate the winged vessel to its assigned parking location at the terminal.Once the winged vessel is parked, the observation flight unit may be reeled in and depowered before undergoing a routine inspection prior to departure on a subsequent voyage. The unit could contain recording technology that would have recorded data relevant to is previous flight, information that could routinely be transferred into a larger land-based recording technology. Marine traffic density at some ports could pose a safety risk for winged boats arriving, except if the winged boat is a Type B version capable of 150 meters flight elevation and will touch down at and lift off from coastal airports.The Bird ProblemBird strikes are certainly a problem at commercial airports. The majority of birds live on land or at coastal areas near land, with few birds being far away from land. During seasonal migration, most migrating birds fly over land with very few flying over the ocean. Some varieties of geese that do migrate across ocean have been discovered flying at very high altitude where air is of low density. The combination of a tether connected to a flying observation unit should pose minimal danger to birds, given that the technology would be deployed away from coastal areas.ConclusionsThere has been a need for the past few centuries in the maritime sector to gain a view of the terrain from high elevation. It began with the crow’s nest followed by the towed balloon that was in turn followed by radar technology. High-speed transportation technology that travels close to the water surface requires the view from high elevation so that the crew would know what lies up to 60 miles ahead of the speeding vessel. The airborne observation technology could include both optical and radar technologies, with combination optical line and power line installed into the towing tether.
- Home >
- Catalog >
- Legal >
- Affidavit Form >
- Statutory Declaration Form >
- Victorian Statutory Declaration Form >
- Navigation-Inspection Guide For Commercial Vessels