How to Edit and sign Design Of Composite Structures Towards Carbon Zero Online
Read the following instructions to use CocoDoc to start editing and completing your Design Of Composite Structures Towards Carbon Zero:
- To get started, look for the “Get Form” button and click on it.
- Wait until Design Of Composite Structures Towards Carbon Zero is ready to use.
- Customize your document by using the toolbar on the top.
- Download your customized form and share it as you needed.
An Easy Editing Tool for Modifying Design Of Composite Structures Towards Carbon Zero on Your Way
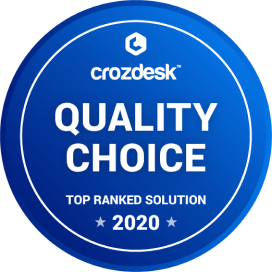
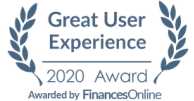
Open Your Design Of Composite Structures Towards Carbon Zero Without Hassle
Get FormHow to Edit Your PDF Design Of Composite Structures Towards Carbon Zero Online
Editing your form online is quite effortless. There is no need to install any software on your computer or phone to use this feature. CocoDoc offers an easy tool to edit your document directly through any web browser you use. The entire interface is well-organized.
Follow the step-by-step guide below to eidt your PDF files online:
- Find CocoDoc official website on your laptop where you have your file.
- Seek the ‘Edit PDF Online’ button and click on it.
- Then you will visit this product page. Just drag and drop the PDF, or choose the file through the ‘Choose File’ option.
- Once the document is uploaded, you can edit it using the toolbar as you needed.
- When the modification is done, click on the ‘Download’ button to save the file.
How to Edit Design Of Composite Structures Towards Carbon Zero on Windows
Windows is the most widespread operating system. However, Windows does not contain any default application that can directly edit PDF. In this case, you can install CocoDoc's desktop software for Windows, which can help you to work on documents productively.
All you have to do is follow the guidelines below:
- Get CocoDoc software from your Windows Store.
- Open the software and then upload your PDF document.
- You can also select the PDF file from OneDrive.
- After that, edit the document as you needed by using the various tools on the top.
- Once done, you can now save the customized document to your laptop. You can also check more details about editing PDF in this post.
How to Edit Design Of Composite Structures Towards Carbon Zero on Mac
macOS comes with a default feature - Preview, to open PDF files. Although Mac users can view PDF files and even mark text on it, it does not support editing. With the Help of CocoDoc, you can edit your document on Mac quickly.
Follow the effortless steps below to start editing:
- First of All, install CocoDoc desktop app on your Mac computer.
- Then, upload your PDF file through the app.
- You can attach the PDF from any cloud storage, such as Dropbox, Google Drive, or OneDrive.
- Edit, fill and sign your paper by utilizing this tool.
- Lastly, download the PDF to save it on your device.
How to Edit PDF Design Of Composite Structures Towards Carbon Zero via G Suite
G Suite is a widespread Google's suite of intelligent apps, which is designed to make your work faster and increase collaboration between you and your colleagues. Integrating CocoDoc's PDF editing tool with G Suite can help to accomplish work effectively.
Here are the guidelines to do it:
- Open Google WorkPlace Marketplace on your laptop.
- Seek for CocoDoc PDF Editor and install the add-on.
- Attach the PDF that you want to edit and find CocoDoc PDF Editor by choosing "Open with" in Drive.
- Edit and sign your paper using the toolbar.
- Save the customized PDF file on your computer.
PDF Editor FAQ
What are the factors affecting fibre-reinforced concrete?
Factors Affecting Durability of Fiber Reinforced Concrete (FRC)Following are the factors which affects the durability of fiber reinforced concrete:Extreme temperature and fireFreezing and thawingDegradation and embrittlement due to alkali attack and bundle affectWeathering and scalingCorrosion resistanceEffect of Extreme Temperature and Fire on Durability of FRCGenerally, concrete has a reasonable resistance to severe temperature because of its low thermal conductivity, great heat capacity, and it is not burn easily while exposed to fire.Concrete constituents for example specific aggregate types and cement clinker are not influenced by high temperature both chemically and physically. However, there are others concrete constituents that affected by temperature changes such as hydration product. It is influenced by loss of water, micro-cracking, and damage by differential expansion.The addition of steel fiber, synthetic fiber, or combination of both to concrete enhances structural concrete elements resistant against substantial temperature and fire.The strength of conventional concrete is decreased considerably if it exposed to fire for long time. Cement paste and aggregate bond in concrete is damaged at a temperature of 202C and about half of the concrete strength is decline at temperature of 427C, and 90% of concrete strength is lost at temperature of larger than 927C.Fiber provision do not impede concrete failure under this sever condition but it increases fire exposure safe time. The extension of fire exposure safe time provides more time during which evacuations and the fire extinguishment can be proceeded safely.It is reported that, the application of hybrid combination of steel and polypropylene fibers in precast concrete fireplace hearths produced small or not explosive spalling.Regarding concrete spalling, when concrete exposed to fire, excess water inside concrete, which used to provide workability during construction, changes to steam pressure. If the pressure inside concrete is not released and surpass concrete tensile strength, explosive spalling will occur.The concrete spalling depends on the amount of free water and its distribution while concrete element is exposed to fire.The damage caused by spalling may penetrate concrete to about 6 cm.Spalling is a serious problem because it may expose steel reinforcement to high temperature. Hence, steel reinforcement is deteriorated quickly which in return ultimate load carrying capacity of concrete member is declined.It is demonstrated that, when concrete reinforced with polypropylene fiber exposed to high temperature, the polypropylene fiber is melted and fine capillary pores will be emptied and this lead to release the accumulated steam pressure and the concrete maintain its strength.The provision of steel fiber increases small concrete slab fire resistance to three to nine times that of the slab with no fibers.Finally, fibers can be added to concrete to bridge cracks and keep structure integrity of the damaged structure.Effect of Freezing and Thawing on Durability of FRCIn this section durability of three fiber reinforced concrete namely steel, synthetic, and cellulose FRC will be explained.It is demonstrated that, among factors such as fiber content, air content, cement content, and water to cement ratio, the air content create significant effect on the steel fiber reinforced concrete resistance against freezing and thawing.Moreover, the reduction of SFRC modulus of rupture due to freezing and thawing is smaller than that of concrete with zero fiber.It is recommended by Rider and Heidersbach that, mix design of SFRC that is used in marine environment, need to have water content of no greater than 0.45, cement content should be at least 519 Kg/m3, and air content ranges from 6-7.5%.Regarding synthetic fiber reinforced concrete, it is pointed out that, not only does the synthetic fibers improves freezing and thawing resistance of synthetic FRC but also enhances concrete ability to withstand deicer scaling.Moreover, freezing and thawing cause reduction of flexural strength of concrete reinforced with polyolefin micro-fiber by about 15% whereas plain concrete flexural strength reduced by 30%.As far as cellulose fiber is concerned, it is found that, fiber reinforced cement board (FRCB) which is laminated material and consist of cellulose fiber, cement, silica, and water, is vulnerable to freezing and thawing deterioration due to its high porosity, hydrophilic and tabular nature of cellulose fibers, and laminated nature of the composite.FRC Degradation and Embrittlement due to Alkali Attack and Bundle EffectStrength of various fibers for example glass, polymeric, and natural fibers are decreased in long term because of weathering. It is substantially important to know time-dependent reduction of durability and strength of those fibers in structurally related areas.That is why deterioration mechanism of various fibers will be explained in this section.Glass Fiber ConcreteReinforced concrete commonly contains alkali resistance glass fibers between 3-5% of the whole composite weight. It is reported that, the corrosion of fiber is the major degradation mechanism.However, it is claimed that, apart from the effect of corrosion, there are other factors that influence the durability of GFRC. Added to that, in most situations, calcium hydroxide, which is a product of cement hydration, is the agent that is to blame for decreasing GFRC durability.That is why attempts made toward the reduction of calcium hydroxide in order t improve the durability of GFRC. Calcium hydroxide can be reduced by either adding admixtures for example fly ash, ground granulated blast furnace slag, and silica fume or avoid the use of conventional Portland cement especially those types which contain calcium aluminates or sulfo aluminates.In summary, the glass fiber reinforced concrete damage mechanisms are chemical attack, mechanical attack, delayed fracture.Cellulose Fiber ConcreteCycles of wetting and drying lead to degrade cellulose fiber and this degradation occur in different mechanism includes change in degree of fiber cement bonding and fiber mineralization.In the former mechanism, hydration product transportation specifically lime within the lumen of fibers and around the fibers lead to reduce interface porosity. This could be the cause of the increase of fiber cement bond and the decline of composite ductility.In the latter mechanism, it is claimed that, the embrittlement of fiber occur as a result of the penetration of cement hydration product into the fiber.Lastly, the durability of cellulose fiber may be increased by Fiber impregnation with blocking agents, and water repellent Agents Sealing of the matrix pore system; Reduction of Ca(OH)2 content in the matrix; and A combination of fiber impregnation and matrix modification.Effect of Weathering and Scaling on Durability of FRCThe deicer salt scaling, which its mechanics is still not clear, is merely affect a thin layer of exposed concrete which not exceed few centimeters. It is reported that, the present fiber and the type of fiber do not influence dicer salt scaling resistance. Moreover, it is pointed out that, steel fibers that in contact with concrete which suffered scaling, rusts.Corrosion Resistance of Fiber Reinforced ConcreteUnlike ordinary reinforced concrete beam, FRC is distributed in concrete and some of them might be close or at the surface of the concrete. Therefore, those fibers which are not protected by concrete might corrode.Factor that could lead to corrosion are chloride induced corrosion, corrosion because of PH reduction in the concrete mix.It is showed that, low carbon steel and galvanized steel fibers do not corrode in chloride concentration that greater than 2 percent by weight. Moreover, at much greater chloride ions, melt extracted fiber does not corrode.Hope it helps you!
What are the steps involved in the design of the structure of an aircraft?
AIRCRAFT BASIC CONSTRUCTIONINTRODUCTIONNaval aircraft are built to meet certain specified requirements. These requirements must be selected so they can be built into one aircraft. It is not possible for one aircraft to possess all characteristics; just as it isn't possible for an aircraft to have the comfort of a passenger transport and the maneuverability of a fighter. The type and class of the aircraft determine how strong it must be built. A Navy fighter must be fast, maneuverable, and equipped for attack and defense. To meet these requirements, the aircraft is highly powered and has a very strong structure.The airframe of a fixed-wing aircraft consists of the following five major units:FuselageWingsStabilizersFlight controls surfacesLanding gearA rotary-wing aircraft consists of the following four major units:FuselageLanding gearMain rotor assemblyTail rotor assemblyYou need to be familiar with the terms used for aircraft construction to work in an aviation rating.STRUCTURAL STRESSLEARNING OBJECTIVE: Identify the five basic stresses acting on an aircraft.The primary factors to consider in aircraft structures are strength, weight, and reliability. These factors determine the requirements to be met by any material used to construct or repair the aircraft. Airframes must be strong and light in weight. An aircraft built so heavy that it couldn't support more than a few hundred pounds of additional weight would beuseless. All materials used to construct an aircraft must be reliable. Reliability minimizes the possibility of dangerous and unexpected failures.Many forces and structural stresses act on an aircraft when it is flying and when it is static. When it is static, the force of gravity produces weight, which is supported by the landing gear. The landing gear absorbs the forces imposed on the aircraft by takeoffs and landings.During flight, any maneuver that causes acceleration or deceleration increases the forces and stresses on the wings and fuselage.Stresses on the wings, fuselage, and landing gear of aircraft are tension, compression, shear, bending, and torsion. These stresses are absorbed by each component of the wing structure and transmitted to the fuselage structure. The empennage (tail section) absorbs the same stresses and transmits them to the fuselage. These stresses are known as loads, and the study of loads is called a stress analysis. Stresses are analyzed and considered when an aircraft is designed.TENSIONTension is defined as pull. It is the stress of stretching an object or pulling at its ends. Tension is the resistance to pulling apart or stretching produced by two forces pulling in opposite directions along the same straight line. For example, an elevator control cable is in additional tension when the pilot moves the control column.COMPRESSIONIf forces acting on an aircraft move toward each other to squeeze the material, the stress is called compression. Compression is the opposite of tension. Tension is pull, and compression is push. Compression is the resistance to crushing produced by two forces pushing toward each other in the same straight line. For example, when an airplane is on the ground, the landing gear struts are under a constant compression stress.SHEARCutting a piece of paper with scissors is an example of a shearing action. In an aircraft structure, shear is a stress exerted when two pieces of fastened material tend to separate. Shear stress is the outcome of sliding one part over the other in opposite directions. The rivets and bolts of an aircraft experience both shear and tension stresses.BENDINGBending is a combination of tension and compression. For example, when bending a piece of tubing, the upper portion stretches (tension) and the lower portion crushes together (compression). The wing spars of an aircraft in flight are subject to bending stresses.TORSIONTorsional stresses result from a twisting force. When you wring out a chamois skin, you are putting it under torsion. Torsion is produced in an engine crankshaft while the engine is running. Forces that produce torsional stress also produce torque.VARYING STRESSAll structural members of an aircraft are subject to one or more stresses. Sometimes a structural member has alternate stresses; for example, it is undercompression one instant and under tension the next. The strength of aircraft materials must be great enough to withstand maximum force of varying stresses.SPECIFIC ACTION OF STRESSESYou need to understand the stresses encountered on the main parts of an aircraft. A knowledge of the basic stresses on aircraft structures will help you understand why aircraft are built the way they are. The fuselage of an aircraft is subject the fives types of stress—torsion, bending, tension, shear, and compression.Torsional stress in a fuselage is created in several ways. For example, torsional stress is encountered in engine torque on turboprop aircraft. Engine torque tends to rotate the aircraft in the direction opposite to the direction the propeller is turning. This force creates a torsional stress in the fuselage. Figure 4-2 shows the effect of the rotating propellers. Also, torsional stress on the fuselage is created by the action of the ailerons when the aircraft is maneuvered.When an aircraft is on the ground, there is a bending force on the fuselage. This force occurs because of the weight of the aircraft. Bending increases when the aircraft makes a carrier landing. This bending action creates a tension stress on the lower skin of the fuselage and a compression stress on the top skin. Bending action is shown in figure 4-3. These stresses are transmitted to the fuselage when the aircraft is in flight. Bending occurs because of the reaction of the airflow against the wings and empennage.When theaircraft is in flight, lift forces act upward against the wings, tending to bend them upward. The wings are prevented from folding over the fuselage by the resisting strength of the wing structure. The bending action creates a tension stress on the bottom of the wings and a compression stress on the top of the wings.CONSTRUCTION MATERIALSLEARNING OBJECTIVE: Identify the various types of metallic and nonmetallic materials used in aircraft construction.An aircraft must be constructed of materials that are both light and strong. Early aircraft were made of wood. Lightweight metal alloys with a strength greater than wood were developed and used on later aircraft. Materials currently used in aircraft construction are classified as either metallic materials or nonmetallic materials.METALLIC MATERIALSThe most common metals used in aircraft construction are aluminum, magnesium, titanium, steel, and their alloys.AlloysAn alloy is composed of two or more metals. The metal present in the alloy in the largest amount is called the base metal. All other metals added to the base metal are called alloying elements. Adding the alloying elements may result in a change in the properties of the base metal. For example, pure aluminum is relatively soft and weak. However, adding small amounts or copper, manganese, and magnesium will increase aluminum's strength many times. Heat treatment can increase or decrease an alloy's strength and hardness. Alloys are important to the aircraft industry. They provide materials with properties that pure metals do not possess.AluminumAluminum alloys are widely used in modern aircraft construction. Aluminum alloys are valuable because they have a high strength-to-weight ratio. Aluminum alloys are corrosion resistant and comparatively easy to fabricate. The outstanding characteristic of aluminum is its lightweight.MagnesiumMagnesium is the world's lightest structural metal. It is a silvery-white material that weighs two-thirds as much as aluminum. Magnesium is used to make helicopters. Magnesium's low resistance to corrosion has limited its use in conventional aircraft.TitaniumTitanium is a lightweight, strong, corrosion-resistant metal. Recent developments make titanium ideal for applications where aluminum alloys are too weak and stainless steel is too heavy. Additionally, titanium is unaffected by long exposure to seawater and marine atmosphere.Steel AlloysAlloy steels used in aircraft construction have great strength, more so than other fields of engineering would require. These materials must withstand theforces that occur on today's modern aircraft. These steels contain small percentages of carbon, nickel, chromium, vanadium, and molybdenum. High-tensile steels will stand stress of 50 to 150 tons per square inch without failing. Such steels are made into tubes, rods, and wires.Another type of steel used extensively is stainless steel. Stainless steel resists corrosion and is particularly valuable for use in or near water.NONMETALLIC MATERIALSIn addition to metals, various types of plastic materials are found in aircraft construction. Some of these plastics include transparent plastic, reinforced plastic, composite, and carbon-fiber materials.Transparent PlasticTransparent plastic is used in canopies, windshields, and other transparent enclosures. You need to handle transparent plastic surfaces carefully because they are relatively soft and scratch easily. At approximately 225°F, transparent plastic becomes soft and pliable.Reinforced PlasticReinforced plastic is used in the construction of radomes, wingtips, stabilizer tips, antenna covers, and flight controls. Reinforced plastic has a high strength-to-weight ratio and is resistant to mildew and rot. Because it is easy to fabricate, it is equally suitable for other parts of the aircraft.Reinforced plastic is a sandwich-type material (fig. 4-4). It is made up of two outer facings and a center layer. The facings are made up of several layers of glass cloth, bonded together with a liquid resin. The core material (center layer) consists of a honeycomb structure made of glass cloth.MaterialsHigh-performance aircraft require an extra high strength-to-weight ratio material. Fabrication of composite materials satisfies this special requirement. Composite materials are constructed by using several layers of bonding materials (graphite epoxy or boron epoxy). These materials are mechanically fastened to conventional substructures. Another type of composite construction consists of thin graphite epoxy skins bonded to an aluminum honeycomb core. Carbon fiber is extremely strong, thin fiber made by heating synthetic fibers, such as rayon, until charred, and then layering in cross sections.LEARNING OBJECTIVE: Identify the construction features of the fixed-wing aircraft and identify the primary, secondary, and auxiliary flight control surfaces.The principal structural units of a fixed-wing aircraft are the fuselage, wings, stabilizers, flight control surfaces, and landing gear. Figure 4-5 shows these units of a naval aircraft.NOTE: The terms left or right used in relation to any of the structural units refer to the right or left hand of the pilot seated in the cockpit.FUSELAGEThe fuselage is the main structure, or body, of the aircraft. It provides space for personnel, cargo, controls, and most of the accessories. The power plant, wings, stabilizers, and landing gear are attached to it.There are two general types of fuselage construction—welded steel truss and monocoque designs. The welded steel truss was used in smaller Navy aircraft, and it is still being used in some helicopters.The monocoque design relies largely on the strength of the skin, or covering, to carry various loads. The monocoque design may be divided into three classes—monocoque, semimonocoque, and reinforced shell.The true monocoque construction uses formers, frame assemblies, and bulkheads to give shape to the fuselage. However, the skin carries the primary stresses. Since no bracing members are present, the skin must be strong enough to keep the fuselage rigid. The biggest problem in monocoque construction is maintaining enough strength while keeping the weight within limits.Semimonocoque design overcomes the strength-to-weight problem of monocoque construction. See figure 4-6. In addition to having formers, frame assemblies, and bulkheads, the semimonocoque construction has the skin reinforced by longitudinal members.The reinforced shell has the skin reinforced by a complete framework of structural members. Different portions of the same fuselage may belong to any one of the three classes. Most areconsidered to be of semimonocoque-type construction.The semimonocoque fuselage is constructed primarily of aluminum alloy, although steel and titanium are found in high-temperature areas. Primary bending loads are taken by the longerons, which usually extend across several points of support. The longerons are supplemented by other longitudinal members known as stringers. Stringers are more numerous and lightweight than longerons.The vertical structural members are referred to as bulkheads, frames, and formers. The heavier vertical members are located at intervals to allow for concentrated loads. These members are also found at points where fittings are used to attach other units, such as the wings and stabilizers.The stringers are smaller and lighter than longerons and serve as fill-ins. They have some rigidity but are chiefly used for giving shape and for attachment of skin. The strong, heavy longerons hold the bulkheads and formers. The bulkheads and formers hold the stringers. All of these join together to form a rigid fuselage framework. Stringers and longerons prevent tension and compression stresses from bending the fuselage.The skin is attached to the longerons, bulkheads, and other structural members and carries part of the load. The fuselage skin thickness varies with the load carried and the stresses sustained at particular loca-tion.There are a number of advantages in using the semimonocoque fuselage.The bulkhead, frames, stringers, and longerons aid in the design and construction of a streamlined fuselage. They add to the strength and rigidity of the structure.The main advantage of the semimonocoque construction is that it depends on many structural members for strength and rigidity. Because of its stressed skin construction, a semimonocoque fuselage can withstand damage and still be strong enough to hold together.Points on the fuselage are located by station numbers. Station 0 is usually located at or near the nose of the aircraft. The other stations are located at measured distances (in inches) aft of station 0. A typical station diagram is shown in figure 4-7. On this particular aircraft, fuselage station (FS) 0 is located 93.0 inches forward of the nose.WINGSWings develop the major portion of the lift of a heavier-than-air aircraft. Wing structures carry some of the heavier loads found in the aircraft structure. The particular design of a wing depends on many factors, such as the size, weight, speed, rate of climb, and use of the aircraft. The wing must be constructed so that it holds its aerodynamics shape under the extreme stresses of combat maneuvers or wing loading.Wing construction is similar in most modern aircraft. In its simplest form, the wing is a framework made up of spars and ribs and covered with metal. The construction of an aircraft wing is shown in figure 4-8.Spars are the main structural members of the wing. They extend from the fuselage to the tip of the wing. All the load carried by the wing is taken up by the spars. The spars are designed to have great bending strength. Ribs give the wing section its shape, and they transmit the air load from the wing covering to the spars. Ribs extend from the leading edge to the trailing edge of the wing.In addition to the main spars, some wings have a false spar to support the ailerons and flaps. Most aircraft wings have a removable tip, which streamlines the outer end of the wing.Most Navy aircraft are designed with a wing referred to as a wet wing. This term describes the wingTRAILING EDGESPARSthat is constructed so it can be used as a fuel cell. The wet wing is sealed with a fuel-resistant compound as it is built. The wing holds fuel without the usual rubber cells or tanks.The wings of most naval aircraft are of all metal, full cantilever construction. Often, they may be folded for carrier use. A full cantilever wing structure is very strong. The wing can be fastened to the fuselage without the use of external bracing, such as wires or struts.A complete wing assembly consists of the surface providing lift for the support of the aircraft. It also provides the necessary flight control surfaces.NOTE: The flight control surfaces on a simple wing may include only ailerons and trailing edge flaps. The more complex aircraft may have a variety of devices, such as leading edge flaps, slats, spoilers, and speed brakes.Various points on the wing are located by wing station numbers (fig. 4-7). Wing station (WS) 0 is located at the centerline of the fuselage, and all wing stations are measured (right or left) from this point (in inches).STABILIZERSThe stabilizing surfaces of an aircraft consist of vertical and horizontal airfoils. They are called thevertical stabilizer (or fin) and horizontal stabilizer. These two airfoils, along with the rudder and elevators, form the tail section. For inspection and maintenance purposes, the entire tail section is considered a single unit called the empennage.The main purpose of stabilizers is to keep the aircraft in straight-and-level flight. The vertical stabilizer maintains the stability of he aircraft about its vertical axis (fig. 4-9). This is known as directional stability. The vertical stabilizer usually serves as the base to which the rudder is attached. The horizontal stabilizer provides stability of the aircraft about its lateral axis. This is known as longitudinal stability. The horizontal stabilizer usually serves as the base to which the elevators are attached. On many newer, high-performance aircraft, the entire vertical and/or horizontal stabilizer is a movable airfoil. Without the movable airfoil, the flight control surfaces would lose their effectiveness at extremely high altitudes.Stabilizer construction is similar to wing construction. For greater strength, especially in the thinner airfoil sections typical of trailing edges, a honeycomb-type construction is used. Some larger carrier-type aircraft have vertical stabilizers that are folded hydraulically to aid aircraft movement aboard aircraft carriers.FLIGHT CONTROL SURFACESFlight control surfaces are hinged (movable) airfoils designed to change the attitude of the aircraft during flight. These surfaces are divided into three groups—primary, secondary, and auxiliary.Primary GroupThe primary group of flight control surfaces includes ailerons, elevators, and rudders. The ailerons attach to the trailing edge of the wings. They control the rolling (or banking) motion of the aircraft. This action is known as longitudinal control.The elevators are attached to the horizontal stabilizer and control the climb or descent (pitching motion) of the aircraft. This action is known as lateral control.The rudder is attached to the vertical stabilizer. It determines the horizontal flight (turning or yawing motion) of the aircraft. This action is known as directional control.The ailerons and elevators are operated from the cockpit by a control stick on single-engine aircraft. A yoke and wheel assembly operates the ailerons and elevators on multiengine aircraft, such as transport andpatrol aircraft. The rudder is operated by foot pedals on all types of aircraft.Secondary GroupThe secondary group includes the trim tabs and spring tabs. Trim tabs are small airfoils recessed into the trailing edges of the primary control surface. Each trim tab hinges to its parent primary control surface, but operates by an independent control. Trim tabs let the pilot trim out an unbalanced condition without exerting pressure on the primary controls.Spring tabs are similar in appearance to trim tabs but serve an entirely different purpose. Spring tabs are used for the same purpose as hydraulic actuators. They aid the pilot in moving a larger control surface, such as the ailerons and elevators.Auxiliary GroupThe auxiliary group includes the wing flaps, spoilers, speed brakes, and slats.WING FLAPS.—Wing flaps give the aircraft extra lift. Their purpose is to reduce the landing speed. Reducing the landing speed shortens the length of the landing rollout. Flaps help the pilot land in small or obstructed areas by increasing the glide angle without greatly increasing the approach speed. The use of flaps during takeoff serves to reduce the length of the takeoff run.Some flaps hinge to the lower trailing edges of the wings inboard of the ailerons. Leading edge flaps are used on the F-14 Tomcat and F/A-18 Hornet. Four types of flaps are shown in figure 4-10. The plain flap forms the trailing edge of the airfoil when the flap is in the up position. In the split flap, the trailing edge of the airfoil is split, and the lower half is hinged and lowers to form the flap. The fowler flap operates on rollers and tracks, causing the lower surface of the wing to roll out and then extend downward. The leading edge flap operates like the plain flap. It is hinged on the bottom side. When actuated, the leading edge of the wing actually extends in a downward direction to increase the camber of the wing. Landing flaps are used in conjunction with other types of flaps.SPOILERS.—Spoilers are used to decrease wing lift. The specific design, function, and use vary with different aircraft. On some aircraft, the spoilers are long narrow surfaces, hinged at their leading edge to the upper surfaces of the wings. In the retracted positionthey are flush with the wing skin. In the raised position, they greatly reduce wing lift by destroying the smooth flow of air over the wing surface.SPEED BRAKES.—Speed brakes are movable control surfaces used for reducing the speed of the aircraft. Some manufacturers refer to them as dive brakes; others refer to them as dive flaps. On some aircraft, they're hinged to the sides or bottom of the fuselage. Regardless of their location, speed brakes serve the same purpose—to keep the airspeed from building too high when the aircraft dives. Speed brakes slow the aircraft's speed before it lands.SLATS.—Slats are movable control surfaces that attach to the leading edge of the wing. When the slat is retracted, it forms the leading edge of the wing. When the slat is open (extended forward), a slot is created between the slat and the wing leading edge. High-energy air is introduced into the boundary layer over the top of the wing. At low airspeeds, this action improves the lateral control handling characteristics. This allows the aircraft to be controlled at airspeeds below normal landing speed. The high-energy air that flows over the top of the wing is known as boundary layer control air. Boundary layer control is intended primarily for use during operations from carriers. Boundary layer control air aids in catapult takeoffs and arrested landings. Boundary control air can also be accomplished by directing high-pressure engine bleed air across the top of the wing or flap surface.FLIGHT CONTROL MECHANISMSThe term flight control refers to the linkage that connects the control(s) in the cockpit with the flight control surfaces. There are several types of flight controls in naval aircraft; some are manually operated while others are power operated.Manually operated flight control mechanisms are further divided into three groups—cable operated, push-pull tube operated, and torque tube operated. Some systems may combine two or more of these types.In the manually operated cable system, cables are connected from the control in the cockpit to a bell crank or sector. The bell crank is connected to the control surface. Movement of the cockpit controls transfers force through the cable to the bell crank, which moves the control surface.In a push-pull tube system, metal push-pull tubes (or rods) are used as a substitute for the cables (fig. 4-11). Push-pull tubes get their name from the way they transmit force.In the torque tube system, metal tubes (rods) with gears at the ends of the tubes are used. Motion is transmitted by rotating the tubes and gears.On all high-performance aircraft, the control surfaces have great pressure exerted on them. At high airspeed, it is physically impossible for the pilot to move the controls manually. As a result, power-operated control mechanisms are used. In a power-operated system, a hydraulic actuator (cylinder) is located within the linkage to assist the pilot in moving the control surface.A typical flight control mechanism is shown in figure 4-12. This is the elevator control of a lightweight trainer-type aircraft. It consists of a combination of push-pull tubes and cables.The control sticks in the system shown in figure 4-12 are connected to the forward sector by push-pull tubes. The forward sector is connected to the aft (rear ) sector by means of cable assemblies. The aft sector is connected to the flight control by another push-pull tube assembly.LANDING GEARBefore World War II, aircraft were made with their main landing gear located behind the center of gravity. An auxiliary gear under the fuselage nose was added. This arrangement became known as the tricycle type of landing gear. Nearly all present-day Navy aircraft are equipped with tricycle landing gear. The tricycle gear has the following advantages over older landing gear:More stable in motion on the groundMaintains the fuselage in a level position Increases the pilot's visibility and controlMakes landing easier, especially in cross windsFigure 4-13.—Typical landing gear system.The landing gear system (fig. 4-13) consists of three retractable landing gear assemblies. Each main landing gear has a conventional air-oil shock strut, a wheel brake assembly, and a wheel and tire assembly. The nose landing gear has a conventional air-oil shock strut, a shimmy damper, and a wheel and tire assembly.The shock strut is designed to absorb the shock that would otherwise be transmitted to the airframe during landing, taxiing, and takeoff. The air-oil strut is used on all naval aircraft. This type of strut has two telescoping cylinders filled with hydraulic fluid and compressed air or nitrogen. Figure 4-14 shows the internal construction of one type of air-oil shock strut.The main landing gear is equipped with brakes for stopping the aircraft and assisting the pilot in steering the aircraft on the ground.The nose gear of most aircraft can be steered from the cockpit. This provides greater ease and safety on the runway when landing and taking off and on the taxiway in taxiing.ARRESTING GEARA carrier-type aircraft is equipped with an arresting hook for stopping the aircraft when it lands on the carrier. The arresting gear has an extendible hook and the mechanical, hydraulic, and pneumatic equipment necessary for hook operation. See figure 4-15. The arresting hook on most aircraft releases mechanically, lowers pneumatically, and raises hydraulically.CATAPULT EQUIPMENTCarrier aircraft have built-in equipment for catapulting off the aircraft carrier. Older aircraft had hooks on the airframe that attached to the cable bridle. The bridle hooks the aircraft to the ship's catapult. Newer aircraft have a launch bar built into the nose landing gear assembly. See figure 4-16. The holdback assembly allows the aircraft to be secured to the carrier deck for full-power turnup of the engine prior to takeoff. For nose gear equipment, a track attaches to the deck to guide the nosewheel into position. The track has provisions for attaching the nose gear to the catapult shuttle and for holdback.NOTE: The holdback tension bar separates when the catapult is fired, allowing the aircraft to be launched with the engine at full power.ROTARY-WING AIRCRAFTLEARNING OBJECTIVE: Identify the construction features of the rotary-wing aircraft and recognize the fundamental differences between rotary-wing and fixed-wing aircraft.Within the past 20 years, helicopters have become a reality, and are found throughout the world. They perform countless tasks suited to their unique capabilities.A helicopter has one or more power-driven horizontal airscrews (rotors) to develop lift and propulsion. If a single main rotor is used, it is necessary to employ a means to counteract torque. If more than one main rotor (or tandem) is used, torque is eliminated by turning each main rotor in opposite directions.The fundamental advantage the helicopter has over fixed-wing aircraft is that lift and control are independent of forward speed. A helicopter can fly forward, backward, or sideways, or it can remain in stationary flight (hover) above the ground. No runway is required for a helicopter to take off or land. For example, the roof of an office building is an adequate landing area. The helicopter is considered a safe aircraft because the takeoff and landing speed is zero, and it has autorotational capabilities. This allows a controlled descent with rotors turning in case of engine failure in flight.FUSELAGELike the fuselage of a fixed-wing aircraft, the helicopter fuselage may be welded truss or some form of monocoque construction. Many Navy helicopters are of the monocoque design.A typical Navy helicopter, the H-60, is shown in figure 4-17. Some of its features include a single main rotor, twin engine, tractor-type canted tail rotor, controllable stabilizer, fixed landing gear, rescue hoist, external cargo hook, and weapons pylons. The fuselage consists of the entire airframe, sometimes known as the body group.The body group is an all-metal semimonocoque construction. It consists of an aluminum and titanium skin over a reinforced aluminum frame.LANDING GEAR GROUPThe landing gear group includes all the equipment necessary to support the helicopter when it is not in flight. There are several types of landing gear on helicopters—conventional fixed (skid type), retractable, and nonretractable.Main Landing GearThe H-60's nonretracting main landing gear consists of two single axle, air/oil type of shock-strut assemblies that mount to the fuselage. Each is equipped with tubeless tires, hydraulic disc brakes, tie-downrings, drag braces, and safety switches. They are part of the lower end of the shock strut piston.Tail Landing GearThe H-60's tail landing gear is a nonretracting, dual wheel, 360-degree swiveling type. It is equipped with tubeless tires, tie-down ring, shimmy damper, tail-wheel lock, and an air/oil shock-strut, which serves as an aft touchdown point for the pilots to cushion the landing shock.MAIN ROTOR ASSEMBLYThe main rotor (rotor wing) and rotor head (hub assembly) are identical in theory of flight but differ in engineering or design. They are covered here because their functions are closely related. The power plant, transmission, drive-train, hydraulic flight control, and rotor systems all work together. Neither has a function without the other.Rotary WingThe main rotor on the H-60 (fig. 4-17) has four identical wing blades. Other types of helicopters mayhave two, four, five, six, or seven blades.Rotary-wing blades are made of titanium, aluminum alloys, fiber glass, graphite, honeycomb core, nickel, and steel. Each has a nitrogen-filled, pressurized, hollow internal spar, which runs the length of the blade. The cuff provides the attachment of the blade to the rotor hub. A titanium abrasion strip covers the entire leading edge of the spar from the cuff end to the removable blade tip faring. This extends the life of the rotor blade.The examples shown in figure 4-18 show other features—trim tabs, deicing protection, balance markings, and construction.Main Rotor Head/Hub AssemblyThe rotor head is fully articulating and is rotated by torque from the engines through the drive train andmain gearbox or transmission. The flight controls and hydraulic servos transmit movements to the rotor blades. The principal components of the rotor head are the hub and swashplate assemblies (fig. 4-19). The hub is one piece, made of titanium and sits on top of the rotor mast. Attaching components are the sleeve and spindles, blade fold components, vibration absorber, bearings, blade dampers, pitch change horns, adjustable pitch control rods, blade fold hinges, balance weights, antiflapping and droop stops, and faring.The swashplate consists of a rotating disc (upper), stationary (lower) portion with a scissors and sleeve assembly separated by a bearing. The swashplate is permitted to slide on the main rotor vertical driveshaft and mounts on top the main transmission. The entire assembly can tilt in any direction following the motion of the flight controls.flight controls to be transmitted to the rotary-wing blades. The sleeve and spindle and blade dampers allow limited movement of the blades in relation to the hub. These movements are known as lead, lag, and flap.Lead occurs during slowing of the drive mechanism when the blades have a tendency to remain in motion.Lag is the opposite of lead and occurs during acceleration when the blade has been at rest and tends to remain at rest.Flap is the tendency of the blade to rise with high-lift demands as it tries to screw itself upward into the air.Antiflapping stops and droop stops restrict flapping and conning motion of the rotary-wing head and blades at low rotor rpm when slowing or stopping.TAIL ROTOR GROUPThe directional control and antitorque action of the helicopter is provided by the tail rotor group.PylonThe pylon, shown in figure 4-20, attaches on the aircraft to the main fuselage by hinge fittings. These hinge fittings serve as the pivot point for the pylon to fold along the fuselage. Folding the pylon reduces the overall length of the helicopter, which helps for confined shipboard handling.The pylon houses the intermediate and tail rotor gearboxes, tail rotor drive shaft, cover, tail bumper, position/anticollision lights, hydraulic servos, flight control push-pull tubes/cables/bell cranks, stabilizer/ elevator flight control surface, some antennas, and rotary rudder assembly.Rotary Rudder HeadThe rudder head can be located on either side of the pylon, depending on the type of aircraft, and includessuch items as the hub, spindle, pitch control beam, pitch change links, bearings, and tail rotor blades.Change in blade pitch is accomplished through the pitch change shaft that moves through the horizontal shaft of the tail gearbox, which drives the rotary rudder assembly. As the shaft moves inward toward the tail gearbox, pitch of the blade is decreased. As the shaft moves outward from the tail gearbox, pitch of the blade is increased. The pitch control beam is connected by links to the forked brackets on the blade sleeves.Rotary Rudder BladesLike the blades on a main rotor head, the blades found on a rotary rudder head may differ, depending on the type of aircraft. Tail rotor blades may consist of the following components:Aluminum alloy, graphite composite, or titanium sparAluminum pocket and skin with honeycomb core or cross-ply fiber glass exteriorAluminum or graphite composite tip capROTARY RUDDER BLADEPITCH CHANGE LINKSPINDLEROTARY RUDDER HUBTAIL ROTORGEAR BOXPYLONPITCH CONTROL BEAMANf0420Figure 4-20.—Tail rotor group.4-18Aluminum trailing edge capAluminum or polyurethane and nickel abrasion leading edge stripAdditionally, rotary rudder blades may have deicing provisions, such as electrothermal blankets that are bonded into the blade's leading edge. or a neoprene anti-icing guard embedded with electrical heating elements.AIRCRAFT HYDRAULIC SYSTEMSLEARNING OBJECTIVE: Identify the components of aircraft hydraulic systems and recognize their functions.The aircraft hydraulic systems found on most naval aircraft perform many functions. Some systems operated by hydraulics are flight controls, landing gear, speed brakes, fixed-wing and rotary-wing folding mechanisms, auxiliary systems, and wheel brakes.Hydraulics has many advantages as a power source for operating these units on aircraft.Hydraulics combine the advantages of lightweight, ease of installation, simplification of inspection, and minimum maintenance requirements.Hydraulics operation is almost 100-percent efficient, with only a negligible loss due to fluid friction.However, there are some disadvantages to using hydraulics.The possibility of leakage, both internal and external, may cause the complete system to become inoperative.Contamination by foreign matter in the system can cause malfunction of any unit. Cleanliness in hydraulics cannot be overemphasized.COMPONENTS OF A BASIC HYDRAULIC SYSTEMBasically, any hydraulic system contains the following units:A reservoir to hold a supply of hydraulic fluid A pump to provide a flow of fluidTubing to transmit the fluidA selector valve to direct the flow of fluidAn actuating unit to convert the fluid pressure into useful workA simple system using these essential units is shown in figure 4-21.You can trace the flow of fluid from the reservoir through the pump to the selector valve. In figure 4-21, the flow of fluid created by the pump flows through the valve to the right end of the actuating cylinder. Fluid pressure forces the piston to the left. At the same time, the fluid that is on the left of the piston is forced out. It goes up through the selector valve and back to the reservoir through the return line.When the selector valve is moved to the position indicated by the dotted lines, the fluid from the pump flows to the left side of the actuating cylinder. Movement of the piston can be stopped at any time simply by moving the selector valve to neutral. When the selector valve is in this position, all four ports are closed, and pressure is trapped in both working lines.removes foreign particles from the fluid, preventing moisture, dust, grit, and other undesirable matter from entering the system.The pressure regulator (fig. 4-22) unloads or relieves the power-driven pump when the desired pressure in the system is reached. Therefore, it is often referred to as an unloading valve. With none of the actuating units operating, the pressure in the line between the pump and selector valve builds up to the desired point. A valve in the pressure regulator automatically opens and fluid is bypassed back to the reservoir. (The bypass line is shown in figure 4-22, leading from the pressure regulator to the return line.)NOTE: Many aircraft hydraulic systems do not use a pressure regulator. These systems use a pump thatautomatically adjusts to supply the proper volume of fluid as needed.The accumulator serves a twofold purpose.It serves as a cushion or shock absorber by maintaining an even pressure in the system.It stores enough fluid under pressure to provide for emergency operation of certain actuating units.The accumulator is designed with a compressed-air chamber separated from the fluid by a flexible diaphragm, or a removable piston.The pressure gauge indicates the amount of pressure in the system.The relief valve is a safety valve installed in the system. When fluid is bypassed through the valve to the return line, it returns to the reservoir. This action prevents excessive pressure in the system.Check valves allow the flow of fluid in one direction only. There are numerous check valves installed at various points in the lines of all aircraft hydraulic systems. A careful study of figure 4-22 shows why the two check valves are necessary in this system. One check valve prevents power pump pressure from entering the hand-pump line. The other valve prevents hand-pump pressure from being directed to the accumulator.HYDRAULIC CONTAMINATIONHydraulic contamination is defined as foreign material in the hydraulic system of an aircraft. Foreign material might be grit, sand, dirt, dust, rust, water, or any other substance that is not soluble in the hydraulic fluid.There are two basic ways to contaminate a hydraulic system. One is to inject particles, and the other is to intermix fluids, including water.Particle contamination in a system may be self-generated through normal wear of system components. It is the injection of contaminants from outside that usually causes the most trouble. Regardless of its origin, any form of contamination in the hydraulic system will slow performance. In extreme cases, it seriously affects safety.A single grain of sand or grit can cause internal failure of a hydraulic component. Usually, this type of contamination comes from poor servicing and fluid-handling procedures. For this reason, the highestlevel of cleanliness must be maintained when working on hydraulic components.Only approved fill stand units are used to service naval aircraft hydraulic systems. By following a few basic rules, you can service hydraulic systems safely and keep contamination to a minimum.Never use fluid that has been left open for an undetermined period of time. Hydraulic fluid that is exposed to air will absorb dust and dirt.Never pour fluid from one container into another.Use only approved servicing units for the specific aircraft.Maintain hydraulic fluid-handling equipment in a high state of cleanliness.Always make sure you use the correct hydraulic fluid.Contamination of the hydraulic system may be caused by wear or failure of hydraulic components and seals. This type of contamination is usually found through filter inspection and fluid analysis. Continued operation of a contaminated system may cause malfunctioning or early failure of hydraulic components.PNEUMATIC SYSTEMSLEARNING OBJECTIVE: Identify the components of aircraft pneumatic systems and recognize their functions.There are two types of pneumatic systems currently used in naval aircraft. One type uses storage bottles for an air source, and the other has its own air compressor.Generally, the storage bottle system is used only for emergency operation. See figure 4-23. This system has an air bottle, a control valve in the cockpit for releasing the contents of the cylinders, and a ground charge (filler) valve. The storage bottle must be filled with compressed air or nitrogen prior to flight. Air storage cylinder pneumatic systems are in use for emergencybrakes, emergency landing gear extension, emergency flap extension, and for canopy release mechanisms.When the control valve is properly positioned, the compressed air in the storage bottle is routed through the shuttle valve to the actuating cylinder.NOTE: The shuttle valve is a pressure-operated valve that separates the normal hydraulic system from the emergency pneumatic system. When the control handle is returned to the normal position, the air pressure in the lines is vented overboard through the vent port of the control valve.The other type of pneumatic system in use has its own air compressor. It also has other equipment necessary to maintain an adequate supply of compressed air during flight. Most systems of this type must be serviced on the ground prior to flight. The air
What are the main differences in the SpaceX's Falcon 9 Block 5?
(Caution: Long Post Ahead).It marked the transitional step of the Falcon 9 from prototype, to fully operational.A lot of people think that up until now, the Falcon 9 has been fully operational for several years. That is far from the truth. Legacy models such as the Block I to IV are all, one way or another, frameworks for the final evolution which is the Block V.To understand the differences, we have to go through the Block system implemented by SpaceX first. And since Block V is essentially the culmination of all of the best of the four previous blocks, you’ll get an insight into it as well in the process.‘Block’ is the denominator that SpaceX uses to identify the hardware with which a booster was built, or equipped with. Of course, the higher the Block number, the more advanced the booster would be.Each Block, before Block V all signifies major milestone in the history of the Falcon 9’s family:Block I was built to test and accomplish vertical landing, the task which B1019 - the first stage core that was used in ORBCOMM-2 mission in 21st of December, 2015 successfully completed.Block II was developed with the task of proving the prospect of re-using an orbital-grade launch vehicle. And this was completed by B1021 - launched and landed first on April 8th, 2016. And launched once more, as well as landed on the same date being March 30th, 2017.Block II also incorporated a few minor tweaks taken from Block I, which was a fix for the post-landing fire beneath the engines that’d leave the engines a bit too warm for the company’s taste. This still happens from time to time.Block III was a performance upgrade with stronger engines, which would mean higher efficiency. Once upgraded to Block III’s standard, a single core can output an additional 7,607 kN of thrust in comparison to older variants. The thing is that the Falcon 9 at the time was not entirely as powerful as the company had projected it could be. But they have to take it slow at the time, and the Block III was the first step toward that final thrust goal.Block IIIs are the most popular boosters for now. They’ve launched far more missions than any other series, and is the series that SpaceX re-use extensively.But this same eagerness for rapid re-use got them into troubles.SpaceX tried to speed up the time that fuels were loaded into the booster. The rapid loading forced the Liquid Oxygen (Which is used as an oxidiser) to solidify into solid-state Oxygen between the carbon-fibre outer layer and the Aluminium liners of the COPV (Composite Overwrapped Pressure Vessel).The layers are ‘glued’ or bonded together with a layer of epoxy.Long story short, the solid-state Oxygen caused the COPV to rupture, and due to its proximity with the main tank, also broke it. This causes LOX to flow uncontrolled to meet with the RP-1 below, and sparked an ignition inside of the vehicle.SpaceX modified their fuel loading procedure, and NASA also demanded that they redesigned the COPV immediately if they wished to have the Falcon 9 rated for human flight.Block IV came. And since the problems with the COPV was attributed to the fuel loading procedure, in the mean time that the COPV was redesigned, Block IV went ahead to take the Falcon 9’s thrust one notch further than Block III. Other than that, this version did not see much changes. Rather, it was meant to be the middle-man between Block III and the final Block V.Here come the Block V.Take all of the goods that every single thing I’ve mentioned above, and crammed it into one thing. You’ll have the Block V. Which was why I wrote that the Block V is an evolution of the Falcon 9.The most noticeable change is surely in the aesthetic department.Instead of an all-white coating, the Falcon 9 Block V’s inter-stage and landing legs are black.In opposition to User-10240581476198209742’s answer (Sorry, mate), his point on the previous white coating to make it looked ‘Sexier’ made me uncomfortable enough I have to write an answer about it.Previous Falcon 9’s were painted white not because they would look sexier. That white paint is a thermal coating.The white ‘paint’ is ablative cork, once met with high temperature, it will peel off.The landing legs not only are among the first components to suffer aerodynamic heating as the first stage plunges through the atmosphere to return to land, but they’re also the closest to the burning engines. Even though carbon fibre is capable of withstanding a lot of heat, they can only stand so much without support.As you can see, the bottom was singed and the outer layer that used to be pristine white was covered in soot.The same coating was also applied to the Aluminium grid fins, which, after flight, all peeled off from the heat.Furthermore, black paint will absorb much more heat that can easily turn uncontrollable.This is a historical lesson: In the past, a miniaturised version of the Saturn V which was used to test the vehicle’s prototype was found to overheat at spots where it was painted black. So more white paint was applied to the body, but black marks still remain to help ground control calculate the roll of the vehicle once it lifted off.That’s also the reason why most rockets are painted white.No, they wouldn’t make the interstage and the landing legs black without justification.And NO! Looking sexier is far from justifiable.The justification is that the black coating is a type of heat-resistant carbon fibre that’s most likely based on Creslan 61 (Polyacrylonitrile).The material was developed to replace the heavy and expensive white ablative. From what I’ve heard, it’s Pyron - a type of oxidised polyacrylonitrile fiber (OPF).Light, inherently flame-retardant, and heat-resistant that can withstand heat up to above 1,000 Centigrade without being damaged. This is a perfect response to the problem of the ablative cork peeling off from the fuselage while re-entering the atmosphere, as it increases cost of re-applying them if you wish to re-use the rocket.Then I heard you ask: “Okay … so why the interstage, too?”Look here.See the scorch marks?Also, throwback to the old picture of the old, Aluminium grid fin which was visibly damaged after it landed:See the scorch marks on the interstage?What happened was that the Falcon 9 was having its grid fins extended during re-entry - the hottest part of the journey.The grid fins create lift by manipulating the air flows weaving through its lattices, by rotating or raising, lowering the fins, you can control the direction the vehicle on which the fins are attached to.But this would also mean that, at supersonic speed regime, the grid fins would also create shock waves that would wash up, hit, and slide along the section of the interstage above it.This would create a lot of heat, almost equivalent to the heat rubbing off on the landing legs. So it also has to be applied the same Thermal Protection System (TPS) as the Octaweb and the legs. Thus, the odd painting scheme.The legs can also be retracted manually now instead of having to be removed and reset after each flights. This aligns well with the improved TPS applied onto the landing legs, and you can consider that the legs have now been ‘fully-reusable’.The new coating allows SpaceX to stop having to fret so much on repainting it, but also reduce labour necessary to fit the legs back into position.Another significant change available to the Block V is to the Octaweb - the structure supporting the nine Merlin engines which also acts as a heatshield to protect the entire booster while it’s on its way back to Earth.It used to be welded, but now it’s bolted.The old, welded Octaweb made it really difficult for technicians to swap it out since welding literally made the Octaweb part of the entire fuselage, and is more difficult to maintain due to the brittleness of the joints. After every flights, they have to re-check the welded joints for micro-cracks, and then re-apply the joint.Now that it’s bolted, it’s supremely easier to repair and maintain the Octaweb. Furthermore, integration with the Falcon Heavy is improved due to the swap-ability. In the FH’s design, the base is where mating clamps are at to connect the three cores together, along with one more pair at the top.The Octaweb for the Falcon Heavy cores are also strengthened to withstand the additional stress the thrust, along with the weight of the extra cores put on it. So making the Octaweb flexible to change is a great step toward fluent integration.For previous Falcon 9 iterations, the Octaweb bottom is protected against re-entry heat during the flight with a composite TPS constructed from a mixture of cork and PICA-X (The material that formed the heat shield of the Dragon capsule). But the presence of cork in general makes it difficult to maintain and repair, still.You can see the scorch marks and peeling done to the Octaweb here.So they swapped it out with Inconel - a nickel-chromium alloy that can maintain integrity within a range of temperature far more diverse than the old shield. This reduce minimum maintenance and cost further.In term of flight control, even though the Titanium grid fins have been experimented for months now on a few Falcon 9 flights, and the Falcon Heavy side-boosters were equipped with them. They weren’t in official service until now on the Block V.Instead of being coated in white cork like the Aluminium grid fins, which has a far lower temperature tolerance than Titanium. The Titanium fins were left unpainted due to the metal’s excellent heat resisting capability. And Titanium is also strong enough that Elon has said that they require no maintenance at all throughout their entire lifespan.These grid fins also have different architecture than the Aluminium ones, by which they are locally swept. Signified by the ‘Teeth’ that the Titanium grid fins have.The teeth allow them to have better lift-to-drag ratio and zero-lift total drag. Making the fins far more superior than the old ones and provide better control overall.Adhering to the thrust-improvement plans, the new Merlin 1-D installed on the Block V has 10% more thrust than the previous Block. The turbopump within the assembly is also strengthened to combat micro-fractures, which was a concern in the past for NASA.In addition, the engine is rated for human flight. Which is also part of the reason why I wrote beforehand that the Block V is the point where the entire Falcon 9 family matures.It has always been aimed at lifting humans into space, and with the Block V, that critical mission goal can finally be satisfied at last.Beside these major overhauls, the Block V also contains the redesigned COPV (Dubbed as ‘COPV 2.0’).You also can’t forget the new, recoverable Fairings (Fairing 2.0).The new fairings are lighter, slightly more spacious than 1.0 version, streamlined so it’s quicker to build, and finally, optimised for reuse. Armed with a parasail, computer, and a lighter weight, the Fairing 2.0 can land accurately into the waiting arms of catching boats to be dragged back to shore.Coupling with a few subtle changes such as hardened valves and internal modifications so that it can be reused several times without maintenance, you have the new, upcoming Block V in all of its overhauled glory!Once again, Block V is the series with the most significant changes to date, gathering all of the lessons and experiences learned from previous models, and implemented here into a complete, near-perfect version.Expected to fly several times per booster in comparison to older models (Rated only for 2–3 flights), and probably would be the one to take the first men to space on a SpaceX-built vehicle. I’m super hyped for the upcoming launch, and surely, I’d try to watch it live if I could.Its meaning may not be as large as the first landing on ground, at sea, the first re-use of a landed booster, or the Falcon Heavy. But it’s a great leap forward toward landing the first man on Mars for its eventual occupation.General Consensus: Hardware Mode.
- Home >
- Catalog >
- Life >
- Calendar Template >
- Birthday Calendar Template >
- birthday calendar maker >
- Design Of Composite Structures Towards Carbon Zero