How to Edit and sign Sample W2 Form Filled Out Online
Read the following instructions to use CocoDoc to start editing and completing your Sample W2 Form Filled Out:
- To start with, find the “Get Form” button and tap it.
- Wait until Sample W2 Form Filled Out is shown.
- Customize your document by using the toolbar on the top.
- Download your customized form and share it as you needed.
An Easy Editing Tool for Modifying Sample W2 Form Filled Out on Your Way
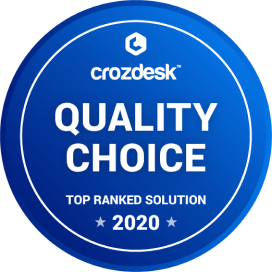
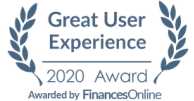
How to Edit Your PDF Sample W2 Form Filled Out Online
Editing your form online is quite effortless. You don't have to get any software via your computer or phone to use this feature. CocoDoc offers an easy tool to edit your document directly through any web browser you use. The entire interface is well-organized.
Follow the step-by-step guide below to eidt your PDF files online:
- Find CocoDoc official website on your device where you have your file.
- Seek the ‘Edit PDF Online’ option and tap it.
- Then you will visit here. Just drag and drop the PDF, or choose the file through the ‘Choose File’ option.
- Once the document is uploaded, you can edit it using the toolbar as you needed.
- When the modification is done, press the ‘Download’ icon to save the file.
How to Edit Sample W2 Form Filled Out on Windows
Windows is the most widespread operating system. However, Windows does not contain any default application that can directly edit document. In this case, you can get CocoDoc's desktop software for Windows, which can help you to work on documents productively.
All you have to do is follow the guidelines below:
- Get CocoDoc software from your Windows Store.
- Open the software and then import your PDF document.
- You can also import the PDF file from Dropbox.
- After that, edit the document as you needed by using the diverse tools on the top.
- Once done, you can now save the customized form to your computer. You can also check more details about the best way to edit PDF.
How to Edit Sample W2 Form Filled Out on Mac
macOS comes with a default feature - Preview, to open PDF files. Although Mac users can view PDF files and even mark text on it, it does not support editing. By using CocoDoc, you can edit your document on Mac quickly.
Follow the effortless instructions below to start editing:
- At first, install CocoDoc desktop app on your Mac computer.
- Then, import your PDF file through the app.
- You can attach the document from any cloud storage, such as Dropbox, Google Drive, or OneDrive.
- Edit, fill and sign your paper by utilizing this tool.
- Lastly, download the document to save it on your device.
How to Edit PDF Sample W2 Form Filled Out on G Suite
G Suite is a widespread Google's suite of intelligent apps, which is designed to make your workforce more productive and increase collaboration with each other. Integrating CocoDoc's PDF document editor with G Suite can help to accomplish work effectively.
Here are the guidelines to do it:
- Open Google WorkPlace Marketplace on your laptop.
- Seek for CocoDoc PDF Editor and download the add-on.
- Attach the document that you want to edit and find CocoDoc PDF Editor by clicking "Open with" in Drive.
- Edit and sign your paper using the toolbar.
- Save the customized PDF file on your device.
PDF Editor FAQ
How do I select aggregate for road construction?
In order to decide the suitability of the aggregate for use in pavement construction, following tests are carried out:Crushing testAbrasion testImpact testSoundness testShape testSpecific gravity and water absorption testBitumen adhesion testCrushing testOne of the model in which pavement material can fail is by crushing under compressive stress. A test is standardized by IS:2386 part-IV and used to determine the crushing strength of aggregates. The aggregate crushing value provides a relative measure of resistance to crushing under gradually applied crushing load. The test consists of subjecting the specimen of aggregate in standard mould to a compression test under standard load conditions (Figure 1). Dry aggregates passing through 12.5 mm sieves and retained 10 mm sieves are filled in a cylindrical measure of 11.5 mm diameter and 18 cm height in three layers. Each layer is tampered 25 times with at standard tamping rod. The test sample is weighed and placed in the test cylinder in three layers each layer being tampered again. The specimen is subjected to a compressive load of 40 tonnes gradually applied at the rate of 4 tonnes per minute. Then crushed aggregates are then sieved through 2.36 mm sieve and weight of passing material (W1) is expressed as percentage of the weight of the total sample (W2) which is the aggregate crushing value.A value less than 10 signifies an exceptionally strong aggregate while above 35 would normally be regarded as weak aggregates.Figure 1: Crushing test setupAbrasion testAbrasion test is carried out to test the hardness property of aggregates and to decide whether they are suitable for different pavement construction works. Los Angeles abrasion test is a preferred one for carrying out the hardness property and has been standardized in India (IS:2386 part-IV). The principle of Los Angeles abrasion test is to find the percentage wear due to relative rubbing action between the aggregate and steel balls used as abrasive charge.Los Angeles machine consists of circular drum of internal diameter 700 mm and length 520 mm mounted on horizontal axis enabling it to be rotated (see Figure 2). An abrasive charge consisting of cast iron spherical balls of 48 mm diameters and weight 340-445 g is placed in the cylinder along with the aggregates. The number of the abrasive spheres varies according to the grading of the sample. The quantity of aggregates to be used depends upon the gradation and usually ranges from 5-10 kg. The cylinder is then locked and rotated at the speed of 30-33 rpm for a total of 500 -1000 revolutions depending upon the gradation of aggregates.After specified revolutions, the material is sieved through 1.7 mm sieve and passed fraction is expressed as percentage total weight of the sample. This value is called Los Angeles abrasion value.A maximum value of 40 percent is allowed for WBM base course in Indian conditions. For bituminous concrete, a maximum value of 35 is specified.Figure 2: Los Angeles abrasion test setupImpact testThe aggregate impact test is carried out to evaluate the resistance to impact of aggregates. Aggregates passing 12.5 mm sieve and retained on 10 mm sieve is filled in a cylindrical steel cup of internal dia 10.2 mm and depth 5 cm which is attached to a metal base of impact testing machine. The material is filled in 3 layers where each layer is tamped for 25 number of blows. Metal hammer of weight 13.5 to 14 Kg is arranged to drop with a free fall of 38.0 cm by vertical guides and the test specimen is subjected to 15 number of blows. The crushed aggregate is allowed to pass through 2.36 mm IS sieve. And the impact value is measured as percentage of aggregates passing sieve (W2) to the total weight of the sample (W1).Figure 3: Impact test setupAggregates to be used for wearing course, the impact value shouldn't exceed 30 percent. For bituminous macadam the maximum permissible value is 35 percent. For Water bound macadam base courses the maximum permissible value defined by IRC is 40 percentSoundness testSoundness test is intended to study the resistance of aggregates to weathering action, by conducting accelerated weathering test cycles. The Porous aggregates subjected to freezing and thawing are likely to disintegrate prematurely. To ascertain the durability of such aggregates, they are subjected to an accelerated soundness test as specified in IS:2386 part-V. Aggregates of specified size are subjected to cycles of alternate wetting in a saturated solution of either sodium sulphate or magnesium sulphate for 16 - 18 hours and then dried in oven at 105 - 110°C to a constant weight. After five cycles, the loss in weight of aggregates is determined by sieving out all undersized particles and weighing. And the loss in weight should not exceed 12 percent when tested with sodium sulphate and 18 percent with magnesium sulphate solution.Shape testsThe particle shape of the aggregate mass is determined by the percentage of flaky and elongated particles in it. Aggregates which are flaky or elongated are detrimental to higher workability and stability of mixes.The flakiness index is defined as the percentage by weight of aggregate particles whose least dimension is less than 0.6 times their mean size. Test procedure had been standardized in India (IS:2386 part-I)Figure 4: Flakiness gaugeThe elongation index of an aggregate is defined as the percentage by weight of particles whose greatest dimension (length) is 1.8 times their mean dimension. This test is applicable to aggregates larger than 6.3 mm. This test is also specified in (IS:2386 Part-I). However there are no recognized limits for the elongation index.Figure 5: Elongation gaugeSpecific Gravity and water absorptionThe specific gravity and water absorption of aggregates are important properties that are required for the design of concrete and bituminous mixes. The specific gravity of a solid is the ratio of its mass to that of an equal volume of distilled water at a specified temperature. Because the aggregates may contain water-permeable voids, so two measures of specific gravity of aggregates are used: apparent specific gravity and bulk specific gravity.Apparent Specific Gravity, , is computed on the basis of the net volume of aggregates i.e the volume excluding water-permeable voids. Thuswhere, is the dry mass of the aggregate, is the net volume of the aggregates excluding the volume of the absorbed matter, W is the density of water.Bulk Specific Gravity, , is computed on the basis of the total volume of aggregates including water permeable voids. Thus (2)where, is the total volume of the aggregates including the volume of absorbed water.Water absorption, The difference between the apparent and bulk specific gravities is nothing but the water-permeable voids of the aggregates. We can measure the volume of such voids by weighing the aggregates dry and in a saturated, surface dry condition, with all permeable voids filled with water. The difference of the above two is . is the weight of dry aggregates minus weight of aggregates saturated surface dry condition. ThusThe specific gravity of aggregates normally used in road construction ranges from about 2.5 to 2.9. Water absorption values ranges from 0.1 to about 2.0 percent for aggregates normally used in road surfacing.Bitumen adhesion testBitumen adheres well to all normal types of road aggregates provided they are dry and free from dust. In the absence of water there is practically no adhesion problem of bituminous construction. Adhesion problem occurs when the aggregate is wet and cold. This problem can be dealt with by removing moisture from the aggregate by drying and increasing the mixing temperature. Further, the presence of water causes stripping of binder from the coated aggregates. This problems occur when bitumen mixture is permeable to water. Several laboratory tests are conducted to arbitrarily determine the adhesion of bitumen binder to an aggregate in the presence of water. Static immersion test is one specified by IRC and is quite simple. The principle of the test is by immersing aggregate fully coated with binder in water maintained at 40°C temperature for 24 hours. IRC has specified maximum stripping value of aggregates should not exceed 5%.SummaryAggregates influence, to a great extent, the load transfer capability of pavements. Hence it is essential that they should be thoroughly tested before using for construction. Not only that aggregates should be strong and durable, they should also possess proper shape and size to make the pavement act monolithically. Aggregates are tested for strength, toughness, hardness, shape, and water absorption.
How do you measure the workability of concrete?
Workability of concrete is the property of freshly mixed concrete which determines the ease and homogeneity with which it can be mixed, placed, consolidated and finished without segregation and bleeding.Workability can be measured with the help of following three tests :Slump apparatus test ( It is a field test and suitable for medium to high workability of concrete )Equipments Required for Concrete Slump Test:Mould for slump test, non porous base plate, measuring scale, temping rod. The mould for the test is in the form of the frustum of a cone having height 30 cm, bottom diameter 20 cm and top diameter 10 cm. The tamping rod is of steel 16 mm diameter and 60cm long and rounded at one end.Procedure for Concrete Slump Test:Clean the internal surface of the mould and apply oil.Place the mould on a smooth horizontal non- porous base plate.Fill the mould with the prepared concrete mix in 4 approximately equal layers.Tamp each layer with 25 strokes of the rounded end of the tamping rod in a uniform manner over the cross section of the mould. For the subsequent layers, the tamping should penetrate into the underlying layer.Remove the excess concrete and level the surface with a trowel.Clean away the mortar or water leaked out between the mould and the base plate.Raise the mould from the concrete immediately and slowly in vertical direction.Measure the slump as the difference between the height of the mould and that of height point of the specimen being tested.Slump Value Observation:The slump (Vertical settlement) measured shall be recorded in terms of millimeters of subsidence of the specimen during the test.Results of Slump Test on Concrete:Slump for the given sample= _____mmWhen the slump test is carried out, following are the shape of the concrete slump that can be observed:True Slump – True slump is the only slump that can be measured in the test. The measurement is taken between the top of the cone and the top of the concrete after the cone has been removed as shown in figure-1.Zero Slump – Zero slump is the indication of very low water-cement ratio, which results in dry mixes. These type of concrete is generally used for road construction.Collapsed Slump – This is an indication that the water-cement ratio is too high, i.e. concrete mix is too wet or it is a high workability mix, for which a slump test is not appropriate.Shear Slump – The shear slump indicates that the result is incomplete, and concrete to be retested.Vee- bee consistometer test ( It is a laboratory test and suitable for low to very low type of workability of concrete )Apparatus for Vee-Bee testThe Vee-Bee test apparatus consist of a Vee-Bee consistometer as per IS: 119 – 1959, The apparatus consists of a vibrating table which is supported and mounted on elastic supports. It also consists of a sheet metal slump cone, a weighing balance, cylindrical container, a standard iron tamping rod and trowels.Procedure of Vee-Bee Test on ConcreteThe procedure for conducting the Vee-Bee test are as follows:Step 1:Initially the sheet metal slump cone is placed inside the cylinder container that is placed in the consistometer. The cone is filled with four layers of concrete. Each concrete layer is one fourth the height of the cone. Each layer after pouring is subjected to twenty-five tamping with the standard tamping rod. The tamping is done with the rounded end of the rod.The strokes are distributed in uniform manner. This must be done in such a way theta the strokes conducted for the second and the subsequent layers of concrete must penetrate the bottom layers.Once the final layer has been placed and compacted, the concrete is struck off to make it in level with the help of a trowel. This makes the cone to be exactly filled.Step 2:After the preparation of the concrete cone, the glass disc attached to the swivel arm is moved and is placed on the top of the slump cone placed inside the cylindrical container. The glass disc has to be placed such that it touches the top of the concrete level and the reading is measured from the graduated rod.Step 3:Now the cylindrical cone is removed immediately by raising the cone slowly in the vertical direction. The transparent disc on the top of the concrete is placed down to the new position and the reading is determined.Step 4:The difference in the values measured from step 3 and step 4 will give the slump.Step 5:Now the electrical vibrator is switched on and at the same time we have to start the stop watch. The concrete is allowed to spread out in the cylindrical container. Until the concrete is remolded the vibration is continued. This stage is when the surface of the concrete becomes horizontal and the concrete surface completely adheres uniformly to the transparent disc.Step 6:The time required for complete remolding in seconds is recorded. This time in seconds gives us the measure of workability of the fresh concrete. This time is expressed in Vee-Bee seconds.Observation and Calculations in Vee-Bee TestInitial reading from the graduated rod, before unmolding (a) in mmThe final reading on the graduated rod after removing the mold (b) in mmSlump = a – b in mmThe time required for complete remolding in secondsHence the consistency of the concrete is measured in ———- vee-bee seconds.Compaction Factor test ( It is a laboratory test and suitable for low type of workability of concrete )ApparatusCompaction factor apparatus consists of trowels, hand scoop (15.2 cm long), a rod of steel or other suitable material (1.6 cm diameter, 61 cm long rounded at one end ) and a balance.SamplingConcrete mix is prepared as per mix design in the laboratory.Procedure of Compaction Factor Test on ConcretePlace the concrete sample gently in the upper hopper to its brim using the hand scoop and level it.Cover the cylinder.Open the trapdoor at the bottom of the upper hopper so that concrete fall into the lower hopper. Push the concrete sticking on its sides gently with the road.Open the trapdoor of the lower hopper and allow the concrete to fall into the cylinder below.Cut of the excess of concrete above the top level of cylinder using trowels and level it.Clean the outside of the cylinder.Weight the cylinder with concrete to the nearest 10 g. This weight is known as the weight of partially compacted concrete (W1).Empty the cylinder and then refill it with the same concrete mix in layers approximately 5 cm deep, each layer being heavily rammed to obtain full compaction.Level the top surface.Weigh the cylinder with fully compacted. This weight is known as the weight of fully compacted concrete (W2).Find the weight of empty cylinder (W).The test is sufficiently sensitive to enable difference in workability arising from the initial process in the hydration of cement to be measured.Each test, therefore should be carried out at a constant time interval after the mixing is completed, if strictly comparable results are to be obtained. Convenient time for releasing the concrete from the upper hopper has been found to be two minutes after the completion of mixing.Calculation of Compaction Factor ValueThe compaction factor is defined as the ratio of the weight of partially compacted concrete to the weight of fully compacted concrete. It shall normally to be stated to the nearest second decimal place.Compaction Factor Value= (W1-W) / (W2-W)Result of Compaction FactorCompaction factor of the concrete =The Compaction factor values ranges from 0.7 to 0.95.Thanks for A2A.Source : The Constructor - Civil Engineering Home for Civil Engineers
Is it necessary to know the impact value of the aggregates before road construction? If so, how is it measured?
Impact value test determines the amount of energy absorbed by a material during fracture. This absorbed energy is a measure of a given material's toughness and acts as a tool to study temperature-dependent brittle-ductile transition. It is to determine whether the material is brittle or ductile in nature.A material's toughness is a factor of its ability to absorb energy during plastic deformation. Brittle materials have low toughness as a result of the small amount of plastic deformation that they can endure.The following procedure is applied, to find out the impact value of aggregate:Aggregates for the test sample can be decided by passing it through 12.5 mm sieve and retained on 10 mm sieve.The sieved aggregates should be dried in an oven and then filled in a cylindrical steel cup and tamped with 25 strokes by temping rod.The test sample is filled in 3 layers and each layer is tamped for 25 numbers of blows.Metal hammer (weighing approx. 14 kg) is pre-arranged to drop with a free fall of 380mm. The test specimen is subjected to 15 numbers of blows each at not less than 1 second.The crushed aggregate is removed from the test specimen and sieve it through the 2.36 mm IS sieve.An impact value is measured as % of aggregates passed through the 2.36mm sieve (W2) to the total weight of the sample (W1).Aggregate impact value (The value of aggregate impact test) = (W1/W2)*100The value of aggregate impact test should not be more than 45% by weight of aggregates, used for concrete other than wearing surface. An impact value 35% is permissible for the bituminous macadam. Maximum permissible impact value for the water bound macadam is 40%. The price of aggregate impact testing machine is approximately Rs 4000 to 6000 in India.
- Home >
- Catalog >
- Business >
- Letter Template >
- Sample Sponsorship Letter >
- Athletic Sponsorship Letter >
- sample sponsorship proposal >
- Sample W2 Form Filled Out