A Useful Guide to Editing The A Range Of Clear Plastic Router Templates, For Use With Any
Below you can get an idea about how to edit and complete a A Range Of Clear Plastic Router Templates, For Use With Any conveniently. Get started now.
- Push the“Get Form” Button below . Here you would be brought into a dashboard that enables you to carry out edits on the document.
- Select a tool you desire from the toolbar that appears in the dashboard.
- After editing, double check and press the button Download.
- Don't hesistate to contact us via [email protected] For any concerns.
The Most Powerful Tool to Edit and Complete The A Range Of Clear Plastic Router Templates, For Use With Any
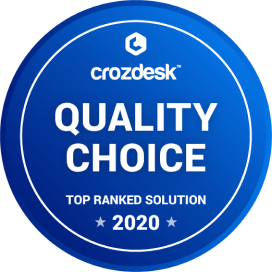
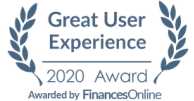
Modify Your A Range Of Clear Plastic Router Templates, For Use With Any Straight away
Get FormA Simple Manual to Edit A Range Of Clear Plastic Router Templates, For Use With Any Online
Are you seeking to edit forms online? CocoDoc can assist you with its comprehensive PDF toolset. You can get it simply by opening any web brower. The whole process is easy and quick. Check below to find out
- go to the CocoDoc's online PDF editing page.
- Import a document you want to edit by clicking Choose File or simply dragging or dropping.
- Conduct the desired edits on your document with the toolbar on the top of the dashboard.
- Download the file once it is finalized .
Steps in Editing A Range Of Clear Plastic Router Templates, For Use With Any on Windows
It's to find a default application able to make edits to a PDF document. Luckily CocoDoc has come to your rescue. View the Manual below to know ways to edit PDF on your Windows system.
- Begin by downloading CocoDoc application into your PC.
- Import your PDF in the dashboard and conduct edits on it with the toolbar listed above
- After double checking, download or save the document.
- There area also many other methods to edit PDF for free, you can check this article
A Useful Handbook in Editing a A Range Of Clear Plastic Router Templates, For Use With Any on Mac
Thinking about how to edit PDF documents with your Mac? CocoDoc is ready to help you.. It enables you to edit documents in multiple ways. Get started now
- Install CocoDoc onto your Mac device or go to the CocoDoc website with a Mac browser. Select PDF form from your Mac device. You can do so by clicking the tab Choose File, or by dropping or dragging. Edit the PDF document in the new dashboard which encampasses a full set of PDF tools. Save the content by downloading.
A Complete Handback in Editing A Range Of Clear Plastic Router Templates, For Use With Any on G Suite
Intergating G Suite with PDF services is marvellous progess in technology, able to simplify your PDF editing process, making it quicker and more cost-effective. Make use of CocoDoc's G Suite integration now.
Editing PDF on G Suite is as easy as it can be
- Visit Google WorkPlace Marketplace and find out CocoDoc
- establish the CocoDoc add-on into your Google account. Now you are able to edit documents.
- Select a file desired by pressing the tab Choose File and start editing.
- After making all necessary edits, download it into your device.
PDF Editor FAQ
What tools do I need to start practicing the skill of carpentry?
HERE ARE ALL THE HAND AND POWER TOOLS needed to start practising the skill of carpentry.If you know of at least, all of these carpenter tools, then you will be in a better position to select the essential equipment for your particular learning/building projects. Good all-round skilful carpenters will require nearly all of these tools.CARPENTRY TOOLS AND EQUIPMENTFrom a publication as recent as 2014.Open, Government/Educational publication.(Edited to fully and simply answer this Quora question).Types of hand toolsHand tools can be divided into categories, each with a specific function or purpose.In this section, you’ll look at tools in the following categories:measuring and marking outsawsimpellingplaneschiselsshapingboringholding and supportingsetting outleveling.Retractable tape measureRetractable tape measures have a built‑in coil spring which automatically retracts the blade into the casing when it’s released.They’re used mostly by site carpenters but can also be useful on larger joinery projects. There are a variety of sizes available but the most common are 5–7.5 m.Retractable tape measureWind‑up tape measureWind‑up tape measures are used for measuring long distances, eg when setting out, buildings.Their blades can be made of steel, plastic or linen and they are available in a variety of sizes (20–100 m). Wind‑up tapes are retracted manually.Steel ruleSteel rules are used mostly in joinery workshops, rather than on building sites but are useful for a range of carpentry work. They are generally available in lengths from 150 mm to 1 m.Scale ruleScale rules are used by carpenters to convert measurements between working (scaled) drawings and the actual dimensions of a project, without having to resort to any mathematical calculations.The scale will depend on the type of drawing being used, but the most common scales are the following:• 1:500 for large site plans• 1:200 for suburban house blocks• 1:100 for floor plans and elevations• 1:20, 1:10, 1:5 and 1:2 for smaller details.Folding ruleFolding rules are used mostly in joinery workshops. They can be made from hardwood or plastic and are generally available in 1 m lengths.Markings are placed at 1 mm, and numbers are written every 10 mm. These days, folding rules have been largely replaced by retractable tape measures and steel rules.Marking out toolsAs you measure materials, you mark the cutting points, lines, and angles.Marking out tools include squares, bevels, and gauges which are used to determine the angles and straight edges required, and pencils, spurs, and knives that create the actual marks.Squares and bevelsSquares and bevels are used by carpenters to mark guide lines on timber at an angle. The square or bevel a carpenter chooses to use usually depends on the angle required for the cut.Try squareTry squares are used to mark out lines at 90° to the face and/or edge of a piece of timber. They consist of two parts:• the ‘stock’ which is held against the side of the timber to position the square• the ‘blade’ which provides a straight edge to draw the lines.Try squares are precision tools used mostly in joinery workshops where tasks requiregreater accuracy or finer detail.Note: In carpentry, the term ‘square’ is often used to describe a line that is at a 90° angle to another surface. If a line or angle is described as ‘out of square’, it means that it is not exactly 90°.Mitre squareMitre squares are similar to try squares in that they have a stock and a blade; however, the blade on a mitre square projects from both sides of the stock to form angles of 45° and 135°, allowing a carpenter to mark out lines on timber at these angles.Mitre squares are used mostly in joinery workshops.Try/mitre squareMostly used in joinery workshops, this square is a combination of the try square and the mitre square. While this tool can be used to mark out an accurate line at 90° to the face/edge of a piece of timber, the top inside corner of the stock is cut to an angle of 45° for marking out lines at that angle.As the stock on the try/mitre square is slightly shorter in length (due to the 45° angle), you must take care to hold the stock firmly against the timber to avoid unintended movement.Combination squareCombination squares are used mostly for site carpentry and are very versatile.They can be used as a square or mitre square and have additional features such as a scribing spur and a spirit level that allow them to be used for a number of other functions.Sliding bevelSliding bevels are used to set out lines at any angle other than 90°. They have a stock with an adjustable blade which is set to the required angle and then locked with a thumb lever.Sliding bevels are used in both joinery workshops and site carpentry.GaugeGauges are used to scribe (scratch) lines along the length and/or width of timber. There are three types of gauges that you’ll use in carpentry, and each has been designed for a specific purpose.Marking gaugeMarking gauges are used to scribe a single line along the grain of the timber parallel to the edge. They consist of a stock, a beam and a spur (a pointed steel pin that creates the mark on the timber).Marking gauges are commonly used in both joinery workshops and site carpentry.Mortise gaugeMortise gauges are similar to marking gauges but they have two spurs instead of one. The distance between the double spurs can be adjusted to produce parallel gauge lines along the grain of the timber.Mortise gauges are used in joinery workshops to mark out mortise and tenon joints(a common 90° joint used for corners and framing), hence the name.Cutting gaugeCutting gauges are different from other gauges in that they’re designed to scribe a parallel line across the grain of the timber. They have a knife edge rather than a spur to allow the fibres in the grain to be severed.Cutting gauges can be used to mark out dovetail joints.Knives, scribes and pencilsThere are a variety of other tools you can use to mark, scribe or cut lines on timber to provide yourself with an accurate guideline to follow. These are an essential part of any carpenter’s toolkit.Marking knifeUsed mostly in joinery, marking knives are for cutting lines across the grain of timber.They can be very accurate when sharpened correctly (on one side only) but you must take care as lines cannot be easily erased if you make a mistake.ScribeSimilar to marking knives, scribes are also used to mark lines across the grain of timber. They have a sharpened point rather than a blade.They’re good for marking out where pencil lines may be hard to see, like on dark timber such as jarrah.Carpenter’s pencilCarpenter’s pencils are large pencils which contain rectangular lead. These pencils produce a thicker line than ordinary pencils and are ideal for marking out on sawn (rough) timber.Primarily used for site carpentry, their large size and shape make them unsuitable for use on joinery work where finer detail is required.The grade of the pencil is important – 2H grade pencils keep their sharpness for longer than softer grades, eg 2B. However, they create very fine lines that may be difficult to see on dark timber such as jarrah.SawsBecause of the availability of power saws these days, hand saws are being used less and less. However, carpenters still need to be proficient in the use of hand saws as there may not be a power source on some construction sites, or it may be quicker and more efficient to use a small handsaw for some jobs.Saws can be split into two groups:•traditional hand saws – used for larger timber sections•back saws – used for smaller detailed work.Traditional hand sawsHand saws are classified by their purpose, the length of their blade, and the size and shape of their teeth. Saw teeth size is measured by the number of teeth in a 25 mm length of blade.Rip sawRip saws have teeth with a square‑faced edge (like a chisel) and are used to cut timber along the grain, ie in the direction the fibres run.They’re the largest of the hand saws and are available in lengths up to 750 mm with 3–6 teeth per 25 mm.Crosscut sawAs the name suggests, crosscut saws are used to cut timber across the grain. Their bevelled teeth have a sharper cutting edge than a rip saw, allowing them to cut the fibres of the grain.They’re available in lengths up to 650 mm and have 6–8 teeth per 25 mm.Panel sawPanel saws are generally used to cut sheet materials such as plywood and particle board.They are available in lengths up to 550 mm and have 10 teeth per 25 mm.Back sawsBack saws have a steel or brass strip on the back of the saw which stiffens the blade so that straight lines can be cut more accurately. The three most commonly used back saws are the:• tenon saw• dovetail saw• gent’s saw.Tenon sawTenon saws, as the name suggests, were designed primarily to cut tenon joints.However, they can also be used to cut other types of carpentry joints, mouldings and beads (lengths of shaped timber).Tenon saws are generally 250 mm and 350 mm long and their teeth size is 10–14 teeth per 25 mm.Dovetail sawSmaller than the tenon saw and with finer teeth, the dovetail saw is primarily designed to cut dovetail joints used in joinery. However, they can also be used to cut mouldings and beads.Dovetail saws are generally between 200–250 mm long and their teeth size is 16–20 teeth per 25 mm.Gent’s sawGent’s saws are the smallest of the back saws and are used primarily for small detail work.They’re between 100–250 mm long with up to 32 teeth per 25 mm.Miscellaneous sawsThere are a number of other saws used by carpenters which have been designed forspecific purposes. These include the:• coping saw• hacksaw (including the junior hacksaw)• keyhole saw.Coping sawCoping saws have a very narrow blade which is tensioned by a spring frame.They’re used primarily to cut curves in timber, but they can also be used to cut away waste in joints like dovetails and bridles.Hacksaw and junior hacksawHacksaws are designed for cutting metals. Blades are available with14, 18, 24 or 32 teeth per 25 mm. The larger teeth are used for cutting softer metalssuch as aluminium and the finer teeth for harder or thinner metal sections.The junior hacksaw is a smaller version of the hacksaw and is used for cutting smaller metal components.Keyhole sawTraditionally, keyhole saws were designed for cutting keyholes in doors (as the name suggests).Sometimes referred to as a pad saw, they’re commonly used on site for cutting holes(for electrical sockets, light fittings, etc) in plasterboard walls and ceilings.Impelling toolsImpelling tools are those that drive or push something. They include hammers, mallets, screwdrivers and nail punches.HammersHammers are used for a variety of purposes in construction, including driving nails, pins and pegs into surfaces, and for demolition. They’re available in many shapes and sizes. The hammers the carpenter requires depend on the type of task being undertaken.Claw hammerThe main purpose of the claw hammer is to drive nails into timber with the claw on the back of the hammer used to extract nails.Claw hammers are available with timber, steel or fibreglass handles. Timber‑handled hammers are best suited to joinery work and the stronger steel and fibreglass types are more suited to on‑site use.Warrington hammerWarrington hammers are small and lightweight, and used for smaller nails such as panel pins (thin nails used for mouldings).They’re also known as tack hammers.Gympie or club hammerGympie hammers (also known as club or lump hammers) are heavier hammers with a variety of uses including driving small wooden pegs into the ground (for setting out buildings, etc), striking cold chisels and for light demolition work.SledgehammerSledgehammers are very heavy hammers used to drive large wooden pegs into the ground (for setting out buildings, etc) and for heavy demolition work.They generally have a longer handle than most hammers. This enables the operator to put more energy into the ‘swing’ motion for heavier work.ScrewdriversScrewdrivers are available in many different sizes with a variety of tips (the shape of the head). Screwdriver tips are sized and shaped to suit the drive of the screw. Traditional screwdriver tips include the following.The following newer screwdriver heads are becoming more commonly used.BradawlsBradawls are used to make small holes in wood (known as a pilot hole) or other materials to help the insertion of a nail or screw. They have a blade similar to that of a small slotted head screwdriver and a handle made from plastic or timber.The blade is placed across the fibres of the timber and twisted 90° which displaces the fibres, creating a hole.Miscellaneous impelling toolsCarpenters may also include the following impelling tools in their toolkits for more specialised tasks.MalletMallets are used primarily to strike wood chisels, although they can also be used to assemble joinery components such as window and door frames.Mallets have two main components – a head (generally hard rubber) and a shaft which is generally made from a hard‑wearing timber such as beech.Nail punch or centre punchNail punches are used (with a hammer) to drive the heads of nails below the surface of timber for a neater finish. The nail hole can then be filled before painting or varnishing.Similar to the nail punch is the centre punch which is used to punch a small mark into materials such as timber or steel before drilling. Its tip is more pointed than the nail punch’s.PincersPincers are used to remove small nails where the use of a claw hammer is restricted.The handle has a built‑in claw, which can be used to prise up the head of the nail to ease its removal.Wrecking bar or pinch barWrecking bars have a number of uses, including the removal of larger nails from timber and as a lever in the demolition or dismantling of a structure or building.PlanesDespite the widespread use of electrical power planes these days, no carpenter’s toolkit is complete without at least one or two hand planes.Hand planes fall into two major categories – bench planes and block planes. The difference is the direction of the bevel of the cutting iron (the part of the plane that does the planing).• On bench planes, the bevel always faces down.• On block planes, the bevel always faces up.The angle of the cutting iron means that bench planes are designed to plane with the grain (the direction of the fibres in the timber), while block planes are designed to plane end grain or against the grain of the timber.Bench planesThere are three types of bench planes you’ll use most frequently, as shown here.The size of the plane and its shape affect the function each plane can perform.Block planesBlock planes are used for cutting rather than smoothing. The three most common types you’ll use are shown here.Specialist planesSome jobs will require the use of a specialist plane. Three types of specialist planes are shown here.Router plane (Granny’s tooth)The router plane is designed to clean out the bottoms of trenches such as housing joints and grooves. It’s also known as a ‘granny’s tooth’ because of its distinctive narrow cutting blade.Router planes are rarely used these days, as the hand router has been replaced by the electric router.ChiselsChisels, like planes, are designed to remove timber using a sharp cutting edge. There are several types of chisels and each has been designed to suit particular tasks.They’re available in a range of sizes, depending on the type; however, common width sizes are 6 mm, 10 mm, 13 mm, 19 mm and 25 mm.Firmer chiselParing chiselParing chisels can be either of the firmer or the bevelled edge type; however, the blade is much longer – approximately 175 mm – enabling it to be used to pare (chisel) long housings such as those found in stair or shelf construction.Cold chiselAlthough cold chisels are not woodworking tools, most carpenters will have one in their toolkit.They’re used with a mallet to chip away bricks, concrete and masonry.Shaping toolsShaping tools are usually used to finish or clean up shaped surfaces. They let you make fine changes to the size and shape of articles created in a variety of materials including timber, metal, plastic and gypsum (plasterboard).FileRaspRasps are coarse files with sharp, raised, pointed teeth. As they have larger clearancebetween teeth, they’re usually used on softer, non‑metallic materials such as timber.SurformSurforms are a cross between a plane and a rasp, and are used mostly to plane the edges of plasterboard. They consist of a steel strip with holes punched out with the rim of each hole sharpened to form a cutting edge. The strip is mounted in a carriage or handle.SpokeshaveSpokeshaves are similar to planes and have short soles that enable them to workon concave (curving in) and convex (curving out) surfaces. They’re used for the final working and cleaning‑up of curved edges. Spokeshaves should be pushed rather than pulled.There are two types of spokeshave:• flat soled which can be used for planing narrow edges and convex curves• round soled for convex curves.Boring toolsBoring tools are used to bore or drill holes in materials such as timber, metal and plastic. With the increasing availability of portable power tools, particularlybattery‑powered drills, the use of manual boring tools like hand drills and ratchet braces is becoming less common. However, they are still a useful addition to any carpenter’s toolkit, as there may be occasions when there is no power source available.Ratchet braceRatchet braces (also known as sweep or bit braces) are very useful, versatile tools which can be used to drill holes anywhere, as they do not need electricity to power them.They rely solely on applied pressure and the turning of a handle. The brace has abuilt‑in ‘ratchet’ which enables it to be used in tight corners or confined spaces.Auger bitAuger bits have a central threaded worm which draws the bit into the wood, while the spur on the cutters scribe the cut which outlines the hole.Sash clampSash cramps consist of a straight steel bar with a fixed head at one end and anadjustable slide at the other.They’re generally used in pairs in the final assembly of joinery work to provide the pressure required to hold the joints on frames together until they’re secured by either wedges or the setting of adhesive.G clamps are general purpose clamps used to clamp items before and after assembly. Their name comes from the shape of the clamp which has a curved frame and straight screw head resembling the letter ‘G’.F clamp or quick‑release clampThe F clamp (also known as a quick‑release clamp) also takes its name from its shape. The F clamp is similar to a G clamp, but it has a wider opening capacity (throat).F clamps are ideal for clamping timber to a workbench or saw stool, or temporarily holding items such as kitchen cabinets together before a more permanent fixing can be made.Speed clampSpeed clamps are modern clamps, available in a variety of types that have a ‘trigger’ action so that they can be operated with one hand.They are faster to apply than traditional cramps, but don’t yield as much pressure, so they’re generally not suitable for jobs where you need a tight‑hold clamp. Speedclamps are also used for holding items together temporarily before a more permanentfixing can be made.Bench holdfastThe bench holdfast (or bench clamp) is used for clamping jobs to the workbench when you’re sawing, cleaning up and finishing. The leg of the holdfast fits into a hole in the workbench top.Floorboard clampFloorboard clamps are specialised tools used for clamping floorboards tightly together before they’re fixed permanently in position. The toothed cams at the bottom of the clamp grip the floor joist and the jaw at the front pushes the boards up tight when the handle is turned. Floorboard clamps are usually used in pairs.ViceVices are holding devices that are fixed in position on the side of a workbench. They’re used to hold timber securely, allowing you to use both hands when completing tasks such as sawing, chiselling, planing, sanding or filing.Bench hookBench hooks are simple holding devices which ‘hook’ over the edge of the workbench or other surface, and are used to hold small timbers while they’re being cut to length. For safety reasons, it’s advisable to clamp the bench hook into the vice on the workbench.Saw stoolDoor blockDoor blocks are simple ‘home‑made’ devices used to hold a door steady when it’s being planed to size on site. They’re usually made from a one‑metre length of90 × 45 mm (or similar) timber, and have a cut‑out for the thickness of the door and an allowance for a wedge that’s used to secure the door in place.Setting out toolsStringlineStringlines are some of the oldest and most basic hand tools used in building and construction. They are typically used in the setting out of buildings to create a straight line between two points.Carpenters use stringlines to check that timber components (such as floor joists, wallframes and roof rafters) have been installed correctly and are in line with each other.Chalk lineChalk lines (also known as snap lines) are used in setting out for creating temporarystraight lines, usually over long distances, on floors, ceilings, walls, etc.They’re basically stringlines with chalk embedded into the string. The stringline is placed across the surface to be marked and pulled tight, then plucked or snapped sharply, causing the line to strike the surface and transfer the chalk onto it.This creates a straight line. You can buy powdered chalk of various colours to refill the outer casing. Be careful when using a chalk line in wet conditions, as the chalk can become damp and clog up the line.Plumb‑bobPlumb‑bobs (also known as plumblines) are heavy metal objects with a pointed tip attached to the end of a stringline. They’re used to transfer points vertically, eg from ceiling to floor, and for checking that a surface is plumb (upright). Plumb‑bobs can be very accurate, but they can also be awkward to use in windy conditions.Carpenter’s roofing squareRoofing squares, as the name suggests, are designed primarily for setting out angles for roofing components. However, when fitted with a fence across the blades, they can also be used for setting out stairs.They are often used in joinery and cabinet work to draw square lines and to check frames, cabinets, etc for ‘square’ (90°).Builder’s squareStar picketStar pickets are a type of fence post (also called a T‑post or Y‑post, depending on their cross‑sectional shape). They’re made of steel and can be used to support various types of wire, wire mesh or plastic barrier fencing mesh.They’re often used when setting out buildings to construct hurdles/profiles to mark the outside perimeters of a building. Another tool called a star picket driver – a steel cylinder with handles on each side – is used to drive star pickets into the ground.Levelling toolsSpirit levelSpirit levels are made up of a body (generally made from aluminium), with a sealed glass tube which is partially filled with ‘spirit’ and contains a bubble of air. The position of the bubble is used to indicate whether a surface is plumb (vertical) or level (horizontal).Line levelLine levels are miniature spirit levels which have a hook on each end. The hooks enable the line level to be suspended on a stringline and used to transfer datums from one point to another. The line level is not very accurate and is used mostly for checking falls in concrete paths.Water levelAs water finds its own level, the water level in its simplest form is a clear plastic tube filled with water which can be used to transfer datums/levels (heights on a construction site) from one point to another.They’re particularly useful when transferring datums from one room to another when there is no clear line of sight.Optical levelAn optical level in its simplest form is a telescope (usually with a magnification of around 20×) mounted on a swivelling base. A sausage level (or circular level) is fixed to the telescope, enabling it to be adjusted, so that it’s exactly level. The optical level is used along with a staff (a specially marked rule used to measure the difference in height between datums on a construction site).Laser levelThere are several types of laser levels available, and they have replaced optical levels to a certain extent. The types of laser level most used in building and construction are as follows.•Rotating – This type of laser level is like a miniature lighthouse. The laser projects a beam out from a rotating prism and sweeps around 360°, forming a horizontal plane. The speed of rotation can be altered from zero to very fast.•Aimable – This type of laser level projects a beam but it does not rotate automatically. Instead, the operator needs to aim the beam at the target with a remote control handset. Buttons on the handset allow the operator to move the laser beams to the desired position.•Continuous plane – In this type, the laser beam is reflected from an inverted cone at the top of the instrument. It spreads a continuous plane of laser light through 360°. Because of the low intensity of this type of laser, the beam is invisible to the eye and a receiver must be used to detect the laser.POWER TOOLSPower sawsPower saws are used by site carpenters and bench joiners to cut a variety of materials including timber, plywood, chipboard and MDF.There are three types of power saw:• portable circular saw• drop saw• reciprocating saw.Circular sawNo other power tool has given carpenters a greater advantage over old hand‑powered methods than the portable circular saw (also known as a skill saw). It’s widely usedon construction sites for cutting timber and sheet materials such as plywood and chipboard.The circular saw is used primarily for ripping and cross‑cutting, but it can also be adjusted to perform a number of other operations such as grooving, rebating and trenching as well as making bevelled and compound cuts.Drop sawDrop saws (also known as chop saws or mitre saws) are a variation of the portable power saw. They consist of a blade and a motor which is mounted onto a short portable bench. They are widely used by ‘second fixing’ carpenters (carpentry carried out after the plaster has been applied to the walls) for cutting skirting, architraves, etc.The cut is made by pulling a trigger on the handle and ‘dropping’ the saw blade down into the work piece. Most drop saws are fitted with a clamp for holding the timber against the fence. The blade can be set square to the fence or swivelled up to 45° on either side. It can also be tilted to produce bevelled and compound cuts.JigsawAlthough jigsaws cut more slowly than circular saws, they can cut curved shapes into materials such as timber, metal and plastic. They’re commonly found in joinery workshops but can also be useful on site for cutting holes in, for example, kitchen worktops for sinks.Most models now have a variable speed control so that you can select the best speed for the job. Fast speeds are more suitable for cutting timber and slower speeds for cutting metal. The base plate of a jigsaw can be tilted to allow bevelled cuts.The teeth of a jigsaw point upward, so the cutting is done during the up‑stroke. This can result in damage to the surface of the timber, especially on sheet materials such as plywood. If necessary, clearance must be allowed for the edges to be cleaned up afterwards.Sabre sawsA sabre saw is a heavier duty saw which can be used for cutting through timber, metal and plastic and is ideal for cutting sections from a framed wall for a door, window or air conditioner.Blades are available in various lengths and with various teeth sizes to suit different materials. The stroke of the blade is about 30 mm.Power sandersPower sanders have an abrasive surface and are used by site carpenters and bench joiners to shape and/or finish work. As with all power tools, they reduce the time and effort required to complete a task. Depending on the type of work and the required finish, carpenters use belt sanders or orbital sanders.Belt sanderBelt sanders are used both in the joinery workshop and on construction sites. They have two rollers, one of which is driven by the motor. A continuous belt passes over the rollers and is held flat on the job by a base plate (called a platen). The undriven roller can be tilted slightly from side to side, which allows the belt to be adjusted so that it ‘tracks correctly’ (remains central to the base).Belt sanders have the advantage of removing wood quickly, which makes them useful for flushing joints and removing defects. However, they’re not suitable for fine finishing or for use on thin veneers.Belts are available in several lengths and widths to suit the various models of power sanders on the market. Different grit grades are also available. Before buying replacement belts, the data label on the sander should be checked to establish the length and width of belt suitable for that model.Orbital sanderOrbital sanders (also known as finishing sanders) sand in a circular motion, and are used to achieve a fine, smooth finish on timber surfaces. They are not suitable for ‘flushing off’ joints or removing wood quickly. A reciprocating sander is very similar to the orbital sander but its motion is back and forth rather than circular.The base of the sander has a soft rubber pad and the abrasive paper is held to it by a spring clip. This paper can be bought in packs of pre‑cut pieces or cut to size from standard sized sheets or rolls. The base of the sander rotates in a circular motion at approximately 12 000 rpm.The circular motion of the abrasive paper can leave swirl marks on the timber surface, which may only become visible after you’ve stained or polished the timber. If a very fine finish is required, you should carry out a final sanding by hand in the direction of the grain.Power planesElectric planes are regularly used on construction sites for planing the edges of doors during the fitting process. They can also be used to perform operations such as chamfering (removing the corner of a piece of timber on an angle) and rebating (taking a square recess out of the corner of a piece of timber).Although electric planes vary from model to model, they are all very similar in appearance and have many of the same features.Routers and trimmersRouters and trimmers are versatile power tools which are widely used by site carpenters and bench joiners to cut and finish edges, and hollow out areas in material. They have taken the place of a range of hand‑operated planes such as moulding, grooving and rebating planes.Portable power routersThe portable power router is simply an electric motor on an adjustable base. A shaft with a chuck is connected to the motor and the chuck holds the cutters (usually known as bits). The depth of cut is consistent and set by adjusting the height of the base in relation to the motor.The motor speed in a portable power router can vary between 24–30 000 rpm. This means that, for a typical bit with two cutting edges, the cutter passes any given point 800–1000 times per second.Plunge routerThe base of a plunge router has a spring‑loaded mounting which allows the bit to be plunged (pushed down) into the timber. This is useful for forming a groove that doesn’t begin or end at the edge of the material. The height can also be locked so that the tool can be used as a normal router (with a set depth).Most routers are supplied with some standard accessories including fences, template guides and bits. Additional accessories such as templates for stair manufacture can be bought or made.Straight bitStraight bits cut grooves, trenches and rebates. They can be used to form:• housings for shelving and stair construction• grooves for drawer bottoms• rebates in doors and windows for plywood or glass.They’re available with different ends for forming a variety of shaped grooves such as those shown here.Edge‑forming bitEdge‑forming bits produce a shaped edge to timber or manufactured boards such as MDF.The bottom of the bit runs along the edge of the board and acts as a guide for the depth of cut. This guide can be a solid pilot or have a small wheel with a bearing race (ball bearing). The latter is preferred because the solid pilot revolves at the same speed as the cutter and can scorch (burn) the wood, especially soft woods such as pine.Some bits can be used to cut more than one shape either by altering the amount that the bit protrudes through the base or by using roller bearings of different diameter.Trimmer bitTrimmer bits have cutters which are exactly the same width as the ball bearing guide roller. They’re used for trimming sheet materials such as plywood and melamine after they’ve been glued down.Slip tongue bitSlip tongue bits are used for cutting grooves in the edge of boards mainly where two boards need to be joined at their edge, eg tongue and groove or biscuit joints.Pneumatic nail gunsPneumatic (air‑powered) nail guns are used widely in the construction industry to drive fixings such as nails and staples into building materials. Although there’s a wide variety of types and sizes of nail guns, they all work on a similar principle – when you pull the trigger, a pulse of compressed air operates a piston, pushing a plunger which punches the fixing into the material. It’s just a matter of choosing the right nail gun for the job.Nail guns operate with an air pressure of 500–800 kPa (kilopascals) or 70–120 psi (pounds per square inch). The air pressure is adjusted at the source to suit the job, eg hardness of the timber, length of nail.Nails, pins and staples are glued together into strips or coils which are loaded into the gun’s magazine. When you’re choosing nails or other fixings, it’s essential you make sure that they’re compatible with the design of the nail gun.While strips are standard in most nail guns, the advantage of coil magazines is that they can hold up to 250 or 300 nails (depending on nail size). This makes them suitable for situations where numerous nails are required, eg hanger straps, triple grips, decking, claddings.Larger guns have a muzzle bracket connected to the valve mechanism. The bracket must be pressed against something before the gun will fire. This safety device prevents the gun from firing accidentally.Portable power equipmentYou can carry out most carpentry tasks using a combination of hand, power or battery‑operated tools, and most construction sites will have a temporary electricity supply which you can use to power tools.However, there may be situations where there’s no electricity supply available or compressed air is required to power pneumatic tools – that’s when portable power equipment can be used as an alternative.Portable electricity generatorPortable electricity generators are often used on construction sites where mains powered electricity is not available. They can be powered by petrol, LPG or diesel and are used to supply 240 volt power to operate electrical powered tools and equipment.Pneumatic compressorThe pneumatic compressor is a device which compresses and stores air under pressure. It is used to operate nail guns, paint spraying equipment, sandblasters and small air tools.Compressors can be either a permanent fixture in a joinery workshop or a portable unit used for work on a construction site. They’re driven by a motor that can be powered by either petrol, LPG, diesel or electricity.Storage of tools, plant and equipmentProper storage of tools and equipment helps to protect them against weathering and theft. It also makes them easier to find when you need them and reduces the risk of injury to yourself, other workers or members of the public.Most people keep their tools, plant and equipment safe in a workshop or garage. Other ways of storing them are shown here.May I add two tools of my own.Tin snips.Impact driver.While both tools look relatively similar side by side and have many of the same functions, there are some distinct differences between the two.This article will compare the two tools and help you determine which one is best suited for your next project.What Is An Impact Driver?An Impact DriverYou probably already know what a power drill is and looks like, but what is an impact driver?An impact driver is a specifically engineered tool designed to do one job: drive screws. Not only does a cordless impact driver drive in screws, it does so with intense speed and power that you won’t find in a traditional power drill.An impact driver does not accept a keyless chuck, instead it uses a collet that uses hex-shanked driver bits. Impact drivers can drive even the longest and fattest screws in with efficiency, where a regular power drill may stall out.A drill (left) accepts many types of shapes. The impact driver only accepts hex bits.The cordless impact drill uses the powerful combination of bit rotation and hard hitting blows to bust through even the thickest or toughest of surfaces. Impact drivers can deliver up to two to three more times power than a traditional drill.Despite its intense power, the driver manages to be easy and comfortable to use. The concussive action of the driver transfers much of its power directly to the screw, not to your hand or wrist. This allows you to drive in screws with incredible force and accuracy without compromising your arm.Drill Vs Impact DriverAt first glance, you may not recognize the difference between a drill and an impact driver, however, there are many differences that allow them to stand apart.For starters, a traditional drill is usually a bit bigger than an impact driver. Drivers are typically smaller and more compact, although they pack a more powerful punch.A standard drill has an adjustable clutch which allows you to adjust the torque, whereas an impact driver does not. The adjustable clutch on a standard drill prevents fasteners from being overtightened and damage to the drilling surface.The head of a standard drill includes a keyed or keyless chuck. Impact drivers, on the other hand do not have a chuck, instead they have a collet that accommodates hex shanks. In order to withstand the force of an impact driver, impact-rated hex bits are required.The impact driver can deliver more power in quick burst, which results in more torque. This action happens automatically when the driver meets resistance. Cordless impact drivers typically come with one gear, however, there are more advanced models available that have up to three gears.Drill vs Impact Driver: The Pros and Cons of EachWhen you are determining which tool to use for your next home improvement or DIY project, it can be helpful to know the pros and cons of each tool. We break it down here for you:Now that you understand the differences between a traditional power drill and an impact driver, which one should you use for your next project? The answer to this question depends on what kind of project you are working on and for what purpose you need a drill.Standard power drills are primarily used for drilling holes and screwing in small fasteners. An impact driver is designed for screwing in large fasteners. Screws that are longer can be driven in much easier with an impact driver.A traditional drill is better suited for jobs that require precision. Considering an impact driver is not well suited for tasks that require precision, it should be used for jobs where the placement of the hole is not crucial, but extra torque is required.A cordless impact driver can easily blast through dense wood or metal, while a traditional power drill may be stopped in its tracks.You may also be interested in this related Quora answer.Where can I get free woodworking PDF books? Just click on links to immediately start reading any of these books, (Promise).The books I have found on the net free to read online.Where can I get a free woodworking PDF books?
What is a plunge router?
Best Plunge Routers to buy in 2021 | getroutertableSerious about fine woodworking and your desire to achieve the best possible finish? If yes, then the best plunge router is must include in your woodworking arsenal. Further, we know that theirs is no shortage of compact routers for performing routing job excellently.So it becomes a little challenging to choose the most suitable for them. Hence, we reviewed top-ten the most versatile plunge routers based on their high-quality, premium features and stunning performing capability for resolving this issue. Hopefully, you’ll like it and find the best one for your need.- Bosch Wood Router 1617EVSPKBosch Router 1617EVSPK is a superb deal if you are in search of a stable base plunge router. With a rugged design and aluminum material, construction stands among the most durable products in the market. Moreover, this mid-sized range router can handle any workload easily.The first top-quality feature it holds is its power generating system; it comes with a 2.25 horsepower motor with an AC motor. Hence, by using it, you can lessen the powertrain load during a startup. This best plunge router isn’t an exhausting experience you ever due to its versatile speed range with different settings.You can install it any time and fix the collet bit range like 1/4, 3/8, 1/2, or 8 millimeters. Secondly, its soft-grip handle helps you in maintaining a fixed speed throughout the cutting procedure. Plus, it has microfine plunge depth features that let you superior routing accuracy.Furthermore, due to the holding soft start feature and consistent working property speed, it is more comfortable than many other traditional plunge routers. A standard wooden base and a plunge base for more accurate and precise cuts make it outstanding in performance.Last, it comes in excellent used plunge routers that are best suitable for intermediate and advanced enthusiasts. And, its design lets you depth adjustment for high-quality cutting. You can also check the complete Bosch Router 1617EVSPK Review we featured here recently.PROSVariable speed motorMotor alignment arrowsRugged and sturdy designPlunge base cutsAccurate and precise cuttingRemovable chip shieldMore comfortable to useCONSScrews are weakIt doesn’t consist of a spindle lock- Dewalt DW618PK ReviewDewalt DW618PK is best known for its mid-range router speed feature. This router tool is best for both novice and professionals. The cam housing motor, sub-base, collets, and router bits are exceptional and play a leading role in its overall performance.The 2.25 peak HP motor carries several tasks efficiently; the cam lock feature of this steel motor makes depth adjustment and base changes quickly. Plus, a start feature lets you minimize torque and reduce the load on the powertrain and electrical current surge during the startup.Moreover, this router goes from 8,000 to 24,000 RPM; 8,000 RPM best suited with diameter and cutter bits, 24,000 RPM with plastics, laminates, and softwoods. You may adjust the speed depending on the project requirement. Further, its speed control feature maintains speed under the load and avoids twisting and burning incidents.With a depth of 360 micro-fine adjustment ring, it provides you an accurate depth of 1/64-inch increment excellently. Hence, you can perform secure and smooth operations up to 1.5inches of precise cutting. The dust-sealed switch collects almost 95% of the dust; this lets you superior visibility.Over-molded rubber handles give you the best comfort, control, and balance ever. Secondly, the cut-out channel of the motor makes it easier to line up with the locking needles. This top-quality router performed on both the even and facile plunge base makes it more valuable. And, we picked it due to its high-quality performing capability.PROSErgonomics gripsSpeed and power is adjustablePowerful steel motorToggle switchUltra-durable routerCONSOverheated quicklyLack of a centering tool- Porter-cable 693LRPKPorter-cable 693LRPK comes with the old design in the 690 models, but it still looks stunning. However, questions produce that what makes it perfect and upgradeable than its previous models. The answer is some exceptional features of this model make it perfect and comfortable in use.With 11 amps motor holding 27,500 RPM and 1 3/4 peak HP, it performs stunningly. You may adjust the depth with its easy fix base cam lever and micro-adjustment system. After the depth setting, you haven’t needed to worry more about moving around during working or cutting.Moreover, it holds six adjustable turret positions that keep your work precise up to 1/28 of an inch and easy cutting. This aluminum production router carries a total weight of 21.2 pounds that is a little bit heavy, but it doesn’t concern a lot due to its high working performance capability.Next, this sturdy built electric router provides you easy control, use and set up—Best-designed for performing mid-size and entry-level jobs efficiently. A dust cover feature protects it, and the sightline is guarded with plastic for enhancing your safety level.Overall, this Porter-cable 693LRPK is an outstanding router package that will last a long time for your fine woodworking. And its oval-shaped handle gives you more comfortable and excellent grip throughout working.PROSVery easy to use and setupEasy fix base cam leverHigh-performance motorAdjustable turret positionsSturdy built designA dust cover prevents from damagingAluminum construction provides extra durabilityCONSLack of variable speed dialHeavy to carry- Plunge Router Makita RP2301FC Electric BrakeAssuredly, the Makita router is a full-size plunge router that is big and heavy to some extent; however, it delivers superior performance. This trusted power tool consists of unique features that rank it in the selling market. You can perform your heavy-duty tasks with this easy to handle router.This router has a 15 Amp potent motor with 3.25 horsepower; hence you can do precise and accurate woodcutting with ease. Even you may use it for the most rigid materials. When it comes to speed control, it ranges from 9,000 to 22,000 RPM that is just outstanding. Despite being heavy, it is easy to control the router.Moreover, it doesn’t run at the chosen speed from its activation period. First, it starts at a lower rate, and then it accelerates slowly; this phenomenon makes easy of brutal cuts. It holds an electric brake that provides you safety and linear ball bearings for ultra-smooth plunge action.A two-finger switch, LED lights, and a lock-on trigger makes it easy to operate for different purposes proficiently. Plus, an added feature is a shaft lock that is the best outfit for easy and fast changes. This best router plunge can efficiently plunge through hard materials, and it is best suitable for industrial work.PROSA robust motorFull-size plunge routerLED lights for clear visibilitySpindle lock for bits changingEasy to control and useA safety toolA warranty productCONSLack of dust collectorReplacement parts aren’t found easily- Triton TRA001 RouterTriton TRA001 is an engineer-oriented plunge router and the best attributed to its durable design in the selling market. It comes in top-selling products with a 4.6 rating and 430 reviews. This high-quality router performs heavy-duty operations excellently due to high-grade steel manufacturing.With a robust motor of 3.5 HP, it performs incredibly excellently, and its blade rotated from a speed of 8000 to 21000 RPM. Its multi-function fences provide you extra control over accurate cuts. Even you can make small or tiny cuts easily with it if you are a skilled person in this profession.Automatic spindle lock makes it the top-selling product because it makes difficult tasks simpler while changing the router’s tip. Moreover, you can get excellent control regardless of working on softwood or hardwood. Aside from this top feature, Triton TRA001 also includes a single button switch and a micro winder for depth adjustments.Another part that makes it more valuable is adjusting the speed according to the cut you will make. Besides, this best plunge router consists of air vents that reduce dust ingestion by the router. A safety switch shutter lock system has forgotten your security concerns while working.This precise plunge router lets you detailed and accurate cuts so that you may use it for complex projects or tasks fearlessly. Furthermore, its stunning features make it best for those stuck to the table works and plunging for long hours of the day. And it is highly recommended by professional and expert woodworkers because of its best fit and useful features.PROSWell-designed for heavy-duty workVery smooth and easy startingSafety switch shutter lockRobust and durable motorAn automatic spindle lock systemSingle-button switchCONSBig and heavyNot suitable for light routing- Hitachi KM12VC RouterHitachi KM12VC is well-known for its durability and high-quality power tools. Even this model is considered as the best product of this brand for plunging. We have to clear that it holds several excellent features that make it different rest of the other traditional routers. Further, its stunning performance makes it an ideal choice for you.With a noise level of 79.7 decibels, it let you perform almost noiseless operations with less vibration. With a motor of 11 amps, electronic speed control, and two-stage motor release clamp features, don’t you think the right package is enough for fine woodworking? You can make load transitions and operate control cuts without any trouble with these features.All this lets you smooth operations and ease of use no matters you are performing a job on soft or hardwoods. Its nickel-plated housing feature offers you fine groove cutting, window cutting, trimming, shaping, chamfering, and pattern cutting. Hence, this tool is best-recommended for its versatility.Next, when it comes to depth adjustments, here this toughest plunge router to a new level. It’s easy to operate depth adjustments, and the thumb-release lever provides you accurate cuts. And it can accept 1/2 and 1/4 inch bits for different types of woodcutting. Ergonomically designed handles enhance controlling ability and accuracy over the plunge router.Last, it’s an aesthetically attractive tool station router, which provides you both versatility and functionality; hence you may use it for performing several various projects quickly. Well-designed with some additional features for acquiring comfort and benefits both at the same time.PROSPowerful and noiseless motorTwo-stage motor-release clampNo need for a batteryA versatile plunge routerErgonomically designedAccurate and precise cutsCONSThe plunge base is unstableAdjustment knobs are greasy- Festool Router 1400Festool offers quality products though they are expensive to some extent but not too expensive that you didn’t afford them. Festool router 1400 is specially designed to keep in various needs of fine woodworking. It’s the best competitor in the market due to holding unique features.The first most fascinating feature is its powerful motor of up to 2.3 HP. This motor lets you accurately cut through oak, beech, hickory, and other hardwood quickly. Hence, this electric router is more than any handheld router. Secondly, it holds a locking switch that offers power maintenance without keeping the trigger depressed.We are hundred percent sure about its excellent performance, and when you use it, you find how comfortable it is in controlling and handling. Moreover, ergonomically designed handles provide you great control over the router for long periods while working on hardwoods.Something more to consider in it is its spindle brake feature that lets the stopping of a bit within seconds, so you also feel secure and safe. Moreover, a chip deflector helps you in working with both corners and curves efficiently. It is customizable with multi-routing templates, a wide range of accessories, and an FS guide rail system.This powerful plunge router is perfect for mid-sized and heavy jobs equally. You can address several issues with its ergonomic design and make sure of accurate/fine woodworking.PROSIt’s a HEPA certified productExcellent user controlSpindle brake for quick and fast stopsComfortably handling and usingA versatile toolIt has a chip deflector featureCONSRelatively expensivePlastic protector makes visibility limited- Black and Decker RP250 RouterBlack and Decker RP250 is an entry-level plunge router, so it is the best wood router for beginners. It is less weak in terms of motor power than other routers, but it’s still a strong competitor due to holding many other stunning features. It smoothly drives and installs the different router bits for performing various tasks. This easy to install and use router has a package of incredible features in it.Knowing that it doesn’t hold a powerful motor then it is listed in the best plunge routers that come to your mind. The answer is that it carries all necessary functions, features, and accessories to look for fine woodworking.With two inches of accurate cutting depth, variable speed selector, this router makes it place in top-rated and top-selling products in the amazon market worldwide. It’s enough for ensuring its superb value and performance capability. Still, some other features also play a different role in considering and reviewing it in the best products list.A variable-speed selector offers you an 8,000 to 27,000 RPM range for performing versatile jobs, and this feature adds sophistication to your work. With a 10 amp quite good motor, it doesn’t let you down in performance, so without fear of harmful or inaccurate outcomes, you may choose it.The sturdy built metal construction of this plunge router made it durable. Thus you don’t need to care about its long-lasting work. Its performance capability matches with other top-listed plunge routers. It is a beautiful choice with a complete package of tool station routers within an eco-friendly budget.PROSDurably constructedA quite good motorExcellent performerVariable speed selectorEasy to set up and useLight in weightCONSIsn’t able to make straight cutLess protective- Metabo HPT M12V2 3.25-HP Plunge RouterMetabo HPT M12V2 is a bit of a beast that aims at professional carpenters and woodworkers. This great plunge router is built with high power full motor around a 15-amp and 3.25 HP. It is the most potent motor still yet in the market, and it has plenty of power to tackle the toughest timbers efficiently.Its broader variable speed range from 8,000 RPM to 21,000 RPM gives excellent accuracy in woodworking. The design makes it a joy to use, and the speed does work quickly in fewer periods. Besides, a speed control dial present on the handle lets you easily adjust speed settings according to the requirements or depending on the wood type.It is the best solution for those who are looking for cleaner, more simple, and depth adjustments on a broad level. Even you may adjust the depth by fractions of an inch or entirety. Metabo brand has tried to design something unique in the modern world; hence, you can use it and find it more beautiful than the others.You may perform the most challenging plunging tasks with ease, thanks to this powerful and uniquely designed router. Besides, the motor starts in a very gentle way; it reduces initial jerkiness and provides the best quality finish to your work. The electronic speed control feature is another added thing to this router that maintains a constant speed.Finally, its innovative adjustment knob works incredibly, makes slight adjustments, and accurately changes the plunge depth. Extra visibility provides you ultra-convenience while working in dark areas. You may convert it into a tablet form; it depends on your usage requirement.PROSQuality finish to your workElectronic speed controllerExtra visibilityInnovative adjustment knobUltra-high quality motorDelivers at excellence levelCONSLack of LED lightHeaviest router- DEWALT DWP611PK Plunge RouterDewalt DWP611PK another best router by the DEWALT brand. With its least expensive features and a perfect motor, you found it in the top-rated products quickly. Moreover, if you are looking for a modest router, this is ideal for saving cash. The nickel-plated housing property lets you fine window/groove cutting, shaping, trimming, and fine chamfering.It sounds simple, withholding several incredible features and best-known as a top-selling product. First, built-in LED lights; this pretty standard feature lets you clear woodworking with more accurate results or outcomes.You can use it as a plunge router or a fixed router simultaneously; hence it well-recognized as a two-in-one router. Its stellar reputation stands it different and unique from many other plunge routers. Quite an excellent handling power and grip make it a more reputable product. Moreover, its aluminum body ensures you that it is much sturdy and quite suitable for hardwoods.It gives you peace of mind with three years of warranty so that you can use it fearlessly. The adjustment ring lets you easily control router bits depth within 1/64-inches of changing. Moreover, the spindle lock button with a low-pressure system enables you easy and comfortable bit changing at any time.The 1.25 HP motor is quite suitable for handling lighter duty projects efficiently, such as routing small profiles, cutting door hinge profiles, and dovetails. Further, the router’s bit size may be varied from 16,000 to 27,000 RPM; hence, it provides you an incredible range of adjustability.PROSLED let you see what you donePlunge base easily installDurably constructed with aluminumA warranty productBest suitable for lighter-duty materialsOutstanding handling power/capabilityCONSIt only comes with a ¼-inches colletThe lower end (16,000 RPM) is relatively high
What different items have been re-made into tables?
The table is a basic piece of household furniture. It generally consists of a flat top that is supported by either a set of legs, pillars, or trestles. The top may be made of stone, metal, wood, or a synthetic material such as a plastic. Tables may be subdivided by any one of a number of criteria, the most basic of which is whether the table is a fixed table or a mechanical table. A fixed table has a top that does not move in any way to expand or reduce in size for storage. The tops on fixed tables can be quite sizable and may be supported by a single column or pedestal. Mechanical tables have tops or legs that move, fold, drop, or in some way may be reconfigured in order to save space or make them more flexible. Mechanical tables include drop leaf tables, tilting tables, or those with legs that fold up or collapse if a mechanism is unlocked.Tables are more commonly subdivided by other criteria such as the material from which they are made, the purpose for which they are constructed, the form they take, and the style of any added decoration. Style is an extremely important part of a table. The look of the table may vary as a result of many factors. These include changing stylistic preferences, advances in technology that make available different materials for the table or methods for its construction, and new table forms that are the result of new human activities or needs.Tables purchased in this country are most frequently mass-produced from wood and can be made with minimal cabinetmaking skill. American-made tables may be made from native hardwoods such as maple, oak, or alder, or soft woods such as pine. American tables may be manufactured unfinished meaning without any stain or sealer or may be purchased ready-to-use in standard or custom finishes. Some table manufacture takes place in the home; these are considered custom or specially made pieces of furniture that must be constructed by a cabinet maker.HistoryUntil about the sixteenth century, when decorative and stylistically distinctive furniture became very important, tables were less frequently found than either the chair or the chest (which held clothing as a chest of drawers does today). However, there were tables in the ancient world. Different cultures made them of different materials. Egyptian tables were of wood or stone and resembled pedestals. It is said the Assyrians made them of metal. Pompeii and Herculaneum populaces had tables made with supporting members of marble.Cathedrals in the Middle Ages used communion tables that stood on masonry or on a base of stone. Castles often included large, rectangular plank tables with the master of the castle in the center and the less important inhabitants or guests at right angles to him. More ordinary medieval tables that survive include simple wooden tables supported by plain side members. Early seventeenth century American tables were generally of the trestle type, with a plank top and vertical planks on the side. Some could be dismantled if more room was needed; many were just moved against the wall to provide space when the table was not in use.Decoration became very important to the wealthy about the sixteenth century as well. Stylish furniture was ornately carved and included turnings made on foot-pedal lathes. Until the mid-seventeenth century most furniture was constructed by joiners who made furniture much as they made houses, with pegs, mortise and tenon construction, and massive members for supporting the slab tops. In the later seventeenth and eighteenth century the cabinetmaker began making fine furniture, creating sculptural pieces that were veneered, carved, and expertly joined including the use of interlocked dovetailing for strength.In the early nineteenth century the machine enabled manufacturers to provide attractive furniture far less expensively. Wood was cut by water, steam, or electrical saws, machine sanded, machine incised and decorated, turned on machine lathes, and so forth. By 1890, all but the very poorest Americans could afford to purchase an inexpensive table and chairs. In the early twentieth century the table changed again, this time because new, unconventional materials were used in its construction such as laminate, plastic, and chipboard, making tables truly affordable for all. As new activities were enjoyed and embraced, tables changed form, too. Table forms that were invented in the past 200 years include the card tables, gaming tables, tea tables, dressing tables, diapering tables, and computer tables.Raw MaterialsRaw materials vary greatly according to the type of table under production. Unfinished pine table made in quantity in this country include pine planks that are called one-by-fours or one-by-sixes. (These are boards that were once truly 1 in [2.5 cm] thick by 4 in [10.1 cm] wide or 6 in [15 cm] wide but are now cut slightly smaller than that size today.) Other materials include water-resistant glue formulated from polyvinyl acetate. Hardware, including screws, vary according to the price point of the piece but are often steel. Most American table manufacturers are careful to obtain woods that are certified, meaning the manufacturer can prove that the trees were harvested legally from controlled forests grown specifically for the manufacture of furniture. Furthermore, furniture-grade wood is especially important in the construction of unfinished tables, in which the grain may not be covered with paint. Furniture-grade wood is virtually knot-free or clear; when there are small knots the company must be sure they can use the wood in a hidden area of the piece such as the back or inside a drawer. Drawer bottoms or sides may be of a plywood, engineered wood (pressed wood chips formed into sheet goods), or even masonite.DesignThe decoration and configuration of tables are fairly important in the unfinished furniture industry. Additive or incised decoration may be found on the table apron (a board which goes across the front of the table running from leg to leg and may hold the drawer front), or on the legs themselves. Painted decoration may be seen at any place on the table. The shape or form of table top, table legs, or the apron determines style and may be created by specialized machineryWhile the high-end manufacturers of ready-to-use furniture spend a great deal of time and money on the design of their furniture, the unfinished furniture generally provides basic forms to the consumer. The unfinished table manufacturer surely cares about selling an attractive table, but it is not likely of the most stylish or innovative table shown at the important furnishings markets. Most larger furniture firms have a design director on staff whose job is to ferret out new designs for their market and work with the production managers to create these styles economically. These larger firms haunt malls, study the shelter and fashion magazines, and perform some audience assessment of taste and style preferences.However, smaller firms, such as those who produce medium to low-price products, point out that unfinished goods may spend less money on the development of styles and decoration, preferring to offer basic tables and forms to the consumer. Some smaller firms may assign the task of developing new products and styles to the production manager. This manager works with staff designers to craft tables that can be manufactured using the equipment used in-house. Interestingly, some prefer to design tables for which parts can easily be interchanged, resulting in a wide array of products with little re-design. For example, a console table may have the same front and back apron and drawers as the coffee table but have a narrower top, sides, and longer legs. A Queen Anne-style coffee table may have cabriole (curved) legs while a Shaker-style coffee table may be identical except the legs are rectilinear and slightly tapered.Designers or production directors generally keep their eye on current styles, assessing what is leading the market and what trends are infiltrating the target market. Generally, when a new style or form is suggested for production, a team of directors, including the director of sales and marketing, the director of manufacturing, and in-house designers assess the viability of the new design. If the design is approved, the director of manufacturing and the designer works with an operator who uses a computer-based design and drafting system such as AutoCAD. This operator works with the design on a computer and then inputs that information into the computer in order to produce that product on computer-driven machines. All staff members work together to devise the best way to get the new table form through the system, especially vigilant that the costs of the new table will not exceed the price point of the intended market and that no new machinery or manufacturing expertise will be necessary to produce the new product.The new table must be made in prototype in order to evaluate how the product will go through the established system. In addition, the staff must physically examine the proposed new table for aesthetics and durability. The prototype is made using templates made on machines. Any changes to the prototype are made, the AutoCAD operator changes computer settings for templates, and the piece is ready for production once approved.The ManufacturingProcessThe pine boards come into the factory fairly rough but cut to predetermined lengths that are then cut to shorter lengths using a power saw. The wood must stay in a carefully temperature and humidity-controlled room or the wood may swell (too much humidity) or shrink (very dry) and the piece will have cracks when finished. Temperatures must stay in the range of 50-85°F (10-29°C).Workers gather up the pine lengths and spread water-resistant wood glue to the long edges of the planks where they join with other boards to make a table top. The planks are then clamped together with furniture clamps to ensure a tight bond and a sturdy top. Several dozens of the tops can be made at one time and must sit for at least one hour.The raw table tops are then sent to wide belt-driven sanders that sand the planks down to take away extreme roughness and splinters.Most tables have some sort of apron or vertical board just below the table top. The apron must be cut next. A computer numerically controlled (CNC) router cuts several aprons according to computer specifications. This router is especially suited to cutting sheet goods such as planks of wood. The shapes to be cut or routed are defined by the drawing programs such as AutoCAD. The information is transferred to a CAD/CAM program that allows the user to define the path of the router tool. When the tool path has been defined, the computer software allows a tap file to be made, which actually runs the tool over the wood or plank, cutting it into the desired shape. The router is able to create high quality routing and carving effects with uniform consistency and with very little wasted wood. The cut aprons are put into a cart and head to the assembly area.The board tops, now glued and sanded, are sent to the CNC router and cut to the desired shape as well as described above.The legs are shaped on a profiler. Before the legs are shaped an aluminum template must be cut on the CNC router. Once the template is cut, the metal template is put on the profiler, and a bearing guide follows the template in order to shape the table legs.Legs with special stylish feet such as a pad foot are put into a chucker which acts like a giant pencil sharpener, shaping the stylish feet. The table tops and legs are put into carts and are sent to the assembly area as well.If the table is to receive a drawer, then the front, sides, and bottom of the drawer are cut on the CNC router. The front is ofThe manufacturing of a medium-sized round table.The manufacturing of a medium-sized round table.pine, but the sides and the bottom of the drawer may be of inferior grade pine, plywood, or engineered wood. For the drawer front, a CNC router cuts a groove for the bottom and sides that will be inset into the back face of the drawer. The face is then flipped over, the grooves receive a coating of waterproof glue, and the bottom and sides are inserted into these tracks and may be nailed together using an automatic nailer for additional stability. The table is now ready for assembly.Many unfinished furniture manufacturers do not ship their tables assembled as the shipping price increases wholesale costs significantly. Those that do not intend to assemble their products proceed to the final sanding before packaging. Companies that do assemble their products employ workers who examine a work order and pull the appropriate parts from the bins, then ready them for assembly. The assembly of the table is done by hand. This is the preferred method in many shops as a manufacturer may produce several tables with very similar parts, thus making it difficult for a machine to discern which parts were used on specific product numbers. Jigs or templates mark where the screws must go. They are laid on the table tops so the table may be screwed in place precisely.The tables are given a final sanding using a hand sander. While this is a fairly careful sanding it is not considered a fine sanding or finish sanding as the company presumes that the consumer will spend time sanding the surface to close the grain, remove hand oils that prevent it from taking a good stain, and further reduce any mill marks.Quality ControlQuality control is monitored at every step of production. Most storage rooms for wood raw materials stay between 50-85°F (10-29°C) and moderate humidity. The moisture content, known as MC in the trade, is the weight of water contained in the wood compared to the wood's oven-dry weight. This moisture content should never exceed 25% and ideally should stay around 12%. Most factories try to find one temperature and humidity and keep these constant so that the wood comes to an equilibrium moisture content. Temperature and humidity must be moderate to ensure that a product does not bend, crack, or warp after manufacture. Excessive humidity can result in the loosening and weakening of joints and even failure at the joint. In fact, most of the problems associated with wood in the manufacture of furniture are associated with dimensional changes or movement of the wood due to variation in humidity.Everyone who assists with production is constantly performing visual checks of the wood. Wood is checked for cracks, knots, or discoloration that are unsightly or may weaken the piece structurally when boards are first chosen for the tops in the gluing process. Hand gluing and stapling of the drawer and hand assembly of the entire table helps ensure a strong, sturdy table. The jig is carefully placed on the table top and apron in order for the screws to be placed in the correct positions, further ensuring stability. Even after the tops are glued and sanded, they are checked again for flaws in the wood. Hand assemblers and hand sanders who come in at the end of the process give the table a visual examination as well. Finally, in packaging, the entire table is looked over, then sent to the warehouse for storage.By products/WasteWood waste generated from the routing and profiling is gathered up and sent in quantity to the factory's "hog" which chops the waste into fine chips. A variety of companies, including remanufactured furniture factories, paper product producers and manufacturers who make particle board, chip board, and so forth may arrange to take away these small, processed chips.The FutureCurrently, the availability of North American woods for the production of unfinished tables is not a problem. Increasingly there is interest from the consumer that the pine used in such tables is certified, meaning it has been legally and carefully harvested and is not a foreign rain forest product. Labor costs for the production of such pieces is not prohibitive and the abandonment of furniture production in this country is not likely in the immediate future. However, stylish, inexpensive, already finished tables of imported wood such parawood are proving to be challenges for some of these manufacturers. As Americans become more concerned about using these foreign woods it may be that these tables, particularly computer tables, will not sell well. However, their price points may be so competitive that the use of certified woods may be deemed unimportant.Where to Learn MoreBooksKrill, Rosemary Troy, and Pauline K. Eversmann. Early American Decorative Arts, 1620-1860. Walnut Creek, CA: 2000.Other"Quality Control in Furniture Manufacture: Moisture Content." December 2001. < http://www.mtc.com.my/publication/library/quality/content.html >.Oral interview with Roger Shinn, Director of Production for Westview Products. Dallas, Oregon. July 2001.Nancy EV BrykRead more: How table is made
- Home >
- Catalog >
- Business >
- Letter Template >
- Business Letter Template >
- Standard Business Letter Template >
- free letter template >
- A Range Of Clear Plastic Router Templates, For Use With Any