A Quick Guide to Editing The This Agreement Is Made And Entered Into This Day January, 2006 By And Between The Co
Below you can get an idea about how to edit and complete a This Agreement Is Made And Entered Into This Day January, 2006 By And Between The Co quickly. Get started now.
- Push the“Get Form” Button below . Here you would be transferred into a dashboard that enables you to carry out edits on the document.
- Select a tool you need from the toolbar that pops up in the dashboard.
- After editing, double check and press the button Download.
- Don't hesistate to contact us via [email protected] if you need further assistance.
The Most Powerful Tool to Edit and Complete The This Agreement Is Made And Entered Into This Day January, 2006 By And Between The Co
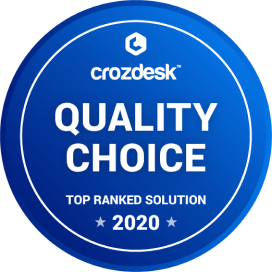
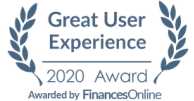
Modify Your This Agreement Is Made And Entered Into This Day January, 2006 By And Between The Co Within Minutes
Get FormA Simple Manual to Edit This Agreement Is Made And Entered Into This Day January, 2006 By And Between The Co Online
Are you seeking to edit forms online? CocoDoc has got you covered with its comprehensive PDF toolset. You can get it simply by opening any web brower. The whole process is easy and convenient. Check below to find out
- go to the free PDF Editor page.
- Import a document you want to edit by clicking Choose File or simply dragging or dropping.
- Conduct the desired edits on your document with the toolbar on the top of the dashboard.
- Download the file once it is finalized .
Steps in Editing This Agreement Is Made And Entered Into This Day January, 2006 By And Between The Co on Windows
It's to find a default application that can help make edits to a PDF document. Fortunately CocoDoc has come to your rescue. Examine the Handback below to know possible approaches to edit PDF on your Windows system.
- Begin by obtaining CocoDoc application into your PC.
- Import your PDF in the dashboard and make modifications on it with the toolbar listed above
- After double checking, download or save the document.
- There area also many other methods to edit PDF text, you can check it out here
A Quick Guide in Editing a This Agreement Is Made And Entered Into This Day January, 2006 By And Between The Co on Mac
Thinking about how to edit PDF documents with your Mac? CocoDoc offers a wonderful solution for you.. It empowers you to edit documents in multiple ways. Get started now
- Install CocoDoc onto your Mac device or go to the CocoDoc website with a Mac browser. Select PDF file from your Mac device. You can do so by hitting the tab Choose File, or by dropping or dragging. Edit the PDF document in the new dashboard which encampasses a full set of PDF tools. Save the content by downloading.
A Complete Guide in Editing This Agreement Is Made And Entered Into This Day January, 2006 By And Between The Co on G Suite
Intergating G Suite with PDF services is marvellous progess in technology, with the power to simplify your PDF editing process, making it quicker and with high efficiency. Make use of CocoDoc's G Suite integration now.
Editing PDF on G Suite is as easy as it can be
- Visit Google WorkPlace Marketplace and search for CocoDoc
- establish the CocoDoc add-on into your Google account. Now you can edit documents.
- Select a file desired by hitting the tab Choose File and start editing.
- After making all necessary edits, download it into your device.
PDF Editor FAQ
What will the next premium iPhone be made of?
Apple will create an iPhone primarily from ZrO2 - Zirconian CeramicsThe journey Apple has taken to adopt Zirconia Ceramic as the their fundamental design material translates like an epic movie plot. We will begin at the end.The Case For (of) ZirconiaZirconia ceramics [1] are structured in a martensite-type [2] transformation mechanism of stress induction. This provides the ability to absorb highest amounts of stress relative to other ceramic materials including:AluminaAluminum NitrideBoron CarbideBoron NitrideCordieriteGraphiteMulliteSapphireSilicon CarbideSilicon NitrideSteatiteTitanium DiborideTungsten CarbideZirconia ceramics exhibits the highest mechanical strength and toughness at room temperature. Zirconium ceramics have the highest fracture toughness of any advanced technical ceramic. Its toughness, mechanical properties and corrosion resistance make it ideal for high pressure applications.Common industrial applications include extrusion dies, wire and pipe extension, guides and other wear rollers, pressure valves, and bearing materials. Its thermal expansion coefficient is very close to steel, this property has made Zirconia ceramics the ideal plunger for use in a steel bore. Its properties are derived from a very precise phase composition. Zirconia has excellent wear, chemical and corrosion resistance, and low thermal conductivity.The properties of Zirconia ceramics are dictated by the types of atoms present, the types of bonding between the atoms, and the way the atoms are packed together. Zirconia is very densely packed. Zirconia ceramics usually have a combination of stronger bonds called ionic. This occurs between a metal and nonmetal and involves the attraction of opposite charges when electrons are transferred from the metal to the nonmetal.There are also covalent bonds that occurs between two nonmetals and involves sharing of atoms. In general, metals have weaker bonds than ceramics, which allows the electrons to move freely between atoms. This type of bond results in the property called ductility, where the metal can be easily bent without breaking, allowing it to be drawn into wire. Thus although stronger than metals, Zirconia ceramics are a bit more brittle. There are various methods to mitigate these effects.In relationship to most other materials, Zirconia ceramics exhibits an impervious resistance to scratching. Aluminum in almost all forms exhibits a higher likelihood of retaining scratches, scuffs and staining. Zirconia ceramics also can be pigmented to any color palette with-out the use of exterior paints.Rocket Science: How NASA Uses CeramicsZirconia ceramics are also extremely efficient at dissipating heat, perhaps better than any other material. Heat dissipation is desired when protecting a system as a barrier to heat, heat conduction is desired when the aim is to transfer heat away from a system. The Space Shuttle used LI-900 silica ceramics as the thermal protection system, a barrier that protected the Space Shuttle Orbiter during atmospheric reentry dissipating ~3,000 °F of accumulated heat protecting the Aluminum skin from thermal gradients no hotter than 350°F . NASA began research into using ceramics spanning from the early 1960s for thermal HRSI layers for entry level spacecraft. NASA drove the research that created all the modern ceramic systems, including the ideas behind using Zirconia ceramics.Zirconia + Alumina Or Aluminum Nitride Conduct HeatThe LI-900 silica ceramics have the opposite effect one would need in most moderne electronic devices, mainly to dissipate heat. Zirconia alone in a ceramic is a very low heat conductor, but this can be changed. In electronics application the introduction of Alumina or better yet Aluminum Nitride the heat conduction coefficients rapidly surpass Aluminum alone. The ratios of these introduction into the Zirconia ceramic can introduce brittleness, however it can be mitigated with an effective balance.Transparent Zirconia CeramicsZirconia ceramics can also be transparent. In 2012 the Tokyo Research Laboratory wrote a landmark paper [3] called the: “Development of highly transparent zirconia ceramics”. Transparent Zirconia ceramics could serve as a new very hard screen.Apple’s Material Science OdysseyApple has been on a journey to craft the products they create from the most advanced elements. Through it’s history Apple has revolutionized the use of Aluminum, from smelting and fabrication to micro-millimeter precision CNC machining. Apple has advanced the use of Aluminum to such a degree they have reached the pinnacle of how much further they can go, other than “transparent Aluminum” (Aluminum oxynitride) [4].Apple’s desire to stretch the bounds of material science may have contributed to the “Bendgate” [5]. As the iPhone became thinner the potential of failure to the structural integrity increased. There are remedial ways to use components inside of the iPhone to aid in the structural integrity, however Apple may have reached the limit.Apple’s Sapphire DetourOn October 1st, 2013 Apple entered into a unique relationship with GT Advanced Technologies on the manufacturing of Sapphire Crystals for production into screens and a new unibody iPhone made primarily of Sapphire. The press release was optimistic, although at the time I had deep concerns over the fact Apple did not fully acquire the company, instead created a unique performance based relationship.On October 31, 2013, GTAT Corporation ("GTAT"), a wholly owned subsidiary of GT Advanced Technologies Inc, and Apple ("Apple") entered into a Master Development and Supply Agreement and related Statement of Work (the "MDSA"), pursuant to which GTAT will supply sapphire material exclusively to Apple for consumer electronics. GTAT has granted Apple certain intellectual property rights in connection with its sapphire growth technologies.The unique relationship required GT Advanced Technologies to produce optically clear and flawless crystals in factory space supplied by Apple in Arizona. The relationship fell apart rapidly as quality and production volume was not nearly as expected at a cost that was several times more expensive than anyone anticipated. Apple ended the relationship and by October, 2014 GT Advanced Technologies was in bankruptcy.The Sapphire screen was to be a central part of the iPhone 6 series and would have added greatly to the structural integrity. Apple had about 5 months before the announcement of the iPhone and compromised on the design. It was a tragic turn of events that is still impacting Apple to this day in the design of the iPhone 7. Apple would normally advance the design of the iPhone ever 2 years. The setback from the failure of GT Advanced Technologies forced Apple took look at other materials. Apple internally vowed to never become reliant on outside vendors for critical foundational technology. They went back to the drawing board.Back To The Drawing Board And The Trail Of Apple PatentsAfter the failure to get very high production quantities of Sapphire at high quality, Apple looked closer at the periodic table of elements and searched for materials that can be manufactured in very high quantities, have similar properties to Sapphire and Aluminum. Apple tested hundreds of ideas but ultimately settled on Zirconia ceramics because of the characteristics stated above. Apple has a patent history using ceramics dating past 2006, thus it was a natural path for their next major leap in material sciences.The ideal material to manufactured and iPhone should be radio transparent [6] allowing the the many radio frequencies to emanate from the device unimpeded. Currently iPhones have antenna lines, even the least iPhone 7 has them, although they have been machined into the unibody of Aluminum. Aluminum successful blocks just about all short band radio frequencies and as devices become smaller, the impact on radio range becomes challenging.The iPhone Becoming Radio TransparantIn summer of August, 2006, about six months before the iPhone was announced by Steve Jobs in January 9, 2007, Apple material scientists Stephen Zadesky and Stephen Lynch were filing patents for: “A handheld computing device includes an enclosure having structural walls formed from a ceramic material that is radio-transparent” [7].The backgrounds statement for the patent says quite a bit:“In recent years, portable computing devices such as laptops, PDAs, media players, cellular phones, etc., have become small, light and powerful. One factor contributing to this phenomena is in the manufacturer's ability to fabricate various components of these devices in smaller and smaller sizes while in most cases increasing the power and or operating speed of such components. Unfortunately, the trend of smaller, lighter and powerful presents a continuing design challenge in the design of some components of the portable computing devices.One design challenge associated with the portable computing devices is the design of the enclosures used to house the various internal components of the portable computing devices. This design challenge generally arises from two conflicting design goals--the desirability of making the enclosure lighter and thinner, and the desirability of making the enclosure stronger and more rigid. The lighter enclosures, which typically use thinner plastic structures and fewer fasteners, tend to be more flexible and therefore they have a greater propensity to buckle and bow when used while the stronger and more rigid enclosures, which typically use thicker plastic structures and more fasteners, tend to be thicker and carry more weight. Unfortunately, increased weight may lead to user dissatisfaction, and bowing may damage the internal parts of the portable computing devices.…The invention relates, in one embodiment, to a portable computing device capable of wireless communications. The portable computing device includes an enclosure that surrounds and protects the internal operational components of the portable computing device. The enclosure includes a structural wall formed from a ceramic material that permits wireless communications therethrough. The wireless communications may for example correspond to RF communications, and further the ceramic material may be radio-transparent thereby allowing RF communications therethrough.When I first read this patent application in 2006 I knew that at some point this would be one of the next foundational direction for materials for Apple. The radio transparency solves a tremendous number of problems. The iPhone needs to transmit and/or receive through 5 primary radio systems including Cellular, WiFI, Bluetooth, NFC, GPS, etc. There is great advantage to using a unibody that is radio transparent.The Apple Zirconia Ceramics Production PatentIn February, 2014 Apple continued to patent more advancements in the production of Zirconia ceramics with: “CERAMIC COMPONENT CASTING” [7]. The patent application deals with a technique that makes production quality much higher by removing the processes that introduces imperfections.“Ceramic-based components can be used in a variety of products including structural/building materials, kitchen and tableware, automotive components, medical devices and electronic devices. These ceramic-based components may be used in such a variety of industries because of the desirable physical properties and characteristics. As one example, ceramic-based materials may include high strength properties (e.g., fracture toughness, ductility), include dielectric constant properties and may be substantially transparent, dependent on manufacture. Conventional ceramic-based components are typically made using two techniques: ceramic injection molding (CIM) and ceramic gel casting.Generally, embodiments discussed herein are related to methods for improved ceramic component casting. The methods of casting may include combining two materials, where the combining of the two materials begin a curing process to form a ceramic component. At least one of the two materials may include zirconia particles. The combined materials, including the zirconia particles, may be disposed within a cavity of a ceramic component mold, and may cure over a predetermined time to form a ceramic component. The forming of the ceramic component may be accomplished by maintaining a minimal compression force and relatively constant temperature surrounding the two materials including the zirconia particles. That is, the formation may not require any additional pressure than the amount of pressure needed to hold the component mold together.Additionally, the formation may not require the addition of heat to the two materials including the zirconia to form the ceramic component. As a result, the mold need not withstand rapid heating and cooling, and may be made from a more cost-effective material. Additionally, through the casting process, the two materials including the zirconia and/or the mold may be subjected to a vacuum in order to remove air bubbles that may negatively affect the formed ceramic component.In this patent Apple is perfecting the production of Zirconia ceramic that allows for higher strength and a lower brittleness factor.The Landmark Zirconia Ceramics iPhone, MacBook And Apple Watch PatentOn August 3rd, 2015 Apple presented the landmark patent for the future direction of Apple products to the USTPO. Innocently titled: “CO-MOLDED CERAMIC AND POLYMER STRUCTURE”. On September 8, 2016 one day after the Apple event that announced the iPhone 7 and the Apple Watch Series 2 the patent was made public. Of particular interest is Apple Watch Edition Series 2. Although I anticipated a ceramic Watch but this time Apple used Zirconia + Alunima. The patent was embargoed since August, 2015 by the USPTO to one day after the event so as not to telegraph a future product shift to competitors.The patent cites this background:As one specific example, ceramic materials have numerous qualities that make them particularly useful for use in electronic device housings. For example, they may be highly scratch resistant, making them particularly well suited for electronic devices that are frequently subject to bumps, scrapes, and scratches, such as wearable electronic devices (e.g., smart watches, glasses and the like), mechanical watches, and other consumer products (including, but not limited to, media players, mobile computers, tablet computing devices, and so on). As a specific example, the high hardness and optical clarity of sapphire crystal (a crystalline ceramic material) may be very well suited as the cover glass for a touch-screen of a wearable electronic device. Ceramic materials may also be relatively light, making handheld or wearable electronic devices easier to carry, wear, and use. Moreover, ceramic materials may be able to achieve a high degree of surface polish making them particularly aesthetically pleasing.However, ceramic materials typically are more difficult to form into complex geometries than plastics, and, thus, manufacturing housing components from ceramic materials can be more difficult than for other materials. Accordingly, described herein are housing components where a polymer material is co-molded with a ceramic component to form a housing component that includes ceramic and polymer material portions. (As used herein, the terms "polymer" and/or "polymer material" encompass natural and synthetic polymers, plastics, rubbers, and the like.) For example, a ceramic housing portion may be co-molded with a polymer material to form a polymer clip that is directly coupled to the ceramic material and can be used to retain the ceramic component with another housing component. As another example, a polymer material may be co-molded with a ceramic component to form a plastic coating on a portion of the ceramic componentAs described herein, a polymer material forming a polymer feature may be coupled to a ceramic component by a co-molding process whereby the polymer material is molded against the ceramic component. By co-molding the polymer material directly onto the ceramic component, the polymer feature may be bonded to the ceramic material without the use of an intervening adhesive or other bonding agent between the ceramic and the polymer feature. For example, instead of separately forming the ceramic component and the polymer feature, and then adhering the polymer feature to the ceramic with glue, pressure sensitive adhesive, heat activated films, epoxy, or the like, the polymer may be molded directly against the ceramic material.Thus, parts that include both ceramic and polymer components can be manufactured more quickly and with higher precision than would be achieved if the components had to be manufactured separately and thereafter coupled together with adhesive. In some embodiments, the polymer material is injection molded onto the ceramic component. In some embodiments, the polymer material is molded onto the ceramic component using techniques other than injection molding, such as gravity casting, or any other appropriate co-molding process. Where the present discussion refers to injection molding, it will be understood that other molding techniques may be used in such instances instead of or in addition to injection molding.Apple has created a system whereby injection moulding can be used to form the unibody of a device and to mate that device efficiently to a screen. There are embodiments that also present the Apple Watch Edition Series 2.The description on the Apple website for Apple Watch Edition follows the narrative of this patent and our story so far:“Uniquely elegant. Brilliantly scratch-resistant.Sleek, light, and extremely durable, ceramic is more than four times as hard as stainless steel — with a pearly, lustrous finish that won’t scratch or tarnish.The craftsmanship behind the case.The process of creating the Apple Watch Edition case begins with a high-strength zirconia powder that’s combined with alumina to achieve its rich, white color. Each case is then compression molded, sintered, and polished using a diamond slurry, which results in a remarkably smooth surface and an exquisite shine. With this precise level of workmanship, every Apple Watch Edition case takes days to make.”One can see Apple is using a Zirconia powder with Alumina. This is for color but also for heat transference. As mentioned above this coincides with what I mentioned above about increasing thermal conductivity of Zirconia ceramics.Apple Watch Edition Series 2 has replaced the solid gold original Watch Edition that sold for $17,000. Apple Watch Edition Series 2 sells for about $1,200 and is now the premium level for the device. Apple is suggesting luxury with the use of this material at this point.What Does This All Mean?One could argue that the premium price could signal that the iPhone made of Zirconia ceramic would be more costly based on this example. However in my analysis the production cost of high yield Zirconia ceramic in sufficient quantities to produce a unibody in the form factor of the current iPhone 7 would actually be less costly than the current manufacturing, milling and CNC machining of the unibody in Aluminum for the iPhone 7, in high production.Thus we have the basis for the next generation of the iPhone, but perhaps all Apple devices including the iPad, MacBook Pro and other others. The reasoning is very simple, the benefits of Zirconia ceramic are especially useful for any modern computer device.Why is Apple moving to Zirconia Ceramics?StrengthRadio TransparencyHeat Conducton/Dissipation - with Alumina / Aluminum NitrideScratch resistanceEase of manufacturingClearly Apple has reached as far as they could with CNC Aluminum and has reached as to the limits of usability for future iPhones. It is one hinderance to the device becoming thinner, the transverse strength is at the limit. As Apple introduces more advanced chips they will induce more heat and this heat needs to be dissipated efficiently.These issues also apply to the iPad and the MacBook. The strength and thermal exchange rate is quite unmatched. As mentioned above, NASA choose silica (for weight, but also made them very brittle) ceramics used in the 24,000 tile LI-900 thermal protection system to dissipated heat efficiently. It worked very well, but was not perfect. With Zirconia ceramics and the introduction of Alumina and or Aluminum Nitride the heat transfer coefficient will exceed Aluminum alone making the new iPhone the best device to dissipate heat seen thus far [8].The Entire iPhone Casing Is A Battery: Meet Lithium-Ceramic BatteriesThere is a very intriguing possibility that new Lithium-Ceramic [9] battery technology could be implemented in to the actual case material of a future iPhone. This new battery technology allows for a very new and unique way to eliminate a separate battery and to fashion it into the actual structure of the iPhone. Although Lithium-Ceramic batteries are currently not as efficient.A Lithium-Ceramic battery as the entire casing system for a future iPhone would allow for a substantially larger battery more than compensating for the lowered efficiency. This manufacturing technique would be revolutionary and create a thinner and lighter iPhone.Lithium-Ceramic batteries are so resilient they can be cut in half and still operate. They are also a magnitude more safe and recyclable. The safety issue is currently a wide concern when it was discovered the Samsung Galaxy Note7 suffered a ban on airlines and a Consumer Products Safety Commission recall because of a explosion and fire hazard. Lithium-Ceramic batteries would be some of the safest batteries in use.The 10th Anniversary iPhone 8In September 2017, Apple will be releasing the 10th Anniversary iPhone 8. It is my view Apple will use this moment to present a completely new iPhone design that will be revolutionary in many ways. I assert the design language will be based on a more organic shape and design. There will be ergonomic curves that will mold into the new AMOLED display being driven by video chips that simply could not have thermally operated in such a small space with-out heat efficiency of Zirconia ceramics. The iPhone 8 will not just be water resistant but water proof and dust proof to a level never seen before on a smartphone. The lightning port will look more like the Mag-Safe system used on the MacBook Pro devices [10] and mostly use inductive charging. Of course there will be no 3.5mm audio jack.I say this: I hope that in some way Apple always has a reason to include something made of Aluminum, you and I and the rest of the world will miss Jony Ive saying Aluminum.Destiny DelayedI think destiny delayed the shift of the iPhone to this new material and design to correlate with the 10 year mark. I think Apple needs the time to craft and engineer this to a level of artistry and perfection never seen before. I think it will be one of Jony Ive’s crowning achievement. I think it will be one of Apple’s crowning achievements. It will be worth the wait.[1] https://scholar.google.com/scholar?q=Zirconia+ceramics+wiki&hl=en&as_sdt=0&as_vis=1&oi=scholart&sa=X&ved=0ahUKEwi4tJ_GpYXPAhVM82MKHZNdBHcQgQMIHDAA[2] https://scholar.google.com/scholar?q=martensite-type+transformation&hl=en&as_sdt=0&as_vis=1&oi=scholart&sa=X&ved=0ahUKEwjt9LaJo4XPAhVC0WMKHTDQCdQQgQMIHDAA[3] http://www.tosoh.co.jp/technology/assets/2012_02_02.pdf[4] Aluminium oxynitride + Star Trek's Transparent Aluminum is Now Real[5] iPhone 6[6] https://en.wikipedia.org/wiki/Radiodensity[7] United States Patent Application: 0060268528[7] United States Patent Application: 0150217479[8] Thermal - Thermal Conductivity[9] https://scholar.google.com/scholar?q=lithium-Ceramic+battery&hl=en&as_sdt=0&as_vis=1&oi=scholart&sa=X&ved=0ahUKEwjmqbW-iYrPAhXFGj4KHYINDYoQgQMIHzAA[10] Patent US7762817 - System for coupling interfacing parts + United States Patent Application: 0110038114
What will the iPhone 8 be like?
Apple will create an iPhone primarily from ZrO2 - Zirconian CeramicsThe journey Apple has taken to adopt Zirconia Ceramic as the their fundamental design material translates like an epic movie plot. We will begin at the end.The Case For (of) ZirconiaZirconia ceramics [1] are structured in a martensite-type [2] transformation mechanism of stress induction. This provides the ability to absorb highest amounts of stress relative to other ceramic materials including:AluminaAluminum NitrideBoron CarbideBoron NitrideCordieriteGraphiteMulliteSapphireSilicon CarbideSilicon NitrideSteatiteTitanium DiborideTungsten CarbideZirconia ceramics exhibits the highest mechanical strength and toughness at room temperature. Zirconium ceramics have the highest fracture toughness of any advanced technical ceramic. Its toughness, mechanical properties and corrosion resistance make it ideal for high pressure applications.Common industrial applications include extrusion dies, wire and pipe extension, guides and other wear rollers, pressure valves, and bearing materials. Its thermal expansion coefficient is very close to steel, this property has made Zirconia ceramics the ideal plunger for use in a steel bore. Its properties are derived from a very precise phase composition. Zirconia has excellent wear, chemical and corrosion resistance, and low thermal conductivity.The properties of Zirconia ceramics are dictated by the types of atoms present, the types of bonding between the atoms, and the way the atoms are packed together. Zirconia is very densely packed. Zirconia ceramics usually have a combination of stronger bonds called ionic. This occurs between a metal and nonmetal and involves the attraction of opposite charges when electrons are transferred from the metal to the nonmetal.There are also covalent bonds that occurs between two nonmetals and involves sharing of atoms. In general, metals have weaker bonds than ceramics, which allows the electrons to move freely between atoms. This type of bond results in the property called ductility, where the metal can be easily bent without breaking, allowing it to be drawn into wire. Thus although stronger than metals, Zirconia ceramics are a bit more brittle. There are various methods to mitigate these effects.In relationship to most other materials, Zirconia ceramics exhibits an impervious resistance to scratching. Aluminum in almost all forms exhibits a higher likelihood of retaining scratches, scuffs and staining. Zirconia ceramics also can be pigmented to any color palette with-out the use of exterior paints.Rocket Science: How NASA Uses CeramicsZirconia ceramics are also extremely efficient at dissipating heat, perhaps better than any other material. Heat dissipation is desired when protecting a system as a barrier to heat, heat conduction is desired when the aim is to transfer heat away from a system. The Space Shuttle used LI-900 silica ceramics as the thermal protection system, a barrier that protected the Space Shuttle Orbiter during atmospheric reentry dissipating ~3,000 °F of accumulated heat protecting the Aluminum skin from thermal gradients no hotter than 350°F . NASA began research into using ceramics spanning from the early 1960s for thermal HRSI layers for entry level spacecraft. NASA drove the research that created all the modern ceramic systems, including the ideas behind using Zirconia ceramics.Zirconia + Alumina Or Aluminum Nitride Conduct HeatThe LI-900 silica ceramics have the opposite effect one would need in most moderne electronic devices, mainly to dissipate heat. Zirconia alone in a ceramic is a very low heat conductor, but this can be changed. In electronics application the introduction of Alumina or better yet Aluminum Nitride the heat conduction coefficients rapidly surpass Aluminum alone. The ratios of these introduction into the Zirconia ceramic can introduce brittleness, however it can be mitigated with an effective balance.Transparent Zirconia CeramicsZirconia ceramics can also be transparent. In 2012 the Tokyo Research Laboratory wrote a landmark paper [3] called the: “Development of highly transparent zirconia ceramics”. Transparent Zirconia ceramics could serve as a new very hard screen.Apple’s Material Science OdysseyApple has been on a journey to craft the products they create from the most advanced elements. Through it’s history Apple has revolutionized the use of Aluminum, from smelting and fabrication to micro-millimeter precision CNC machining. Apple has advanced the use of Aluminum to such a degree they have reached the pinnacle of how much further they can go, other than “transparent Aluminum” (Aluminum oxynitride) [4].Apple’s desire to stretch the bounds of material science may have contributed to the “Bendgate” [5]. As the iPhone became thinner the potential of failure to the structural integrity increased. There are remedial ways to use components inside of the iPhone to aid in the structural integrity, however Apple may have reached the limit.Apple’s Sapphire DetourOn October 1st, 2013 Apple entered into a unique relationship with GT Advanced Technologies on the manufacturing of Sapphire Crystals for production into screens and a new unibody iPhone made primarily of Sapphire. The press release was optimistic, although at the time I had deep concerns over the fact Apple did not fully acquire the company, instead created a unique performance based relationship.On October 31, 2013, GTAT Corporation ("GTAT"), a wholly owned subsidiary of GT Advanced Technologies Inc, and Apple ("Apple") entered into a Master Development and Supply Agreement and related Statement of Work (the "MDSA"), pursuant to which GTAT will supply sapphire material exclusively to Apple for consumer electronics. GTAT has granted Apple certain intellectual property rights in connection with its sapphire growth technologies.The unique relationship required GT Advanced Technologies to produce optically clear and flawless crystals in factory space supplied by Apple in Arizona. The relationship fell apart rapidly as quality and production volume was not nearly as expected at a cost that was several times more expensive than anyone anticipated. Apple ended the relationship and by October, 2014 GT Advanced Technologies was in bankruptcy.The Sapphire screen was to be a central part of the iPhone 6 series and would have added greatly to the structural integrity. Apple had about 5 months before the announcement of the iPhone and compromised on the design. It was a tragic turn of events that is still impacting Apple to this day in the design of the iPhone 7. Apple would normally advance the design of the iPhone ever 2 years. The setback from the failure of GT Advanced Technologies forced Apple took look at other materials. Apple internally vowed to never become reliant on outside vendors for critical foundational technology. They went back to the drawing board.Back To The Drawing Board And The Trail Of Apple PatentsAfter the failure to get very high production quantities of Sapphire at high quality, Apple looked closer at the periodic table of elements and searched for materials that can be manufactured in very high quantities, have similar properties to Sapphire and Aluminum. Apple tested hundreds of ideas but ultimately settled on Zirconia ceramics because of the characteristics stated above. Apple has a patent history using ceramics dating past 2006, thus it was a natural path for their next major leap in material sciences.The ideal material to manufactured and iPhone should be radio transparent [6] allowing the the many radio frequencies to emanate from the device unimpeded. Currently iPhones have antenna lines, even the least iPhone 7 has them, although they have been machined into the unibody of Aluminum. Aluminum successful blocks just about all short band radio frequencies and as devices become smaller, the impact on radio range becomes challenging.The iPhone Becoming Radio TransparantIn summer of August, 2006, about six months before the iPhone was announced by Steve Jobs in January 9, 2007, Apple material scientists Stephen Zadesky and Stephen Lynch were filing patents for: “A handheld computing device includes an enclosure having structural walls formed from a ceramic material that is radio-transparent” [7].The backgrounds statement for the patent says quite a bit:“In recent years, portable computing devices such as laptops, PDAs, media players, cellular phones, etc., have become small, light and powerful. One factor contributing to this phenomena is in the manufacturer's ability to fabricate various components of these devices in smaller and smaller sizes while in most cases increasing the power and or operating speed of such components. Unfortunately, the trend of smaller, lighter and powerful presents a continuing design challenge in the design of some components of the portable computing devices.One design challenge associated with the portable computing devices is the design of the enclosures used to house the various internal components of the portable computing devices. This design challenge generally arises from two conflicting design goals--the desirability of making the enclosure lighter and thinner, and the desirability of making the enclosure stronger and more rigid. The lighter enclosures, which typically use thinner plastic structures and fewer fasteners, tend to be more flexible and therefore they have a greater propensity to buckle and bow when used while the stronger and more rigid enclosures, which typically use thicker plastic structures and more fasteners, tend to be thicker and carry more weight. Unfortunately, increased weight may lead to user dissatisfaction, and bowing may damage the internal parts of the portable computing devices.…The invention relates, in one embodiment, to a portable computing device capable of wireless communications. The portable computing device includes an enclosure that surrounds and protects the internal operational components of the portable computing device. The enclosure includes a structural wall formed from a ceramic material that permits wireless communications therethrough. The wireless communications may for example correspond to RF communications, and further the ceramic material may be radio-transparent thereby allowing RF communications therethrough.When I first read this patent application in 2006 I knew that at some point this would be one of the next foundational direction for materials for Apple. The radio transparency solves a tremendous number of problems. The iPhone needs to transmit and/or receive through 5 primary radio systems including Cellular, WiFI, Bluetooth, NFC, GPS, etc. There is great advantage to using a unibody that is radio transparent.The Apple Zirconia Ceramics Production PatentIn February, 2014 Apple continued to patent more advancements in the production of Zirconia ceramics with: “CERAMIC COMPONENT CASTING” [7]. The patent application deals with a technique that makes production quality much higher by removing the processes that introduces imperfections.“Ceramic-based components can be used in a variety of products including structural/building materials, kitchen and tableware, automotive components, medical devices and electronic devices. These ceramic-based components may be used in such a variety of industries because of the desirable physical properties and characteristics. As one example, ceramic-based materials may include high strength properties (e.g., fracture toughness, ductility), include dielectric constant properties and may be substantially transparent, dependent on manufacture. Conventional ceramic-based components are typically made using two techniques: ceramic injection molding (CIM) and ceramic gel casting.Generally, embodiments discussed herein are related to methods for improved ceramic component casting. The methods of casting may include combining two materials, where the combining of the two materials begin a curing process to form a ceramic component. At least one of the two materials may include zirconia particles. The combined materials, including the zirconia particles, may be disposed within a cavity of a ceramic component mold, and may cure over a predetermined time to form a ceramic component. The forming of the ceramic component may be accomplished by maintaining a minimal compression force and relatively constant temperature surrounding the two materials including the zirconia particles. That is, the formation may not require any additional pressure than the amount of pressure needed to hold the component mold together.Additionally, the formation may not require the addition of heat to the two materials including the zirconia to form the ceramic component. As a result, the mold need not withstand rapid heating and cooling, and may be made from a more cost-effective material. Additionally, through the casting process, the two materials including the zirconia and/or the mold may be subjected to a vacuum in order to remove air bubbles that may negatively affect the formed ceramic component.In this patent Apple is perfecting the production of Zirconia ceramic that allows for higher strength and a lower brittleness factor.The Landmark Zirconia Ceramics iPhone, MacBook And Apple Watch PatentOn August 3rd, 2015 Apple presented the landmark patent for the future direction of Apple products to the USTPO. Innocently titled: “CO-MOLDED CERAMIC AND POLYMER STRUCTURE”. On September 8, 2016 one day after the Apple event that announced the iPhone 7 and the Apple Watch Series 2 the patent was made public. Of particular interest is Apple Watch Edition Series 2. Although I anticipated a ceramic Watch but this time Apple used Zirconia + Alunima. The patent was embargoed since August, 2015 by the USPTO to one day after the event so as not to telegraph a future product shift to competitors.The patent cites this background:As one specific example, ceramic materials have numerous qualities that make them particularly useful for use in electronic device housings. For example, they may be highly scratch resistant, making them particularly well suited for electronic devices that are frequently subject to bumps, scrapes, and scratches, such as wearable electronic devices (e.g., smart watches, glasses and the like), mechanical watches, and other consumer products (including, but not limited to, media players, mobile computers, tablet computing devices, and so on). As a specific example, the high hardness and optical clarity of sapphire crystal (a crystalline ceramic material) may be very well suited as the cover glass for a touch-screen of a wearable electronic device. Ceramic materials may also be relatively light, making handheld or wearable electronic devices easier to carry, wear, and use. Moreover, ceramic materials may be able to achieve a high degree of surface polish making them particularly aesthetically pleasing.However, ceramic materials typically are more difficult to form into complex geometries than plastics, and, thus, manufacturing housing components from ceramic materials can be more difficult than for other materials. Accordingly, described herein are housing components where a polymer material is co-molded with a ceramic component to form a housing component that includes ceramic and polymer material portions. (As used herein, the terms "polymer" and/or "polymer material" encompass natural and synthetic polymers, plastics, rubbers, and the like.) For example, a ceramic housing portion may be co-molded with a polymer material to form a polymer clip that is directly coupled to the ceramic material and can be used to retain the ceramic component with another housing component. As another example, a polymer material may be co-molded with a ceramic component to form a plastic coating on a portion of the ceramic componentAs described herein, a polymer material forming a polymer feature may be coupled to a ceramic component by a co-molding process whereby the polymer material is molded against the ceramic component. By co-molding the polymer material directly onto the ceramic component, the polymer feature may be bonded to the ceramic material without the use of an intervening adhesive or other bonding agent between the ceramic and the polymer feature. For example, instead of separately forming the ceramic component and the polymer feature, and then adhering the polymer feature to the ceramic with glue, pressure sensitive adhesive, heat activated films, epoxy, or the like, the polymer may be molded directly against the ceramic material.Thus, parts that include both ceramic and polymer components can be manufactured more quickly and with higher precision than would be achieved if the components had to be manufactured separately and thereafter coupled together with adhesive. In some embodiments, the polymer material is injection molded onto the ceramic component. In some embodiments, the polymer material is molded onto the ceramic component using techniques other than injection molding, such as gravity casting, or any other appropriate co-molding process. Where the present discussion refers to injection molding, it will be understood that other molding techniques may be used in such instances instead of or in addition to injection molding.Apple has created a system whereby injection moulding can be used to form the unibody of a device and to mate that device efficiently to a screen. There are embodiments that also present the Apple Watch Edition Series 2.The description on the Apple website for Apple Watch Edition follows the narrative of this patent and our story so far:“Uniquely elegant. Brilliantly scratch-resistant.Sleek, light, and extremely durable, ceramic is more than four times as hard as stainless steel — with a pearly, lustrous finish that won’t scratch or tarnish.The craftsmanship behind the case.The process of creating the Apple Watch Edition case begins with a high-strength zirconia powder that’s combined with alumina to achieve its rich, white color. Each case is then compression molded, sintered, and polished using a diamond slurry, which results in a remarkably smooth surface and an exquisite shine. With this precise level of workmanship, every Apple Watch Edition case takes days to make.”One can see Apple is using a Zirconia powder with Alumina. This is for color but also for heat transference. As mentioned above this coincides with what I mentioned above about increasing thermal conductivity of Zirconia ceramics.Apple Watch Edition Series 2 has replaced the solid gold original Watch Edition that sold for $17,000. Apple Watch Edition Series 2 sells for about $1,200 and is now the premium level for the device. Apple is suggesting luxury with the use of this material at this point.What Does This All Mean?One could argue that the premium price could signal that the iPhone made of Zirconia ceramic would be more costly based on this example. However in my analysis the production cost of high yield Zirconia ceramic in sufficient quantities to produce a unibody in the form factor of the current iPhone 7 would actually be less costly than the current manufacturing, milling and CNC machining of the unibody in Aluminum for the iPhone 7, in high production.Thus we have the basis for the next generation of the iPhone, but perhaps all Apple devices including the iPad, MacBook Pro and other others. The reasoning is very simple, the benefits of Zirconia ceramic are especially useful for any modern computer device.Why is Apple moving to Zirconia Ceramics?StrengthRadio TransparencyHeat Conducton/Dissipation - with Alumina / Aluminum NitrideScratch resistanceEase of manufacturingClearly Apple has reached as far as they could with CNC Aluminum and has reached as to the limits of usability for future iPhones. It is one hinderance to the device becoming thinner, the transverse strength is at the limit. As Apple introduces more advanced chips they will induce more heat and this heat needs to be dissipated efficiently.These issues also apply to the iPad and the MacBook. The strength and thermal exchange rate is quite unmatched. As mentioned above, NASA choose silica (for weight, but also made them very brittle) ceramics used in the 24,000 tile LI-900 thermal protection system to dissipated heat efficiently. It worked very well, but was not perfect. With Zirconia ceramics and the introduction of Alumina and or Aluminum Nitride the heat transfer coefficient will exceed Aluminum alone making the new iPhone the best device to dissipate heat seen thus far [8].The Entire iPhone Casing Is A Battery: Meet Lithium-Ceramic BatteriesThere is a very intriguing possibility that new Lithium-Ceramic [9] battery technology could be implemented in to the actual case material of a future iPhone. This new battery technology allows for a very new and unique way to eliminate a separate battery and to fashion it into the actual structure of the iPhone. Although Lithium-Ceramic batteries are currently not as efficient.A Lithium-Ceramic battery as the entire casing system for a future iPhone would allow for a substantially larger battery more than compensating for the lowered efficiency. This manufacturing technique would be revolutionary and create a thinner and lighter iPhone.Lithium-Ceramic batteries are so resilient they can be cut in half and still operate. They are also a magnitude more safe and recyclable. The safety issue is currently a wide concern when it was discovered the Samsung Galaxy Note7 suffered a ban on airlines and a Consumer Products Safety Commission recall because of a explosion and fire hazard. Lithium-Ceramic batteries would be some of the safest batteries in use.The 10th Anniversary iPhone 8In September 2017, Apple will be releasing the 10th Anniversary iPhone 8. It is my view Apple will use this moment to present a completely new iPhone design that will be revolutionary in many ways. I assert the design language will be based on a more organic shape and design. There will be ergonomic curves that will mold into the new AMOLED display being driven by video chips that simply could not have thermally operated in such a small space with-out heat efficiency of Zirconia ceramics. The iPhone 8 will not just be water resistant but water proof and dust proof to a level never seen before on a smartphone. The lightning port will look more like the Mag-Safe system used on the MacBook Pro devices [10] and mostly use inductive charging. Of course there will be no 3.5mm audio jack.I say this: I hope that in some way Apple always has a reason to include something made of Aluminum, you and I and the rest of the world will miss Jony Ive saying Aluminum.Destiny DelayedI think destiny delayed the shift of the iPhone to this new material and design to correlate with the 10 year mark. I think Apple needs the time to craft and engineer this to a level of artistry and perfection never seen before. I think it will be one of Jony Ive’s crowning achievement. I think it will be one of Apple’s crowning achievements. It will be worth the wait.[1] https://scholar.google.com/scholar?q=Zirconia+ceramics+wiki&hl=en&as_sdt=0&as_vis=1&oi=scholart&sa=X&ved=0ahUKEwi4tJ_GpYXPAhVM82MKHZNdBHcQgQMIHDAA[2] https://scholar.google.com/scholar?q=martensite-type+transformation&hl=en&as_sdt=0&as_vis=1&oi=scholart&sa=X&ved=0ahUKEwjt9LaJo4XPAhVC0WMKHTDQCdQQgQMIHDAA[3] http://www.tosoh.co.jp/technology/assets/2012_02_02.pdf[4] Aluminium oxynitride + Star Trek's Transparent Aluminum is Now Real[5] iPhone 6[6] https://en.wikipedia.org/wiki/Radiodensity[7] United States Patent Application: 0060268528[7] United States Patent Application: 0150217479[8] Thermal - Thermal Conductivity[9] https://scholar.google.com/scholar?q=lithium-Ceramic+battery&hl=en&as_sdt=0&as_vis=1&oi=scholart&sa=X&ved=0ahUKEwjmqbW-iYrPAhXFGj4KHYINDYoQgQMIHzAA[10] Patent US7762817 - System for coupling interfacing parts + United States Patent Application: 0110038114
What is the best Indian military equipment?
India is one of the most rapidly growing nation with such a huge infantry power and unrivaled powerful weapons.Day by day Indian Armed forces updating itself by new and most powerful weapons and technologies which help them to stand in front of any threat. As we know the India is heavily dependent on foreign suppliers for equipment as the local industry hasn’t able to delivered as promised.This article covers the top most Powerful weapons of Indian Armed Forces. No doubt after seeing this list you came to know that most of the weapons are foreign supplied but Indians have modified according to their requirement and made them more powerful,accurate and Most deadliest weapons ever.I know the article is lengthy but definitely I’ll sure you after reading this article you don’t left with any doubt about the present most powerful weapons in Indian Armed forces. So here we Start….Just sit and enjoy the reading.TOP Most Powerful Weapons in INDIAN ARMED FORCES 20161)Su-30Mki-The FighterThe Su-30Mki is the best ever aircraft made to serve its service in Indian Air force.It is the cream of Indian Air Force.The twin-jet Air Superiority Fighter designed and developed by Russia’s Sukhoi and built under licence by India’s Hindustan Aeronautics limited (HAL).It is the heavy long range all weather fighter that introduced in IAF in September 27,2002 and with his unrivalled capabilities IAF today has more than 200 Sukhoi Su-30Mki’s.The aircraft has a outstanding aerodynamic configuration and integrated with unmatched avionics suite.The aircraft is well known for its performance ; it can fly with a speed of 2100 km/h and has rate of climb of 230m/s.Moreover it is equipped with 30mm GSH-1 gun with 12 hardpoints, 6 types of Air-to-Air missiles, anti-ship, cruise and air to surface missile and 6 types of bombs. By 2016 it will integrated with BrahMos and Nirbhay missile which would give it strike capabilities that have never seen before in IAF.2)Brahmos missile-The Game FinisherBRAHMOS is a short range ramjet supersonic cruise missile developed by BrahMos Aerospace Private Limited which is formed by a Joint venture between Russian Federation’s NPO Mashinostroeyenia and India’s Defence Research and development Organisation(DRDO).It can be launched from submarines,ships,aircraft or Page Redirection is considered the world’s fastest cruise missile in operation.This is the best missile in the Indian Armed forces with its outstanding performance Resources and Information. is better than other existing state-of-art subsonic cruise missile by various factors like it is 3 times more faster than any other missile in Indian Armed Forces,It has 3 times more flight range,3 to 4 times more seeker range and 9 times more kinetic energy than any other subsonic cruise missile.The missile has identical configuration for land,sea an sub-sea platforms and uses a Transport Launch Canister (TLC) for transportation,storage and Lunch.The ship based weapons complex and Land based weapon complex version are in service but the Air Launch version is in Progress.With the growing demands the next version Brahmos-II is also launched within few years.3)Arjun Mark-II Main Battle TankArjun Mark-II the Main Battle tank in Indian Armed forces is the deadliest weapon . The Arjun Mark 2 is an advanced third generation main battle tank and an upgraded version of the Arjun main battle tank with several http://improvements.It was developed by DRDO .The Arjun MK.2 has the improved protection,fire-power and mobility than its predecessor.The Tank has total of 13 major improvements with 93 of total upgrades.The Arjun Mark II tank can perform well under various circumstances,such as driving across cross-country over rugged sand Dunes easily,Detecting,observing and quickly engaging targets. It has advanced hydro-pneumatic suspension system which consists of each side of seven dual rubber-tyred road-wheels with the drive sprocket at the rear,idler at the front and track-return rollers.The MBT is integrated with advanced Armaments,Avionics and Accessories .A Remote Controlled Weapon Station mounted on top of the turret with 12.7mm NSVT machine gun.With the unmatched capabilities and unrivalled performance it is the Wall for Enemies in Indian Army.4)INS Vikramaditya-Floating airfield and Mini cityINS Vikramaditya is the King of Indian http://ocean.It is the best aircraft carrier in the Indian Armed Forces. Once integrated, INS Vikramaditya will bring transformational capabilities to the Indian Navy and will be a ‘game changer’.INS Vikramaditya is a modified Kiev-class aircraft carrier which entered into service with the Indian Navy in 2013. She was commissioned on 16 November 2013 at a ceremony held at Severodvinsk, Russia. On 14 June 2014, Prime Minister of India Narendra Modi formally inducted INS Vikramaditya into the Indian Navy and dedicated it to the nation.As the Modified Kiev-class aircraft carrier it has the 45,400 tons of loaded http://displacement.It is 283.5 metres long and has 22 decks.it has 6 turbo alternators and 6 diesel alternators are installed that are capable of generating 18 Mwatt of power.Whereas 8 turbo-pressurised boilers,4 shafts,4 geared steam turbines are responsible for propulsion generating 180,000 horsepower .The aircraft carrier has a range of 7000 nautical miles at its full speed :32 knots (59km/h).Tha aircraft carrier has the capacity if loading up to 36 maximum aircrafts including 30 Mikoyan MiG-29k multi role fighters and 6 x Kamov ka-31 AEW&C and Kamov ka-28 ASW Helicopters.5) INS Chakra-Shark made of SteelINS Chakra is a Russia-made, nuclear-propelled, hunter-killer submarine of Indian. Unlike conventional submarines that India operates which need to surface to charge their batteries often – sometimes as frequently as 24 hours-INS Chakra can stay under water as long as it wants.Its ability to stay underwater is restrained only by human endurance to Stay Underwater. INS Chakra has been taken on lease from Russia for 10 years and would provide the Navy the opportunity to train personnel and operate such nuclear-powered vessels.The akula class submarine submarine carry conventional weapons: four 533mm and four 650mm torpedo tubes that will be used to hunt and kill enemy ships.The Submarine can displaces 8140 tons and can do over at 30 knots twice the speed of any other http://submarine.It is the quietest nuclear submarine around with the 80 crew members on Board.6)Agni V-The killer MissileAgni-V is an intercontinental ballistic missile developed by the Defence Research and Development Organisation (DRDO) of India. Agni V is part of the Agni series of missiles, one of the missile systems under the original Integrated Guided Missile Development Program.The agni V has the maximum operational range of 8000 km. and Carry nuclear warhead of 1000kg with the speed of Mach 24 and can hit the target with the accuracy of less than 10m.Agni V is the most successful ICBM missile of India. The indigenously developed, intercontinental, surface to surface, nuclear capable ballistic missile is unlike other missiles in the Agni series. Agni-V is the most advanced system so far, which has various new technologies incorporated in it in terms of navigation and guidance, warhead and engine.7)Phalcon AwacsIndia was late in entering the Airborne Early Warning and Control System (AWACS) scene, but the entry of India was bang with the most advanced AWACS in the world. In January 2004, India and Israel signed a $1.1 billion contract for 3 Phalcon airborne warning and control system (AWACS) aircraft, as part of a $1.5 billion tripartite agreement with Russia. With the arrival of its first IL-76 Phalcon, India joined the global ranks of AWACS operators. The aircraft has to monitor huge swathes of Indian airspace, intercept communications and log radar frequencies, add some ground surveillance, and help command IAF responses. By 2012 India announced that it wanted to follow up on that procurement with native capabilities.The AWACS consists of an Israeli Elta EL/W-2090 radar mounted on a Russian II-76 aircraft. This radar is a 360 ° Active electronically Scanning Array (AESA) which is mounted inside a dome on top of the Il-76. The speciality of the radar is that it is stationary as its beams are electronically steered as well, which eliminates the need for the radar to be steered mechanically. This allows it to track targets 10 times faster when compared to well-known systems like the E-3 Sentry. It has an integrated IFF system, Electronic Counter Measures (ECM) and ECCM suites for self-protection, Electronic Intelligence (ELINT) for collecting data about enemy radars and monitoring communications and SatCom systems.8)INS Vikrant UndockedINS Vikrant (IAC-I) is the first aircraft carrier built in India and the first Vikrant-class aircraft carrier built by Cochin Shipyard (CSL) for the Indian Navy.The vikrant-class-carrier is 262 metres (860 ft) long and 60 metres (200 ft) wide, and displaces about 40,000 metric tons (39,000 long tons). It features a Short Take-Off But Arrested Recovery (STOBAR) configuration with a ski-jump. The deck is designed to enable aircraft such as the MiG-29K to operate from the carrier. It is expected to carry an air group of up to 30 aircraft, which will include up to 30 fixed-wing aircraft, primarily the Mikoyan MiG-29K and the naval variant of the HAL Tejas Mark 2, besides carrying 10 Kamov Ka-31 or Westland Sea King helicopters. The Ka-31 will fulfill the airborne early warning (AEW) role and the Sea King will provide anti-submarine warfare (ASW) capability.Vikrant is powered by four General Electric LM2500+ gas turbines on two shafts, generating over 80 megawatts (110,000 hp) of power. The gearboxes for the carriers were designed and supplied by Electron Engineering.9)Barak 8-Shield for Incomming missilesNaval Barak-8 is a long-range anti-air and anti-missile naval defence system being developed jointly by Israel Aerospace Industries (IAI) and the Defence Research & Development Organisation (DRDO) of India. Surface-to-air missiles (SAM) can counter attack aircraft, UAVs and incoming anti-ship missiles. The missile entered service with the Indian Navy in 2013.In January 2006, India and Israel signed a $350m agreement to co-develop a new generation long-range surface-to-air missile (LR-SAM) for Indian Navy ships.in April 2009, Israel signed a $1.1bn contract to deliver an upgraded Barak-8 air defence system to India. Deliveries are expected to be concluded by 2017.On 10 November 2014 the Barak 8 was successfully test fired in Israel with all integrated operational components for both the marine & land System Resources and Information. December 2014 it was reported that destroyer INS Kolkata, the largest warship built in India, will fire a long-range surface-to-air missile (LR-SAM) for the first time in 2015.10)T-90s Bheeshma-The destroyerThe T-90 is a Russian third-generation main battle tank that is a modernisation of the T-72. It is the latest development in the T-series of Russian tanks and represents an increase in firepower, mobility and protection. It is manufactured by Uralvagonzavod in Nizhnyi Tagil, Russia.The T-90S entered service with the Russian Army in 1992. In February 2001, the Indian Army signed a contract for 310 T-90S tanks, Out of which 120 were delivered completely, 90 in semi knocked down kits and 100 in complete knocked down kits.The T-90 weighs around 46 tonnes and has a new diesel engine,jaming system,laser warning receivers.The main armament of T-90 is 125mm smoothbore gun with 43 rounds and a 12.7 mm heavy machine gun is also mounted on the tank that is operated manually as well as remotely controlled from the inside the turret by the commander.it has a crew members of 3.After a series of imports from Russia, finally India got the licence to manufacture the T-90S. Russia supplied documents for the local manufacture of the tank in India. A T-90S Bhishma tank was thus manufactured by the Heavy Vehicles Factory at Avadi, Tamil Nadu on January 7, 2004. Following which 10 others were manufactured by the end of 2009.11)P-81 Neptune-Maritime Surveillance AircraftThe P-8I Neptune is a variant of the US Navy’s P-8A Poseidon multi-mission maritime patrol aircraft (MPA). The government of India selected the P-8I long-range maritime reconnaissance and anti-submarine warfare aircraft by signing a $2.1 billion contract on January 1, 2009. The Indian Navy will take delivery of eight aircraft between 2013 and 2015. They will carry out anti-submarine warfare missions; search and rescue; maritime interdiction; and long-range intelligence, surveillance, target acquisition and reconnaissance. In July 2015, India ordered four additional aircraft.This is the best aircraft to protect India’s 7500 km stretched coastline and hundred of Islands which need protection and where costly build submarines and aircraft carriers are difficult to reach.
- Home >
- Catalog >
- Business >
- Letter Template >
- Confirmation Letter >
- Sample Business Confirmation Letter >
- confirmation letter format >
- This Agreement Is Made And Entered Into This Day January, 2006 By And Between The Co