How to Edit The Supply Of Labor And Materials For The Installation Of Aluminum conviniently Online
Start on editing, signing and sharing your Supply Of Labor And Materials For The Installation Of Aluminum online under the guide of these easy steps:
- click the Get Form or Get Form Now button on the current page to make your way to the PDF editor.
- hold on a second before the Supply Of Labor And Materials For The Installation Of Aluminum is loaded
- Use the tools in the top toolbar to edit the file, and the edits will be saved automatically
- Download your modified file.
A top-rated Tool to Edit and Sign the Supply Of Labor And Materials For The Installation Of Aluminum
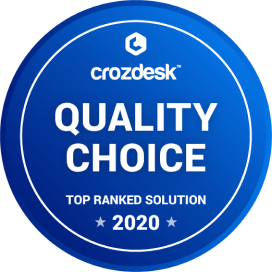
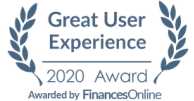
Start editing a Supply Of Labor And Materials For The Installation Of Aluminum straight away
Get FormA clear direction on editing Supply Of Labor And Materials For The Installation Of Aluminum Online
It has become much easier in recent times to edit your PDF files online, and CocoDoc is the best free app you would like to use to make a series of changes to your file and save it. Follow our simple tutorial to start!
- Click the Get Form or Get Form Now button on the current page to start modifying your PDF
- Add, modify or erase your text using the editing tools on the top tool pane.
- Affter editing your content, add the date and add a signature to finalize it.
- Go over it agian your form before you click the download button
How to add a signature on your Supply Of Labor And Materials For The Installation Of Aluminum
Though most people are in the habit of signing paper documents using a pen, electronic signatures are becoming more common, follow these steps to sign PDF for free!
- Click the Get Form or Get Form Now button to begin editing on Supply Of Labor And Materials For The Installation Of Aluminum in CocoDoc PDF editor.
- Click on the Sign icon in the toolbar on the top
- A box will pop up, click Add new signature button and you'll be given three options—Type, Draw, and Upload. Once you're done, click the Save button.
- Move and settle the signature inside your PDF file
How to add a textbox on your Supply Of Labor And Materials For The Installation Of Aluminum
If you have the need to add a text box on your PDF for making your special content, follow the guide to finish it.
- Open the PDF file in CocoDoc PDF editor.
- Click Text Box on the top toolbar and move your mouse to carry it wherever you want to put it.
- Fill in the content you need to insert. After you’ve put in the text, you can take use of the text editing tools to resize, color or bold the text.
- When you're done, click OK to save it. If you’re not settle for the text, click on the trash can icon to delete it and start over.
An easy guide to Edit Your Supply Of Labor And Materials For The Installation Of Aluminum on G Suite
If you are seeking a solution for PDF editing on G suite, CocoDoc PDF editor is a recommendable tool that can be used directly from Google Drive to create or edit files.
- Find CocoDoc PDF editor and establish the add-on for google drive.
- Right-click on a chosen file in your Google Drive and click Open With.
- Select CocoDoc PDF on the popup list to open your file with and allow access to your google account for CocoDoc.
- Make changes to PDF files, adding text, images, editing existing text, annotate with highlight, give it a good polish in CocoDoc PDF editor before hitting the Download button.
PDF Editor FAQ
Should other nations follow Germany's lead on promoting solar power?
The answer is the most forceful possible no.Solar power itself is a good thing, but Germany's pro-renewables policy has been a disaster. It has the absurd distinction of completing the trifecta of bad energy policy:Bad for consumersBad for producersBad for the environment (yes, really; I'll explain)Pretty much the only people who benefit are affluent home-owners and solar panel installation companies. A rising tide of opposition and resentment is growing among the German press and public.I was shocked to find out how useless, costly, and counter-productive their world-renowned energy policy has turned out. This is a serious problem for Germany, but an even greater problem for the rest of the world which hopes to follow in their footsteps. The first grand experiment in renewable energy is a catastrophe! The vast scale of the failure has only started to become clear over the past year or so. So I can forgive renewables advocates for not realizing it yet -- but it's time for the green movement to do a 180 on this.Some awful statistics before I get into the details:Germany is widely considered the global leader in solar power, with over a third of the world's nameplate (peak) solar power capacity. [1] Germany has over twice as much solar capacity per capita as sunny, subsidy-rich, high-energy-cost California. (That doesn't sound bad, but keep going.)Germany's residential electricity cost is about $0.34/kWh, one of the highest rates in the world. About $0.07/kWh goes directly to subsidizing renewables, which is actually higher than the wholesale electricity price in Europe. (This means they could simply buy zero-carbon power from France and Denmark for less than they spend to subsidize their own.) More than 300,000 households per year are seeing their electricity shut off because they cannot afford the bills. Many people are blaming high residential prices on business exemptions, but eliminating them would save households less than 1 euro per month on average. Billing rates are predicted by the government to rise another 40% by 2020. [2]Germany's utilities and taxpayers are losing vast sums of money due to excessive feed-in tariffs and grid management problems. The environment minister says the cost will be one trillion euros (~$1.35 trillion) over the next two decades if the program is not radically scaled back. This doesn't even include the hundreds of billions it has already cost to date. [3] Siemens, a major supplier of renewable energy equipment, estimated in 2011 that the direct lifetime cost of Energiewende through 2050 will be $4.5 trillion, which means it will cost about 2.5% of Germany's GDP for 50 years straight. [4] That doesn't include economic damage from high energy prices, which is difficult to quantify but appears to be significant.Here's the truly dismaying part: the latest numbers show Germany's carbon output and global warming impact is actually increasing [5] despite flat economic output and declining population, because of ill-planned "renewables first" market mechanisms. This regime is paradoxically forcing the growth of dirty coal power. Photovoltaic solar has a fundamental flaw for large-scale generation in the absence of electricity storage -- it only works for about 5-10 hours a day. Electricity must be produced at the exact same time it's used. [29] The more daytime summer solar capacity Germany builds, the more coal power they need for nights and winters as cleaner power sources are forced offline. [6] This happens because excessive daytime solar power production makes base-load nuclear plants impossible to operate, and makes load-following natural gas plants uneconomical to run. Large-scale PV solar power is unmanageable without equally-large-scale grid storage, but even pumped-storage hydroelectricity facilities are being driven out of business by the severe grid fluctuations. They can't run steadily enough to operate at a profit. [2,7] Coal is the only non-subsidized power source that doesn't hemorrhage money now. [8] The result is that utilities must choose between coal, blackouts, or bankruptcy. Which means much more pollution.So it sucks on pretty much every possible level. If you're convinced by these facts, feel free to stop reading now, throw me an upvote, and go on about your day. This is going to get long -- I haven't even explained the half of it yet. There are lots of inter-related issues here, and the more you get into them, the worse the picture gets.Issue 1: Wrong place, wrong tech to start the green revolutionRenewables advocates constantly hold up Germany as an example of how large-scale rooftop solar power is viable. But the problem is, Germany's emphasis on solar power is bad policy. I'm pretty sure other countries can do solar better, but that isn't saying much because German solar is just awful. To be blunt, it's a stupid place for politicians to push solar panels. I was there all last week for a work meeting and I didn't see the sun the entire time. From talking to the locals, it's overcast for about a third of the year in the region near Hanover where I was staying. Their solar resource is simply bad, nearly the worst of any well-populated region in the world:Annual Solar IrradianceBetween the northern latitude, the grey weather, and the Alps blocking much of the diffused morning sunlight from the south, Germany is a terrible place for solar power. When you put the US side-by-side on the same scale, you realize that Germany has the same solar power potential as dismal Alaska, even worse than rain-soaked Seattle:Solar Radiation MapI look at this and ask, "what on earth are they thinking?" They couldn't have picked a worse generation technology for their climate.But most people seem to look at it and say, "if Germany is investing so much in solar power, then it's obvious the US should build solar panels too." I insist we examine the contrapositive: if solar power is only taking off slowly in the US, even with significant subsidies/incentives and one of the world's best solar resources, then the Germans should be building even less solar capacity. It's clear their market must be severely distorted for them to pursue such a sub-optimal energy policy.You're welcome to disagree with my thought process here, but the simplest proof can be seen in the capacity factor, which is the percent of the nameplate capacity that is actually generated over the course of a year. The existence of nighttime means solar capacity factors must be less than 50%, and when you add clouds, dawn, dusk, dust, and non-optimal installations, 18% is the average capacity factor for panels in the continental US. [9] In contrast, Germany's total solar capacity factor in 2011 was under 9%! [1]German residential solar panel installations today cost about $2.25/watt capacity, [10] versus a hair over $5/watt in the US. [11] (Numbers vary over a considerable range. Most of this is labor/permitting costs.) But German panels generate less than half as much actual power over time. So when you normalize the panel install cost by capacity factor, US and German solar power generation are already at cost parity. The payback periods for solar investments are about the same in California and Germany. This is surprising to most solar advocates, who tend to blame higher costs for the low uptake rates in the US. But system economics alone do not explain disparities in installation rates.So why does Germany have 16 times as much nameplate panel capacity per capita as the US? [12] Yes, permitting is much easier there, but that's mostly captured by the $/watt costs since installation companies usually pull the permits. And I don't think the German people are that much more pro-environment than the rest of the world. There's no good reason for the disparity that I can find -- it ought to swing the opposite way. Solar just isn't a good power source for a cold, dark country that has minimal daytime air conditioning load. Solar in Phoenix, Arizona makes sense, but not in Frankfurt. The only conclusion I can come to is that Germany's solar power boom is being driven entirely by political distortions. The growth of solar is not economically justified, nor can it continue without massive political interference in power markets.Many people are surprised to hear that Germany only gets a tiny 2.0% of its total energy / 4.6% of its electricity from solar power (in 2012). [5,13] All the headlines about new records on peak summer days make it seem more like 50%. Despite all the cost and pain and distortions, PV solar has turned out to be a very ineffective way of generating large amounts of energy. They could have generated at least four times as much carbon-free power via new nuclear plants for the same cost. [14] (Nuclear would have been a better option for a lot of reasons. I'll get to that later.)With subsidies for new solar systems phasing out over the next 5 years, solar growth has already started to decline. The installation rate peaked and is now dropping. [13, 15] Despite falling panel and installation costs, the majority of new German solar projects are expected to stop when subsidies end. They're already on the downward side of the technology uptake bell curve:(Data after 2008 from [14], prior to 2008 from Wikipedia)If you pay close attention, all the pro-solar advocates are still using charts with data that stops after 2011. That's because 2011 was the last year solar was growing exponentially. Using data through July 2013 and official predictions for the rest of this year, it's now clear that solar is not on an exponential growth curve. It's actually on an S-curve like pretty much every other technology, ever. Limitless exponential growth doesn't exist in the physical world. [13]Also note the huge gap on that graph between the actual generation and the nameplate capacity. That's where the miserable capacity factor comes in. (I think this is the source of a lot of misplaced optimism about solar's growth rate.) Green media outlets only report solar power either in peak capacity or as percent of consumption on sunny summer days. Both of these measurements must be divided by about 10 to get the true output throughout the year.In reality, solar is scaling up much slower than conventional energy sources scaled up in the past, despite solar receiving more government support. This graph shows the growth rate of recent energy transitions in the first 10 years after each source reached grid scale (1% of total supply):[13]I think this chart is the best way to make an apples-to-apples comparison of uptake rates. Only about a quarter of the "renewables" line is due to solar (the majority is biomass, wind, and trash incineration). So the true solar growth rate from 2001-2011 is only 1/4th as fast as nuclear from 1974-1984, and 1/6th as fast as natural gas from 1965-1975. [13]When a new energy source is genuinely better than the old energy sources, it grows fast. Solar is failing to do so. Yet it's had every advantage the government could provide.What this all implies is that without government intervention, PV solar can't be a significant source of grid power. The economics of German solar have only made sense up til now because they tax the hell out of all types of energy (even other renewables), and then use the proceeds to subsidize solar panels. Utilities are forced to buy distributed solar power at rates several times the electricity's market value, causing massive losses. The German Renewable Energy Act directly caused utility losses of EUR 540 million in August 2013 alone. [16] It's a shocking amount of money changing hands. When you strip away the well-intentioned facade of environmentalism, this is little more than a forced cash transfer scheme. It's taking from utilities (who are losing money hand over fist on grid management and pre-existing conventional generation capacity) and from everyone who doesn't have rooftop panels, and shoveling it into the pockets of everyone who owns or installs panels. Which means it's both a massive market distortion and a regressive tax on the poor.This explains why per-capita solar uptake is so high in Germany. The government has engineered a well-intentioned but harmful redistribution system where everyone without solar panels is giving money to people who have them. This is a tax on anyone who doesn't have a south-facing roof, or who can't afford the up-front cost, or rents their residence, etc. People on fixed incomes (eg welfare recipients and the elderly) have been hardest hit because the government has made a negligible effort to increase payments to compensate for skyrocketing energy prices. The poor are literally living in the dark to try to keep their energy bills low. Energiewende is clearly bad for social equality. But Germany's politicians seem to have a gentleman's agreement to avoid criticizing it in public, particularly since Merkel did an about-face on nuclear power in 2011. [17]Issue 2: Supply VariabilityOne major problem with all this solar-boosting, ironically, is oversupply. It's mind-boggling to me that a generation technology that provides less than 5% of a country's electricity supply can be responsible for harmful excess electricity production, but it's true. On sunny summer afternoons, Germany actually exports power at a loss compared to generation costs: EUR 0.056/kWh average electricity export sale price in 2012, [18] vs EUR 0.165/kWh average lifetime cost for all German solar installed from 2000 to 2011. [14] (This is optimistically assuming a 40 year system life and 10% capacity factor -- reality is probably over EUR 0.20/kWh.) German utilities often have to pay heavy industry and neighboring countries to burn unnecessary power. On sunny summer days, businesses are firing up empty kilns and furnaces, and are getting paid to throw energy away.You can argue that this excess summer solar generation is free, but it's not -- not only is this peak summer output included in the lifetime cost math, but excess solar power actually forces conventional power plants to shut down, thereby lowering the capacity factor of coal & gas plants. Yes, this means large-scale solar adoption makes non-solar power more expensive per kWh, too! On net, excess solar generation is a significant drag on electricity economics. You're paying for the same power generation equipment twice -- once in peak conventional capacity for cloudy days, and again in peak solar capacity for sunny days -- and then exporting the overage for a pittance.Why would they bother exporting at a loss? Because the feed-in-tariff laws don't allow utilities to shut off net-metered rooftop solar. Utilities are forced by law to pay residential consumers an above-market price for power that isn't needed. Meanwhile, Germany's fossil-burning neighbors benefit from artificially-low EU energy market prices. This discourages them from building cleaner power themselves. It's just a wasteful, distorted energy policy.Remember, electricity must be used in the same moment it's generated. [29] The technology for grid-scale electricity storage does not yet exist, and nothing in the development pipeline is within two orders of magnitude of being cheap enough to scale up. Pumped-hydro storage is great on a small scale, but all the good sites are already in use in both Europe and the US. The only plan on the table for grid-scale storage is to use electric car batteries as buffers while they're charging. But that still won't provide anywhere near enough capacity to smooth solar's rapidly-changing output. [19] And if people plug in their cars as soon as they get home from work and the sun goes down, the problem could get even worse. California's regulators have recently acknowledged that the generation profile at sundown is the biggest hurdle to the growth of solar power. The classic illustration is the "duck chart" (shaped like a duck) that shows how solar forces conventional power plants to ramp up at an enormous rate when the sun stops shining in the evening:[29]People often complain about wind power being unreliable, but when you get enough wind turbines spread over a large enough area, the variability averages out. The wind is always blowing somewhere. This means distributed wind power is fairly reliable at the grid level. But all solar panels on a power grid produce power at the same time, meaning night-time under-supply and day-time over-supply. This happens every single day, forever. At least in warm countries, peak air conditioning load roughly coincides with peak solar output. But Germany doesn't use much air conditioning. It's just a grid management nightmare. The rate of "extreme incidents" in Germany's power grid frequency/voltage has increased by three orders of magnitude since Energiewende started. [20]The severe output swings have even reached the point where Germany's grid physically cannot operate without relying on neighboring countries to soak up the variability. The ramp-down of solar output in the evening happens faster than the rest of Germany's generation capacity can ramp-up. (Massive power plants can't change output very quickly.) Which either means blackouts as people get home from work, or using non-solar-powered neighbors as buffers. Here's one day's generation profile for German solar power, showing how net electricity imports/exports are forced to oscillate back and forth to smooth out the swings in production:[21]If Germany's neighbors also had as many solar panels, they would all be trying to export and import at the same time, and the system would fall apart. The maximum capacity of the entire EU grid to utilize solar power is therefore much lower than the level reached by individual countries like Germany and Spain.Solar boosters often say people need to shift their energy consumption habits to match generation, instead of making generation match consumption. That's feasible, to an extent -- perhaps 20% of power consumption can be time-shifted, mostly by rescheduling large consumers currently operating at night like aluminum electrosmelters. But modern civilization revolves around a particular work/sleep schedule, and you can't honestly expect to change that. People aren't going to give up cooking and TV in the evening, or wait three hours after the sun goes down to turn on the lights. And weekends have radically different consumption profiles from weekdays.It all adds up. PV solar output doesn't properly sync up with power demand. That severely limits the maximum percentage of our electricity needs it can provide. Germany hit that limit at about 4%. They are now finding out what happens when you try to push further.Issue 3: Displacing the wrong kinds of powerYou may have noticed in the daily generation chart above how wind power is throttled back when the sun comes out. Residential solar has legal right-of-way over utility-scale wind. A lot of the power generation that solar is displacing is actually other renewables. Most of the rest is displacing natural gas and nuclear power. Coal power is growing rapidly. [6,8]Here's what the weekly generation profile is predicted to look like in 2020:[22]Notice the saw-tooth shape of the big grey "conventional" (coal/gas) category. What all this solar is doing is eating into is daytime base load generation, which seems good for displacing fossil fuels, but in the long run it's doing the opposite.The majority of electricity worldwide comes from coal and nuclear base load plants. They are big, efficient, and cheap. But base load generation is extremely difficult and expensive to throttle up and down every day. To simplify the issue a bit, you cannot ramp nuclear plants as fast as solar swings up and down every day. It takes several days to shut down and restart a nuclear plant, and nuclear plants outside France are not designed to be throttled back, so nuclear cannot be paired with the daily oscillations of PV solar. Supply is unable to match demand. You end up with both gaps and overages.Most people think Germany is decommissioning its nuclear fleet because of the Fukushima accident, but the Germans didn't really have a choice. They are being forced to stop using nuclear power by all the variability in solar output. That's a big, big problem -- Germany gets four times more electricity from nuclear than solar, so the math doesn't add up. The generation time-profile is wrong, and the total power output from solar is too low. They have to replace nuclear plants with something else.The normal way to handle variable power demand is via natural gas "peaker" plants. But Germany has minimal domestic natural gas resources and load-following gas plants are very expensive to operate, so what they're doing is building more coal plants, and re-opening old ones. [6,8,22] It's expensive and inefficient, but you can run a coal plant all night and then throttle it back when the sun comes up. It has better load-following capabilities than nuclear (although worse than gas). The German Green Party has been fighting nuclear power since the 1970s, and has finally won. Nuclear is out, and coal is in.If you're a regular follower of my writing, you'll know what a terrible idea this is. [23] Replacing nuclear power with coal power is unquestionably the most scientifically-illiterate, ass-backwards, and deadly mistake that any group of environmentalists has ever made. It's unbelievable how much cleaner and safer nuclear power is than coal power. The Fukushima meltdown was pretty much a "worst case scenario" -- one of the largest earthquakes ever recorded, the largest tsunami to ever hit Japan, seven reactor meltdowns and three hydrogen explosions -- and not a single person has died from radiation poisoning. [24] The expected lifetime increase in cancer rates due to the released radiation is somewhere between zero and a number too small to measure. [25] Even spectacular nuclear disasters are barely harmful to the public. Studies are now showing that the stress from the evacuation has killed more people than would have been killed by radiation if everyone had just stayed in place. [26,27]In comparison, coal power kills about a million people per year, fills the oceans with mercury and arsenic, releases more carbon dioxide than any other human activity, and is arguably one of the greatest environmental evils of the industrialized world. [23]This is counter-intuitive, but second-order effects are enormously important. Expansion of photovoltaic solar power past 1-2% of total electricity demand means less nuclear, and more coal. The amount of damage this does completely overwhelms the environmental benefit from the solar panels themselves. You have to avoid building so much solar power that it destabilizes and eliminates other clean power sources. When you get to the "duck chart" stage, things start to get bad. Otherwise you'll end up worse off than when you started, as Germany has found out to its dismay.So that all sucks a lot. German solar power is hurting people and the planet. But there's more.Issue 4: The kickerThe category for "biomass" power you see in all these charts is actually firewood being burned in coal plants. 38% of Germany's "renewable energy" comes from chopping down forests and importing wood from other countries. [28] Effing firewood, like we're back in the Middle Ages or something. Due to overzealous renewables targets, and a quirk in the EU carbon pricing system that considers firewood carbon-neutral, Europe is chopping down forests at an alarming rate to burn them as "renewable biomass." The environmental movement has spent most of the last 200 years of industrialization trying to fight deforestation, and that noble goal has been reversed in an instant by bogus carbon emission calculations.In the very long run, over 100 years or so, firewood is close to carbon neutral because you can regrow the trees and they absorb CO2 as they grow. Unfortunately, using firewood for fuel destroys a living carbon sink and releases all its carbon to the atmosphere right now. When you consider that you're destroying a carbon sink as well as releasing stored carbon, firewood is actually much worse than coal for many decades thereafter. [28] The next few decades is humanity's most critical time for reducing carbon emissions, so this policy is mind-boggling lunacy.Germany is so focused on meeting renewables targets that it is willing to trample the environment to get there. They've managed to make renewables unsustainable! It's tragicomic.To summarize: Energiewende is the worst possible example of how to implement an energy transition. The overzealous push for the wrong generation technology has hurt citizens, businesses, and the environment all at the same time.I want to make it clear that I'm not saying we should abandon solar. It should definitely be part of our generation mix. Due a mix of bad climate and bad policy, Germany ran into problems at a very low solar penetration, and other countries will be able to reach higher penetrations. But even if we ignore cost, there is still a maximum practical limit to solar power based on the realities of grid management.You can't build more PV solar than the rest of the grid can ramp up/down to accept. The necessary grid storage for large-scale solar power is a "maybe someday" technology, not something viable today. Calls for 50% of power to come from solar in our lifetimes are a fantasy, and we need to be realistic about that.You can't force utilities to buy unneeded power just because it's renewable. The energy and materials to build the excess capacity just goes to waste. That is the opposite of green.We have to learn those lessons. We can't sweep this failure under the rug.Every time a renewables advocate holds Germany up as a shining beacon, they set back the credibility of the environmental movement. It's unsupported by reality and I think even gives ammunition to the enemy. We have to stop praising Germany's Energiesheiße and figure out better ways to implement renewables. Other models should work better. They have to -- the future of the world depends on it.[1] Solar power by country[2] Germany's Energy Poverty: How Electricity Became a Luxury Good - SPIEGEL ONLINE[3] German 'green revolution' may cost 1 trillion euros - minister[4] Global Warming Targets and Capital Costs of Germany's 'Energiewende'[5] Germany's 'Energiewende' - the story so far[6] Germany: Coal Power Expanding, Green Energy Stagnating[7] Merkel's Blackout: German Energy Plan Plagued by Lack of Progress - SPIEGEL ONLINE[8] Merkel’s Green Shift Backfires as German Pollution Jumps[9] Capacity factor, Price per watt[10] German Solar Installations Coming In at $2.24 per Watt Installed, US at $4.44[11] It Keeps Getting Cheaper To Install Solar Panels In The U.S.[12] Germany Breaks Monthly Solar Generation Record, ~6.5 Times More Than US Best[13] Germany and Renewables Market Changes (source link in original article is broken, here is an updated link:http://www.bp.com/content/dam/bp...)[14] Cost of German Solar Is Four Times Finnish Nuclear -- Olkiluoto Nuclear Plant, Plagued by Budget Overruns, Still Beats Germany’s Energiewende[15] 313 MWp German PV Capacity Added in July 2013 - 34.5 GWp Total[16] EEG Account: 5,907 GWh of Renewable Energy in August Sold for EUR 37.75 at Expenses of EUR 399.52 per MWh - EUR 540 Million Deficit[17] Germany will dilute - not abandon - its Energiewende plan[18] German power exports more valuable than its imports[19] Ryan Carlyle's answer to How large would an array of solar panels have to be to power the continental US? How much would such an array cost to build? What are the major engineering obstacles to powering the US this way?[20] Electricity demand response shows promise in Germany[21] Energiewende in Germany and Solar Energy[22] Problems with Renewables and the Markets[23] Ryan Carlyle's answer to What are some policies that would improve millions of lives, but people still oppose? Why do people oppose them? What is the one area where you wish politicians and the public would pay attention to scientific consensus or other data?[24] Stephen Frantz's answer to What is a nuclear supporter's response to the Fukushima disaster?[25] Fukushima Cancer Fears Are Absurd[26] Evacuation ‘Fukushima’ deadlier then radiation[27] Was It Better to Stay at Fukushima or Flee?[28] The fuel of the future[29] Fowl Play: how the utility industry’s ability to outsmart a duck will define the power grid of the 21st century
What is Tesla's 'secret sauce' that even the biggest automakers can't replicate even though they've stripped down Teslas to study them?
Simple - Alien Dreadnought.Alien Dreadnought is what Elon calls the machine that builds the machine. When you take apart a Tesla, all you get are what parts there are and how they fit together. It tells you very little about the machine that puts it together.When you see two plates fastened together with a bolt, do you know if that bolt was installed and tightened by a person, a machine or a combination of both?Tesla has invested tremendously in automating the process to make stuff. From basic stuff like car seats to installing wiring harnesses in cars. Most car makers laughed when Tesla had to rip out a large portion of the Model 3 lines when robots couldn’t effectively install wiring harnesses. This missed the obvious point - wiring harnesses are hard, but if you can beat that manufacturing problem with robots, then pretty much the entire process can be done with robots.Thus with Model Y, a redesigned wiring harness with 90% less wire than the Model S and designed from the start to be handled by robots were patented by Tesla. We will have to wait to see if it actually makes it into production in 2020, but if it does, it means Tesla will be another step ahead of the competition.Vertical integration - as part of the machine that makes the machine, Tesla also ensures its part supply. By making its own parts it has total control of the quality and design of them, it can make compromises or absorb higher costs that a parts contractor might not be willing to do. This doesn’t show when you look at a part, all you can do is estimate how much it cost. By controlling all of these aspects, Tesla can make changes quickly and with less red tape and expense than a standard car maker who has to deal with separate parts suppliers.If you find a part that shows unique welding or shape from forming, you don’t necessarily know how it was done. All you can see is the final result. For instance, Tesla has patented a new casting machine to make the frame to the Model Y, a crazy machine that could reduce a car frame from 70 separate parts that need to be formed and assembled to a single piece. Tesla Goes Patent Crazy With Huge Casting Machine For Model YThat said, it doesn’t really matter that you can’t tell this process from just looking at the pieces. Tesla has released all its patents for any company to read and use. Most choose not to do so. All Our Patent Are Belong To YouUPDATE: 01/15/2020Thanks everyone for the Upvotes!With more comments from Elon regarding Full Self Driving being “feature complete” in 2020, the importance of Alien Dreadnought becomes more important. Software, AI and full self driving capabilities are definitely products that competitors can’t replicate simply by taking the car apart. Even looking at the software code, especially for the AI doesn’t tell you how Tesla got there.Tesla is pushing AI faster and farther, not just in the end product Self Driving AI, but in the training techniques and even the hardware used to run the software to train. This is all part of the Alien Dreadnought - build the machines that build the machines.Tesla Quietly Acquired a Machine Learning Startup That's 'Squeezing' A.I.As for the “parts supply” of this portion of the machine, it is driving data. And Tesla has worked hard to make sure it has a nearly endless supply of driving data. With every Tesla equipped with sensors and most equipped with the full self driving suite of sensors such as cameras, radar and ultrasonics, every Tesla on the road is feeding data back to Tesla, billions (with a B) of miles of it every year. To put that into perspective, Waymo just hit 20 million miles of data total, currently running about a million miles per month. Waymo’s autonomous cars have driven 20 million miles on public roadsAI’s train best on lots of unusual data. Having access to billions of miles means Tesla’s have probably seen lots of weird things on the road - flying cars, kangaroos, planes landing on the highway etc. And with Sentry cam, it can record things even while parked. Tesla's millions of cameras are capturing some crazy things - videos - Electrek This is useful for teaching the AI about human behavior, not just things that happen on roads, so perhaps in the future the AI can determine social interactions like “a fight is happening” and predict that people are going to run out into the road.By designing its own processing chip and designing teaching supercomputers like Dojo, Tesla continues to make the machines to make the machines. Something conventional automakers are completely unable to do.Elon Musk hints at Tesla's secret project 'Dojo' making the difference in race to full self-driving - ElectrekUpdate 02/24/2020And the Alien Dreadnought rolls on - Tesla Self Driving Computer, designed from a clean sheet of paper, puts Tesla years ahead of the competition. Designed in house using the best talent in the world and manufactured exclusively for Tesla by Samsung in Austin.Tesla Self-Driving Computer architect Jim Keller is confident about solving autonomous driving - ElectrekThe issue is not that other companies can’t design their own chips to match the technology, but they can’t get rid of their current contracts and manufacturers for years. Again, by bringing manufacturing in-house, Tesla continues to ensure the supply.“The real reason for holding off? Automakers worry that computers like Tesla’s will render obsolete the parts supply chains they have cultivated over decades, the engineer said. Such systems will drastically cut the number of electronic control units, or ECUs, in cars. For suppliers that depend on these components, and their employees, this is a matter of life and death.” Tesla teardown finds electronics 6 years ahead of Toyota and VWUPDATE 4/28/20Additional evidence that “Alien Dreadnought” is the correct path. VW has had to delay the release of the ID.3 due to “software issues.”. From a highly optimistic 2018 prediction that VW would be producing a vehicle to match Tesla for “half the price” by 2020 - VW Claims By 2020, Its Electric Cars Will Match Tesla At Half Price to the stark reality of having thousands of vehicles bricked and sitting in lots - VW ID.3: thousands of electric cars spotted being stockpiled in Germany - Electrek the reality of failing to invest in the machine to make the machine is evident. While the machine in this case is software, VW’s lack of investment in internal software development shows how unprepared the entire company is for the future of vehicle production.“Today, our share [self-developed software as a portion of all software in Volkswagen Group vehicles] is less than 10 percent. That is clearly too small. In the Volkswagen Group, we want to achieve a share in software development of more than 60 percent by 2025.”Volkswagen Software Comments — 10 Months Ago vs. TodayShortages of robots (Tesla bought the company VW was using), shortages of programmers (Tesla produces most of its software in house and already has a massive team of programmers), a lack of integrated design (VW is trying to integrate dozens of different hardware/software suppliers) all prevent VW from producing a viable vehicle at this time. The machine that makes the machine isn’t working.Now in discussions with Daimler-Benz to try to pool software resources, they are very late to the game and late to the realization that software is as important as hardware. Daimler flirtet mit BMW und VW Simply building the physical isn’t enough, what runs the car is as important, if not more important than the physical parts to producing a top rate EV.UPDATE 05/19/20VW is learning that the future of cars IS to treat them like smartphones. Their software issues now extend to a conventional model - The iconic VW Golf (Gen 8). Failure of the emergency call system is halting their delivery of even conventional vehicles because of software difficulties. Despite having 46 years of experience producing the Golf, VW seems very inexperienced with software. It will have a difficult time building the expertise to handle these problems, let alone getting ahead due to the huge demand worldwide for such expertise as EVERY carmaker realizes that software is the future of the car.https://www.motor1.com/news/423689/vw-golf-software-issues-arise/New Volkswagen Golf Mk. 8 Deliveries Stopped Over eCall Software IssueUPDATE 06/30/20Building the factories to house the machines that makes the machine.As proven by the build speed of Gigafactory 3 (Shanghai) going from a muddy field to a producing manufacturing line in less than one year and with the ground breaking and rapid build out of Gigafactory 4 (Berlin), Tesla shows how important Alien Dreadnought is. Knowing what processes and parts that need to be manufactured and scaling the buildings from the beginning allow Tesla to create a factory space rapidly and repeatedly. If Gigafactory 5 (Texas) becomes an operational reality in 2021, then Tesla will have built 3 operating mega factories in less than 3 years.Breaking! Tesla Gigafactory 3 Groundbreaking In China In A Few Hours — UPDATEDTesla’s Chinese factory just delivered its first carsTesla breaks ground on foundation at Gigafactory Berlin, brings in heavy machinery - ElectrekInteresting details during construction, especially regarding the Model Y. For American built Model Y’s, the back frame is two cast parts, not the one part envisioned in the patent.However, for Giga Shanghai and Fremont, new supersized casting machines were ordered.Tesla Giga Shanghai Could Be Constructing The Next Level Casting Machine for MIC Model YSo a single piece rear frame casting could come online this year for Model Y. I would assume that Giga Berlin will also be equipped with the “Gigapress” for European Model Y production.UPDATE 07/08/2020More signs that vertical integration, cross pollination and diverse investment can prove to be innovative. A bonus efficiency when you control all aspects of the Alien Dreadnought.So it appears that Tesla is looking for a visual image engineer to work at the new Fremont Battery Factory. Current theories run that Tesla is going to apply visual AI to the quality assurance process. This is an indicator that Tesla’s investment in AI, particularity visual AI will provide additional benefits other than driving.Quality control is one of Tesla’s biggest current problems. It involves inspecting pieces and work, identifying if they are correct or incorrect and then (sometimes) fixing the problem. This has traditionally been a human job since the variety of problems (paint problems, panel gaps, incorrectly installed wires, misted headlights, etc.) was too much to simply program in with a huge variety of visual cues. With an AI visually learning what a problem looks like and its thousands of variations, it could quickly be able to inspect, flag and note how to correct any imperfections during the manufacturing process, thus saving time and effort at a later date. Since it will be run by robots and AI, this means it will always be vigilant and always provide a complete inspection.“Vision Systems Engineer, Cell EngineeringSAVETeslaFremont, CAApply on LinkedInApply on Careers For Veterans At Tesla - Veteran HiringApply on Jobilize LLCApply on JobsApply on BIGHiredApply on LocalJobs.com25 days agoFull-timeThe RoleTelsa’s cell manufacturing engineering group is looking for a highly-motivated equipment development engineer to accelerate our next-generation battery cell manufacturing program. This role will be involved in the design, development, commissioning and ramping of high-throughput equipment, while working in a cross-functional team to test, validate, and roll-out process and product design changes. The battery cell is a critical component in Tesla vehicles and storage systems. This role will have the opportunity to make meaningful contributions to our products. The work environment is demanding, fast-paced and incredibly exciting. The ideal candidate should be ready to push their limits, as they join in a highly motivated and capable team to make unbelievable things into reality.Responsibilities • Drive design, commissioning ramp of a complex manufacturing tool that is the first of its kind at Tesla • Work collaboratively as the equipment expert to ensure production lines run in a safe, efficient manner producing high-quality parts. • Become owner/subject matter expert to drive equipment-related process improvement including detailed troubleshooting and root cause analysis. • Troubleshoot and recover processes by PLC, HMI, or tool management software, and implement changes/improvements • Build training material, maintenance routines, and related documentation for equipment life cycle management • Lead safety and ergonomic improvements to production equipment which meets or exceeds regulations or best practices. • Identify equipment critical spare parts and ensure sufficient coverage to prevent extended downtime situations • Participate in supplier/ internal equipment buyoffs • Debug and optimize automated processes to maximize cycle time and uptime. • Develop and manage FMEA risk assessments to prioritize equipment improvement projects and ensure sufficient repair strategies. • Provide hands-on support to the maintenance team to troubleshoot and resolve extended downtime situations. Requirements • Either a BS with 6+ years’ relevant experience or an MS with 3+ years relevant experience in interdisciplinary/integrated engineering, manufacturing engineering, or equivalent • Evidence of exceptional ability. • Strong engineering foundations. Aptitude to learn • Demonstrated experience ramping equipment into manufacturing - automation equipment, web handling, design of electromechanical systems, PLCs, motion controls, and data capture • Demonstrated experienced solving complex electromechanical and software systems with limited documentation to debug issues, build process know-how, and kick off improvement projects • Structured thinking and problem-solving abilities. Proven through a number of root cause analysis following a data-driven approach, statistical software (JMP) a plus • 2D ACAD experience in creating/validating layouts, tooling drawings, Pneumatic and electrical schematics • Experience with robot programming, backup, and restoration a plus • Experience in automotive or high volume manufacturing is highly desired”UPDATE 07/29/20Alien Dreadnought - Building edition. Tesla has gained sufficient experience to make even the manufacturing of factory buildings faster and more efficient. Pre-fab concrete panels to accelerate the building of Gigafactory Berlin.Giga Berlin will come together at an impossible-seeming speed. The prefabricated construction method in Germany is extremely impressive.— Elon Musk (@elonmusk) July 27, 2020Tesla Giga Berlin is coming together quickly thanks to prefabricated constructionWill Giga Berlin break the Giga China construction record? With Giga Texas already clearing land, will Texas be built even faster? With talks of a second China Gigafactory and another Gigafactory somewhere in Asia, the machine that makes the factories to hold the machines seems to be running faster and faster.UPDATE 09/23/20 - BATTERY DAYSo much vertical integration, Alien Dreadnought, and evidence that Tesla is not just an EV company. From investing in a new process to extract lithium from clay using water and salt and being able to return the dirt back into the ground, to producing larger, more capable batteries faster, cheaper and in less space than the 2170, utilizing new chemistry and integrating the battery pack as a primary structure, being able to recycle the batteries at the end of their life with minimal processing, Elon and Baglino showed how integrated manufacturing and vertical integration of the supply chain are the core of Tesla.Everything You Need To Know About Tesla's New 4680 Battery CellWhile it will take some time to ramp up production of the new 4680 cell, the pilot plant just down the street in Fremont is designed for 10 GWh of production, 1/3 that of Gigafactory Nevada in a building 12 times smaller. With limited production already beginning, design and testing of vehicles to use the new battery cell is well underway (Model S Plaid).Bigger batteries that are more efficient, cheaper to make, faster to make, more environmentally friendly and providing additional benefits to charging, structure, weight and longevity. All the result of Alien Dreadnought.UPDATE 10/28/20 - FULL SELF DRIVING BETALimited FSD beta releasing on Tuesday next week, as promised. This will, at first, be limited to a small number of people who are expert & careful drivers.— Elon Musk (@elonmusk) October 12, 2020With the recent release of FSD Beta, limited, it again highlights Tesla’s use of Alien Dreadnought. Since every recent Tesla with HW 3.0 chip is capable of FSD, Tesla has already built a test fleet of hundreds of thousands of vehicles. By slowing releasing beta to “expert & careful drivers” Tesla has recruited dozens if not hundreds of Tesla owners to test drive FSD, for free. Already on YouTube are hundreds of hours of video of FSD beta in action showing how it acts in all kinds of places, times, weather and situations. There are self reported testers in at least 9 states.Tesla Starts to Rollout Full Self-Driving FSD Beta for Different States' EAP MembersWhile the first days showed definite errors or quirks - always taking the leftmost turn lane even if there were two turn lanes, slowing, but not enough for speed bumps, mistaking an angle parked car as a moving car after a turn, taking longer to turn into traffic allowing a crossing car to come close, etc. patches are apparently fast and furious. With massive uploads of driving data - Tesla is collecting insane amount of data from its Full Self-Driving test fleet - Electrek Tesla is well positioned to acquire the data for cheap or free, have vast quantities of it, and apparently process it, use it to reteach the AI and update FSD within a day, if not hours. The machine to teach the machine is running fast and furious.Many of the “driver interventions” occur because FSD doesn’t drive in a fashion that makes the driver comfortable - staying in the center of a lane when there are parked cars rather than riding the dividing line, staying in the left lane when other cars are trying to pass, hitting speed bumps a bit fast, hitting the brakes at the last second, waiting too long to merge so the lagging car closes the gap quite close, etc. This information will be useful to Tesla in terms of creating a tolerable human interface, as many passengers, while quite safe with this driver, would find the experience unnerving.UPDATE 02/10/2021 -Elon Interview, Asking the right question.In an interview with Sandy Munro, Elon described why the first Model 3 wheel wells were a mess. As he mentions, they had many engineers working on the project and each one probably got the right answer for the part they were working on. One piece needed to be corrosion resistant, so the engineer picked the best corrosion resistant material, One part had a complex shape so that engineer picked a material that could be formed easily. One part was a heavy duty part that saw a lot of stress so that engineer picked a strong material. Individually each engineer came to the correct answer for her/his question. But the result was a mess - many parts, different materials, new problems in how to attach them together, new problems on how to seal the gaps due to difficulties in fitting them together well, etc. These questions had answers and they were implemented. It was a disaster. As Sandy noted, he hated how the early Model 3 wheel wells were constructed - too many parts, too many materials, too much labor. So Tesla had asked the wrong questions, and even though they had correct answers to those questions, it didn’t really provide the right solution. So Tesla engineers took a step back and asked the right questions - what does this part do, what does it need to made of and using Elon’s favorite design strategy - no part is the best part - how to eliminate the part. The result? Model Y rear structure megacasting - a single piece that replaces 70, is corrosion resistant, strong, and using the gigacasting machines, able to form complex shapes. As an added bonus, the removal of so many parts meant that 300 less robots were need to work on that section. Ask the right questions, get the right answer. Being vertically integrated allowed Tesla to move forward and scrap what wasn’t working for a whole new direction without dealing with suppliers, contracts or unions.UPDATE 04/13/21 - To the Moon and Beyond - Vertical Integration of Sustainable energyAs Gigafactory Texas takes shape, the first Gigapress is starting preliminary operations using large tanks of Liquid Natural Gas for its furnace to melt Tesla’s proprietary aluminum alloy. It is assumed that this will eventually be piped in through a large natural gas pipeline when the factory is in full operation.Musk’s warming up to gas evident once more at Texas GigafactoryFour tanker trucks belonging to a Houston-based liquefied natural gas company could be seen parked outside the Texas gigafactory construction sitehttps://www.detroitnews.com/story/business/autos/2021/03/30/musks-warming-up-gas-evident-once-more-texas-gigafactory/7060681002/Liquid Natural Gas is methane. Elon has shown a path to make even this process sustainable.Capture Carbon.XPRIZE Carbon RemovalTruly Meaningful Impact The world's leading scientists estimate that we may need to remove as much as 6 gigatons of CO2 per year by 2030, and 10 gigatons per year by 2050 to avoid the worst effects of climate change. For humanity to reach the Paris Agreements goal of limiting the Earth’s temperature rise to no more than 1.5˚(C) of pre-industrial levels, or even 2˚(C), we need bold, radical tech innovation and scale up that goes beyond limiting CO2 emissions, but actually removes CO2 already in the air and oceans. If humanity continues on a business-as-usual path, the global average temperature could increase 6˚(C) by the year 2100. This four-year global competition invites innovators and teams from anywhere on the planet to create and demonstrate solutions that can pull carbon dioxide directly from the atmosphere or oceans ultimately scaling massively to gigaton levels, locking away CO2 permanently in an environmentally benign way. Solutions will be scientifically evaluated across multiple criteria such as; amount of CO2 removed, life cycle analysis of the removal process, energy efficiency, land footprint and sequestration capabilities. Any carbon negative solution is eligible: nature-based, direct air capture, oceans, mineralization, or anything else that sequesters CO2 permanently.https://www.xprize.org/prizes/elonmusk2. Convert carbon to methane, using hydrogen made from water and energy from solar.Correct, pure electric. Wish orbital rockets could be so too, but there’s no escaping Newton’s Third Law. SpaceX is already developing high efficiency CO2 capture with H2O to form liquid CH4 (methane) & O2. Critical for propellant production at Mars Base Alpha.— Elon Musk (@elonmusk) June 10, 2018Sabatier reaction - WikipediaMethanation process of carbon dioxide with hydrogen The Sabatier reaction or Sabatier process produces methane and water from a reaction of hydrogen with carbon dioxide at elevated temperatures (optimally 300–400 °C) and pressures (perhaps 30 bar [1] ) in the presence of a nickel catalyst . It was discovered by the French chemists Paul Sabatier and Jean-Baptiste Senderens in 1897. Optionally, ruthenium on alumina (aluminium oxide) makes a more efficient catalyst. It is described by the following exothermic reaction . [2] CO 2 + 4 H 2 → pressure 400 ∘ C CH 4 + 2 H 2 O {\displaystyle {\ce {CO2{}+4H2->[{} \atop 400\ ^{\circ }{\ce {C}}][{\ce {pressure}}]CH4{}+2H2O}}} ∆ H = −165.0 kJ/mol There is disagreement on whether the CO 2 methanation occurs by first associatively adsorbing an adatom hydrogen and forming oxygen intermediates before hydrogenation or dissociating and forming a carbonyl before being hydrogenated. [3] CO + 3 H 2 ⟶ CH 4 + H 2 O {\displaystyle {\ce {{CO}+ 3H2 -> {CH4}+ H2O}}} ∆ H = −206 kJ/mol CO methanation is believed to occur through a dissociative mechanism where the carbon oxygen bond is broken before hydrogenation with an associative mechanism only being observed at high H 2 concentrations. Methanation reaction over different carried metal catalysts including Ni, [4] Ru [5] and Rh [6] has been widely investigated for the production of CH 4 from syngas and other power to gas initiatives. [3] Nickel is the most widely used catalyst due to its high selectivity and low cost. [2] Applications [ edit ] Creation of synthetic natural gas [ edit ] Methanation is an important step in the creation of synthetic or substitute natural gas (SNG). [7] Coal or wood undergo gasification which creates a producer gas that must undergo methaneation in order to produce a usable gas that just needs to undergo a final purification step. The first commercial synthetic gas plant opened in 1984 and is the Great Plains Synfuel plant in Beulah, North Dakota. [2] It is still operational and produces 1500 MW worth of SNG using coal as the carbon source. In the years since its opening, other commercial facilities have been opened using other carbon sources such as wood chips. [2] In France, the AFUL Chantrerie, located in Nantes, started in November 2017 the demonstrator MINERVE. This methanation unit of 14 Nm3 / day was carried out by Top Industrie, with the support of Leaf. This installation is used to feed a CNG station and to inject methane into the natural gas boiler. [8] It has been seen in a renewable-energy-dominated energy system to use the excess electricity generated by wind, solar photovoltaic, hydro, marine current, etc. to make hydrogen via water electrolysis and the subsequent application of the Sabatier reaction to make methane [9] [10] In contrast to a direct usage of hydrogen for transport or energy storage applications, [11] the methane can be injected into the existing gas network, which in many countries has one to two years of storage caphttps://en.wikipedia.org/wiki/Sabatier_reaction3. Use methane to heat the furnace for melting aluminum alloys.So vertical integration of energy sources - solar to methane to heat, will allow Tesla to continue to pursue its goal of sustainable energy, even while using conventional technologies such as a natural gas furnace.UPDATE 05/04/2021 - Alien Dreadnought vs. Chip ShortageAt the recent Q1 2021 Earnings Call, Elon mentioned that the chip shortage was a major problem and that Tesla was able to pivot and use other chips. This shows a huge advantage that Tesla has.Elon Musk says pandemic supply-chain issues and a global microchip shortage resulted in 'insane difficulties' for Tesla"We've had some of the most difficult supply chain challenges that we've ever experienced in the life of Tesla," Musk said, citing the chip shortage.https://www.businessinsider.com/elon-musk-tesla-supply-chain-issues-chip-shortage-insane-difficulties-2021-4#:~:text=Elon%20Musk%20told%20investors%20during,supply%20chain%20issues%20in%202021.&text=The%20CEO%20said%20the%20global,port%20delays%20impacted%20manufacturing%20goals.However, Tesla was able to INCREASE production during a shortage, rather than having to idle its plants for weeks and have decreased production.Tesla delivers another record in Q1/2021 - electrive.comTesla announced new record deliveries of 184,800 electric cars during the first quarter of 2021. Q1 of any year but especially this Covid-year is traditionally a slow quarter for car companies which makes it even more remarkable. Figuring in the numbers, Tesla delivered 184,800 electric cars to customers from January to March 2021, including 182,780 […]https://www.electrive.com/2021/04/05/tesla-reports-another-slight-delivery-record-in-q1-2021/#:~:text=For%20production%2C%20Tesla%20produced%20a,units%20made%20in%20Q4%2F2020.The only other car company not seriously impacted by the chip shortage? Toyota. Why? Because Toyota (proponent of Just In Time Manufacturing) actually does virtual Vertical Integration and forces it suppliers to maintain up to a 6 month stock of critical materials and parts.Why Toyota had a big pile of chips when semiconductor shortage dealt others a bad handToyota's good fortune in the global semiconductor shortage and is stockpile of key components in cars goes back a decade to the Fukushima disaster.https://www.autoblog.com/2021/03/09/toyota-how-it-avoided-semiconductor-shortageAs mentioned before, Tesla uses fewer, higher end chips in its EV’s, while traditional car makers use dozens of simpler, cheaper ones, basically every electronic system has its own simple chip.“Traditional manufacturers have relied on their suppliers for various car parts, and many of them are equipped with ECUs (Electronic Control Units) which are controlled by the individual suppliers. Tesla’s hardware, on the other hand, reduces this number from dozens of ECUs to just a few, making changes to the hardware and especially software updates much easier.Switching to such an electronic architecture would lead to major disruptions among car manufacturers and suppliers. The control over the ECUs would switch to the manufacturers, and with it the responsibility for faulty control systems etc. This threatens many jobs at the suppliers who are currently responsible for these control units.”Tesla Electronics Is 6 Years Ahead Of Other Car CompaniesThe struggle for dominance in the automotive sector is running along all fronts. If electric cars were “only” about batteries or electric motors, competitors might be able to catch up w…https://thelastdriverlicenseholder.com/2020/02/17/tesla-electronics-is-6-years-ahead-of-other-car-companies/This design where fewer, higher level chips, handle a variety of different functions allowed Tesla to pivot, find new suppliers of chips and then simply reprogram the EV’s firmware to adapt to the new chips.Design and manufacture of higher level chips, treating the EV like a smartphone or computer, is a key factor in the flexibility and value of the EV. This is a core reason Tesla is able to make so many changes and upgrades by simply sending an update over the air.Other car companies are just starting to see the value in this, and the chip shortage highlights how inadequate their current designs using many different, cheap, simple chips are.Volkswagen to design its own chips for its autonomous vehicles, says CEOBringing chip development in-house allows for better flexibility, Diess sayshttps://driving.ca/volkswagen/auto-news/industry/volkswagen-to-design-its-own-chips-for-its-autonomous-vehicles-says-ceoPeople are clamoring for Ford F-150s now trapped in Detroit parking lotFord is storing thousands of F-150s by the Detroit Department of Public Works even while dealers beg for products to sell.https://www.freep.com/story/money/cars/ford/2021/04/16/ford-f-150-semiconductor-chip-shortage/7175158002/
Why doesn't the U.S. government nationalize factories to produce ventilators like in WW2?
The government didn’t nationalize factories in WW2.An excellent book on how AMERICA mobilized without nationalization is “Freedom’s Forge: How American Business Produced A Victory in World War II” by Arthur Herman. Here is a short version of what is contained in the book“It didn't take William S. Knudsen long to make up his mind. President Roosevelt needed him, so there was only one answer the General Motors president could give.“In May 1940, the United States was still at peace but war was raging in Europe. Knudsen, a Danish immigrant, gathered family members in his Detroit living room and announced he was leaving GM to head FDR's new National Defense Advisory Commission.“The family was dumbfounded, said automotive historian and author Michael W.R. Davis. Then one child broke the silence to ask her father why he was doing that."This country has been good to me, and I want to pay it back," Knudsen said."Big Bill" Knudsen, who had become famous for his expertise in mass production, would lead a mobilization of U.S. industry to build the nation's defense arsenal.Military and Veteran Benefits, News, Veteran Jobs | By Ward Carroll“America wasn't at war as Hitler's military blitzkrieg'd its way across Poland in September of 1939, but the lessons that emerged from that swift German victory weren't lost on thought leaders – both in government and industry – in the United States. More than anything else the internal combustion engine had played the leading role in Nazi Germany's new type of warfare. The motorized Panzer Divisions made up of tanks and self-propelled artillery had thundered into Poland. Waves of Stuka dive bombers had terrorized civilians behind the Polish lines and destroyed communications to the rear. It was over in a matter of days. As Poland fell and Britain and France declared war on Germany, the U.S. government began to reach out to industrialists to dialog about proposed military requirements in the event the nation was dragged into the war. Among those companies that government reps approached was one that would ultimately provide the lion's share of hardware to the American military: General Motors. Two main factors made GM well suited to answer the nation's needs during the march to war: Corporate leadership had the right attitude about what had to be done, and the company divisions were structured with enough autonomy to allow them to tackle vastly different military production requirements moving forward. The right corporate leadership attitude started at the very top of GM. About the time the Nazis advanced into Holland, Belgium and France in the late spring of 1940, President Franklin D. Roosevelt asked GM's chief William S. Knudsen to head the new National Defense Advisory Commission. "Big Bill" felt like he had no choice but to accept the offer. As he told his daughter when she asked why he was making such a professionally risky move, Knudsen said, "This country has been good to me, and I want to pay it back." Knudsen relocated to Washington to lead the mobilization of American industry to build the nation's defense arsenal (a move that ultimately came with significant personal cost). Meanwhile back in Detroit the new GM president C.E. Wilson began shepherding the corporation into its "guns and butter" phase – the period where GM made its first moves towards manufacturing military hardware while maintaining a steady level of civilian-focused automobile production. Wilson challenged each GM division with basic military projects, ones that, where possible, to some degree fit with that division's commercial expertise and production facilities. These early efforts were done under the U.S. government's "Lend-Lease" program designed to assist the allies in the European Theater. In short order GM was tackling the manufacture of machine guns, rifles, and Navy guns to arm ships ferrying war supplies across the Atlantic. One of the first contracts with the French covered an order for 700 V-1710 Allison engines, but the delivery was never made because there was no agency on the French side to assume custody (or make payment) as the government crumbled in June – tangible evidence to an otherwise detached American workforce that the situation for our friends in Europe was rapidly deteriorating. Although GM might have been organizationally postured to answer the military's needs better than most large American companies at the time, that still didn't make the undertaking easy or immediate. In essence, GM was being asked by the United States government to start a new business. As the requirements came in it became obvious that GM's manpower was generally deficit in their understanding of what it was going to take to bridge the difference between material "on order" and material "on hand." Materials for defense were more highly stressed and had to be made with a greater degree of accuracy – which was to say, they were not designed with mass production in mind, at least not the auto industry's approach to mass production. A good example of this was the difference between the manufacture of a car engine and a military aircraft engine, something Allen Orth described in his internal corporate document titled "The War Years" written in 1956. In the paper Orth outlines that the Cadillac automobile engine, which was one of the finest in the automotive field, had been developed for nearly 30 years by an organization pressurized by continuous marketplace competition to develop max value per dollar of cost. The result was an engine weighing about six pounds per horsepower. Airplane engines, on the other hand, were designed around getting the greatest horsepower in a structure of the lowest possible weight and bulk, and that design yielded an engine that weighed only about one pound per horsepower. So as the Cadillac motor manufacturing line undertook the building of Allison-designed military airplane engines the team faced a steep learning curve, to put it mildly. Orth uses the differences in connecting rods as an example. The Cadillac engine required 25 matching operations while that for the Allison airplane engine required 93 operations – almost 4 times as many. There were two-tenths of a man hour of labor on the Cadillac rod compared to 11 man hours – 55 times more – on the Allison. And the Allison engine required not only more workers but more and radically different machine tools. The 10 months of GM's "guns and butter" period ended abruptly with the Japanese attack on Pearl Harbor. The nation forgot about peacetime products and clamored for war supplies. What had been defense production became war production. And in early 1942 GM completely dropped its commercial automobile business and turned entirely to the manufacture of military trucks, planes, engines, weapons, and ammunition. At the same time, 114,000 of the company's employees left to fight the war. As GM went "all-in" behind defeating the Axis Powers Lt. Gen. Brehon Somervell, the U.S. Army Supply Chief at the time, toured a few of the Michigan factories. At the tail-end of his visit he said, "When Hitler put his war on wheels, he ran it straight down our alley. When he hitched his chariot to an internal combustion engine, he opened up a new battle front – a front we know well. It is called Detroit."Military and Veteran Benefits, News, Veteran Jobs | By Ward Carroll“In February 1942, Fisher Body completely stopped making auto bodies and began assembling the famous M-4 "Sherman" tank in its No. 1 plant in Flint. The operation eventually moved to Grand Blanc and would turn out 11,358 tanks by 1945.“Buick tackled the manufacture of ammunition, churning out 75,000 casings per month for the duration. By the war's end, the division had supplied more than 12.5 million casings.Buick also retooled to meet the demands of making engines for the B-24 bomber. At first, they talked of about 500 engines a month, but the government doubled its order by the time Buick had its tooling in place. By 1944, Buick's Melrose Park factory was regularly turning out 2,000 engines a month.“To produce the cylinder heads, Buick set up its own aluminum foundry, which it then leased to the government. The initial production target was 25,000 a month, but that was tripled before construction began and the foundry had to be scaled up nine or 10 different times. The goal was later set at 125,000 heads a month, and Buick met it.“The Army also asked Buick to design a new kind of war machine: the tank destroyer. The specs called for a lightly armored, highly mobile tracked vehicle fitted with a 37mm cannon in a 360-degree turret. The Army initially wanted diesel power but settled on gasoline engines to speed up delivery. Buick even devised an automatic transmission for it -- a hydraulic torque converter.“The vehicle was officially known as the M-18, but Buick workers dubbed it the "Hellcat." The division eventually built 2,507 M-18s. The transmission was later made four times bigger to accommodate the requirements for the Pershing tank.“GM's Cadillac division took to making tanks, specifically the M-5. The design was obsolete, but at the beginning of America's involvement in World War II the Army wanted all of them it could get.“Down in Indianapolis, the V-1710 aircraft engine designed by GM's Allison division was a long way from being production-ready, and Allison was hopelessly short of production capacity. Yet it was a vital power unit, destined for both the twin-boom Lockheed P-38 "Lightning" and North American Aviation's P-51 "Mustang" fighters.“In time, GM's auto engineers developed the turbocharged V-12 that was probably the most advanced aircraft engine to see action during World War II. Cadillac's Clark Avenue home plant speeded its production by turning out the required crankshafts, connecting rods, camshafts, and reduction-gear assemblies.“Chevrolet plants produced shells, gun parts, and aircraft engines. The division made around 3,000 armored cars and built a light-armor half-track that saw action in General George Patton's North African campaign. Part of Chevy's Tarrytown plant built 1.5-ton trucks and ambulances for the U.S. Army, while another part produced wing section and fuselage components as a subcontractor to Grumman Aircraft.“Oldsmobile manufactured 48 million rounds of artillery ammunition, 140,000 aircraft machine guns, 350,000 high-precision aircraft engine parts, and 175 million pounds of forgings for military trucks, tanks, guns and aircraft.“Pontiac, as one ad at the time put it, "was at war nine months before Pearl Harbor," first making an anti-aircraft gun for the U.S. Navy and then clearing 200,000 square feet in its sheet metal plant to install the precision equipment needed to make the Swedish-designed Bofors automatic field guns for the U.S. Army.“Pontiac also supplied front axles for the M-5 tanks built by Cadillac and air-launched torpedoes for the U.S. Navy. The torpedoes were a challenge in that each one had 5,222 parts and 1,225 assemblies that had to fit inside a slim envelope about 20 feet long.“In all, more than 113,000 employees left GM to serve while the company churned out $12.3 billion in aircraft, tanks, vehicles and arms.“When it was all counted up after the war, GM had produced 854,000 trucks (including the legendary DUKW, or "Duck" amphibious vehicles), 198,000 diesel engines, 206,000 aircraft engines, and 38,000 tanks, tank destroyers, and armored vehicles, not to mention vast quantities of guns and ammunition.”How GM's Divisions Tackled the War Effort
- Home >
- Catalog >
- Business >
- Sign In Sheet Template >
- Equipment Sign Out Sheet >
- Equipment Sign-out Form >
- sign out sheet template excel >
- Supply Of Labor And Materials For The Installation Of Aluminum