How to Edit and draw up Downtime Report Claim Form For Online
Read the following instructions to use CocoDoc to start editing and drawing up your Downtime Report Claim Form For:
- To get started, seek the “Get Form” button and press it.
- Wait until Downtime Report Claim Form For is ready to use.
- Customize your document by using the toolbar on the top.
- Download your finished form and share it as you needed.
The Easiest Editing Tool for Modifying Downtime Report Claim Form For on Your Way
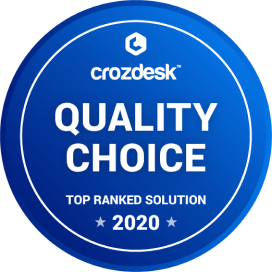
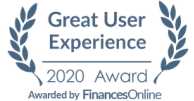
How to Edit Your PDF Downtime Report Claim Form For Online
Editing your form online is quite effortless. There is no need to download any software via your computer or phone to use this feature. CocoDoc offers an easy tool to edit your document directly through any web browser you use. The entire interface is well-organized.
Follow the step-by-step guide below to eidt your PDF files online:
- Browse CocoDoc official website from any web browser of the device where you have your file.
- Seek the ‘Edit PDF Online’ icon and press it.
- Then you will open this free tool page. Just drag and drop the PDF, or choose the file through the ‘Choose File’ option.
- Once the document is uploaded, you can edit it using the toolbar as you needed.
- When the modification is completed, tap the ‘Download’ option to save the file.
How to Edit Downtime Report Claim Form For on Windows
Windows is the most conventional operating system. However, Windows does not contain any default application that can directly edit PDF. In this case, you can download CocoDoc's desktop software for Windows, which can help you to work on documents effectively.
All you have to do is follow the steps below:
- Install CocoDoc software from your Windows Store.
- Open the software and then upload your PDF document.
- You can also select the PDF file from Google Drive.
- After that, edit the document as you needed by using the various tools on the top.
- Once done, you can now save the finished paper to your laptop. You can also check more details about how to modify PDF documents.
How to Edit Downtime Report Claim Form For on Mac
macOS comes with a default feature - Preview, to open PDF files. Although Mac users can view PDF files and even mark text on it, it does not support editing. Thanks to CocoDoc, you can edit your document on Mac quickly.
Follow the effortless guidelines below to start editing:
- First of All, install CocoDoc desktop app on your Mac computer.
- Then, upload your PDF file through the app.
- You can upload the PDF from any cloud storage, such as Dropbox, Google Drive, or OneDrive.
- Edit, fill and sign your template by utilizing this tool developed by CocoDoc.
- Lastly, download the PDF to save it on your device.
How to Edit PDF Downtime Report Claim Form For with G Suite
G Suite is a conventional Google's suite of intelligent apps, which is designed to make your job easier and increase collaboration between you and your colleagues. Integrating CocoDoc's PDF document editor with G Suite can help to accomplish work handily.
Here are the steps to do it:
- Open Google WorkPlace Marketplace on your laptop.
- Look for CocoDoc PDF Editor and get the add-on.
- Upload the PDF that you want to edit and find CocoDoc PDF Editor by selecting "Open with" in Drive.
- Edit and sign your template using the toolbar.
- Save the finished PDF file on your cloud storage.
PDF Editor FAQ
For police officers, what do you do to pass the time away in-between radio calls while on patrol?
Hahahaha! I'm guessing this question was really for the fire department? They get all kinds of time to watch movies, nap, make elaborate meals, wash their pretty fire trucks, etc.As a cop there are frequently nights when you don't even get a chance to get a bite to eat, let alone down time. Especially in the summer on a graveyard shift. I once spent 4 1/2 hours trying to respond to a suicidal guy's house. He called in saying he had a knife to his throat and wanted to die. The entire shift tried to respond out there numerous times, but we kept getting diverted to higher priority calls. We had a fatality MVA, a shooting, two stabbings, a gang fight with 15 to 20 people in the streets with knives and sticks and I shit you not, chains and bottles! Who the heck brings a chain to a gang fight!? Anyway, by the time I was able to respond to dude's house he got sick of waiting and went to bed. He claimed he didn't want to kill himself anymore and was mad that nobody ever came out to his threats.Being a cop is kind of like being an ER doctor. In Zimbabwe. During a bout of ethnic cleansing. You slap a bandaid on the battle ax wound and move on to the next call hoping things don't kick back off before the end of your shift.On the rare few moments you DO have downtime, you are still handling calls. Usually snatching up phone details and trying to catch up on reports. There is a TON of writing, documenting, making copies of photos, logging evidence, catching up with cases assigned to you for follow up, trying to clean the puke out of your back seat from the last drunk and generally trying to keep your head above water and not get into trouble for dropping the ball on something. Cops are expected to be PERFECT. Nobody holds cops to a higher standard than other cops. Unfortunately the reality is there isn't always the time available to devote to every situation as much as we would like.With that being said there have been a few times things were…well…the Q word (quiet). Shhhhh! Don't say it out loud! It angers the gods if you utter the Q word out loud. Anyway those rare occasions when you aren't running around like your hair is on fire AND are caught up on paper, you tend to do what you enjoy.I like to check my various “fishing holes” where I know people like to go for illegal activities. Those out of the way spots only dopers know about. If I can find a partner who isn't on a call, I also enjoy serving warrants. I like to keep at least one on hand of somebody who REALLY needs to go to jail. Some of the solid domestic violence types or child rapists. It brings me great joy when I get to arrest someone who truly needs to be arrested. Other guys like to run traffic or work on pet projects, like watching certain high crime doper compounds to see who is coming and going.In the end you are pretty much ALWAYS busy in some form or another. Even when it doesn't look like it. Ever see a few cops go wandering through a bar near closing time? Or seem to be hanging around out front? We are either looking for someone in particular, or looking to be a presence in the bar. A sort of visual cue that “Hey…maybe I should call a cab or NOT act like a dumbass right now.”You should contact your local agency and schedule a ride along. I think it would be a real eye opener!
What methods can I use to increase production capacity in a manufacturing plant? I'm focusing on capacity planning and control for my report.
First, determine that you have already maximized your current production capacity. All production problems can be summarized in 4M (Man, Material, Methods, Machinery). So, there you have it, the starting point. I have done this exercise so many times over the years that sometimes it confounds me that these basic elements have not been identified OR defined. Here is a list of some of the questions that need to be answered:Do you have an adequate labor pool?Is the labor pool properly trained?Is the labor pool assigned properly?Has the number of available production hours been maximized?Is there and adequate supply of raw material?Is the raw material being purchased in the optimum quantity and in the optimum configuration?Can some of the raw material be purchased in a prefinished form?Is the machinery running at full capacity?Is there too much downtime?Is there machinery that can increase the production rate?Is the machinery able to meet quality specifications on a continuous basis?Is the machinery utilized in the proper sequence?Is the floor plan conducive or a hindrance to production quantity?Are there operations that can be combined?Are there operations that can be eliminated?Are there operations that could be outsourced?This is just a small sampling of the questions I usually ask a client and the answers are generally discouraging. Has a Pareto Analysis been performed on every question? I have put together over the years a twenty something odd page list of questions that require significant investigation to make a determination and recommendation to my clients. More often than not I can generally get at least a 10%-20% increase in factory throughput without having to make major capital purchases. I always start with defining the problem and establishing the limits of the current capacity. Manpower is first on my list. Yield is second. It will surprise most to find that poor quality (direct loss) and rework are the fastest and cheapest ways to increase production throughput and yet are often overlooked. I will review machinery output currently achieved against vendors claims and downtime and maintenance schedules. A plant layout and analysis is essential and I will employ PERT, CPM, and Gantt Charts to lay the foundation for my review.Before I begin my work it is also imperative that my client express to me what they believe to be the current status of their operation and the operational goal of production capacity. In their own words that must tell me what they believe to be the current production capacity and what their perceived limitations are. They must accept ownership of the current state of affairs so that what comes back to them in my report is not only not a shock but can be examined with little personal embarrassment, because, believe me, it is personal to them and negative feedback reflects negatively on everyone at every step in the process including upper management. I have had clients that were very receptive to my reports and were relieved that significant improvement could be made at little to no expense and I have had clients that were adamant that they were doing things correctly and my report had too many errors. As is often said; Pride goeth before the fall.
What is Tesla's 'secret sauce' that even the biggest automakers can't replicate even though they've stripped down Teslas to study them?
Simple - Alien Dreadnought.Alien Dreadnought is what Elon calls the machine that builds the machine. When you take apart a Tesla, all you get are what parts there are and how they fit together. It tells you very little about the machine that puts it together.When you see two plates fastened together with a bolt, do you know if that bolt was installed and tightened by a person, a machine or a combination of both?Tesla has invested tremendously in automating the process to make stuff. From basic stuff like car seats to installing wiring harnesses in cars. Most car makers laughed when Tesla had to rip out a large portion of the Model 3 lines when robots couldn’t effectively install wiring harnesses. This missed the obvious point - wiring harnesses are hard, but if you can beat that manufacturing problem with robots, then pretty much the entire process can be done with robots.Thus with Model Y, a redesigned wiring harness with 90% less wire than the Model S and designed from the start to be handled by robots were patented by Tesla. We will have to wait to see if it actually makes it into production in 2020, but if it does, it means Tesla will be another step ahead of the competition.Vertical integration - as part of the machine that makes the machine, Tesla also ensures its part supply. By making its own parts it has total control of the quality and design of them, it can make compromises or absorb higher costs that a parts contractor might not be willing to do. This doesn’t show when you look at a part, all you can do is estimate how much it cost. By controlling all of these aspects, Tesla can make changes quickly and with less red tape and expense than a standard car maker who has to deal with separate parts suppliers.If you find a part that shows unique welding or shape from forming, you don’t necessarily know how it was done. All you can see is the final result. For instance, Tesla has patented a new casting machine to make the frame to the Model Y, a crazy machine that could reduce a car frame from 70 separate parts that need to be formed and assembled to a single piece. Tesla Goes Patent Crazy With Huge Casting Machine For Model YThat said, it doesn’t really matter that you can’t tell this process from just looking at the pieces. Tesla has released all its patents for any company to read and use. Most choose not to do so. All Our Patent Are Belong To YouUPDATE: 01/15/2020Thanks everyone for the Upvotes!With more comments from Elon regarding Full Self Driving being “feature complete” in 2020, the importance of Alien Dreadnought becomes more important. Software, AI and full self driving capabilities are definitely products that competitors can’t replicate simply by taking the car apart. Even looking at the software code, especially for the AI doesn’t tell you how Tesla got there.Tesla is pushing AI faster and farther, not just in the end product Self Driving AI, but in the training techniques and even the hardware used to run the software to train. This is all part of the Alien Dreadnought - build the machines that build the machines.Tesla Quietly Acquired a Machine Learning Startup That's 'Squeezing' A.I.As for the “parts supply” of this portion of the machine, it is driving data. And Tesla has worked hard to make sure it has a nearly endless supply of driving data. With every Tesla equipped with sensors and most equipped with the full self driving suite of sensors such as cameras, radar and ultrasonics, every Tesla on the road is feeding data back to Tesla, billions (with a B) of miles of it every year. To put that into perspective, Waymo just hit 20 million miles of data total, currently running about a million miles per month. Waymo’s autonomous cars have driven 20 million miles on public roadsAI’s train best on lots of unusual data. Having access to billions of miles means Tesla’s have probably seen lots of weird things on the road - flying cars, kangaroos, planes landing on the highway etc. And with Sentry cam, it can record things even while parked. Tesla's millions of cameras are capturing some crazy things - videos - Electrek This is useful for teaching the AI about human behavior, not just things that happen on roads, so perhaps in the future the AI can determine social interactions like “a fight is happening” and predict that people are going to run out into the road.By designing its own processing chip and designing teaching supercomputers like Dojo, Tesla continues to make the machines to make the machines. Something conventional automakers are completely unable to do.Elon Musk hints at Tesla's secret project 'Dojo' making the difference in race to full self-driving - ElectrekUpdate 02/24/2020And the Alien Dreadnought rolls on - Tesla Self Driving Computer, designed from a clean sheet of paper, puts Tesla years ahead of the competition. Designed in house using the best talent in the world and manufactured exclusively for Tesla by Samsung in Austin.Tesla Self-Driving Computer architect Jim Keller is confident about solving autonomous driving - ElectrekThe issue is not that other companies can’t design their own chips to match the technology, but they can’t get rid of their current contracts and manufacturers for years. Again, by bringing manufacturing in-house, Tesla continues to ensure the supply.“The real reason for holding off? Automakers worry that computers like Tesla’s will render obsolete the parts supply chains they have cultivated over decades, the engineer said. Such systems will drastically cut the number of electronic control units, or ECUs, in cars. For suppliers that depend on these components, and their employees, this is a matter of life and death.” Tesla teardown finds electronics 6 years ahead of Toyota and VWUPDATE 4/28/20Additional evidence that “Alien Dreadnought” is the correct path. VW has had to delay the release of the ID.3 due to “software issues.”. From a highly optimistic 2018 prediction that VW would be producing a vehicle to match Tesla for “half the price” by 2020 - VW Claims By 2020, Its Electric Cars Will Match Tesla At Half Price to the stark reality of having thousands of vehicles bricked and sitting in lots - VW ID.3: thousands of electric cars spotted being stockpiled in Germany - Electrek the reality of failing to invest in the machine to make the machine is evident. While the machine in this case is software, VW’s lack of investment in internal software development shows how unprepared the entire company is for the future of vehicle production.“Today, our share [self-developed software as a portion of all software in Volkswagen Group vehicles] is less than 10 percent. That is clearly too small. In the Volkswagen Group, we want to achieve a share in software development of more than 60 percent by 2025.”Volkswagen Software Comments — 10 Months Ago vs. TodayShortages of robots (Tesla bought the company VW was using), shortages of programmers (Tesla produces most of its software in house and already has a massive team of programmers), a lack of integrated design (VW is trying to integrate dozens of different hardware/software suppliers) all prevent VW from producing a viable vehicle at this time. The machine that makes the machine isn’t working.Now in discussions with Daimler-Benz to try to pool software resources, they are very late to the game and late to the realization that software is as important as hardware. Daimler flirtet mit BMW und VW Simply building the physical isn’t enough, what runs the car is as important, if not more important than the physical parts to producing a top rate EV.UPDATE 05/19/20VW is learning that the future of cars IS to treat them like smartphones. Their software issues now extend to a conventional model - The iconic VW Golf (Gen 8). Failure of the emergency call system is halting their delivery of even conventional vehicles because of software difficulties. Despite having 46 years of experience producing the Golf, VW seems very inexperienced with software. It will have a difficult time building the expertise to handle these problems, let alone getting ahead due to the huge demand worldwide for such expertise as EVERY carmaker realizes that software is the future of the car.https://www.motor1.com/news/423689/vw-golf-software-issues-arise/New Volkswagen Golf Mk. 8 Deliveries Stopped Over eCall Software IssueUPDATE 06/30/20Building the factories to house the machines that makes the machine.As proven by the build speed of Gigafactory 3 (Shanghai) going from a muddy field to a producing manufacturing line in less than one year and with the ground breaking and rapid build out of Gigafactory 4 (Berlin), Tesla shows how important Alien Dreadnought is. Knowing what processes and parts that need to be manufactured and scaling the buildings from the beginning allow Tesla to create a factory space rapidly and repeatedly. If Gigafactory 5 (Texas) becomes an operational reality in 2021, then Tesla will have built 3 operating mega factories in less than 3 years.Breaking! Tesla Gigafactory 3 Groundbreaking In China In A Few Hours — UPDATEDTesla’s Chinese factory just delivered its first carsTesla breaks ground on foundation at Gigafactory Berlin, brings in heavy machinery - ElectrekInteresting details during construction, especially regarding the Model Y. For American built Model Y’s, the back frame is two cast parts, not the one part envisioned in the patent.However, for Giga Shanghai and Fremont, new supersized casting machines were ordered.Tesla Giga Shanghai Could Be Constructing The Next Level Casting Machine for MIC Model YSo a single piece rear frame casting could come online this year for Model Y. I would assume that Giga Berlin will also be equipped with the “Gigapress” for European Model Y production.UPDATE 07/08/2020More signs that vertical integration, cross pollination and diverse investment can prove to be innovative. A bonus efficiency when you control all aspects of the Alien Dreadnought.So it appears that Tesla is looking for a visual image engineer to work at the new Fremont Battery Factory. Current theories run that Tesla is going to apply visual AI to the quality assurance process. This is an indicator that Tesla’s investment in AI, particularity visual AI will provide additional benefits other than driving.Quality control is one of Tesla’s biggest current problems. It involves inspecting pieces and work, identifying if they are correct or incorrect and then (sometimes) fixing the problem. This has traditionally been a human job since the variety of problems (paint problems, panel gaps, incorrectly installed wires, misted headlights, etc.) was too much to simply program in with a huge variety of visual cues. With an AI visually learning what a problem looks like and its thousands of variations, it could quickly be able to inspect, flag and note how to correct any imperfections during the manufacturing process, thus saving time and effort at a later date. Since it will be run by robots and AI, this means it will always be vigilant and always provide a complete inspection.“Vision Systems Engineer, Cell EngineeringSAVETeslaFremont, CAApply on LinkedInApply on Careers For Veterans At Tesla - Veteran HiringApply on Jobilize LLCApply on JobsApply on BIGHiredApply on LocalJobs.com25 days agoFull-timeThe RoleTelsa’s cell manufacturing engineering group is looking for a highly-motivated equipment development engineer to accelerate our next-generation battery cell manufacturing program. This role will be involved in the design, development, commissioning and ramping of high-throughput equipment, while working in a cross-functional team to test, validate, and roll-out process and product design changes. The battery cell is a critical component in Tesla vehicles and storage systems. This role will have the opportunity to make meaningful contributions to our products. The work environment is demanding, fast-paced and incredibly exciting. The ideal candidate should be ready to push their limits, as they join in a highly motivated and capable team to make unbelievable things into reality.Responsibilities • Drive design, commissioning ramp of a complex manufacturing tool that is the first of its kind at Tesla • Work collaboratively as the equipment expert to ensure production lines run in a safe, efficient manner producing high-quality parts. • Become owner/subject matter expert to drive equipment-related process improvement including detailed troubleshooting and root cause analysis. • Troubleshoot and recover processes by PLC, HMI, or tool management software, and implement changes/improvements • Build training material, maintenance routines, and related documentation for equipment life cycle management • Lead safety and ergonomic improvements to production equipment which meets or exceeds regulations or best practices. • Identify equipment critical spare parts and ensure sufficient coverage to prevent extended downtime situations • Participate in supplier/ internal equipment buyoffs • Debug and optimize automated processes to maximize cycle time and uptime. • Develop and manage FMEA risk assessments to prioritize equipment improvement projects and ensure sufficient repair strategies. • Provide hands-on support to the maintenance team to troubleshoot and resolve extended downtime situations. Requirements • Either a BS with 6+ years’ relevant experience or an MS with 3+ years relevant experience in interdisciplinary/integrated engineering, manufacturing engineering, or equivalent • Evidence of exceptional ability. • Strong engineering foundations. Aptitude to learn • Demonstrated experience ramping equipment into manufacturing - automation equipment, web handling, design of electromechanical systems, PLCs, motion controls, and data capture • Demonstrated experienced solving complex electromechanical and software systems with limited documentation to debug issues, build process know-how, and kick off improvement projects • Structured thinking and problem-solving abilities. Proven through a number of root cause analysis following a data-driven approach, statistical software (JMP) a plus • 2D ACAD experience in creating/validating layouts, tooling drawings, Pneumatic and electrical schematics • Experience with robot programming, backup, and restoration a plus • Experience in automotive or high volume manufacturing is highly desired”UPDATE 07/29/20Alien Dreadnought - Building edition. Tesla has gained sufficient experience to make even the manufacturing of factory buildings faster and more efficient. Pre-fab concrete panels to accelerate the building of Gigafactory Berlin.Giga Berlin will come together at an impossible-seeming speed. The prefabricated construction method in Germany is extremely impressive.— Elon Musk (@elonmusk) July 27, 2020Tesla Giga Berlin is coming together quickly thanks to prefabricated constructionWill Giga Berlin break the Giga China construction record? With Giga Texas already clearing land, will Texas be built even faster? With talks of a second China Gigafactory and another Gigafactory somewhere in Asia, the machine that makes the factories to hold the machines seems to be running faster and faster.UPDATE 09/23/20 - BATTERY DAYSo much vertical integration, Alien Dreadnought, and evidence that Tesla is not just an EV company. From investing in a new process to extract lithium from clay using water and salt and being able to return the dirt back into the ground, to producing larger, more capable batteries faster, cheaper and in less space than the 2170, utilizing new chemistry and integrating the battery pack as a primary structure, being able to recycle the batteries at the end of their life with minimal processing, Elon and Baglino showed how integrated manufacturing and vertical integration of the supply chain are the core of Tesla.Everything You Need To Know About Tesla's New 4680 Battery CellWhile it will take some time to ramp up production of the new 4680 cell, the pilot plant just down the street in Fremont is designed for 10 GWh of production, 1/3 that of Gigafactory Nevada in a building 12 times smaller. With limited production already beginning, design and testing of vehicles to use the new battery cell is well underway (Model S Plaid).Bigger batteries that are more efficient, cheaper to make, faster to make, more environmentally friendly and providing additional benefits to charging, structure, weight and longevity. All the result of Alien Dreadnought.UPDATE 10/28/20 - FULL SELF DRIVING BETALimited FSD beta releasing on Tuesday next week, as promised. This will, at first, be limited to a small number of people who are expert & careful drivers.— Elon Musk (@elonmusk) October 12, 2020With the recent release of FSD Beta, limited, it again highlights Tesla’s use of Alien Dreadnought. Since every recent Tesla with HW 3.0 chip is capable of FSD, Tesla has already built a test fleet of hundreds of thousands of vehicles. By slowing releasing beta to “expert & careful drivers” Tesla has recruited dozens if not hundreds of Tesla owners to test drive FSD, for free. Already on YouTube are hundreds of hours of video of FSD beta in action showing how it acts in all kinds of places, times, weather and situations. There are self reported testers in at least 9 states.Tesla Starts to Rollout Full Self-Driving FSD Beta for Different States' EAP MembersWhile the first days showed definite errors or quirks - always taking the leftmost turn lane even if there were two turn lanes, slowing, but not enough for speed bumps, mistaking an angle parked car as a moving car after a turn, taking longer to turn into traffic allowing a crossing car to come close, etc. patches are apparently fast and furious. With massive uploads of driving data - Tesla is collecting insane amount of data from its Full Self-Driving test fleet - Electrek Tesla is well positioned to acquire the data for cheap or free, have vast quantities of it, and apparently process it, use it to reteach the AI and update FSD within a day, if not hours. The machine to teach the machine is running fast and furious.Many of the “driver interventions” occur because FSD doesn’t drive in a fashion that makes the driver comfortable - staying in the center of a lane when there are parked cars rather than riding the dividing line, staying in the left lane when other cars are trying to pass, hitting speed bumps a bit fast, hitting the brakes at the last second, waiting too long to merge so the lagging car closes the gap quite close, etc. This information will be useful to Tesla in terms of creating a tolerable human interface, as many passengers, while quite safe with this driver, would find the experience unnerving.UPDATE 02/10/2021 -Elon Interview, Asking the right question.In an interview with Sandy Munro, Elon described why the first Model 3 wheel wells were a mess. As he mentions, they had many engineers working on the project and each one probably got the right answer for the part they were working on. One piece needed to be corrosion resistant, so the engineer picked the best corrosion resistant material, One part had a complex shape so that engineer picked a material that could be formed easily. One part was a heavy duty part that saw a lot of stress so that engineer picked a strong material. Individually each engineer came to the correct answer for her/his question. But the result was a mess - many parts, different materials, new problems in how to attach them together, new problems on how to seal the gaps due to difficulties in fitting them together well, etc. These questions had answers and they were implemented. It was a disaster. As Sandy noted, he hated how the early Model 3 wheel wells were constructed - too many parts, too many materials, too much labor. So Tesla had asked the wrong questions, and even though they had correct answers to those questions, it didn’t really provide the right solution. So Tesla engineers took a step back and asked the right questions - what does this part do, what does it need to made of and using Elon’s favorite design strategy - no part is the best part - how to eliminate the part. The result? Model Y rear structure megacasting - a single piece that replaces 70, is corrosion resistant, strong, and using the gigacasting machines, able to form complex shapes. As an added bonus, the removal of so many parts meant that 300 less robots were need to work on that section. Ask the right questions, get the right answer. Being vertically integrated allowed Tesla to move forward and scrap what wasn’t working for a whole new direction without dealing with suppliers, contracts or unions.UPDATE 04/13/21 - To the Moon and Beyond - Vertical Integration of Sustainable energyAs Gigafactory Texas takes shape, the first Gigapress is starting preliminary operations using large tanks of Liquid Natural Gas for its furnace to melt Tesla’s proprietary aluminum alloy. It is assumed that this will eventually be piped in through a large natural gas pipeline when the factory is in full operation.Musk’s warming up to gas evident once more at Texas GigafactoryFour tanker trucks belonging to a Houston-based liquefied natural gas company could be seen parked outside the Texas gigafactory construction sitehttps://www.detroitnews.com/story/business/autos/2021/03/30/musks-warming-up-gas-evident-once-more-texas-gigafactory/7060681002/Liquid Natural Gas is methane. Elon has shown a path to make even this process sustainable.Capture Carbon.XPRIZE Carbon RemovalTruly Meaningful Impact The world's leading scientists estimate that we may need to remove as much as 6 gigatons of CO2 per year by 2030, and 10 gigatons per year by 2050 to avoid the worst effects of climate change. For humanity to reach the Paris Agreements goal of limiting the Earth’s temperature rise to no more than 1.5˚(C) of pre-industrial levels, or even 2˚(C), we need bold, radical tech innovation and scale up that goes beyond limiting CO2 emissions, but actually removes CO2 already in the air and oceans. If humanity continues on a business-as-usual path, the global average temperature could increase 6˚(C) by the year 2100. This four-year global competition invites innovators and teams from anywhere on the planet to create and demonstrate solutions that can pull carbon dioxide directly from the atmosphere or oceans ultimately scaling massively to gigaton levels, locking away CO2 permanently in an environmentally benign way. Solutions will be scientifically evaluated across multiple criteria such as; amount of CO2 removed, life cycle analysis of the removal process, energy efficiency, land footprint and sequestration capabilities. Any carbon negative solution is eligible: nature-based, direct air capture, oceans, mineralization, or anything else that sequesters CO2 permanently.https://www.xprize.org/prizes/elonmusk2. Convert carbon to methane, using hydrogen made from water and energy from solar.Correct, pure electric. Wish orbital rockets could be so too, but there’s no escaping Newton’s Third Law. SpaceX is already developing high efficiency CO2 capture with H2O to form liquid CH4 (methane) & O2. Critical for propellant production at Mars Base Alpha.— Elon Musk (@elonmusk) June 10, 2018Sabatier reaction - WikipediaMethanation process of carbon dioxide with hydrogen The Sabatier reaction or Sabatier process produces methane and water from a reaction of hydrogen with carbon dioxide at elevated temperatures (optimally 300–400 °C) and pressures (perhaps 30 bar [1] ) in the presence of a nickel catalyst . It was discovered by the French chemists Paul Sabatier and Jean-Baptiste Senderens in 1897. Optionally, ruthenium on alumina (aluminium oxide) makes a more efficient catalyst. It is described by the following exothermic reaction . [2] CO 2 + 4 H 2 → pressure 400 ∘ C CH 4 + 2 H 2 O {\displaystyle {\ce {CO2{}+4H2->[{} \atop 400\ ^{\circ }{\ce {C}}][{\ce {pressure}}]CH4{}+2H2O}}} ∆ H = −165.0 kJ/mol There is disagreement on whether the CO 2 methanation occurs by first associatively adsorbing an adatom hydrogen and forming oxygen intermediates before hydrogenation or dissociating and forming a carbonyl before being hydrogenated. [3] CO + 3 H 2 ⟶ CH 4 + H 2 O {\displaystyle {\ce {{CO}+ 3H2 -> {CH4}+ H2O}}} ∆ H = −206 kJ/mol CO methanation is believed to occur through a dissociative mechanism where the carbon oxygen bond is broken before hydrogenation with an associative mechanism only being observed at high H 2 concentrations. Methanation reaction over different carried metal catalysts including Ni, [4] Ru [5] and Rh [6] has been widely investigated for the production of CH 4 from syngas and other power to gas initiatives. [3] Nickel is the most widely used catalyst due to its high selectivity and low cost. [2] Applications [ edit ] Creation of synthetic natural gas [ edit ] Methanation is an important step in the creation of synthetic or substitute natural gas (SNG). [7] Coal or wood undergo gasification which creates a producer gas that must undergo methaneation in order to produce a usable gas that just needs to undergo a final purification step. The first commercial synthetic gas plant opened in 1984 and is the Great Plains Synfuel plant in Beulah, North Dakota. [2] It is still operational and produces 1500 MW worth of SNG using coal as the carbon source. In the years since its opening, other commercial facilities have been opened using other carbon sources such as wood chips. [2] In France, the AFUL Chantrerie, located in Nantes, started in November 2017 the demonstrator MINERVE. This methanation unit of 14 Nm3 / day was carried out by Top Industrie, with the support of Leaf. This installation is used to feed a CNG station and to inject methane into the natural gas boiler. [8] It has been seen in a renewable-energy-dominated energy system to use the excess electricity generated by wind, solar photovoltaic, hydro, marine current, etc. to make hydrogen via water electrolysis and the subsequent application of the Sabatier reaction to make methane [9] [10] In contrast to a direct usage of hydrogen for transport or energy storage applications, [11] the methane can be injected into the existing gas network, which in many countries has one to two years of storage caphttps://en.wikipedia.org/wiki/Sabatier_reaction3. Use methane to heat the furnace for melting aluminum alloys.So vertical integration of energy sources - solar to methane to heat, will allow Tesla to continue to pursue its goal of sustainable energy, even while using conventional technologies such as a natural gas furnace.UPDATE 05/04/2021 - Alien Dreadnought vs. Chip ShortageAt the recent Q1 2021 Earnings Call, Elon mentioned that the chip shortage was a major problem and that Tesla was able to pivot and use other chips. This shows a huge advantage that Tesla has.Elon Musk says pandemic supply-chain issues and a global microchip shortage resulted in 'insane difficulties' for Tesla"We've had some of the most difficult supply chain challenges that we've ever experienced in the life of Tesla," Musk said, citing the chip shortage.https://www.businessinsider.com/elon-musk-tesla-supply-chain-issues-chip-shortage-insane-difficulties-2021-4#:~:text=Elon%20Musk%20told%20investors%20during,supply%20chain%20issues%20in%202021.&text=The%20CEO%20said%20the%20global,port%20delays%20impacted%20manufacturing%20goals.However, Tesla was able to INCREASE production during a shortage, rather than having to idle its plants for weeks and have decreased production.Tesla delivers another record in Q1/2021 - electrive.comTesla announced new record deliveries of 184,800 electric cars during the first quarter of 2021. Q1 of any year but especially this Covid-year is traditionally a slow quarter for car companies which makes it even more remarkable. Figuring in the numbers, Tesla delivered 184,800 electric cars to customers from January to March 2021, including 182,780 […]https://www.electrive.com/2021/04/05/tesla-reports-another-slight-delivery-record-in-q1-2021/#:~:text=For%20production%2C%20Tesla%20produced%20a,units%20made%20in%20Q4%2F2020.The only other car company not seriously impacted by the chip shortage? Toyota. Why? Because Toyota (proponent of Just In Time Manufacturing) actually does virtual Vertical Integration and forces it suppliers to maintain up to a 6 month stock of critical materials and parts.Why Toyota had a big pile of chips when semiconductor shortage dealt others a bad handToyota's good fortune in the global semiconductor shortage and is stockpile of key components in cars goes back a decade to the Fukushima disaster.https://www.autoblog.com/2021/03/09/toyota-how-it-avoided-semiconductor-shortageAs mentioned before, Tesla uses fewer, higher end chips in its EV’s, while traditional car makers use dozens of simpler, cheaper ones, basically every electronic system has its own simple chip.“Traditional manufacturers have relied on their suppliers for various car parts, and many of them are equipped with ECUs (Electronic Control Units) which are controlled by the individual suppliers. Tesla’s hardware, on the other hand, reduces this number from dozens of ECUs to just a few, making changes to the hardware and especially software updates much easier.Switching to such an electronic architecture would lead to major disruptions among car manufacturers and suppliers. The control over the ECUs would switch to the manufacturers, and with it the responsibility for faulty control systems etc. This threatens many jobs at the suppliers who are currently responsible for these control units.”Tesla Electronics Is 6 Years Ahead Of Other Car CompaniesThe struggle for dominance in the automotive sector is running along all fronts. If electric cars were “only” about batteries or electric motors, competitors might be able to catch up w…https://thelastdriverlicenseholder.com/2020/02/17/tesla-electronics-is-6-years-ahead-of-other-car-companies/This design where fewer, higher level chips, handle a variety of different functions allowed Tesla to pivot, find new suppliers of chips and then simply reprogram the EV’s firmware to adapt to the new chips.Design and manufacture of higher level chips, treating the EV like a smartphone or computer, is a key factor in the flexibility and value of the EV. This is a core reason Tesla is able to make so many changes and upgrades by simply sending an update over the air.Other car companies are just starting to see the value in this, and the chip shortage highlights how inadequate their current designs using many different, cheap, simple chips are.Volkswagen to design its own chips for its autonomous vehicles, says CEOBringing chip development in-house allows for better flexibility, Diess sayshttps://driving.ca/volkswagen/auto-news/industry/volkswagen-to-design-its-own-chips-for-its-autonomous-vehicles-says-ceoPeople are clamoring for Ford F-150s now trapped in Detroit parking lotFord is storing thousands of F-150s by the Detroit Department of Public Works even while dealers beg for products to sell.https://www.freep.com/story/money/cars/ford/2021/04/16/ford-f-150-semiconductor-chip-shortage/7175158002/
- Home >
- Catalog >
- Business >
- Report Template >
- Report Writing Format >
- Informal Reports Format >
- differences between formal and informal reports >
- Downtime Report Claim Form For