A Comprehensive Guide to Editing The Liquid Caustic Soda, Annual Supply
Below you can get an idea about how to edit and complete a Liquid Caustic Soda, Annual Supply step by step. Get started now.
- Push the“Get Form” Button below . Here you would be introduced into a dashboard making it possible for you to make edits on the document.
- Choose a tool you require from the toolbar that emerge in the dashboard.
- After editing, double check and press the button Download.
- Don't hesistate to contact us via [email protected] if you need some help.
The Most Powerful Tool to Edit and Complete The Liquid Caustic Soda, Annual Supply
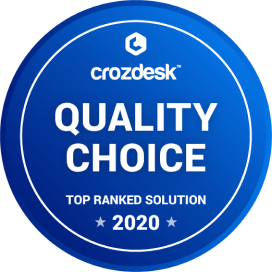
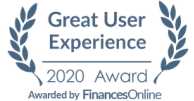
A Simple Manual to Edit Liquid Caustic Soda, Annual Supply Online
Are you seeking to edit forms online? CocoDoc is ready to give a helping hand with its comprehensive PDF toolset. You can make full use of it simply by opening any web brower. The whole process is easy and quick. Check below to find out
- go to the free PDF Editor Page of CocoDoc.
- Upload a document you want to edit by clicking Choose File or simply dragging or dropping.
- Conduct the desired edits on your document with the toolbar on the top of the dashboard.
- Download the file once it is finalized .
Steps in Editing Liquid Caustic Soda, Annual Supply on Windows
It's to find a default application which is able to help conduct edits to a PDF document. However, CocoDoc has come to your rescue. Take a look at the Manual below to find out possible methods to edit PDF on your Windows system.
- Begin by acquiring CocoDoc application into your PC.
- Upload your PDF in the dashboard and make alterations on it with the toolbar listed above
- After double checking, download or save the document.
- There area also many other methods to edit PDF files, you can check this post
A Comprehensive Handbook in Editing a Liquid Caustic Soda, Annual Supply on Mac
Thinking about how to edit PDF documents with your Mac? CocoDoc is ready to help you.. It allows you to edit documents in multiple ways. Get started now
- Install CocoDoc onto your Mac device or go to the CocoDoc website with a Mac browser. Select PDF paper from your Mac device. You can do so by pressing the tab Choose File, or by dropping or dragging. Edit the PDF document in the new dashboard which includes a full set of PDF tools. Save the file by downloading.
A Complete Instructions in Editing Liquid Caustic Soda, Annual Supply on G Suite
Intergating G Suite with PDF services is marvellous progess in technology, a blessing for you simplify your PDF editing process, making it faster and more cost-effective. Make use of CocoDoc's G Suite integration now.
Editing PDF on G Suite is as easy as it can be
- Visit Google WorkPlace Marketplace and get CocoDoc
- install the CocoDoc add-on into your Google account. Now you are able to edit documents.
- Select a file desired by pressing the tab Choose File and start editing.
- After making all necessary edits, download it into your device.
PDF Editor FAQ
How can I convert a harmful SO2 into some other gas and it should not be harmful?
Sulphur dioxide (SO2) is one of a group of highly reactive gases known as “oxides of sulphur”. SO2 is linked with a number of adverse effects on the respiratory system and other environmental issues. It is an important industrial emission gas which causes several difficulties in the environment like acid rain. Sulphur dioxide is a ubiquitous component of fuel combustion exhausts and one of the first air pollutants to be regulated all over world. Several approaches have been adopted to reduce SO2 content in the environment. One of the most difficult environmental problems facing industry is how to economically control SO2 emissions. Conversion of H2SO4 from SO2, which could be a great impact on reducing pollution. Production of sulphuric acid is one of the best choice considering its economical values and utilities. This paper addresses the different processes to control SO2 and to use SO2 in most economic and productive way to reduce SO2 effect inenvironment. A review of various treatment methods has been provided and a brief description of each process has been included and their technical applicability is also compared.KeywordsSulphuric acid; Sulphur dioxide; Scrubber; Reduction; OxidationIntroductionSix common air pollutants were identified as criteria pollutants in the Clean Air Act of 1970. Sulphur dioxide (SO2) is one of them, the other five being carbon monoxide, lead, nitrogen dioxide, ozone and particulate matter. High level of sulphur dioxide emission is associated with various ecological damages and health problems. Sulphur dioxide is harmful to health and it also contributes to acidification of soil and water. The major health issues are respiratory illness, breathing difficulties etc. [1]. Short-term exposure to SO2 may cause wheezing, chest tightness and shortness of breath. Longer-term exposure to sulphur dioxide in conjunction with high levels of particulate soot may result in respiratory illness, alterations in the lungs' defenses and aggravation of existing cardiovascular disease. The environmental effects of SO2 are detrimental. It reacts on the surface of a variety of airborne solid particles. It is soluble in water and can be oxidized within airborne water droplets to form sulphuric acid (H2SO4), which falls as acid precipitation, or “acid rain”. Acid rain pollutes and acidifies the soil.Combustion of conventional fuels i.e. hard coal and brown coal, oil and natural gas causepollution of the atmosphere with sulphur oxides (SO2 and SO3), nitrogen oxides (NOx) and dust. Discontinuing use of these energy sources in the nearest future seems unlikely. Hence, the only acceptable solution is application of appropriate technologies and equipment eliminating substances hazardous for the environment formed from fuels or after combustion of waste gases. The emission of SO2 from coal-fired boilers is regulated strictly in many countries. The increase in coal uses will also result in an increase in sulphur dioxide emission. There are many methods available for controlling the emission of SO2 of coal-fired boilers. Methods of removing SO2 from boiler and furnace exhaust gases have been studied for over 150 years. Tall flue gas stacks disperse emissions by diluting the pollutants in ambient air. Once SO2 is released into the atmosphere, it may be converted to other compounds and/or removed from the atmosphere by various mechanisms. Processes such as oxidation, wet deposition, dry deposition, absorption by vegetation and by soil, dissolution into water and other processes contribute to the removal of SO2 from the atmosphere. As recent environmental concern enforces more strict regulations of the emission of SO2, the treatment of SO2 in flue gas has attracted increasing attention. So the approaches to address this issue have been to reduce emission of SO2 as well as conversion of SO2 to sulphuric acid. Historically, there has been a multitude of processes for SO2 emission control.In flue gas cleaning processes, SO2 is usually removed by absorption with lime (CaOH2·2H2O) or other compounds having high alkalinity. State of-the-art desulphurization can remove more than 98% of the SO2 from the flue gas. SO2 is therefore removed from the atmosphere either unchanged or in the form of sulphuric acid and sulphates. The conversion of SO2 to sulphuric acid and sulphates represents approximately 10% of the rate of removal of SO2 from the atmosphere. The different process of sulphur dioxide removal from various sulphur operations and production of sulphuric acid from this SO2 is studied in this paper. It presents a detailed overview of the trends in control of SO2 emissions from industrial sources and also discusses technologies for production of sulphuric acid from SO2 emission. Broadly, the following discussions are presented in five sections. (1) Various sources of SO2 emissions are discussed. (2) Detailed overview of various approaches for SO2 emission control. (3) Selection of appropriate fluegas desulphurisation technique. (4) Trends in the technologies for recovery of sulphuric acid from SO2 emission (5) Conclusion.Sources of Sulphur DioxideSulphur dioxide and nitrogen oxides are regulated air pollutants. They are usually emitted from industrial, transportation and domestic activities and in many occasions simultaneously. Sulphur dioxide is introduced inenvironment as a result of both natural phenomena and anthropogenic activities such as combustion of fossil fuels, oxidation oforganic material in soil, volcanic eruptions,biomass combustion etc. [2]. Fossil fuels, including coal, oil and to a lesser extent gas, contain sulphur both in organic and inorganic form. Urbanization and industrialization contribute to the addition of SO2 in environment. Also meteorological condition affects significantly the amount of SO2 in environment.The largest sources of SO2 emissions are from fossil fuel combustion at power plants (73%) and other industrial facilities (20%). In a thermal power plant SO2 is generally produced when sulphur containing fuel is combusted. Smaller sources of SO2 emissions include industrial processes such as extracting metal from ore, and the burning of high sulphur containing fuels by locomotives, large ships, and non-road equipment.• Wood and cellulose rich biomass (<0.1 %)• Natural gas (0-15 percent)• Crude oil (0.3 to several percent)• Coal (0.5 to >3.0 percent)Fossil fuels like coal and crude oil deposits typically contain 1-2% sulphur by weight [3]. Combustion of fossil fuel thus is the major cause of anthropogenic emission of SO2 in the environment. SO2 is derived from various plants with other gases, like coal power plant, furnace off gases, sulphuric acid plants, cement industry, ship emission etc. [1,4-7]. The cargo and passenger ships sailing on sea routes were the largest sources of SO2 along with other pollutants like NOx and PM emissions of waterborne traffic in Finnish and nearby sea and lake areas in 2000.Sulphur dioxide is found in many industrial gases emanating from plants involved in roasting, smelting and sintering sulphide ores, or gases from power plants burning high sulphur coal or fuel oils or other sulphurous ores or other industrial operations involved in the combustion of sulphur-bearing fuels, such as fuel oil. One of the more difficult environmental problems facing industry is how to economically control SO2 emissions from these sources.Approaches and Strategies for SO2 Emission Control Various methods for SO2 control are based on either prevention of SO2 pollution or end-of-pipe treatment of flue gases. But small-scale flue gas cleaning is often impractical and not feasible; substitution of sulphur-containing fuels by clean fuel is desirable. Various approaches for controlling SO2 emissions include [8]:• Use of clean fuel: This includes either switching to a fuel with reduced amount of sulphur or else a reduction of fuel-sulphur before its firing. Since SO2 emissions are directly proportional to the sulphur content of fuel, and also to the amount of fired, a reduction in emissions can be achieved by switching to lowsulphur fuels and to higher quality ones.• Removal of sulphur from the fuel: This includes coal washing. Hence various cleaning methods have been developed for desulphurizing sulphur-bearing fuels prior to their firing. Sometimes this is associated with changes in the physical characteristic of the fuel, resulting in operational problems.• Preventing production and release of SO2 during combustion: Several technologies have been developed to control SO2 emission during combustion, however only few of them have been commercialized. The most developed are the fluidized bed combustion and integrated gasification combined cycle (IGCC).• Flue gas desulphurization: The end-of-pipe treatment is based on flue gas desulphurization (FGD). The flue gas is treated before it is emitted into the atmosphere via the stack.All of these methods can be used separately, or in conjunction with each other, depending on the quality of the fuel and the emissions requirements. The immediate focus of this paper is on flue gas desulphurisation (FGD) process. FGD technology is used to remove SO2 from exhaust flue gases. FGD systems have been installed and operated on many industrial and utility boilers and on some industrial processes for a number of years [9]. These systems are capable of removing approximately 70 to 90% of the SO2 in the flue gas, depending on the operating conditions of the system. Some systems have achieved an SO2-removal efficiency of greater than 95%.FGD technique offers several advantages such as:• Effect of concentration: Fuel contains sulphur in a more concentrated solid or liquid form; in flue gas it is considerably diluted by nitrogen and excess combustion air.• Effect of scale: Using clean fuel, desulphurized at refineries is simpler than installing pollution control at each small or medium-sized plant.• Resource conservation: Desulphurization separates sulphur from fuel, yielding elemental sulphur that is marketable, easily recovered, shipped and handled.Classification of FGD systemsIn order to minimise the adverse effects of sulphur dioxide and sulphur trioxide on the environment, many power plants and industrial facilities use flue gas desulphurisation (FGD) scrubbers to remove SO2 and SO3 from combustion gases. F1ue gas desulphurization systems can be broadly categorized as (1) Throw away or once through and (2) Recovery systems or regenerative system. In the throwaway systems, the sulphur removed from the flue gas is rejected from the process in a waste sludge [10]. In recovery systems, the sulphur-absorbing reagent is regenerated for recirculation to the flue gas contacting device and the sulphur removed from the flue gas is converted into its elemental form or into sulphuric acid.Both once-through and regenerative technologies can be classified into wet and dry types. The wet processes involve production of wet slurry wastes as by products. The flue gas leaving the absorbent is saturated with moisture. Regenaretive systems use expensive sorbents that are recovered by stripping sulphur oxides from the scrubbing medium. These produce useful by products including sulphur, sulphuric acid and gypsum. Recovery systems have generally higher capital costs than throwaway systems but lower waste disposal requirements and costs. The dry processes produce dry waste material and the flue gas leaving the absorbent is not saturated with moisture. SO2recovery efficiency of the dry processes (50-60%) is considerably less than the wet ones (93-98%) [9,11]. However, in recent times dry processes with more than 90% SO2removal efficiency are available.Wet scrubber: In the wet scrubbing technique, slurry of an alkaline chemical reagent is used to absorb SO2, and the gaseous SO2 is converted into either a liquid or solid by product. The dominant choices for commercial installations have been the wet, throwaway (lime/limestone) systems.Lime/limestone scrubbing: There are several types of wet nonregenerative processes. Among these lime/limestone scrubbing is the most popular. Frequently, limestone is used as the sorbent, generating gypsum as a by-product. Usually counter current vertical oriented spray tower is used as absorbent application. When the fraction of the CaSO4 is more than 15%, gypsum scale is formed. The lime stone forced oxidation (LSFO) process prevents this scale formation by forcing oxidation of CaSO3 to CaSO4 by blowing air into the reaction tank or into an additional hold tank.In the United States, over 90% of U.S. flue gas desulphurization system capacity uses lime or limestone. This trend will likely continue into the next phase of federally mandated SO2 reduction from coal burning power plants. These are about 80% of the market share and are used in large utility boilers. This is due to the high SO2removal efficiency achieved and low costs involved.Limestone/gypsum system: Globally the most commonly used flue gas desulphurization system is based on limestone/gypsum system. It involves mixing of crushed limestone/lime with water to form a slurry and spraying it into the sulphur containing flue gases. The sorbent reacts with SO2 and forms an aqueous slurry of calcium sulphite. About 90% SO2 removal can be achieved. Limestone-gypsum wet flue gas desulphurization method is most widely accepted due to its efficiency and reliability [12].Sodium (hydroxide) scrubbing: The throw away sodium FGD systems have been used mostly on industrial boilers. These systems use a sodium scrubbing liquor that is very efficient in absorbing SO2 emissions. They produce liquid wastes that can cause waste disposal problems. FGD systems used on utility boilers generate large quantities of liquid wastes. Therefore, throwaway-sodium systems have mainly been used on industrial boilers.Ammonia scrubbing: Ammonia is used as a reagent and by product is ammonium sulphite, which can be used as a fertilizer. Based on extensive operation of this process, several advantages have been reported by Evans et al. [2009] [13]. Unlike the calcium based wet FGD, no CO2is produced in this process, and waste water discharge is also minimized. Scaling or blockage problems are unlikely. However, high capital cost and a large footprint are the disadvantages [13].Seawater scrubbing process: Due to its natural alkalinity, seawater can absorb acidic gases. In this process, flue gases flow counter current to seawater in an absorption tower. The sea water gets heated and the flue gas is cooled. SO2 in the flue gases is absorbed by the sea water and then passes to a water treatment plant where further seawater is added to increase the pH. Air is supplied to oxidize the SO2 to sulphite and to saturate the seawater with oxygen. This system can remove up to 99% SO2. There is no disposal of waste to the land, but heavy metals and chlorides are present in the water released to the sear. Sea water scrubbing has found application in coal and oil-fired power plants, metal smelters, oil refineries, petrochemical industries and chemical processing plants. However, this process is suitable only for plants in the coastal area.Magnesium oxide: Magnesium oxide (MgO) slurry is sometimes used as an alternative. SO2 absorbed in the scrubber slurry forms insoluble magnesium sulphite (MgSO3), which is oxidized by injected oxygen to form MgSO4. MgSO3 and MgSO4 are used in acid plants to produce SO2for sulphuric acid production.Magnesium hydroxide: This process can achieve higher than 98% SO2 removal efficiency, and is compact, simple and involve less equipment [14]. Hence it has a low capital cost. Its use is much widespread in Japan.Spray dry system: Slurry of alkali sorbent is injected into the flue gases in a fine spray. Usually slaked lime is used as alkali sorbent. The water evaporates due to heat from the flue gases, and the flue gases get cooled. SO2 in the flue gases reacts with the drying sorbent to form a solid reaction product. No waste water is produced in this process.Circulating dry scrubber (or fluidized bed FGD): It has high SO2 removal efficiency with extremely low water consumption. It has the ability to bridge the size gap between spray dryer absorber and wet FGD technology.Wet regenerative processesWet regenerative processes include Wellman-Lord Process and DESONOX processes. The basic principles of the Wellman Lord process consist of removing highly diluted SO2 from the flue gas in the absorption section and then turning it into rich SO2 gas in the regeneration section. In the absorption stage, ash, hydrogen chloride, hydrogen fluoride and SO3 are removed as the hot flue gases are passed through a pre-scrubber. The gases are then cooled and fed into the absorption tower where a saturated solution of sodium sulphite is sprayed from the top onto the flue gases, which reacts with the SO2 to form sodium bisulphite. The concentrated bisulphite is then collected and passed to an evaporation system for regeneration. In the regeneration stage, steam is used to break down sodium bisulphite. The sodium sulphite produced is recycled back to the flue gases.Wellman-Lord FGD systems have been used to reduce SO2 emissions from utility and industrial boilers and from a number of industrial processes. These systems have the advantage of regenerating the scrubbing liquor and producing a saleable product instead of a sludge that can be a disposal problem. However, these systems are more expensive to install and operate than lime, limestone, or dualalkali systems. The DESONOX process is a combined catalytic process by which nitrogen oxides and sulphur dioxide are separated from the flue gas. Sulphuric acid is obtained as the final product which can be used in the chemical industry. Residual dust and aerosols are also collected from the flue gas.Dual alkali: A sodium hydroxide and sodium sulphite solution is used in the scrubbing system. Reaction of this solution with SO2produces a solution of sodium bisulphite and sodium sulphite. This reacts with lime or limestone outside the scrubber to produce a precipitate of calcium salts containing calcium sulphite. After dewatering the solids are disposed of in a landfill. The liquid fraction containing soluble salts is recirculated to the absorber. The use of dualalkali systems on utility boilers is attractive because of their ability to remove SO2 very efficiently and to reduce scaling problems. The system has zero liquid discharge and eliminates the need for a waste water discharge permit. Using lime to capture the SO2 reduces operating costs as compared to using either caustic or soda ash.Dry and semi-dry scrubbingThere are four types of dry/semi-dry FGD - spray dryer absorber (SDA), sorbent injection, and dry circulating FGD. Both sorbent injection and spray dryer absorber processes are non-regenerative processes. The most common choice to date for dry scrubbing has been the spray dryer absorber, which is actually a semi-dry process. In this process atomized lime slurry is sprayed into the flue gas within the reaction vessel. SO2 reacts with the atomized slurry to form calcium sulphite (CaSO3). A part of the CaSO3 reacts with oxygen to form calcium sulphite (CaSO4). The dried reacted particulates are collected at the downstream in an electrostatic precipitator or fabric filter. This process requires production of correctly sized lime slurry droplets and proper residence time such that the particulates are dry but well related when reaching the ESP or fabric filters. Although well-proven, this process can be difficult.Sorbent Injection technologies require relatively low capital cost. A sorbent is injected into the boiler or flue gas Dry Injection type processes are available with lime, trona, activated carbon and other dry reagents. Such systems with more than 90% have been developed. The activity of sorbents are dependent on temperatures, e.g., activated carbon (<100oC), alumina- and silica-supported sorbents (300oC), alumina- CaO (120-240oC but regeenration with H2 at 750-850oC). Since the flue gas temperatures in the burners range between 120oC to 250oC, SO2 removal in this temperature is economical for industrial applications [14]. In circulating FGD solid lime and recirculated byproduct are injected together. Hydrated lime is injected directly in the CFB reactor. Water is injected independently. SO2 removal efficiency of 93-97% can be achieved at a Ca/S molar ratio of 1.2-1.5. The process does not require any high maintenance mechanical equipment.To address the issue of lower desuphurization efficiency of semi dry processes as compared to wet processes, powder particle spouted bed was developed [15]. Increasing the utilization of lime in semi-dry/dry FGD systems is one of the current challenges researchers have to deal with. Most of the approaches that have been applied to increase the performance of the sorbent make use of the capacity of the additive to increase the surface area of CaO. The reactivity of hydrated sorbents is closely related to the sorbent surface area. Inorganic hygroscopic salts such as barium, potassium, sodium and calcium chlorides and nitrates of sodium and calcium have been found to be effective in increasing the performance of hydrated lime. Some of the siliceous materials which are viable for conditioning of the hydrated material include fly ash, bottom ash and incinerator ash. Palm oil ash has also been used.Selection of FGD ProcessesDue to differences in site conditions, available resources, and waste stream requirements, SO2 removal solutions are very site and process specific. Key design considerations to consider when selecting a scrubbing technology include inlet SO2 concentration and variation, efficiency and outlet concentration requirements, scrubbing liquor pH, liquid-to-gas ratio, prevention of scaling and plugging, liquid and gas distribution and contact, by-product handling and disposal, remoteness of site etc. The regenerative FGD process is suitable for high concentrations of SO2 such as copper converting units. The concentrated SO2 stream from the regenerative methods can then be reduced to elemental sulphur with CH4, H2 or CO. The throw-away method is well suited for coal-based power plants with lower SO2 concentrations (about 1000 rpm). Lime is the most important material used. About 70% of the FGD capacity in the United States use wet lime scrubbing with forced oxidation (LSFO), wet lime scrubbing with magnesium enhanced lime (MEL), or dry lime scrubbing using conventional spray dryer absorber. Dry lime scrubbing with circulating fluidized bed absorber is more widely used in Europe. Approximately 75% of the FGD systems installed on utility boilers are either lime or limestone scrubbing.There have been significant improvements in the wet lime processes in recent years that have improved its performance and reliability, and reduced capital and operating costs. Such improvements include use of a single absorber module for power generating units with (capacity 500 MW and greater and increase in sulphur dioxide removal efficiency (>95%).The advantages of the wet scrubbing process are relatively high removal efficiency (90-95%), low cost of operation, minimal safety hazards (explosion, fires), and ability to collect both gas and particulate matters. However the disadvantages are wet waste production (contaminated scrubber liquid), formation of highly corrosive acids, and high power requirements. Waste water treatment is required in wet scrubbing systems. The waste stream produced contains sodium sulfite (for sodium based system), ammonium sulphite (for ammonia based systems) and gypsum (for limestone based systems). Although spray towers are most common, the Chiyoda and Alstom Flowpack immersion technologies and the Advatech Double Contact Flow Scrubber have gained some market share.In terms of space requirement, the regenerative systems have little or no requirement for reagent preparation area. However, they require significant resources and space for solvent regeneration. Both regenerable and non regenerable systems can produce a saleable byproduct. However, since the markets for sodium sulphite or gypsum are limited, it is more common for the caustic, lime and limestone non regenerable systems to direct their byproducts to waste. On the other hand, the regenerable systems direct SO2 into sulphuric acid or elemental sulphur markets. SO2 can often be readily absorbed by the sulphur recovery units existing in most refineries, yielding elemental sulphur as a by-product.Although the most common desulphurization methods are the “Wet” types, the total and the annual costs of the “Dry” ones are considerably less, due to simplicity, less water consumption and easier residues handling. The “Dry” methods are easily installed and require less space. Hence, they are good choices for the existing units modernization [16,17]. FGD can be classified as wet, semidry [15], dry process. Since the SO2 recovery efficiency in “Dry” methods (50-60%) is considerably less than the “Wet” ones (93-98%), the dry methods are recommended in cases where SO2 emission is low.The scale of operation also influences selection of appropriate FGD technology. For example, the wet scrubber technology used in utility power plants is too large and costly for solid waste incinerators. On the other hand dry sorbent injection may be more suitable option for these applications due to low capital cost, small footprint, ease of operation, and flexibility to fuel changes. A new type of gas scrubber called the double-contact flow scrubber (DCFS) for flue gas desulphurization has been developed which achieved energy conservation together with high desulphurization and high dedusting efficiencies by spouting absorbent liquid from the new type of nozzles located at the bottom of the scrubber to ensure the better gas liquid contact [15].The amount of energy consumed by an FGD process has a direct impact on the power plants heat rate and also on the available net electric generating capacity. The amount of sulphur to be removed depends upon the sulphur content of coal and the emissions control of the requirement. The following table gives an overall comparison of SO2 control systems [18] .Recovery of Sulphuric AcidVarious raw materials that can be used to manufacture sulphuric acid include elemental sulphur, sulphide ores, spent acid and gases like H2S. When elemental sulphur is used, solid sulphur is melted and the liquefied sulphur is then purified and burnt to produce sulphur dioxide. The gases are cooled and then passed through a multi-stage converter system. The conversion steps include (i) Conversion of SO2 into SO3 (ii) Absorption of SO3 in H2SO4 for form H2SO4, with addition of appropriate amount of water to maintain the concentration of H2SO4.Regenerative SO2 recovery systems are available, which are effective for variety of tail gases with varying SO2 concentrations [23]. Processes for adsorption of SO2 in activated carbon beds and periodical regeneration of the carbon with water washing to produce dilute H2SO4 of 15-20% concentration have been around since decades [24].Production of sulphuric acid is considered to be the most viable option of sulphur recovery from smelter off gas and abatement of SO2 emissions to the atmosphere. Thus processing of the SO2off-gas to sulphuric acid at pyrometallurgical smelters based on sulphidic ore concentrates of copper, nickel, lead or zinc, is a well-established process. In process development for metallurgical sulphuric acid plants a major objective has been to enable the operation with very high SO2 concentrations, while simultaneously avoiding the generation of diluted gas.Among the various FGD processes [25], the DeSONOX process produces sulphuric acid as the end product. Sulphuric acid can be produced in the Wellman-Lord Process by aqueous absorption and desorption, concentration and then oxidation of concentrated SO2 to sulphuric acid catalytically [15,26]. The wet gas sulphuric acid (WSA) technology developed by Haldor Topsoe is a very popular and well accepted method to remove SO2 and recover it in the form of concentrated sulphuric acid of commercial grade. In a WSA plant, SO2conversion is similar to the SO2 conversion in a conventional acid plant based on absorption, except the catalytic conversion takes place in a wet gas. The WSA technology treats the furnace off-gas directly from upstream gas cleaning plants. No further drying is required, since the humidity present in the off-gas is used to hydrate the SO3 generated in the converter and produce sulphuric acid. More than 55 countries use the WSA technology developed by Halder Topse. Applications include refineries, coal gasification, metallurgical and mineral industry, power plant. The heat generated during the oxidation, hydration and condensation processes is principally reused in the process to preheat the off-gas to the required temperature level, and also to generate high pressure superheated steam for process use. This advantage of steam production, coupled with lower water and power consumption requirements, is particularly important in the African production environment. Having fewer process components than conventional acid plants, the WSA technology is a simple and compact operation, which makes it easier to retrofit into an existing smelter plant. Further, the WSA technology simultaneously offers the possibility to treat multiple gas streams arising within the production facility due to superior flexibility in terms of SO2 concentration and turndown ratio.There are two main limitations of the WSA technology. The concentrations of SO2 in the feed gas inlet should be restricted to 6-7% by volume. This is due to the need of restricting the dew points of sulphuric acid to around 260oC, from the consideration of the construction materials in the WSA condenser. Dilution of the gas with atmospheric air to overcome this limitation would increase the volume of the gas leading to the increase in the dimension of the plant. Secondly, since it is a single-contact process, the conversion is limited to typically 99.4 - 99.7%. Scrubbing of tail gas with caustic or hydrogen peroxide results higher conversion, but at the expense of additional investment and operating cost.To address these issues, Topsoe has introduced the WSA-DC technology (“DC” means double condensation), that can accept feed gases with SO2 concentrations of 13 volume% or higher. This technology is suitable only for applications where the water vapour content of the gas is controllable. H2S gas with high water vapour content would result in production of acid of lower concentration.The SNOx process is based on the WSA process and also includes integrated selective catalytic reduction DeNOx step. The SNOx process removes sulphur dioxide, nitrogen oxides and particulates from the flue gas, the sulphur is recovered as concentrated sulphuric acid and the nitrogen oxides are reduced to free nitrogen. The process involves catalytic reactions and does not consume water or absorbents[14,27]. Apart from the separated dust, no other waste is produced. Since this process can also handle other sulphurous streams, it is highly interesting in refineries. SNOx process increases thermal efficiency and reduces CO2 emission when using high sulphur coal for power generation. The main advantages of this process are excellent heat recovery, reduced CO2emission, no process chemicals, no process water consumption, no production of waste solids and liquids, valuable sulphuric acid product, clean technology and low operating and maintenance cost.MECS Sulfox technology is also a popular and well accepted technology to produce sulphuric acid from sulphur off gases. This is based on thermal and catalytic conversion of SO2 into sulphuric acid. MECS also developed single stage HRS which also reduced the investment cost in heat recovery system installed in sulphuric acid plant. The benefits of this technology are no liquid effluent other than sulphuric acid (the product), very low acid mist emission, high SO2 conversion so low SO2 emission, use of proven catalyst and low operating cost.Emerging TrendsR&D efforts towards improvement of FGD technologies are directed towards addressing various issues that impact the cost, SO2 absorption efficiency and energy consumption. Much of the research efforts on the limestone/gypsum process have been directed towards understanding the absorption process, which is a complex one due to the presence of soluble microparticles in the slurry [28]. Conventional wet limestone-gypsum FGD process has the problem of poor limestone utilization since limestone is not a very reactive reagent and does not completely dissolve in the scrubber system [Liu et al 2008]. Limestone is pulverized to an average size of 5 to 20 lm (95% a 325 mesh) to improve its utilization, reduce FGD operating costs and solid-waste disposal volumes, and improve reliability as well as gypsum quality. However pulverization is associated with significant amount of power consumption and further increases the operation costs. Avoiding the requirement of additional power for pulverization has been a major focus for R&D efforts towards improvement of conventional wet limestone-gypsum FGD process. One of the approach for increasing absorption efficiency is the addition of amine. Reversible hydration and ionization reactions that take place for dissolved SO2 in water solution and produce bisulphite and sulphite. Adding the amine, to the water increases the quantity of SO2 dissolved as the amine drives the equilibria to the right by reacting with the hydrogen ions. Requirement of a large column packed with various packings or spray tower, rotating-stream tray scrubber, etc in the traditional SO2 absorption process is responsible for high capital and operating costs. Improvement in mass transfer efficiency can reduce the size of columns. Process intensification can play an important role in this regard. In this context, rotating packed bed (RPB) has been studied [29]. It rotates a doughnut-shaped packing element to generate a centrifugal acceleration as high as several hundred folds of g to intensify mass transfer efficiency. Many gasliquid contacting processes, such as distillation, absorption, extraction, desulphurization, deaeration, reactive precipitation, chemosynthesis, removal of dust, and making nano-material employ RPB.To reduce the cost of flue gas purification, development of new technologies and equipments of simultaneous flue gas desulphurization and denitrification has become the leading research direction in the air pollution control field. In the recent years, the interests in simultaneous desulphurization and denitrification of flue gas increased rapidly. Many technologies have been proposed, among which the simultaneous removal of sulphur dioxide and nitrogen dioxide by using wet scrubber is most growing one.ConclusionSulphur dioxide emission control is expected to assume more and more significance with the emission norms becoming even more stringent in future. At the same time SO2 treatment methods need to have minimum waste disposal requirements, and also economical. Considering these, production of sulphuric acid is one of the best choice considering its economical values and utilities. The possibility of stricter regulations regarding GHG emissions in future may raise issues related to conventional wet scrubbing technologies in utilities. The limestone-sulphur dioxide reaction produces carbon-dioxide. On the other hand use of lime of mag-lime in wet scrubbers can be cost prohibitive [30,31]. The purpose of this study is to review the various methods of emission reduction of SO2, the installation and operational cost as well as good environmental performance. Although many of the processes for FGD are established since long, need for reducing cost, energy consumption and SO2removal efficiency are driving further R&D efforts. Various techniques for process intensification may play an important role towards development of better processes for SO2 removal and generation of by-products like H2SO4
- Home >
- Catalog >
- Life >
- Letterhead Template >
- Church Letterhead Template >
- Liquid Caustic Soda, Annual Supply