How to Edit Your Aircraft Battery Maintenance Work Order Online Lightning Fast
Follow these steps to get your Aircraft Battery Maintenance Work Order edited with ease:
- Select the Get Form button on this page.
- You will enter into our PDF editor.
- Edit your file with our easy-to-use features, like highlighting, blackout, and other tools in the top toolbar.
- Hit the Download button and download your all-set document for reference in the future.
We Are Proud of Letting You Edit Aircraft Battery Maintenance Work Order With a Simplified Workload
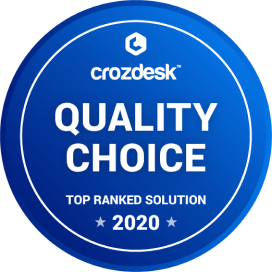
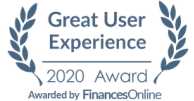
How to Edit Your Aircraft Battery Maintenance Work Order Online
When you edit your document, you may need to add text, Add the date, and do other editing. CocoDoc makes it very easy to edit your form just in your browser. Let's see how to finish your work quickly.
- Select the Get Form button on this page.
- You will enter into our PDF text editor.
- Once you enter into our editor, click the tool icon in the top toolbar to edit your form, like checking and highlighting.
- To add date, click the Date icon, hold and drag the generated date to the field you need to fill in.
- Change the default date by deleting the default and inserting a desired date in the box.
- Click OK to verify your added date and click the Download button for the different purpose.
How to Edit Text for Your Aircraft Battery Maintenance Work Order with Adobe DC on Windows
Adobe DC on Windows is a popular tool to edit your file on a PC. This is especially useful when you finish the job about file edit in your local environment. So, let'get started.
- Find and open the Adobe DC app on Windows.
- Find and click the Edit PDF tool.
- Click the Select a File button and upload a file for editing.
- Click a text box to optimize the text font, size, and other formats.
- Select File > Save or File > Save As to verify your change to Aircraft Battery Maintenance Work Order.
How to Edit Your Aircraft Battery Maintenance Work Order With Adobe Dc on Mac
- Find the intended file to be edited and Open it with the Adobe DC for Mac.
- Navigate to and click Edit PDF from the right position.
- Edit your form as needed by selecting the tool from the top toolbar.
- Click the Fill & Sign tool and select the Sign icon in the top toolbar to make you own signature.
- Select File > Save save all editing.
How to Edit your Aircraft Battery Maintenance Work Order from G Suite with CocoDoc
Like using G Suite for your work to sign a form? You can edit your form in Google Drive with CocoDoc, so you can fill out your PDF just in your favorite workspace.
- Add CocoDoc for Google Drive add-on.
- In the Drive, browse through a form to be filed and right click it and select Open With.
- Select the CocoDoc PDF option, and allow your Google account to integrate into CocoDoc in the popup windows.
- Choose the PDF Editor option to begin your filling process.
- Click the tool in the top toolbar to edit your Aircraft Battery Maintenance Work Order on the needed position, like signing and adding text.
- Click the Download button in the case you may lost the change.
PDF Editor FAQ
What will happen when a Tesla gets old? Will it have to be junked?
^ ABC7 News~~~~Q. What will happen when a Tesla gets old? Will it have to be junked?A. For old or wrecked Teslas:I imagine that a multi-level repair system will constellate—either one designed and developed by Tesla, AND/OR the market will provide.AND, IMO, most parts of a Tesla will last a long long time before they need work—except if they are in an accident.So the real question, I think, is what will happen to wrecked Teslas?~~~~In the US military, aircraft are kept in working order, often, for decades, despite damage, wear and tear. In order to do this, there are different levels of maintenance and repair facilities:Local—Squadron-level MaintenanceThese have personnel generally trained and outfitted to R&R—remove and replace—major assemblies and consumable parts. They do not do major rebuilding of engines and transmissions, or computers. They simply take the old one out and put in the new or remanufactured “RFI”—ready for issue—replacement part or assemblyRegional AIMD—Aircraft Intermediate Maintenance DepartmentCan do more sophisticated work, with more highly trained specialists and special equipmentNational Depot-level Repair and RemanufactureEven more sophisticatedFactory-level Repair and RemanufactureMost sophisticatedToday, Tesla is talking about making more highly integrated major assemblies like complex castings that replace hundreds of parts, or even batteries within castings.^ TesmanianTesla Battery Day: Revolutionary Casting Alloy Requires No Heat Treating or Coating~~~~Replacing many parts with a few large assemblies saves weight and complexity, and especially number of parts. But what happens when that major assembly gets squished in an accident, or just gets old and starts failing?Will the local service center repair it?Maybe not.Maybe fixing such a sophisticated component will require shipping to one of very few facilities that has the trained personnel, test equipment and proper tools.DETAILSI am not saying big parts will not be repaired. I am saying that they likely will not be repaired locally, but at a higher level and more central facility. So I am saying that large assemblies will be locally removed and replaced (R&Red), and the old part or “core” will be reconditioned, remanufactured or recycled.My experience that relates is: I am a former US Navy Pilot who did maintenance and post maintenance check flights. It was my job to flight test the aircraft with the guidance of trained maintenance personnel, help the team diagnose problems and identify the failing parts/assemblies. Then the local maintenance crew would remove the old parts that were no longer operating within limits—and replace with RFI—Ready For Issue—”new” parts. Or send the aircraft “up” to the next level.That old part that was removed might go to an AIMD—Aircraft Intermediate Maintenance Department. The intermediate-level repair facilities were few. But these areas had the expertise to make the part like new. Or it would go to the higher depot-level repair facility, or even back to the factory, if needed.By instituting this system, it was common for aircraft to be kept in good working order for many decades.MORE DETAILSI flew and did maintenance on a number of aircraft in the Navy. One type was the large H-53 helicopters. I started flying H-53s in 1982.Most of the airframes I was flying already had a decade on them, and some H-53 aircraft, I am told, flew for 40+ years before they were scrapped or sold for civilian use. This despite daily flights, often in extreme weather and hostile environments, including exposure to salt water, abrasive sandstorms, excessive heat and cold, and even in war zones.How was this possible?Local maintainers only removed and replaced major assemblies and small “consumables” parts, because they were not specialized enough and did not have the correct tools to do major assembly diagnosis, remanufacture, calibration, testing and configuration.For example, a jet (turbine) engine has fine tolerances and is difficult to disassemble and reassemble. Today, almost all military aircraft use turbines—even helicopters and propeller aircraft have a “jet” engine inside.To even figure out what blades have eroded too much, you need special tools—especially NDI—non-destructive inspection—tools. These can be huge and expensive pieces of equipment that cannot be afforded in every local repair facility. And to use these well takes personnel years of training and specialization.Nondestructive testing - WikipediaNDIHere are some examples of NDI equipment:—Dye penetrant—this is the cheapest and easiest to use, and would often be available locally^ X-ray vault—X-ray (just like the doctor uses on our bodies)—Neutron scanning—Gamma ray scanning—Ultrasonic Imaging (like medical ultrasound)SYSTEM ORGANIZATION INTO LEVELS / STRATIFICATIONIt is like the medical system:Internal diagnosis of the major parts of a sophisticated machine…is just like going to the hospital for a human with major disease.Hospitals have sophisticated equipment and specialists that are too costly to have at every small local clinic. You may have to travel hundreds of miles to go to a hospital that specializes in a certain issue—to find the right specialist physicians and techs with the right equipment.I think it may be the same for Teslas—there will be regional or national centers—like the Navy’s Depot-level repair facilities, or areas of specialization located within the factories themselves.This is also how my own company does it—major repairs and remanufacture/rebuilding, major updating and upgrading of very expensive equipment comes back to the factory. Because we have the trained people, test equipment, and tools to do the work, that would be too expensive to replicate elsewhere.Some old parts are cheaper to just trash, but large assemblies that are not obsolete will not be thrown out. They will be rebuilt or the parts or metals recycled.HOW IT IS DONE WHERE I LIVE TODAY — EXAMPLE: SUBARUMajor AssembliesRemanufactured engines and transmissions are one source of parts, and the other is parts from wrecks.For example, on my Subaru, I had the engine rebuilt by pros, here in the US.But, if the car had been in better shape, I would have bought a superior remanufactured engine from Subaru Japan. My 2001 Subaru was starting to show significant wear in all parts in 2018, so instead of getting a new engine that should last 180,000 miles, I got a local rebuild that I think will last 100,000. The rebuild kit came from the Factory. But the labor was local.For a car that would last a long time, a factory reconditioned or remanufactured item is always superior to something that is done in a local shop, IMO. Because the guys in the factory do ONLY that, and have superior tools, parts and knowledge. And the warranty is great on most remanufactured items.The same local pros got a Subaru transmission and catalytic converter from a low mileage wreck, when I needed those. This swapping out of major assemblies is something I think we will see much of when a Tesla wrecks or needs a new battery.I don’t think it will be as common for a local garage to repair a battery—as opposed to replacing.The replaced battery “core” then WILL BE reused in another application—like home storage battery…or will be repaired in a depot-level or factory-level repair facility that can make it “like new,” or it will be recycled. While there may be local mechanics who specialize in battery reconditioning, I doubt it will ever be as good as work done at Tesla.o
Do airplane wheels begin rotation before touchdown to match speeds?
As an engineer, I spend my days buried deep inside aircraft maintenance manuals writing courses to train mechanics on business jet maintenance. I've read a lot of the answers, but none of them have convinced me completely. Let me just address some of the recurring themes:"The pilots don't like it because they won't know when the plane has touched down": Planes are already fitted with WoW (weight-on-wheels) switches, that trigger when the landing gear shocks are compressed by the weight of the plane. They're used by many of the avionics onboard to switch them between "flight" mode and "ground" mode (for example, on some aircraft types the WoW signal triggers the ground spoilers upon landing and kills the auto-throttle). Adding a cockpit indication when the aircraft is on the ground would be a trivial matter. You could add an indication on the PFD (primary flight display) or an aural alert that speaks the word "touchdown" to the pilot when it happens. The hardware is already there; what's another indication to add to the other 500 already there, or another aural alert to add to the existing 50?"The gyroscopic forces affect the handling of the plane": Two issues here. First of all, while it's true that spinning wheels generate gyroscopic forces, the weight of the wheels is so small relative to the weight of the plane that I doubt gyroscopic precession is going to make much of a difference. Remember you have two or more engines weighing multiple tonnes onboard, and their high-pressure turbines and compressors are spinning at 15,000 RPM. No one complains of precession effects from those, so what difference are a few wheels at 1000rpm going to make? Secondly, even if they did pose a precession problem, most modern airliners use fly-by-wire (with the exception of the Boeing 737). Since that uses data from the IRS (Inertial Reference System) and other sensors to determine what the plane is actually doing, then makes the appropriate control surface motions to get the plane to do what the pilot is commanding it to, the existing system, as fitted to current planes, will automatically compensate for any gyroscopic effects of the spun wheels without any software changes."You'll need lots of power to spin up the wheels": Nope. You only need the system to operate briefly before landing (short duty cycle), and it only needs to accelerate a few hundred kilos (weight of rim and tyre) to ~1000rpm, which isn't that big a deal. So you can use small components and work them hard (but briefly). Fortunately, there's already a component on every plane that does something very similar. Presenting... the ATS (Air Turbine Starter):The ATS is the unit that I've indicated with a red circle.Here's what it looks like from the other end:It is responsible for starting the entire engine you see in the picture (in this case it's a CFM56 - used on Boeing 737s and Airbus A320s). It's a small turbine that uses compressed air from the APU (auxiliary power unit), or from a ground start cart, or from a running engine (if the plane has one already started) to spin up the engine during startup. That little thing accelerates the entire high pressure (N2) spool of the engine (weighing several tons) from zero to over 7,000 rpm in about 30 seconds when the pilot hits the starter switch. The downside is that you can only use it for about 5 minutes at a time before it needs to cool down (plenty of time to start an engine though). Looking at the size of the starter relative to the engine, I reckon a proportionately scaled-down turbine, sized for spinning just a wheel and tyre, would weigh not more than a few tens of kilograms. A hydraulic or electric solution would be similar in size and weight."What if it breaks? Then the plane would be grounded and the airline would lose money!": Nope. Your plane has what's called an MEL (Minimum Equipment List). It's a list of items that have to be working or you can't legally fly. Since this item is optional (you can still land fine with wheels not pre-spun up), and it would be coupled via a one-way clutch so the wheels can still spin if it jams (same protection fitted to current ATS units so the engine can keep spinning if the ATS seizes), then it won't be an MEL item; i.e. planes are free to take off and land normally if it's broken.I suspect what's really holding things back is steep certification requirements. You need time and lots and lots of money to prove to the authorities that something is safe enough for use on an aircraft. It's why gasoline piston engines for aircraft are still based on 1960s designs... and why the 787 uses lithium-cobalt batteries, when safer chemestries have been invented since it was certified. It's just too expensive to certify these things and there isn't enough return on investment to cover that cost. Ironically it sometimes leads to a worse-performing and less safe aircraft, but it's the best system humanity could develop in 110 years of aviation.There are some advantages of the wheel-spinning-up system no one else seems to have mentioned. Imagine you make the motors big enough to propel the plane at slow speeds (0-30mph). And you make the APU generator a little bigger. You now have a plane that can taxi without starting the engines.Imagine that - the passengers board the plane (with the APU already started up, to supply the air conditioning), the pilot "drives" it to the runway using electric power alone (engines still off, APU supplying the electricity for the motors in the wheels), then starts the engines while waiting near the runway. You've just saved a good 20 minutes of fuel burn and wear & tear on the main engines, and all it cost you was a few wheel motors and a larger APU (which planes like the 787 already have). So I think it's not a matter of "if", but a matter of "when" the economic advantages of engine-off taxiing outweigh any disadvantages of this system, and it becomes a standard feature of all passenger airliners.
Why was Captain Pearson punished for Air Canada Flight 143 (July 23, 1983) when he actually saved hundreds of lives by gliding the plane superbly?
TL; DR — Air Canada chose to lay the majority of the blame on Pearson as he was the captain of the flight. This was successfully appealed. However for a good read, keep reading.I'm not a pilot, but as my dad was a pilot for AC at the time and a union representative, I got the union side of things on this accident. I have also read the TSB report.Some location shorthand:YEG — Edmonton International Airport.YUL — Montreal Dorval International Airport at the time, now Pierre Elliott Trudeau International Airport. Trivia: Pierre was Justin Trudeau's father.YOW — Ottawa International Airport.YWG — Winnipeg International Airport.Facts and events before the accident:The aircraft had a manufacturing defect in the fuel quantity indicator system processor. The fault was one the computer was not programmed to handle so the computer blanked the fuel gauge displays.There were no spare processors available.The day before in YEG a maintenance technician discovered that if he disconnected the channel of the processor with the fault (the processor has two channels) the gauges worked. He pulled the relevant breaker, put a tag on it to warn people to leave it pulled and wrote it up in the log book that the aircraft was cleared to fly so long as the fuel gauge readings were confirmed with a manual drip check. (Like checking the oil level in your car.) The aircraft flew to YUL the next day with no problems.After arrival in YUL, a maintenance technician decided to run his own tests on the fuel quantity indicator system. He reset the breaker which caused the gauges to go blank. After completing his tests he was distracted by the arrival of the pilots and the refueller, did not pull the breaker again nor remove the breaker tag. Neither the pilots nor the refueller noticed the breaker was not pulled and as the gauges weren't working as stated in the log book, the blank gauges were not a surprise.Based on the published Minimum Equipment List (MEL) the aircraft was not legal to operate with the gauges blank. When the pilots pointed this out, the maintenance technicians convinced the pilots that the aircraft was cleared to fly by Maintenance Central. (Later during the investigation it was found that this was total baloney.) The pilots acquiesced to the technician’s explanations however Captain Pearson elected to load all the fuel necessary to fly all the way to YEG; normally they would have only loaded enough fuel to fly to YOW. This decision likely prevented a greater tragedy had the aircraft ran out of fuel on approach to YOW and crashed in a populated area.The necessary fuel was calculated for the trip to YEG with a stop in YOW. As others mentioned the AC 767s were calibrated in metric. The fuel load was thus in kilograms. The refueller's truck measured fuel in litres and all of the other aircraft types in AC's fleet at the time measured fuel in pounds. It is not hard to see where this is going. Kerosene weighs 1.77 pounds per litre but only 0.8 kilograms pet litre. Normally the refueller connects the hose, enters the desired total fuel quantity in kilograms into the aircraft's refueling panel and the aircraft quenches its' own thirst. With the computer inoperative, the fueling had to be done manually including the conversion of litres into kilograms. The refueller and the pilots both used 1.77 instead of 0.8 and the aircraft only had 40% of the fuel load required and the same error was made on the manual drip check.The flight left YUL and during the stopover in YOW the tanks were drip checked again and the same math error occurred.Once airborne and enroute from YOW to YEG the stage was set for one of the best feats of airmanship. Here is brief list of events:About halfway to YEG, the pilots get their first indication of trouble — a low fuel pump pressure warning followed by a second.Pearson wasted no time and diverted the flight to YWG. A descent was started and at about 35,000 ft. one engine quit and shortly after that the second one quit as well. Everyone was now in a large glider with no thrust, no electrical power save for the batteries and no hydraulics. The pilots lost their electronic instruments and had to rely on standby instruments. As Captain Pearson put it, he had less instrumentation than a Piper Cub.Fortunately Boeing built in a failsafe — the ram air turbine. This little gizmo popped into the slipstream and its' propeller driven pump provided limited hydraulic pressure for the flight control surfaces. It would not however power the landing gear or flaps.Between the pilots and ATC they worked on gliding to YWG. As this was the days before ‘green dot’ best glide speed indication (all Airbus pilots know about this,) Pearson had to figure out his best guess for a speed that would produce the best range. As a private glider pilot he had experience to draw on.Eventually they figured out they weren't going to make it. ATC offered Gimli, an retired air force base. F/O Quintal, having been based there when he was in the military, knew the field. They headed for Gimli. What they didn't know was that the runways had been converted into a dragstrip.With no hydraulics to lower the landing gear, the gear was lowered by gravity. The mains clunked into place and locked, but because the nose gear swings forward when it drops, the slipstream did not allow it to lock. This would help later.Approaching Gimli, Pearson realized they were too high. Not wanting to risk running out of altitude or stalling while executing a 360º turn, Pearson drew on his glider experience again and executed a maneuver called a forward slip, where the plane is banked in one direction and the rudder applied in the opposite direction. The result is the aircraft maintains its' heading and speed, but descends much more quickly.Just before touchdown Pearson leveled out and flared, but because there were no flaps, at a much higher speed. He touched down 600 ft into the ideal touchdown zone (usually the first 1000 ft of a runway.) Some tires blew from the high speed and when the nose settled, the nose gear collapsed back into the wheel well and the plane slid on its' nose.The pilots noticed some kids on bikes on the runway (remember the runway is now a dragstrip,) and they see a guardrail that had been installed to create the strip racing lanes. He maneuvered using the brakes to rub up against the guardrail and the aircraft managed to stop without hitting anyone.No one was injured during the landing and the aircraft was evacuated using the slides. Because of the nose down attitude, the rear slides were steeper than normal and some passengers were injured sliding down these slides.When the tanks were checked they were dry.The aircraft was patched up enough to be fueled and flown to YWG for repairs and ultimately was returned to service. The Gimli Glider flew until 2008 when it was retired and sent to an aviation boneyard in the Mojave Desert for storage and eventual scrapping.So at what point could all of this been prevented? There were many, these are some:Had there been spare parts on hand.Had the YEG technician documented better.Had the YUL technician not been interrupted and/or returned and pulled the breaker.Had the correct conversion constant been used by 3 people (the pilots and the refuellers) both in YUL and YOW.Had AC ordered its’ 767s with imperial measure.Had AC provided better training on manual refueling procedures for the 767.Had the maintenance technicians not lied to the pilots over the legality of flying the aircraft as it was.Had the pilots refused to operate the flight.As there were so many who made errors along the way, the pilot's union thought it unfair to pin all the blame on Captain Pearson and F/O Quintal. The review board (not the TSB) agreed and their suspensions were overturned.I will also add what one comment mentioned: As I recall my father telling me, Air Canada put six different crews into a 767 simulator and recreated the scenario. None of the six managed to land the aircraft intact. I originally thought the TSB did this, but it was not mentioned in the report. If I'm wrong I'll have to get the memory chips in my head cleaned again.See the TSB's report: https://reports.aviation-safety.net/1983/19830723-0_B762_C-GAUN.pdfIf you don't have the time, here's the Wikipedia entry: Gimli Glider - WikipediaEdit: Wow! 20k views in less than 24 hours. I never thought that 35 years after the fact that the Gimli Glider would still draw such interest. My own is obvious from my father's connection to it and my love of aviation. Thanks for reading!Edit #2: Made some grammatical corrections and some factual changes after re-reading the TSB report to refresh my memory. Also made some readability changes. Thanks again for reading!Edit #3: After some more comments, I've decided to do a Paul Harvey and add the rest of the story. Enjoy and thanks again for reading!
- Home >
- Catalog >
- Business >
- Order Template >
- Work Order Template >
- Work Order Form >
- job order format >
- Aircraft Battery Maintenance Work Order