How to Edit and draw up Outbound Bill Of Lading Shipping Label Online
Read the following instructions to use CocoDoc to start editing and finalizing your Outbound Bill Of Lading Shipping Label:
- To start with, look for the “Get Form” button and click on it.
- Wait until Outbound Bill Of Lading Shipping Label is appeared.
- Customize your document by using the toolbar on the top.
- Download your finished form and share it as you needed.
The Easiest Editing Tool for Modifying Outbound Bill Of Lading Shipping Label on Your Way
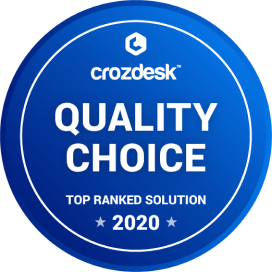
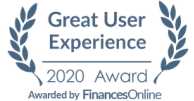
How to Edit Your PDF Outbound Bill Of Lading Shipping Label Online
Editing your form online is quite effortless. You don't need to install any software through your computer or phone to use this feature. CocoDoc offers an easy tool to edit your document directly through any web browser you use. The entire interface is well-organized.
Follow the step-by-step guide below to eidt your PDF files online:
- Browse CocoDoc official website on your laptop where you have your file.
- Seek the ‘Edit PDF Online’ option and click on it.
- Then you will open this tool page. Just drag and drop the form, or attach the file through the ‘Choose File’ option.
- Once the document is uploaded, you can edit it using the toolbar as you needed.
- When the modification is completed, press the ‘Download’ button to save the file.
How to Edit Outbound Bill Of Lading Shipping Label on Windows
Windows is the most conventional operating system. However, Windows does not contain any default application that can directly edit template. In this case, you can install CocoDoc's desktop software for Windows, which can help you to work on documents efficiently.
All you have to do is follow the steps below:
- Install CocoDoc software from your Windows Store.
- Open the software and then import your PDF document.
- You can also import the PDF file from OneDrive.
- After that, edit the document as you needed by using the varied tools on the top.
- Once done, you can now save the finished form to your laptop. You can also check more details about editing PDF.
How to Edit Outbound Bill Of Lading Shipping Label on Mac
macOS comes with a default feature - Preview, to open PDF files. Although Mac users can view PDF files and even mark text on it, it does not support editing. By using CocoDoc, you can edit your document on Mac without hassle.
Follow the effortless instructions below to start editing:
- At first, install CocoDoc desktop app on your Mac computer.
- Then, import your PDF file through the app.
- You can upload the template from any cloud storage, such as Dropbox, Google Drive, or OneDrive.
- Edit, fill and sign your template by utilizing some online tools.
- Lastly, download the template to save it on your device.
How to Edit PDF Outbound Bill Of Lading Shipping Label via G Suite
G Suite is a conventional Google's suite of intelligent apps, which is designed to make your work faster and increase collaboration between you and your colleagues. Integrating CocoDoc's PDF file editor with G Suite can help to accomplish work handily.
Here are the steps to do it:
- Open Google WorkPlace Marketplace on your laptop.
- Look for CocoDoc PDF Editor and download the add-on.
- Upload the template that you want to edit and find CocoDoc PDF Editor by choosing "Open with" in Drive.
- Edit and sign your template using the toolbar.
- Save the finished PDF file on your computer.
PDF Editor FAQ
How do Amazon employees on the warehouse floor receive an order when it has been placed?
ALRIGHT, well, working in an AR facility, I can divulge some of what I know about how orders are processed. Non-AR facilities do use a hand-cart and PDA for Order Picking; however, Amazon is trying to retrofit a lot of these facilities with Robotics. Therefore, Batch Order Picking is handled by KIVA Robotic technology at these facilities. Each KIVA robot, which floats around the floor like an orange hockey puck, has on top of it a large yellow “pod,” each filled with a seemingly random selection of items. Each ‘location’ has a specific QR code so the facility can keep track of what items belong to what Seller. These robots inhabit a ‘cage’ and these groups of ‘cages’ makeup a ‘mod.’Orders come in a variety of different ways. When a day starts, there is a certain number of ‘Predicted Charge’ for the day. This number of orders is based on historical data as well as what we believe our numbers will be based on sales, promotions, inventory on-site, and many other factors. Pick Managers and Process Assistants can ‘open’ and ‘close’ Process Paths which are basically destination locations for Pick Totes, and so can remote Operations Managers who run flow for certain regions, especially for transshipment. The company uses an algorithm called ‘Spock’ which evenly distributes inventory between certain FCs due to historical customer demand and ‘deadweight,’ which essentially means low-demand items that are taking up too much space in the FC and need to be transported to make room for higher-demand items.Process Paths can range from customer orders, to vendor returns, to transshipment, to destroy orders, to liquidation orders, to gift wrap, to even charitable donation orders. There are about 30–40 different types of orders that can be placed by customers, managers, Spock, or by the system running on its own performing live order requests in real-time. Customer orders are, of course, prioritized, but in general, ‘Fast Track,’ or Same/Next or Second Day (Prime 2-Day) Shipping, orders are highly prioritized without a hard cap on Shipping cost if CPT (Critical Pull Time, more on that later) is missed, whereas the ‘standard’ orders are put in the ’not prioritized’ pool and are usually hard-capped at a certain shipping cost; the maximum that Amazon is willing to spend. ‘Premium’ orders can be considered ‘Standard’ or ‘No Rush Delivery,’ and International Shipments which can take sometimes 1–2 weeks to reach the destination. ‘Super Saver’ is at the bottom of the barrel, and covers FEW customer orders, but mainly Spock’s distributive inventory requests and deadweight transshipment. The group that makes Shipping decisions is called ATROPS (Adaptive Transportation Operations Systems? I think?), and always chooses the most cost-effective Ship method, but also the one which makes the most sense with what is departing the FC and at what time. Certain trailer loads can only handle so much, so the Cubiscan technology built in to all SLAMs (more on this later) detects exactly which orders are going where by box identifier barcode, and can change the Shipment or Carrier at whim by data pulled from SSP (can’t remember what that stands for but the group programs all Sort Center and Outbound Shipping software). If a Shipment is deemed to too big to fit in the trailer the Ship Clerks ordered for that particular sort based on cubic volume, it can be reassigned to another sort which may depart later in the day but still hits the Promised Ship By Date.On to Customer Shipment Order Batch Picking: picking is done in AR facilities at ‘Nike’ stations (I don’t know the connection between companies), which will automatically highlight the particular ‘bin’ in the ‘pod’ that needs to be picked. The items are picked to a tote, and depending on whether the customer ordered single or multiple-item shipments, is then routed to the department which would handle such Shipments.Pack Singles has (in our particular facility), three different “arms”—Singles Large, which may handle items like personal fans on up to desk printers, Slam-at-Pack, which handles smaller items like books, jewelry, DVDs, etc, and ‘SmartPac’ which polybags bigger items which normally might have been designated for standard cardboard boxes. SmartPac associates are sometimes asked to put liquid items, such as multiple quantities of Windex, inside these polybags, because even if the item were to explode during transit, other items surrounding the bag would not be “hit” as it would with a normal Amazon box or manilla envelope. The polybag is then sealed by the SmartPac machine and sent down the line.Pack-Multi, or AFE (Amazon Fulfillment Engine) works differently in AR vs non-AR facilities. Pack Multi usually involves a tote full of a few customer orders. AFE is a lot more involved. Items which arrive in a tote are separated one-by-one into ‘sort trays’ which are run through a sorter. They then arrive at a ‘re-bin’ station, in which the ‘sort tray’ is scanned against a laser on and then directly ‘binned’ again (as the original Stower was the first ‘binner’ when placing the item into a designated bin in a KIVA Pod—yes, we’re back to that again!). Items are not packed out until the order (or at least all items available at that particular FC for the order) have arrived in the corresponding bin or chute. Sometimes, it can be several hours before all items arrive, depending on the Shipment priority. The Packer (or Chuter as they are sometimes called) is directed to Pack these completed shipments if the facility is using a Directed Pack system. If not, the Chuter usually has free reign to pack whatever they choose, but Directed Pack is more efficient and most likely being retrofitted to some legacy FCs.The packer upon completion, whether in a Multi- or Singles pack scenario, then attaches a sticker which is then ‘scanned’ with customer information. If you notice on most Amazon packages you receive, there is usually a rectangular barcode starting with “sp.” These are nicknamed the ‘SP00’ and are encoded with all customer information after the Shipment is packed out.The last step before sortation is to pass through SLAM. SLAM stands for ‘System Label Applied in Manifest.’ The SLAM printer measures the Shipment’s mass (in grams) based on its weight, reads the SP00 to generate the Label, and will also kick out any item that does not conform to weight in the Amazon catalogue. This usually prevents Shipments from being sent which are either missing an item, or might have too many of a certain item (sometimes, Pickers will pick ‘Master Packs’ when the customer only ordered one of the item. The SLAM will call the Operator’s attention to this so that instead of receiving 12 of the item, they should only receive one).Once SLAM is complete, the Shipment is transferred to outbound shipping, where it is put through one of two different sorters (Flats for smaller shipments, or a ‘Singulator’ for larger Shipments). Each sorter has a ‘failsafe’ for Shipments which do not belong there, usually a kickout bin. Shipping associates either palletize the Shipment, then wrap and load it onto a trailer, stick it into a Gaylord, or straight fluid-load the truck. These options are based on whether the destination facility, whether it be a UPS facility, an Amazon Sort Center, the US Post Office or an Amazon Delivery Station (among many others), have an extendable conveyor that can reach all the way into a 53 or 48 foot trailer. If it does, the trailer is usually fluid-loaded (meaning walls are built); if not, they’re palletized or thrown into Gaylords.At CPT (Critical Pull Time), a large wave of Shipments are sent out to multiple locations. There are generally nine or ten CPTs per shift, each with multiple destinations and Shipment methods. Trailers are loaded with the last-arrived Shipments (Shipments which arrive 25 minutes or less to CPT are automatically upgraded to either an Express shipment or the same sort but the following day’s CPT, hence a 25-minute ‘Pad time’ which allows us to conform to our PrSD (Promised Ship by Date) and ExSD (Expected Ship by Date)). Truck drivers are given their Bill of Lading, and are then checked out and directed to the next facility for a more granular level of sortation. Generally, Sort Centers work with DDU (basically the Post Office), Delivery Stations work with Same/Next Orders (but have recently branched into Second day), and there are other options such as Prime Air (for example, in our region of the country, KCVG sends Air freight from Kentucky to places like Oakland, Phoenix, Dallas, etc…locations that ground shipment simply can’t get there in time, while on the West Coast, KSMF might ship to locations like Chicago and Milwaukee). Either way, “Last Mile” sortation does not take place at the FC. Amazon has recently been making strides to handle more of the delivery aspect themselves, recently encouraging aspiring business owners who would like to become Amazon employees to purchase a fleet of trailers, rather than work with contractors or an open bidding system which is in place now through NOC, or a group based out of India which awards the job to the lowest bidder. Too, Amazon has instigated ‘AZNG’ (Amazon ground) trailers with Amazon employees as drivers, and of course, there is the Flex driver program for Delivery Stations (AMZL—or Amazon Logistics stations), Prime Now Hubs and Fresh locations, which is sort of like Uber but for Amazon deliveries. Flex drivers usually have the option to use their own personal vehicle for more pay, or use Amazon’s ‘van’ which can handle more Orders per trip.So this is usually how an Order is handled. There are, of course, a hundred and one different issues that arise during any given day at any given location, and it can take a large degree of creative problem solving to make sure CPTs and ExSD are met on time, IF not sooner.
How can I track my inventory using barcode systems automatically?
(1) Goods warehousingBefore the goods are put into storage, the following preparations should be made:1. Scientifically code the location of the warehouse and mark it with bar code symbols to realize the location management of the warehouse. Scientifically code the location of the warehouse and use the bar code symbol to identify it, and collect the location of the substance when entering the warehouse. , And import the management system at the same time. Warehouse location management is conducive to quickly locating the location of inventory in warehouses or multi-variety warehouses, is conducive to achieving the first-in-first-out management goals and improving the efficiency of warehouse operations, thereby reducing warehouse management costs.2. Scientifically code the goods, and print the barcode labels of the inventory according to different management objectives (for example, whether to track single products or to achieve shelf life/batch management). On the basis of scientific coding, the barcode label of the goods is printed out before storage, and pasted on the packaging of the goods to facilitate automatic data collection in the future.3. When the designated goods are delivered to the warehouse, the warehouse management personnel will accept the goods according to the order, and use the handheld terminal barcode data collector to quickly and accurately complete the receipt data collection. When receiving the goods, the operator uses the handheld terminal to scan or enter the barcode and the actual quantity of the goods according to the content of the receipt. The data is saved to the warehouse management system, and warehouse personnel or management personnel can query the relevant receipt data. Data upload and synchronization Upload the collected data to the material management system, and automatically update the data in the system. At the same time, the updated data in the system can be downloaded to the handheld terminal for inquiries and calls on site. Specific steps:When the materials are in the warehouse, scan the barcodes of different goods and enter the corresponding contents of the barcodes into the system. In this way, by querying the barcode, you will see the storage time, unit price, storage location, supplier and other related information of the material. In the flow links such as the requisition of materials, just scan the barcode and write the required quantity, and other information will be automatically loaded. If the goods in the original package do not have a bar code, prepare the internal bar code and label the internal bar code on the corresponding product packaging without the original bar code.After the goods are put into the warehouse, they are arranged in the corresponding location according to their classification and attributes. After scanning the barcode of the product to be placed with the handheld terminal, scan the barcode of the location on the shelf (or directly enter the location number), and then enter the relevant information. Such as: document number, package number, actual weight, etc. Make the goods of different barcodes correspond to the warehouse location, and improve the efficiency of inventory and picking.After all the goods are placed, the handheld terminal is connected to the computer system, and the arrival and inventory location data of the goods are transmitted to the computer. Complete the final operation.Advantages of using barcode technology for storage:– Paperless receiving operation;-Check the difference between the manifest and the received goods to ensure the correctness of the received goods and data-Convenient to save the corresponding data and upload it back to the PC for update and query-Quick operation, improve work efficiency(2) Delivery of goodsThe warehouse staff picks the goods at the designated goods location according to the requirements of the documents, and sends the goods to the public delivery area, uses the data collection terminal to scan the goods position and the bar code of the goods, and enter the actual quantity of the goods (if When the sent goods are inconsistent with the outbound order number, the terminal will automatically display and alarm to avoid wrong operation)Warehouse personnel or management personnel can query relevant shipping data; specific operation steps;The warehouse management staff generates a delivery list according to the bill of lading, and prints the delivery list;Warehouse management personnel download the outbound order data to the handheld scanning terminal;When shipping, the shipper first scans the outbound order number and its order to be shipped;After ordering the goods correctly, load the goods away and complete the delivery;Through the hand-held terminal verification, the delivery operation of the complement code can be carried out in time;Check the difference between the manifest and the shipped goods to ensure that the received goods and data are correct;Inventory-is the regular or irregular warehouse personnel or management personnel can query related shipping data.For material delivery, add a delivery list on the handheld terminal, and then scan the material barcode to handle the delivery of the material.Substance consumption workshops and teams use handheld terminals to consume the substances to be used.When the material moving keeper moves the equipment to the storage location, first scan the material barcode with the mobile handheld terminal, and scan the original cargo location barcode of the substance and the current cargo location barcode at the same time, and the storage location information of the substance is recorded in the system in.(3) Inventory of goodsInventory-is the inventory of goods in the warehouse regularly or irregularly, compared with the actual inventory and the difference in the data form, to improve the accuracy of inventory data. Its purpose is to:Determine the existing stock. Inventory can determine the actual inventory quantity of existing inventory goods, and adjust the inventory book quantity to the actual inventory quantity through profit and loss adjustment. Due to many records, mistakes, and omissions, the inventory data records are not true. In addition, due to product damage, loss, and incorrect inventory during acceptance and shipment; sometimes the inventory method is improper, resulting in incorrect inventory, double inventory, and missing inventory. For this reason, it is necessary to check the inventory regularly, find out the problems and find out the reasons, and adjust them in time.Confirm the profit and loss of corporate assets. The total amount of inventory goods directly reflects the use of the company’s current assets. If the inventory is too high, the normal operation of the liquidity will be threatened. The inventory amount is directly proportional to the inventory and its unit price. Therefore, in order to accurately calculate the actual profit and loss of the enterprise , Must pass the inventory.Verify the effectiveness of commodity management. Through the inventory, you can find the problems in the operation and management, and solve the problems to improve the operation process and operation methods, and improve the quality of personnel and the management level of the enterprise. The system can generate an inventory plan based on the warehouse area.
- Home >
- Catalog >
- Business >
- Order Template >
- Bill Of Lading Form >
- Uniform Straight Bill Of Lading Original >
- fedex bill of lading instructions >
- Outbound Bill Of Lading Shipping Label