How to Edit Your M10 Notice Of Commencement Online On the Fly
Follow these steps to get your M10 Notice Of Commencement edited with the smooth experience:
- Select the Get Form button on this page.
- You will enter into our PDF editor.
- Edit your file with our easy-to-use features, like signing, highlighting, and other tools in the top toolbar.
- Hit the Download button and download your all-set document for reference in the future.
We Are Proud of Letting You Edit M10 Notice Of Commencement With a Streamlined Workflow
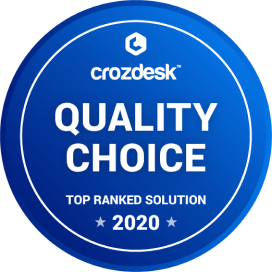
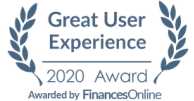
How to Edit Your M10 Notice Of Commencement Online
When you edit your document, you may need to add text, complete the date, and do other editing. CocoDoc makes it very easy to edit your form fast than ever. Let's see how can you do this.
- Select the Get Form button on this page.
- You will enter into this PDF file editor web app.
- Once you enter into our editor, click the tool icon in the top toolbar to edit your form, like signing and erasing.
- To add date, click the Date icon, hold and drag the generated date to the field you need to fill in.
- Change the default date by deleting the default and inserting a desired date in the box.
- Click OK to verify your added date and click the Download button once the form is ready.
How to Edit Text for Your M10 Notice Of Commencement with Adobe DC on Windows
Adobe DC on Windows is a popular tool to edit your file on a PC. This is especially useful when you prefer to do work about file edit without network. So, let'get started.
- Find and open the Adobe DC app on Windows.
- Find and click the Edit PDF tool.
- Click the Select a File button and upload a file for editing.
- Click a text box to give a slight change the text font, size, and other formats.
- Select File > Save or File > Save As to verify your change to M10 Notice Of Commencement.
How to Edit Your M10 Notice Of Commencement With Adobe Dc on Mac
- Find the intended file to be edited and Open it with the Adobe DC for Mac.
- Navigate to and click Edit PDF from the right position.
- Edit your form as needed by selecting the tool from the top toolbar.
- Click the Fill & Sign tool and select the Sign icon in the top toolbar to make you own signature.
- Select File > Save save all editing.
How to Edit your M10 Notice Of Commencement from G Suite with CocoDoc
Like using G Suite for your work to sign a form? You can integrate your PDF editing work in Google Drive with CocoDoc, so you can fill out your PDF with a streamlined procedure.
- Add CocoDoc for Google Drive add-on.
- In the Drive, browse through a form to be filed and right click it and select Open With.
- Select the CocoDoc PDF option, and allow your Google account to integrate into CocoDoc in the popup windows.
- Choose the PDF Editor option to begin your filling process.
- Click the tool in the top toolbar to edit your M10 Notice Of Commencement on the specified place, like signing and adding text.
- Click the Download button in the case you may lost the change.
PDF Editor FAQ
Is there any reference agreement / contract template available (between client & contractor) for villa construction? If so please forward me.
Construction Draft Agreement formARTICLES OF AGREEMENTThis deed of agreement is made in the form of agreement on _____(date) between Mr.____________ or his authorized representative (hereinafter referred to as the first party) and Mr.________________ , S/O _______________ resident of ______________ (hereinafter referred to as the second party), to execute the work of construction of _______________________________ (hereinafter referred to as works) on the following terms and conditions.2. Cost of the ContractThe total cost of the works (hereinafter referred to as the “total cost”) is Rs. ____ Lacks as reflected in Annexure - 1.3.1 Payments under its contract:Payments to the second party for the construction work will be released by the first party in the following manner:-MS NoON COMPLETION OFPAYMENT %VALUE (INR)CUMULATIVEMS-01Land Registration & agreement signature20% (based on land value)MS-02On reaching plinth level05% of the total costMS-03On completion of GF15% of the total costMS-04On reaching roof level15% of the total costMS-05Flooring, bathroom tiling and MEP works10% of the total costMS-06Painting, toilet fixtures & Roof tiling10% of the total costMS-07Well, Boundary wall & External landscape.10% of the total costMS-08Clearing of punch list & Project hand over.15% (adjust based on first MS%)3.2 Payments at each stage will be made by the first party :(a) on the second party submitting an invoice for an equivalent amount ;(b) on certification of the invoice (except for the first installment) by the engineer nominated by the first party with respect to quality of works in the format in Annexure - 2; and(c) upon proper and justified utilization of at least 50 % of the previous installment and 100 % of any prior installment.4. Notice by Contractor to EngineerThe second party, on the works reaching each stage of construction, issue a notice to the first party or the Engineer nominated by the first party (who is responsible for supervising the contractor, administering the contract, certifying the payments due to the contractor, issuing and valuing variations to the contract, awarding extensions of time etc.), to visit the site for certification of stage completion. Within 15 days of the receipt of such notice, the first party or the person nominated by it, will ensure issue of stage completion certificate after due verification.5. Completion timeThe works should be completed in ___ (Normally villa project finish by10-12 months) months from the date of this Agreement. In exceptional circumstances, the time period stated in this clause may be extended in writing by mutual consent of both the parties.6. If any of the compensation events mentioned below would prevent the work being completed by the intended completion date, the first party will decide on the intended completion date being extended by a suitable period:a)The first party does not give access to the site or a part thereof by the agreed period.b)The first party orders a delay or does not issue verified / approved drawings, specifications or instructions for execution of the work on time.c)Ground conditions are substantially more adverse than could reasonably have been assumed before issue of letter of acceptance and from information provided to second party or from visual inspection of the site.d)Payments due to the second party are delayed without reason.e)Certification for stage completion of the work is delayed unreasonably.7. Any willful delay on the part of the second party in completing the construction within the stipulated period will render him liable to pay liquidated damages. @ Rs. 500 per day to a maximum of Rs.150, 000/- which will be deducted from payments due to him. The first party may cancel the contract and take recourse to such other action as deemed appropriate once the total amount of liquidated damages exceeds 2 % of the contract amount.8. Duties and responsibilities of the first party8.1 The first party shall be responsible for frequent visits and guidance to the second party for carrying out the works as per specifications. This will include written guidelines and regular site visit of the authorized personnel of the first party, for checking quality of material and construction to ensure that it is as per the norms.8.2 The first party shall supply 3 sets of drawings, specifications and guidelines to the second party for the proposed works.8.3 Possession of the site will be handed over to the second party within 10 days of signing of the agreement.8.4 The Engineer or client representative as may be authorized by the first party shall hold meeting once in a month where the second party or his representative at site will submit the latest information including progress report and difficulties if any, in the execution of the work. The whole team may jointly inspect the site on a particular day to take stock of activities.8.5 The Engineer shall record his observations/instructions at the time of his site visit in a site register maintained by the second party. The second party will carry out the instructions and promptly rectify any deviations pointed out by the engineer. If the deviations are not rectified, within the time specified in the Engineer’s notice, the first party as well as the engineer nominated by it, may instruct stoppage or suspension of the construction. It shall thereupon be open to the first party or the engineer to have the deviations rectified at the cost of the second party.9. Duties and responsibilities of the second party9.1 The second party shall:a)take up the works and arrange for its completion within the time period stipulated in clause 5;b)employ suitable skilled persons to carry out the works ;c)regularly supervise and monitor the progress of work ;d)abide by the technical suggestions / direction of supervisory personnel including engineers etc. regarding building construction ;e)be responsible for bringing any discrepancy to the notice of the representative of the first party and seek necessary clarification :f)ensure that the work is carried out in accordance with specifications, drawings and within the total of the contract amount without any cost escalation ;g)keep the first party informed about the progress of work on daily basis. Use electronic / social media to transmit daily progress photograph in case client / representative is not available at work place.h)be responsible for all security and watch and ward arrangements at site till handing over of the building to the first party ; andi)maintain necessary insurance against loss of materials/cash, etc. or workman disability compensation claims of the personnel deployed on the works as well as third party claims.f) Pay all duties, taxes and other levies payable by construction agencies as per law under the contract (First party will effect deduction from running bills in respect of such taxes as may be imposed under the law).10. Variations / Extra ItemsThe works shall be carried out by the second party in accordance with the approved drawings and specifications. However, if, on account of site conditions or any other factors, variations are considered necessary, the following procedure shall be followed:-a)The second party shall provide the Engineer with a quotation for carrying out the Variation when requested to do so by the Engineer. The Engineer shall assess the quotation, which shall be given within seven days of the request before the Variation is ordered.b)If the quotation given by the second party is unreasonable, the Engineer may order the Variation and make a change to the Contract Price which shall be based on Engineer’s own forecast of the effects of the Variation on the Contractor’s costs.c)The second party shall not be entitled to additional payment for costs which could have been avoided by giving early warning.11. SecuritiesThe Performance Security shall be provided to the Employer no later than the date specified in the Letter of Acceptance and shall be issued in an amount and form and by a bank or surety acceptable to the Employer. The Performance Security shall be valid until a date 28 days from the date of issue of the Certificate of Completion in the case of a Bank Guarantee.12. Termination12.1 The first party may terminate the Contract if the other party causes a fundamental breach of the Contract.12.2 Fundamental breaches of Contract include, but shall not be limited to the following:(a) the contractor stops work for 28 days and the stoppage has not been authorized by the Engineer;(b) the Contractor has become bankrupt or goes into liquidation other than for a reconstruction or amalgamation;(c) the Engineer gives Notice that failure to correct a particular Defect is a fundamental breach of Contract and the Contractor fails to correct it within a reasonable period of time determined by the Engineer;(d) the Contractor does not maintain a security which is required;12.3 Notwithstanding the above, the Employer may terminate the Contract for convenience.12.4 If the Contract is terminated the Contractor shall stop work immediately, make the Site safe and secure and leave the Site as soon as reasonably possible.13. Payment upon Termination13.1 If the Contract is terminated because of a fundamental breach of Contract by the Contractor, the Engineer shall issue a certificate for the value of the work done less advance payments received up to the date of the issue of the certificate, less other recoveries due in terms of the contract, less taxes due to be deducted at source as per applicable law.13.2 If the Contract is terminated at the Employer’s convenience, the Engineer shall issue a certificate for the value of the work done, the reasonable cost of removal of Equipment, repatriation of the Contractor’s personnel employed solely on the Works, and the Contractor’s costs of protecting and securing the Works and less advance payments received up to the date of the certificate, less other recoveries due in terms of the contract and less taxes due to be deducted at source as per applicable law.14. Dispute settlementIf over the works, any dispute arises between the two parties, relating to any aspects of this Agreement, the parties shall first attempt to settle the dispute through mutual and amicable consultation.In the event of agreement not being reached, the matter will be referred for arbitration by a Sole Arbitrator not below the level of retired Assistant Engineer, PWD to be appointed by the first party. The Arbitration will be conducted in accordance with the Arbitration and Conciliation Act, 1996. The decision of the Arbitrator shall be final and binding on both the parties.Annexure IBILL OF QUANTITIESNoDescription of WorkQty.UnitEstimated Cost (Rs.)RemarksIn figureIn WordsGross Total Cost : Rs. ..........................We agree to execute the works in accordance with the approved drawings and technicalspecifications at ............ percentage above/below the estimated rates, i.e., for a total contract price of Rs. ...........(amount in figures ) (Rs. ........... amount in words).Signature of ContractorAnnexure - 2Milestone Completion CertificateCertified that the works upto -------------------------------------------------- level in respect of construction of ------------------------------------- at ----------------------------------- have been executed in accordance with the approved drawing and technical specifications.SignatureName & Designation (Official address)Place :Date :Office sealAnnexure - 3Standards & Specification4.1 Civil and Structural worksa)The building should be RCC slab with wall support structure. The cladding / sub structure wall should be of laterite masonry stone supported on RCC slabs and RCC plinth beams. The roof of the building should cast with structural reinforced concrete of M30 Grade (1:1:2) ready mix concrete for integrity & strength. Staircases should be of RCC M30 grade concrete.b)All main walls shall be 200 mm solid concrete walls made from first quality laterite stones pointed with 1:5 cement sand mortar with a maximum 10mm thickness. Higher thickness of walls shall be adopted for living room slab supported wall for excess load resulted from wider span.c)All external faces of walls and RC members shall be provided with 20 mm thick cement mortar plastering in CM 1:5. All internal faces of walls shall be provided with 12 mm thick plaster in CM 1:5. RCC ceiling, if any, shall be provided with 6 mm thick plaster in CM 1:4.d)Roof shall be treated with bitumen felt waterproofing as per IS-1346. Underground sump & holding tank shall be of RCC M30 water retaining structure design. Construction joints should be linked with water bars to avoid leakage.e)Considering clay content in the soil, bottom soil shall be removed and replaced with granular imported soil, levelled & compacted with optimum moisture content .100mm thick Lean / plain cement concrete of grade M10 should be used to prevent settlement & uniform load distribution to grade.f)The building shall be designed in accordance with the latest Indian Standard Codes and shall be designed to resist wind and seismic forces.g)Minimum grade of reinforced concrete used shall be M25. Ordinary Portland cement of Grade-43 conforming to IS-8 112 shall be used.h)Reinforcement bars will be high yield strength deformed bars of grade Fe-4 15 conforming to IS-1786. Steel structure shall be designed in accordance with provisions of IS 800 - 1984. Structural steel shall conform to IS-2062. Tubular sections shall conform to IS4923. Gr. Yst-240.i)Contractor to ensure minimum Seven days curing with moistened sack bags at three times a day for all RCC members & plastered surfaces. For roof slab curing, water flooding method to use for efficient curingj)Contractor is advised to carry out its own tests/ investigations related to soil quality/ profile.k)Contractor to apply anti-termite treatment inside grade slab & external periphery 1mtr wide around plinth beam.4.2 Hard landscape & Drainagea)Well shall be located 30mtr away from nearby septic tank to avoid seepage.b)External boundary walls shall be made of grade1 laterite stone on top of RCC plinth /belt beam with section details similar to villa structure.c)A suitable arrangement for carrying the sewage shall be designed using the stoneware pipes and sewage shall be disposed to the nearby municipal sewer line.4.3 Architectural Worksd)The minimum quality of finishes used for various building areas are furnished in this section. However, the Contractor would be free to suggest and select in consultation with Project Engineer alternative material, which can meet similar requirements of durability, texture, abrasion, corrosion and moisture absorption.e)Flooring: The nominal total thickness of floor finish shall be 50 mm including under bed and topping. The flooring shall be laid on already matured concrete base. The under bed for floors shall consist of cement concrete 1:2:4 with stone chips 12.5 mm down graded as coarse aggregates. The under bed shall be provided with appropriate slope towards catch pit for floor drainage.f)Heavy duty ceramic tiles: HD ceramic tiles with matt finish shall be used in toilets, locker rooms etc. The tiles shall be 300x300x7 mm of approved makes.g)Bath tiles- Floor tiles should be non-slippery type laid on water proofed surface.h)Kitchen dado tiles shall be up to 0.8 mtr height from slab level. Kitchen double sink with rotating center tap. Provision for cooking range / gas stove embedded to granite. Gas connection line from work area gas storage area to gas stove.i)Granite Flooring: Minimum 20 mm thick 900x900 machine cut machine polished granite flooring shall be used. The tiles shall be of approved makes and acceptable to client.j)Skirting / Dado : 150 mm skirting matching with floor finish shall be provided in all areas unless specified otherwise elsewhere. Toilets & wash Room shall be provided with dado of full wall height with ceramic tiles of minimum 5 mm thickness as per IS:777.Plasteringa)Sand and cement in the specified proportion shall be mixed dry on a water tight platform / mixer machine and minimum water added to achieve working consistency.b)External face of all walls shall be provided with 18 mm thick cement mortar plastering with an under layer 12 mm thick in CM 1:6 and top second layer (Thickness 6 mm) thick layer in CM 1:4 with approved water proofing compound.c)For internal walls 18 thick plaster in CM 1:6 shall be provided on the uneven side of the wall and 12 mm thick plaster in CM 1:6 on the even side of the wall.d)Inside surfaces of walls shall be provided with 2 mm thick putty punning over the plastered surfaces for uniformity.e)Ceiling of all buildings shall be given 6 mm thick cement sand plaster 1:4Internal plastering on walls shall be done to cover surfaces from skirting level to bottom of roof slab in all areas including areas where false ceiling is proposed.f)All drips, grooves, mouldings, and cornices shall be done with special care to maintain true lines, levels and profiles. After the plastering work is completed, all debris shall be removed and the area left clean.g)Neat cement finish: After achieving a true plastered surface with the help of a wooden straight edge, the entire area shall be uniformly treated with a paste of neat cement at the rate of 1 kg. per Sq.M. and rubbed smooth with a trowel.h)Curing: All plastered surface after laying, shall be watered, for a minimum period of seven days, and shall be protected from excessive heat and sunlight by suitable approved means. Moistening shall commence, as soon as the plaster has hardened sufficiently and not susceptible to damage. Each individual coat of plaster shall be kept damp continuously, for at least two days, and then dried thoroughly, before applying the next coat.Paintinga)Details furnished here in below are the minimum acceptable standard for painting.b)Water proof cement based paint as per IS:5410 shall be provided on external faces of walls, sunshades, etc.c)Inside surfaces shall be provided with Acrylic emulsion paint as per 15:5411 Part-I / oil bound distemper as per IS :428d)All plastered ceilings shall be provided with water bound distempere)All wood work shall be provided with fire resistant transparent paint as per 15:162 over French polish as per 15:348 or flat oil paint as per 15:137.f)Painting for structural steel shall be done as per relevant IS standards.g)Following general instruction for painting shall be followed.ØFor painting on concrete, masonry and plastered surfaces IS:2395 parts I and II shall be followed.ØFor painting on wood work IS:2338 part I & II shall be followed.ØConventional painting methodology should be followed. ie. Moisten wall surface, apply base primer coat, putty filling for undulations, putty 2mm thick overall coating for smooth finish, primer prior to paint and two coats of paint.ØAll painting on masonry or concrete surfaces shall preferably be applied by rollers.ØPaint manufacturer method of application & recommendations shall be followed strictly.Roof coveringa)Roof tiles quality certificate shall be produced prior to purchase and get approved by client. Paint on top of roof tile shall be applied if requested by client.b)For efficient drainage of rain water, roof concrete shall be given a gradient of a minimum of 1 in 100. The gradient shall preferably provide by sloping the structural framing system itself. Gradient may also be provided using screed concrete 1:2:4 using 12.5 mm downgraded aggregate. But the average thickness of such screed concrete may be restricted to about 50 mm. Ic)All roof water proofing shall be provided using high solid content liquid applied elastomeric water proofing membrane with separate wearing course as per ASTM C-898. Thickness of the membrane shall be a minimum of 1.5mm. The treatment includes application of polymerised mortar over sloped roof to achieve a smooth surface and a primer coat. Flat roof shall be provided with chequered cement tiles as per IS: 13801 over water proofing treatment in areas where movement of personnel is expected. Minimum width of pathway i locally shall be 1000 mm.d)Number and size of rain water down comer pipe shall be decided based on the provisions of IS:1742 and IS:2527. The pipes shall be mild steel pipe conforming to class ‘medium’ of IS: 1239 with welded joint. In the case of tall structures, where maintenance is not possible these pipes shall be galvanised. Where access is available for maintenance, these pipes may be painted as specified elsewhere in this document similar to any other steel work. It is recommended that the minimum diameter of the pipe be kept as 150 mm The down comer pipes shall be suitably concealed with masonry work, cement concrete or sheeting to match with the exterior finish.Doors & Windowsa)Unless otherwise specified, all doors, windows and ventilators of air conditioned areas, entrance lobby of all buildings and windows/ventilators provided on the outer face of all buildings shall have, electro-colour coated (anodised) aluminium framework with glazing. All doors of toilet areas shall be of factory made pre-laminated particle board of minimum 35mm thick (MDF exterior grade) conforming to IS 12406.b)Single glazed panels with aluminium frame work shall be provided as partition between two air-conditioned areas wherever clear view is necessary.iv. Doors shall be complete with all hardware and fixtures like door closer, tower bolts, handles, stoppers, aldrops, etc.c)Hollow extruded section of minimum 3mm wall thickness shall be used for all aluminium doors, windows and ventilators.Double glazed wall panel with aluminium frame shall be provided between air- conditioned and non-air-conditioned areas.Glazinga)Double glazing shall consist of two 6 mm thick clear toughened safety glass conforming to IS:2553, hermetically sealed and separated by 12 mm thick gap for thermal insulation.b)For single glazed aluminium partitions and doors, Float glass or flat transparent sheet glass of minimum 5.5 mm thickness shall be used.c)Ground glass / frosted glass of minimum 4 mm thickness shall be used for all windows / ventilators in toilets.d)Unless specified otherwise in this specification minimum thickness of plain sheet glass used for windows/ventilators shall be minimum 5.5 mm.e)Float glass or flat transparent sheet glass on hand rail shall conform to IS:2835. All glazing work shall conform to IS:1083 and IS:3548.f)All glazing clips, bolts, nuts, putty, mastic, cement etc as required shall be supplied and thoroughly cleaned before putting in position, Each glass panel shall be held in place by special glazing clips. After completing of glazing work all dirt stains, excess putty etc. shall be removed and cleaned. All broken, cracked or damaged glass shall be replaced by new glass.g)Neoprene gaskets with snap fit glazing beads shall be fixed as per manufacturer’s instruction to give a leak proof installation.Water Supply And Sanitationh)Roof water tank of adequate capacity depending on the number of users and minimum 8 hours requirement shall be provided. Polyethylene water storage tank conforming to IS:12701 shall be used. The tank shall be complete with all fittings including float valve, stop cock etc.i)Galvanised M.S. pipe of medium class conforming to 15:1239 shall be used for internal piping works for potable water supply.j)Sand C.I.pipes with lead joints conforming to IS:1729 shall be used for sanitary works above ground level.Each toilet block shall have the following minimum facilities. Unless specified all the fittings shall be of chromium plated brass.k)WC (Indian type) Orissa pattern (580x440mm) as per IS:2556 (Part-3) with all fittings including flushing arrangement of appropriate capacity and type- 1 no for Maids bath.l)WC western type 390 mm high as per IS:2556 (part 2) with toilet paper roll holder and all fittings including flushing system of appropriate capacity and type in all other bath rooms.m)Wash basin (oval shape) with all fittings as per IS:2556 to be fixed on concrete platform finished with i2 mm thick polished granite stone in hand wash & all toilets.n)Wall to wall Bathroom mirror (5.5 mm thick float glass) with beveled edges including all fittings.o)Stainless steel towel rail (600 x 20mm) in all bath rooms & wash area.p)Stainless steel liquid soap holder in all bathrooms.Water heater & necessary copper pipe network in all bathrooms.Towel rail & shelfs as per client requirement.Water proof Power socket for electric shaver & hair drier.List of Approved Makes / brands:ØCeramic tiles - Johnson/ KajariaØVitrified tiles - Johnson/ SomanyØLight fixture – Philips /ØSwitches & Socket – Legrande / MK (16Ambs socket - 6 Nos)ØPaints & distempers - Asian/bergcr/ Nerolac . External –Asian paint apexØJoinery – Main Door Teak wood, Toilet- Superior moulded , other Doors seasoned hardwood of good quality.ØDoor fittings - Dorma/ Casma/ DlcoØGlass - Modi/ Glavcrbcl/ Saint GobainØSanitary ware - Hindware/ Cera (Wall mounted WC with concealed cisternØPlumbing fixtures - Jaguar/ Ess Ess / GroheØElectrical wiring / cables – Havells /ABB / SchneiderØFan – Usha / HavellsØCupboard – Wooden MDFØDB ,ELCB,MDB – MBB or equivalentØSand- Good quality river sand collected from non-saline reviser body.4.4 MEP & Miscellaneous requirements (Project Specific requirements)ØDB with breaker system / surge protection systemØEarthing with proper earth rod installedØWeather proof external socketsØIP-55 rated externa lights to protect from rain & ductØProvision for power to following equipmentsØGym equipments – First floor bed to convert to study / gymØProjector in the upstairs living areaØFalse ceiling bulk head lights in all rooms except kitchen & bathØWater heater points in all bath roomsØProvision for mirror lights in dining room wash, all toilet mirrors & Pooja areaØDish TV cable & telephone connection in upper / lower living room & master bed roomØWater tap near car porch , external soft landscape & up stair gardeningØGRP double skinned water tank of 2000Ltr capacity with shade.ØProvision for solar water heater & solar powerØProvision for UPS in a concealed areaØProvision for AC in all bed roomØProvision for water purified in the work areaØProvision for periphery wall /gate security system & CCTV cameraØProvision for sliding gateØProvision for dish wash unit below kitchen cupboard / external washØProvision for washing machine , dryer , ironing table in the upper utility room (wash room)ØShower area – Rain shower , shower mixer & glass partition between dry & wet areaØLiquid / kitchen waste disposal unit to be installed���Z�
- Home >
- Catalog >
- Life >
- Speech Examples >
- Graduation Speech Examples >
- student graduation speech examples >
- M10 Notice Of Commencement