The Guide of modifying Spill Kit Inventory Checklist Online
If you are curious about Customize and create a Spill Kit Inventory Checklist, heare are the steps you need to follow:
- Hit the "Get Form" Button on this page.
- Wait in a petient way for the upload of your Spill Kit Inventory Checklist.
- You can erase, text, sign or highlight of your choice.
- Click "Download" to preserver the changes.
A Revolutionary Tool to Edit and Create Spill Kit Inventory Checklist
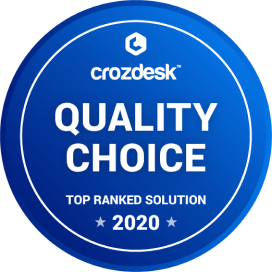
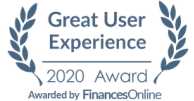
How to Easily Edit Spill Kit Inventory Checklist Online
CocoDoc has made it easier for people to Customize their important documents through the online platform. They can easily Edit as what they want. To know the process of editing PDF document or application across the online platform, you need to follow these simple ways:
- Open the official website of CocoDoc on their device's browser.
- Hit "Edit PDF Online" button and Select the PDF file from the device without even logging in through an account.
- Add text to PDF for free by using this toolbar.
- Once done, they can save the document from the platform.
Once the document is edited using online website, the user can export the form as you need. CocoDoc provides a highly secure network environment for accomplishing the PDF documents.
How to Edit and Download Spill Kit Inventory Checklist on Windows
Windows users are very common throughout the world. They have met lots of applications that have offered them services in modifying PDF documents. However, they have always missed an important feature within these applications. CocoDoc aims at provide Windows users the ultimate experience of editing their documents across their online interface.
The procedure of editing a PDF document with CocoDoc is very simple. You need to follow these steps.
- Choose and Install CocoDoc from your Windows Store.
- Open the software to Select the PDF file from your Windows device and move toward editing the document.
- Customize the PDF file with the appropriate toolkit presented at CocoDoc.
- Over completion, Hit "Download" to conserve the changes.
A Guide of Editing Spill Kit Inventory Checklist on Mac
CocoDoc has brought an impressive solution for people who own a Mac. It has allowed them to have their documents edited quickly. Mac users can fill PDF form with the help of the online platform provided by CocoDoc.
In order to learn the process of editing form with CocoDoc, you should look across the steps presented as follows:
- Install CocoDoc on you Mac firstly.
- Once the tool is opened, the user can upload their PDF file from the Mac in minutes.
- Drag and Drop the file, or choose file by mouse-clicking "Choose File" button and start editing.
- save the file on your device.
Mac users can export their resulting files in various ways. They can download it across devices, add it to cloud storage and even share it with others via email. They are provided with the opportunity of editting file through multiple ways without downloading any tool within their device.
A Guide of Editing Spill Kit Inventory Checklist on G Suite
Google Workplace is a powerful platform that has connected officials of a single workplace in a unique manner. When allowing users to share file across the platform, they are interconnected in covering all major tasks that can be carried out within a physical workplace.
follow the steps to eidt Spill Kit Inventory Checklist on G Suite
- move toward Google Workspace Marketplace and Install CocoDoc add-on.
- Select the file and Click on "Open with" in Google Drive.
- Moving forward to edit the document with the CocoDoc present in the PDF editing window.
- When the file is edited completely, download it through the platform.
PDF Editor FAQ
What is a case study? What are the topics for a case study for a fresher from an engineering background?
Technical AnalysisExample 1: Surface Condensate & Tank FarmDuring the period from February 11, 2019, to March 13, 2019, I worked on Chevron’s 13-27 early production wellbore clean-out projects (13-27-64-16W5, six-well pad). The scope of work was to conduct wellbore clean-out, to collect production data, and to ship out produced fluid. My role as a good tester was to work with my co-workers to man the wellheads, line heater, junk catcher, and choke manifolds, high stage, and low stage test separators, knockout tanks, and flare stacks, to collect data from the equipment, as well as to manage to ship out fluid through the pipeline or to trucks.After the completion of wellbore cleanout for the second well, we encountered an issue with the condensate pressure vessel (the 250psi low stage test separator) transferring capability to the 400 bbl fluid storage tank in the tank farm (total six 400 bbl tanks in the tank farm: two 400 bbls for condensate storage and four 400 bbls for produced water storage).When I attempted to ship down the condensate accumulated from the previous cleanout operations from the condensate pressure vessel to the tank farm, as my job on that day was to operate the condensate vessel and organize the fuel truck traffic to off-load the condensate directly from the vessel or indirectly from the 400 bbl, I found it took a prolonged period (five hours) to transferred 30 m3out of the condensate vessel to the fuel trucks. I reported this issue to my well testing core supervisor.After carefully access and analyze the situation with my core supervisor and coworkers, we concluded that there were 3 possible solutions to better facilitate condensate transferring time:1.To increase the low stage static pressure from 25psi to 50psi to allow for shorter transferring time, as a higher static pressure created a higher force to push and move the fluid.2.To increase the restrictive 1/2” choke adjustable valve installed in the condensate shipping line to 3/4” to allow for a higher flow rate.3.To implement a procedure when enough condensate oil dumped into the condensate vessel, the condensate would be immediately transferred to the 400 bbl once the condensate level reached 15 m3then shipped down to 10 m3(bottom of dirty side sight glass), in order to keep the condensate level as low as possible to allow for enough volume buffer in case of an intensive condensate flow to surface occurred at the time we were not inline to the pipeline. The chevron well-site representative had approved; and he let us try out these options as we completed the flowing of the remaining wells.In the following days when we were completing the remaining cleanout operations, I was also involved with implementing these solutions as we tried to figure out which method would work best. I found that when we used the first two options while loading the fuel truck directly, it created an unsafe condition as the excess amount of force pushing condensate through the shipping line outlet valve (SandMax plug valve) into the pressure hose connected to the fuel truck: the excess force caused the pressure hose to bounce. Also, the increased flow velocity of condensate caused condensate to release vapor rapidly out from the vent of the truck or the vent of the 400 bbl. One time the excess vapor released to the atmosphere triggered the gas monitor located at the tank farm to go off.We further investigated the situation and suggested the Chevron representative to install an ammonia gas scrubber unit to the vent of the 400 bbl, and used the 3/4" chock when we transferred condensate to 400 bbl. When we needed to load the fuel truck, we used the 3/4" chock partially opened to minimize the vibration of the pressure hose.Furthermore, we implemented the third option and created a new procedure to ship down the condensate pressure vessel to the 400 bbl when enough condensate oil dumped to the condensate vessel once the condensate level reached 15 m3and ship down to 10 m3(bottom of the dirty side sight glass).The new configurations and procedures had been proven safe and effective in transferring condensate promptly. The transferring time was dramatically reduced from 5 hours to 3 hours.Example 2: Manifold Cap O-RingDuring the period of October 31, 2018, to November 20, 2018, I worked on Chevron’s 06-25 early production wellbore clean-out projects (11-25-62-24W5, five well pad). The scope of work was to conduct wellbore cleanout, to collect production data, and to ship out produced fluid. My role as a well-tester was to work with my coworkers to man the wellheads, line heater, junk catcher, and choke manifolds, high stage and low stage test separators, knockout tanks, and flare stacks, to collect data from the equipment, as well as to manage to ship out fluid through the pipeline or to trucks.I arrived at the well-site after the completion of the flowing of the second well and started to flow the third well as we were increasing the choke size from 12/64 to 24/64. I was informed by the core supervisor that we had gone through 30 manifold corner cap o-rings after the flowing of the first two wells. And we only had 10 o-rings left until we got new ones in a couple of days. I asked my coworker how frequently they swapped side to check the choke and junk basket and they responded twice per shift or when the o-rings failed to seal and vapor leaked out from the manifold corner cap hole.I checked the field notes and found that the flowing temperature for these wells was relatively high at around 600C, significantly higher than the normal flowing temperature of 500C in other jobs. Additionally, the sand cut remained relatively high at two percent most of the time, most likely due to the new completion design (cluster /stage tools and intervals) causing a potential for additional volumes of sand during flow-back. I also inspected the new o-ring package and found that the buna-cap o-rings were rated for temperature up to 2750F (1350C). Although the current flow temperature was only at 600C, it was significantly higher than the other job. I figured that the relatively high flowing temperature plus the abrasive effect as the result of high sand content caused the excessive wear and tear on the manifold, including those manifold corner cap o-rings.I further inspected the field notes and figured out the o-rings tended to fail to hold pressure at the 4-hour mark. I discussed with my supervisor and got his permission to swap side every 3 hours so that I was able to inspect the choke and the manifold corner, at the same time, switched out and replaced the o-rings with the new ones. The supervisor reminded me that the additional swabbing operation might cause extra wear and tear on the 3” 10K plug valves on the manifold as the grease in the valve body that protect the valve mechanism got flushed away every time the valves functioned open and close. I promised to step up the effort to put extra grease into these plug valves on the manifold after swabbing sides.Furthermore, since our o-ring inventory was low, I tried to prolong the life of the old ones and reuse them if they were still in good shape. After they were removed from the cap, I cleaned the o-rings and lubricated them with lithium grease, then set them aside and let them cool down and shrink back to its original size. After an hour, I carefully inspected the o-rings to see if they were suitable for another run.The new procedures worked extremely well, as we only went thru 9 o-rings for the third wells. It had been dramatically improved from going through 15 of them per well previously. Although I got only one new o-ring left, we received a new package of 100 o-rings on the next day. We were able to complete the rest of the job without any o-ring issue.Technical Implementation & DesignExample 1: Grove Back Pressure Regulating ValveDuring the period from January 11, 2019, to February 13, 2019, I worked on the 11-27 chevron early production well-bore clean-out projects (11-27-61-16W5 six well-Pads) the scope of work was to conduct wellbore cleanout, collect production data and ship out the produced fluid. My role as a well-tester was to take a turn with my coworkers to man the wellheads, line heater, and junk catcher and choke manifolds; high stage and low stage test separators, knockout tanks, and flare stacks, to collect data from the equipment, as well as to manage the tank farm for shipping.One day when I came on shift to perform an equipment walk-around check, I found the tank pressure and fluid lever were high in the low stage separator which was used for condensate storage tanks. The pressure rating of the low stage separator was rated for 250 psi, in this scenario, the pressure should be kept around 30 psi and not over 50 psi for the condensate storage vessel and not over 80 psi for the water storage vessel, and the fluid level should be kept at a minimum in the storage tanks just have enough storage room to keep a volume buffer in case the well produce an extended amount of condensate on the surface in a short period, and we were not inline to pipeline and have to temporary store the condensate in the out-storage tank. To flood the, just enough to push the condensate to the tank truck for shipping or to the tank farm for temporary storage.I noticed the problem was due to the grove back pressure regulating valve. It appeared that someone left the upstream pressure valve open when they increase the grove bag pressure to designated vessel static pressure for shipping condensate but forgot to shut in the upstream pressure regulating valve when the pressure reached 30 psi. If the left open upstream grove valve kept open and the pressure kept rising as the tank kept filling with condensate, it might trigger the high-pressure alarm which led to shutting in the well and stopping the operation.I immediately inform the core supervisor, and with his permission, shut the upstream valve, bleed off the excess tank pressure slowly thru the main knockout tank to the flare stack to 30 psi., bled off the excess grove regulating pressure to 30 psi. Bring the condensate fluid level to the minimum. Have a co-worker to double-check on both the condensate and water storage tanks pressure and fluid level after this is done. I completed a hazard id card on the matter.To rectify this situation, at the end of the job, after discussing the issue with the core supervisor, we decided to install a tee and isolation valve on each grove bag reservoir to supply fuel gas from the Propane tank thru a small scrubber and regulator to independently raise, set and maintain the backpressure in the bag, instead of relying on setting grove back pressure thru tank static pressure thru the upstream valve, to prevent the same problem to occur again.Example 2: Frozen Slight Glass & Isolation ValveDuring the period from October 21, 2018, to December 13, 2018, I worked on the 10-28 chevron hydraulic fracturing completion project (10-28-61-17W7 six well-Pad) the scope of work was to conduct wellhead, fracture support, flow-back screen out operations. My role as a well-tester was to provide wellhead and well spread (Time-Efficiency manifold) support during fracturing and wire-line operation, as well as to operate the junk catcher and choke manifolds, high stage, and low stage test separators, flare stacks, to collect data from the equipment, as well as to manage the tank farm for shipping during the flow-back operation.One day when I came on shift we were informed of the screen-out flow-back operation, and we need flow-back from 60 m3well fluids to the flow-back site. We equalized pressure of 40 MPa with a 15k triplex pump to the manifold to be ready to open the opposite well, and set up to the low stage and be ready for flow back screen out the operation.At the time I was manning the high stage and low stage test separators and recording numbers from the choke manifolds, test separators, and the tank farm. After opening up for flow-back and 30 minutes into the operations, I spotted that mist (water vapor) was coming out of the flare stack. I informed the situation to the core supervisor and the well was then shut-in.During the investigation, I trace the line from the flare-stack to the high stage to the chock manifold and found the high stage isolation valve connected to the choke manifold was left partially open causing the flow-back fluid flood the high stage and got pushed into the gas lines. Additionally, due to the cold weather, the slight glasses of the high stage tank were frozen and the fluid level was wrong.I immediately closed the high stage isolation valve fully; clear the blockage till the fluid level was found, worked with the vacuum truck operator to suck out the gas lines going to the flare stack, as quickly as possible to not hold up the fracture operation any longer.I have learned the lesson that I should have checked the entire valve placement fully including those that are not directly used for the operations. Since that and in the future operations I worked. I always took the time to check all equipment fully to make sure.Technical EvaluationExample 1: UT ReportDuring the period from February 19, 2019, to March 10, 2019, I worked on the 10-28 Chevron early production well-bore clean-out project (10-28-61-17W7 six well-Pad) the scope of work was to rig in a flow-back package to conduct a wellbore cleanout operation. My role as a well-tester supervisor was to assist the core supervisor and coworker to position, install the wellheads, ESD, line heater, junk catcher and choke manifolds, high stage and low stage test separators, knockout tanks, flare stacks, 400bbl tank farm, and associated piping based on the engineering drawings and P&ID, as well as to perform function test, pressure test on the equipment, based on the safe operating procedures.My role as a supervisor trainee was to complete the pre-job & startup check-list and consumable inventory list for early production, including hazard assessment, equipment certification, equipment capability rating, ESD, and high low alarm devices, and miscellanea items.After rigging in the flow line my job was to capture off all certs from the 15K and 2K flow-line piping certs off and hang them into the core supervisor.After we are rigging in, the chevron representative together with our core supervisor went through the flow-line serial numbers we captured of the pipe we have rigged in. they found there are many items were missing certs and UT reports, which we will have to switch out and arranged for a 3rd party UT company to come up to recertify onsite. It happened that the UT Company was near and they would be able to arrive on-site in 2 hours. My core supervisor informed us we should remove all the piping, pulps, and elbow swings uncertified off all the flow-line, had they laid out on pallet so that when the UT Company arrives, they would be able to shoot the item, go through the UT inspection promptly.I took the initiative, worked together with my coworkers to start taking down the uncertified item off the flow-line and onto the pallet, just in time for the UT operator arrived 2 hours later. As they completed UT inspection, we put them back on the flow-line immediately. I also took the time to double-check the rest of the flow-line to ensure all uncertified items had been taken down for inspection before the UT Company left the site.Although we worked extra 2 hours on that day the chevron representative was happy all the certification for the flow-line were in order, and we didn’t hold up for the well-bore cleanout operation scheduled to begin the next day.Example 2: Triplex PumpDuring the period from October 21, 2018, to December 13, 2018, I worked on the 10-28 Chevron hydraulic fracturing completions project (10-28-61-17W7 six well-Pad) the scope of work was to conduct wellhead, fracture support, flow-back screen out operations. My role as a well-tester was to provide wellhead and well spread (Time-Efficiency manifold) support during fracturing and wire-line operation, as well as to operate the junk catcher and choke manifolds, high stage, and low stage test separators, flare stacks, to collect data from the equipment, as well as to manage the tank farm for shipping during the flow-back operation.When I camp on site I noticed we test running a new piece of equipment, a 15K triplex pump. We were using the triplex to monitor fracture backpressure, provide equalization pressure to open the opposite valve and to perform pressure tests for the flow-back site. Since it is a new piece of equipment and everyone is still learning to use it efficiently. After my first day, I learned the basic operation of the pump, start-up, running, shut down, and basic maintenance from my cross shift. I take the extra step to obtain the operational and maintenance manual, as well as the high-pressure fitting manual from my core supervisor. I read both the document after I got back to the camp before begs. The next day I was able to run the triplex efficiently and safely and perform 2 equalization tasks and 1 pressure test, as well as back pressure monitoring efficiently and safely. Also, I caught the there was some minor issue with the steam of a high-pressure needle valve I was able to quickly isolate the needle valve, bled off, and replace it promptly.Project ManagementExample: Job PreparationDuring the period of February 19, 2019, to March 10, 2019, I was sent to the TechnipFMC’s fort St. John shop with a coworker to prepare for a new job for the Crew Energy early production well-bore clean-out project (10-28-61-17W7 six well-Pad) the scope of work was to prepare for the job, pick all required items ready from the shop, check on all equipment and ESD certification. Complete all documentation including pre-job startup checklist. My role as a well-tester supervisor was to assist supervisors from red deer to get this done in five days. The challenge of this project was that TechnipFMC had decided to close the Fort St John Shop and lay off most of the workers except the secretary. I and my coworker are from red deer and unfamiliar with the fort St. John shop and equipment, as well as the client Crew Energy requirements, and we had to complete the preparation promptly (normally it took 10 days to prepare for a new job).I took the initiative to work with my coworker to start going through the checklist and check equipment. I found most of the ESD of the test separator (tank ESD and scrubber ESD) certifications are about to expire, and we worked with the shop secretary to order a replacement from town, sent to old one out for replacement. We installed the new ESD in the next days. We also found the upper portion of the scrubber pot in the operator compartment of the test separator had sheared off where the upper scrubber attaches to the bottom scrubber 1” valve, likely due to rough roads during transport on the field road. We will need to order the new upper portion parts from town Because it is getting closed to the Christmas holidays most part shops in town had closed and the security was not able to place the order and getting the part on time. I decided to salvage the parts from other test separator and used it on this one for now. We also found that the scrubber has no went line coming out from the scrubber ESD to the outside atmosphere, so if it trips over-pressure, it will release pressure in the operator compartment, which will create an unsafe situation. I decided to bellow parts from the equipment. Get the tank back in service.We planned to work on this task first thing in the morning and done by the afternoon, then function tests the 3 flare stack in the yard that would be the last tasks for this project. Unfortunately, the weather forecast indicated there will be a heavy snowstorm coming into the city around noon time. I discussed with my coworker and changed our plan to first test the flare-stack in the morning, and when the snowstorm arrived we will finish the scrubber installation inside the test separator and minimize the risk of working outside in the snow. We finished function testing the 3 flare-stack only half an hour when the snow started to fall. We finished installing the scrubber upper portion and the vent line coming out of the compartment wall through a new drilled hole. After some struggling with a few small items, we have completed the task list at the end of that day.We received positive feedback from the fort St. John manager and secretary as we have completed the job preparation on time and everything was good to go.Professional AccountabilityExample 1: Review Data & Technical DocumentDuring my job in technipFMC and in Voltage Wire-line, every time I encounter a new process or equipment I always request the manual or safe operation procedure to read and learn about running the equipment safely and efficiently. For example, when I was with TechnipFMC, I actively participate in the year-end assessment and prepare to challenge the assessment by gathering well-tester manual, process, and equipment material. When I was with Voltage Wire-line, even only with them for 2 months, I have read the entire wire-line operator manual; obtained wire-line operation files from the manager, additionally.I am also trying to complete my petroleum engineering technology program and I am keen to learn, adaptable, organized, have good time management skills and the ability to multitask effectively, I am currently working full time as a Shift Power Engineer and Valve Technician at Caltrax (Calgary), meanwhile, pursuing my BAPT Bachelor of Applied Petroleum Technology Degree from SAIT thru distance /online learning. I am in the 2nd year of the program and have 90% of the program course load completed, and am expected to graduate in December 2020. Additionally, I am in the process of applying for the C.Tech / C.E.T designation as a Certified Petroleum Engineering Technologist from ASET (Association Of Science and Engineering Technology Professionals Of Alberta, Application ID #126384), expected to obtain the designation by the end of 2020. I am strongly committed to continuous self-improvement and self-development through my work and education.Example 2: Diesel RefuelFor example: when I was a junior well-tester in a fracture assist operation in a shell site. One time in the winter I was refueling a diesel generator; I got distracted from another task because of the cold temperature the nozzle level doesn’t work properly and the generator fuel tank was overfilled. About 3 liters of diesel leaked out drip to the ground, I immediately shut the level, reported to my immediate supervisor, obtained the spill kit to clean up the spill to the degree that meets the environmental regulation, deposal the waste, and submitted a report to my immediate supervisor (less than 5 liters thus didn’t report to the environmental regulator). After this incident, I always make sure to pay extra attention when refueling and never leave my hands from level until refueling is done.I always use proper spill kits to clean up any fluid and oil spill on the ground to minimize environmental damage; for example, in well-testing, use a proper container to collect fluid when draining separator, manifold, remove soil contaminated by the fluid spill to the ground. During wire-line, use wire-line guns and spill kit to contain oil and fluid drip off from the wire-line gun.Technical CommunicationDuring the period from October 21, 2018, to December 13, 2018, I worked on the 10-28 Chevron hydraulic fracturing completions project (10-28-61-17W7 six well-Pad) the scope of work was to conduct wellhead, fracture support, flow-back screen out operations. My role as a well-tester was to provide wellhead and well spread (Time-Efficiency manifold) support during the fracturing and wire-line operation, as well as to operate the junk catcher and choke manifolds, high stage, and low stage test separators, flare stacks, to collect data from the equipment, as well as to manage the tank farm for shipping during the flow-back operation.I was on night shift provide fracture monitor duty at the test separator, when I paid close attention to the fracture radio about the fracture situation as we approached the end of the fracturing of the 30 stages of the alpha well at 6:30 am, and before dayshift arrived, we were informed of fracture sand off and screen out operation will be conducted thru the communication radio from our core supervisor.After a brief discussion with the Chevron representative, the core supervisor got to the flow-back site and he let us know there were 80 MPa left on the well-bore and the fracture had been isolated and bled off. I listened carefully as the core supervisor went on the say that the fracture-crew should have bled off till below 69 MPa as they normally did. I watched the supervisor’s body language as he pointed to the alpha well and then to the bravo well and said the Chevron representative decided to have some of our crew to open all pod valves on the Time-Efficiency Manifold and equalized to 40 MPa with our 15K triplex pump to open opposite well so we can bleed the 80 MPa from alpha well into bravo well to bled off. The core supervisor asked me to set up the flow-back operation, check all the valve orientation and placement for the junk catcher and choke manifold to the high and low stage test separators, as well as the flow-line from the low stage separator to the tank farm, passed this information to the day crew after they came out of the safety meeting and arrived to the flow-back site, and asked the day crew to help set up the flow-back operation, as he will send another coworker to start up the 15K triplex pump to get ready for the equalization operation, and took the rest of the coworkers to open the TE manifold. I confirmed the procedure with him by repeating the information he just mentioned, at the same time pointed at the well-heads and equipment, asked for his confirmation as if I understand what he meant. He nodded his head to confirm that my understanding is correct.When the day crew arrived on the flow-back site, we gather a circle and I passed the information to everyone, in the same manner, my core supervisor told me to, at the same time pointed to all the equipment as I talked. In the end, I confirmed with everyone to see if they understand what I meant and everyone nodded their head. And then I asked them to help me prepare the flow-back operation as usual.The flow-back operation went smoothly as the instructions from the Chevron representative passed down accurately and efficiently as our entire crew member understands the situation very well.
- Home >
- Catalog >
- Life >
- Time Chart >
- Time Zone Chart >
- Us Standard Time Zones >
- Spill Kit Inventory Checklist