How to Edit The Inspection Report Form (Field Use easily Online
Start on editing, signing and sharing your Inspection Report Form (Field Use online refering to these easy steps:
- click the Get Form or Get Form Now button on the current page to access the PDF editor.
- hold on a second before the Inspection Report Form (Field Use is loaded
- Use the tools in the top toolbar to edit the file, and the change will be saved automatically
- Download your modified file.
A top-rated Tool to Edit and Sign the Inspection Report Form (Field Use
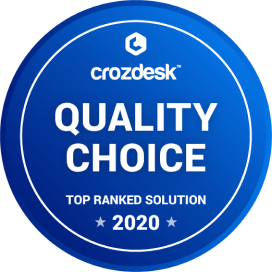
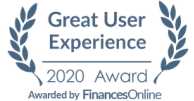
A clear direction on editing Inspection Report Form (Field Use Online
It has become quite easy these days to edit your PDF files online, and CocoDoc is the best PDF text editor you have ever used to make changes to your file and save it. Follow our simple tutorial to start!
- Click the Get Form or Get Form Now button on the current page to start modifying your PDF
- Add, modify or erase your content using the editing tools on the tool pane above.
- Affter editing your content, add the date and make a signature to bring it to a perfect comletion.
- Go over it agian your form before you save and download it
How to add a signature on your Inspection Report Form (Field Use
Though most people are in the habit of signing paper documents with a pen, electronic signatures are becoming more general, follow these steps to finish the PDF sign!
- Click the Get Form or Get Form Now button to begin editing on Inspection Report Form (Field Use in CocoDoc PDF editor.
- Click on the Sign icon in the tools pane on the top
- A box will pop up, click Add new signature button and you'll have three choices—Type, Draw, and Upload. Once you're done, click the Save button.
- Move and settle the signature inside your PDF file
How to add a textbox on your Inspection Report Form (Field Use
If you have the need to add a text box on your PDF for customizing your special content, do some easy steps to get it done.
- Open the PDF file in CocoDoc PDF editor.
- Click Text Box on the top toolbar and move your mouse to carry it wherever you want to put it.
- Fill in the content you need to insert. After you’ve writed down the text, you can utilize the text editing tools to resize, color or bold the text.
- When you're done, click OK to save it. If you’re not settle for the text, click on the trash can icon to delete it and do over again.
An easy guide to Edit Your Inspection Report Form (Field Use on G Suite
If you are seeking a solution for PDF editing on G suite, CocoDoc PDF editor is a commendable tool that can be used directly from Google Drive to create or edit files.
- Find CocoDoc PDF editor and establish the add-on for google drive.
- Right-click on a chosen file in your Google Drive and click Open With.
- Select CocoDoc PDF on the popup list to open your file with and allow access to your google account for CocoDoc.
- Make changes to PDF files, adding text, images, editing existing text, mark with highlight, polish the text up in CocoDoc PDF editor before pushing the Download button.
PDF Editor FAQ
What are the best practices for construction safety inspections?
Construction safety inspections are the most effective means of catching and countering bad habits and hazards.(Next to inspections, the two most important components of a good safety program are planning and training.)Here is a detailed guide on construction safety inspections.Overall, construction companies—large and small—are reporting positive financial impacts from safety programs. And the size of those benefits increases as the depth of the program increases. In an industry that operates on low margins, this is a powerful finding.Let’s take a look at the benefits of safety1) Worker safety and retentionFirst of all, you want your workers to be safe. You want them going home in the same condition they came to work in.Companies that fail to provide safe work environments are unable to retain their workforce, at least in the long term.On the contrary, when companies comply with regulations, provide all necessary PPE, eliminate jobsite hazards and risks, and listen to their workers when concerns are raised, they enjoy the benefits of safe worksites—which translates into both a high retention rate of current workers and an increased flow of new ones.In times of construction worker shortage, this alone can give you a big competitive advantage. But there’s more.2) ReputationA well-performing safety program will give you a big advantage in the marketplace. Developers are becoming more interested in safety programs as well. They recognize that a safety-conscious general contractor reduces their potential liability for lawsuits and bad publicity. A safety program is a legitimate marketing advantage that allows you to separate your firm from your competition.3) OperationsA safety program is a benefit from an operational standpoint as well, as it will prevent you from suffering incidents and project disruptions that create delays and waste time. Obviously, this leads to improved performance and more on-time project deliveries.Also, workers will come to your job sites trusting that they operate within a safe work environment, which improves both morale and productivity.Let’s also not forget that injuries lead to higher insurance premiums and potential fines.4) RegulationsIf OSHA or another outside person/agency inspects the work site, you will have clear documentation about the inspections that have been performed. For example, if a crane on your jobsite malfunctions but you have documentation showing it was recently inspected, you can demonstrate you followed proper safety procedures.=> Let’s sum up the benefits of construction safety once more:Your workers will be safeIt will be easier for you to find and retain workersIt will give you a reputation advantage and help you win dealsIt will reduce delays (due to incidents) and insurance premiums while increasing worker morale and productivityIt will help you comply with regulations (and avoid fines)Applying the best practices listed in this article will increase the success of your safety program and your safety inspections. So keep on reading.In this guide you’ll learn the following:What are construction safety inspections?Construction safety inspections: How often and by whom?Best practices for safety inspection site visitsSafety inspections and checklistsWhat goes into a safety inspection report?Best practices for safety inspection reportsHow to draft safety inspection reports without spending an hour at the end of the dayHow to select the right safety inspection appBest practices for getting the most out of your safety inspectionsConstruction safety inspections: How often and by whom?How often should you we do safety inspections?As in all things, it depends—but here’s a useful guideline:Informal inspections should be done by all supervisors whenever they are out on site. Such inspections identify hazardous conditions and either correct them immediately or report them for corrective action. The frequency of these inspections varies with the frequency and conditions of equipment use.Formal documented inspections are ideally done weekly by supervisors and monthly by health and safety representatives.It’s also a good idea to get project managers or even company leadership involved with inspections to emphasize their importance.Best practices for safety inspection site visitsHere are a couple of useful tips for executing safety inspection site visits:Draw attention to the presence of any immediate danger. Other items can await the final report.Shut down any hazardous items that cannot be brought to a safe operating standard until repaired.Do not operate equipment. Ask the operator for a demonstration. If the operator of any piece of equipment does not know what dangers may be present, this is cause for concern. Never ignore any item because you do not have knowledge to make an accurate judgment of safety.Look up, down, around and inside. Be methodical and thorough. Do not spoil the inspection with a “once-over-lightly” approach.Make “on-the-spot” recordings of all findings before they are forgotten.Ask questions, but do not unnecessarily disrupt work activities.Consider operational factors, such as how the work is organized or the pace of the work, and how these factors impact safety.Discuss as a group whether any problem, hazard or accident might generate from a given work situation. Determine what corrections or controls are appropriate.Take a lot of photos.Safety inspections and checklistsThe goal of safety inspections is to identify hazards—and the best way to do that is with a checklist. With everything written down, it’s easy to make sure you’ve covered all your bases, reducing the chance of missing a potential hazard.For his must-read book The Checklist Manifesto, Atul Awnada interviewed experts from many disciplines (pilots, doctors, contractors).His conclusion? People need checklists to execute projects efficiently. Checklists reduce the risk of mistakes and increase the likelihood everything will get done as specified.When it comes to safety inspections, a checklist is a powerful way to ensure you don’t overlook important details. They free up your mental RAM.The checklist should be comprehensive, covering the following topics at a minimum:Personal Protective Equipment (PPE): Has the correct gear been distributed to all workers? Is each piece of equipment in good repair?Tools and equipment: Are they in proper working order? Are people using the right tool for the job?Fall protection methods: Is fall protection in use? Is it properly set up?Protective devices and signs: Are welders surrounded by a curtain to protect others? Are signs easy to read and warnings clear?Electrical concerns: Are electrical cords safe, and kept off the floor? Is there proper lighting? Is temporary electricity safely installed?Scaffolding: Are all connections secure? Is scaffolding tied to the structure? Are all connections secure?Now, let’s move on to the safety inspection reports that result from the inspections.What goes into a safety inspection report?Obviously, not all safety inspection reports will look the same. Depending on your business and the type of projects you perform, you’ll need to include different items.Here are the most common elements of a safety inspection report:Project information: add the project name, project number, address, name of the person who created the report, etc.Report date: If you want to record what happened or what didn’t happen on particular day or week, you need to put the date on your report.Safety hazards and incidents:Copy all unfinished items from the previous report on the new report.Document all safety risks and observations with enough photos to illustrate the issue. Add recommended methods of control.in - This website is for sale! - Control Resources and Information. the case of accidents or incidents, record who they impacted, who was involved, when and where they occurred, the impact on work, and any photos of the event.Number each item consecutively.Classify hazards. A hazard rating establishes priorities for corrective action and also highlights the level of severity or seriousness of the hazards.Add a due date to the items.Assign the items so responsibilities are clear. This will facilitate accountability and prevent problems from slipping through the cracks. It’s not enough for workers to note they found problems; those problems also need to be resolved quickly.Make sure the location of the item is clear, e.g. by adding annotations to a floor planSignatures: Optionally, you can ask people present to sign off the report.Best practices for safety inspection reportsYour inspections and reports are the basis for corrective actions and follow-up, which will prevent incidents from happening in the first place. So it’s worthwhile to make your safety reports are effective by following these best practices:Provide sufficient detail: State exactly what has been detected and accurately identify its location, together with pictures.Document items and file reports as early as possible: Memories can fade quickly. The shorter the time frame between events and notation, the more accurate the reports will be. Using an app, you can document observations immediately. Copies of inspection reports should also be sent to managementReadability: Keep it simple, use common language, and include enough pictures. Don’t use specialist terms, but don’t be too prosaic, either. Just stick to a concise and clear description of the facts so anyone can read and understand the reports. Also remember that often people don’t read long texts, but they will look at pictures. As the old adage goes, a picture says more than a 1000 words, so make sure to include enough pictures.Layout and branding: Clean, structured, professional reports that include the company’s logo, header, footer, and other branding will radiate a professional attitude regarding safety towards all parties involved (client, workers, subcontractors, etc). If you demonstrate that you are being serious about safety, others will be more inclined to be serious as well.Include positive elements, too: When certain safety risks are managed well, or when a hazard that had been registered during a previous inspection has been addressed, don’t forget to compliment the workers on site and to mention this on your inspection report as well. People will be more receptive to your advice — and like you better, too. Safety officers that only include problems and non-conformities in the report rarely achieve good results. Including compliments and positive items are great for worker motivation. With positive reinforcement, you add a reward for workers exhibiting desired behavior. Rewarding good conduct, rather than punishing negative actions, is a proven method to help promote positive behavior in both children and adults. By doing so you reinforce the desired action, which has a much stronger effect than punishment.Here is a preview of a safety report generated with ArchiSnapper:How to draft safety inspection reports without spending an hour at the end of the dayIf you’re still reading, you probably have no doubt that safety management and safety inspections are fundamental. Nevertheless, there has to be a better way to draft your safety report than having to spend at least an hour to manually put it together: writing out the text, inserting photos, managing the layout of the report, etc.It’s no secret that construction safety reports are a big struggle for safety officers and supervisors.With today’s technology, safety inspection reports do not require that much effort. With tools like ArchiSnapper, you can easily fill in a checklist, take photos and write text (or use voice to text), and the inspection reports will immediately be made available for everyone. Your logo, header, footer and other branding and layout settings will be applied automatically.With such an app you can use your tablet or phone on site. Just open the app, tap “new report,” and provide the required data:Fill in the project statusReview a checklistWrite texts or use the voice-to-text functionalityTake photos and annotate themHave the report signed off (if needed)Find the report archived to your cloud automatically, together with the signed versions and distribution historyThis way, you won’t have to spend an hour or so typing out scribbled notes, transferring pictures from your phone to your PC and then importing them into the report, or struggling with the layout in Word.Curious to see how this works with ArchiSnapper? Check out this video.How to select the right safety inspection appWhen you’re selecting a safety inspection app, make sure to take into account the following:SimplicityLess is more. At first, it might be tempting to choose an app with a lot of features, fields, forms, and configurations.But keep in mind that 90% of the time, you’ll only need 10% of your app’s core functionalities. What you need is a quick and easy way to review your safety checklist from your phone or tablet, with the ability to include photos and notes.Fewer buttons and functionalities means less risk for bugs, issues, and misunderstandings—and more adoption by your team, more standardization, and less frustration.Offline functionalitySooner or later, you’ll be without a reliable internet connection. (Think: broken wifi, no 4G network, unpaid telecommunications invoices…)So make sure your app works offline—and that you can at least capture notes and photos without a connection.Cloud storageYou don’t want to lose all your daily reports if your phone gets stolen or breaks. So your software should have a web backend where your data is synced, and which allows multiple colleagues to access all the inspection reports for viewing, editing, or distribution.CompatibilityThough it probably goes without saying, your app should work on both your mobile device and computer.I hear from a lot of safety professionals who prefer to use their phone on-site (to take photos and add quick notes) and then finish the report online from their desktop.Just a suggestion: I’d avoid buying a Windows device, since the software giant is no longer developing new features or hardware for Windows 10 mobile.Ample featuresThough your app should be simple, it should also include these essential capabilities and functions:Checklist functionalityThe ability to capture notes by typing on your phone/tablet/desktop OR using voice-to-textThe ability to capture photos with annotationsThe ability to draw and sketch on photosThe ability to generate safety reports in PDF format with brandingSignature capture functionalityThe ability to email the PDF construction reports to all parties involvedAutomatic data archiving and backupsThe ability to export/import data from other systemsAuto-numbering of items and reportsBest practices for getting the most out of your safety inspectionsDoing safety inspection visits and generating safety reports takes a lot of time and energy. So don’t forget to apply the following practices in order to get the best results from this process.Planning aheadPrior to doing inspections you need to make sure to have a checklist, an inspection schedule, that inspection members are trained, etc.You also must develop a plan for using your data, not just collecting it. How will the findings be communicated and shared? Will they be corrected in a timely manner and tracked to completion? As trends develop, how will action plans be developed and implemented to prevent reoccurrence?For most construction companies, each jobsite has its own unique risks. Devote time before construction starts to identify those risks and establish a plan to address them. Communicate this safety analysis regularly to workers so they know what hazards to expect and how to work around them.Follow upObservations are the beginning, not the end, of the inspection process.Any health and safety deficiencies identified during the inspection should be noted and corrective action should be taken. Follow up to see that the corrective action has been taken and that the hazard has been effectively dealt with. That’s why it makes sense to always start from your previous inspection report and keep unfinished items in the report—and mark solved items as “OK.” (Positive reinforcement, remember!)Where inspections are being done by the company’s health and safety coordinator or the site health and safety representative, the site supervisor should accompany them so that any corrective action needed can be implemented as soon as possible.AnalyzeMost companies stop once the inspection is completed and the initial hazards are discovered, shared, and fixed (i.e., once the moles are whacked). This is a major error that will prevent meaningful improvements in the safety process.If you are not conducting trend analysis on the observations you collect, these incidents could be happening quite often. Ideally, you should be looking at trends and leading metrics on a number of fronts, for instance:What are the top hazards identified by hazard category?Who are the most at-risk contractors?What are the most at-risk projects?What recurring trends are developing?By tracking and trending this information, you can turn collected data into actionable information.Don’t shoot the messengerIt is essential that the observation reporting, especially significant hazards, be non-punitive and protected. In other words, don’t shoot the messenger! This often occurs from a misperception that finding unsafe observations is a reflection of how well one does the job, which will then reflect poorly on the observer or project team. It also can occur if a senior manager reacts poorly to the discoveries, such as reprimanding the observer or failing to act on the data collected.Management involvementKey to the success of any safety program is strong commitment, support, and backing from management. Frontline supervisors and safety officers do the majority of planned general inspections, but middle and upper management must also conduct safety tours.Whatever the project manager and leadership focuses on will be viewed by the team as important. The old saying, “Actions speak louder than words,” is true. Project managers who place a premium on integrating safety into their projects will ensure better overall project performance. They set the tone, agree to and enforce standards, and establish the concept that focusing on safety is the only way to do business.Furthermore, workers and their representatives should also be involved in all aspects of your safety program—including setting goals, identifying and reporting hazards, investigating incidents, and tracking progress.Workers should be encouraged and have the means to communicate openly with management, to report safety and health concerns without fear of retaliation.
Why are all the opposition leaders, who were demanding CAG report (filed in the Lok Sabha today) on the Rafale deal all these days, now not interested in it?
The waiting is over.The opposition leaders expected that they can find even a small loophole in the deal which they can magnify and convince the public. But they have been disappointed with the out come of the report.All these years all opposition parties are yelling that NDA government spent more money on the deal, but CAG report made it clear that it is cheaper than the UPA government price.Also so many allegations made by those opposition parties became null and void.The salient features of the CAG report filed is enclosed here with.{New Delhi: The CAG (Comptroller and Auditor General) report on the Rafale deal which was submitted to the Rajya Sabha on Wednesday has predictably set into motion another round of political bickering between the ruling NDA and the Opposition Congress, which has been alleging that the deal is mired in corruption.However, the 141-page CAG report of which 32 pages are dedicated to the Rafale deal, makes some important points about the deal clinched by the Narendra Modi government and the one which was being negotiated by the Congress-led UPA government, suggesting that many of the NDA government’s claims about the deal have been vindicated.Let’s look at some of the key takeaways of the CAGNDA’s Rafale deal is cheaper than UPA’sThis is the single biggest takeaway: The CAG report agrees with the Modi government's assessment that the NDA Rafale deal was cheaper than the one that was being negotiated by the UPA.The report states: “Overall, it may seen that as against the Aligned Price as estimated by the Audit of “CV” million € the contract was concluded for “U” million € i.e. 2.86 per cent lower than the Audit Aligned Price.”However, it’s not 9% cheaper as claimed by the Centre, but 2.6% cheaper, according to the report. Nevertheless, CAG’s assertion will be seen as vindication by the NDA, which has consistently claimed that the deal’s pricing made perfect sense. It also appears to blow a hole in the Congress’s allegation that the deal struck by the NDA was a loss-making one for India.NDA’s deal made significant savings in India Specific EnhancementsAs per the CAG report, compared to the 126-plane deal negotiated by the UPA, India was able to save 17.08 per cent money for what are known as the India Specific Enhancements in NDA’s Rafale contract. New Delhi had asked for 13 specific changes to be made to the Rafale jet for making it better suited to India’s defence parameters. However, these upgrades are cheaper now. As the report says: “As against this the contract was signed for “AX3” M€, a saving of 17.08 per cent.”Quicker delivery, same fly-away priceAnother CAG finding which NDA ministers are likely to quote is that the delivery schedule of the Rafale jets has been enhanced by 5 months. Also, the CAG report indicates that the flyaway price of the fighter jet is same as was agreed by the UPA government in 2007.Letter of Comfort instead of sovereign guaranteeThough the union law ministry had asked for a sovereign guarantee, the French government only provided a ‘Letter of Comfort’, the CAG report says. Also, France did not agree to the opening of an Escrow account as a safeguard measure.In the 2007 offer, Dassault Aviation had provided financial and performance guarantees amounting to 25% of the total contract value. However, since there was no such warranty or guarantee in 2016 contract, it led to savings for Dassault, the report says. }(1)So, now name calling of CAG will begin, in fact it has begun even before the report is submitted, terming it as “chowkidaar Audit report”If CAG works according to the Government Orders, see this report of CAG on August13, 2013 when UPA Government is in rule.{NEW DELHI: A report by the government auditor, CAG, has found major irregularities in a Rs. 3,600-crore VVIP helicopter deal with Italian manufacturer AgustaWestland (AW). In its report tabled in Parliament today, the Comptroller and Auditor General or CAG said that the government had failed to follow defense procurement policy rules in awarding the contract for 12 VIP choppers.Here are some of the findings of the report:The fact remains that despite the directions of the Prime Minister's Office (PMO) to make SQR (staff qualitative requirements) broad-based to increase competition, the SQR were made more restrictive which narrowed down the choice to a limited range of helicopters, capable of meeting the requirements of VVIP fleet."We have observed that the past trend of low utilization levels (29 per cent) over a period of 11 years (1999-2010) of the existing fleet of eight helicopters by VVIP and rest of the flying for training ad use by OEPs does not lend credence to the ministry's justification for additional procurement of helicopters. This apprehension was also expressed by RM."Revision of SQR... the acquisition process again led to a resultant single vendor situation in 2010 and AW 101 was selected.Field trials are held with representative helicopters of AW 101 and actual helicopters AW -101.The contracted helicopter was still in its developmental phase, as stated by the vendor. The recommendation and assurance given by the Indian Air Force (IAF) Chief (October 2007) to conduct evaluation trials abroad lacked justification.Audit is unable to agree with the Ministry's assertion as the Field Evaluation Team (FET), in its inspection report, had clearly mentioned (January 2008) that AW-101 as offered to the IAF was in a product developmental phase. Therefore, the FET was carried out on a Merlin MK- 3A (primarily for evaluation of avionics, navigation systems and maintenance).The benchmark cost adopted by Cost Negotiation Committee was unreasonably high compared to the offered cost. Hence, it provided no realistic basis for obtaining an assurance about a reasonable cost procurement of AW -101. There were also violations in Defense Procurement Policy (DPP) in respect of fulfillment of offset obligations.}(2)So it is clear that the CAG reports the facts irrespective of the government in power.Of course, the opposition, particularly Congress will argue that they have that freedom to CAG where as now it was not give. Of course no body believes them.Now the next step Rahul Gandhi would talk about JPC. Even if it formed and opinioned that there is no irregularities in the deal, he will start name callling process of the parliamentarians who supported the deal.The game of blaming goes on.We can wake up a person who is sleeping, but we can not wake up a person who is pretending as sleeping.GOD SAVE INDIA FROM THESE SELFISH PEOPLEBHARAT MATA KI JAI1.CAG report on Rafale deal decoded2.VVIP chopper scam: Key findings of CAG repor
Which is the best commercial gym equipment manufacturers in china?
HI, we are Ntaifitness.We are a manufacturer of gym equipment located in DeZhou city, ShanDong Province. NtaiFitness supplies Commercial Strength Fitness Equipment and commercial cardio fitness equipment for Gyms.Why choose Ntai fitness equipment manufacturersA: After the order is confirmed, we have a meeting with all departments before production, to discuss all the fitness equipment production technology and technical details to ensure that all the details are under control.Check all the materials to ensure that they will match the customer’s requirements before production.Check the semi-finished products.Strict online quality control.products quality control.Final check while packing up all the fitness equipment. If there is no problem at this stage, our QC will issue the inspection report and release it for shipping.B: Our serviceQuality and Service: We have always been to “customer first, service first” for the principle, for all customers to have better fitness equipment.Quick Lead Time: We’re dedicated to providing the quickest turnaround times and work very hard to ensure that all of your deadlines are met. Our general delivery is 25-50 days, which is according to the quantity of your order.After Sales Service: We can keep continuous communication and satisfy various needs of customers. If there’s any problem after the sale, the service department will try the best to improve the relevant services based on customers’ comments and feedback.Management Team: Our management team is formed by numerous professional experts in the fitness field. If our team is assumed to be blood, then our DNA will comprise morality, passion, professionalism, management experiences, plus successful cases.The advantage of Ntaifitness equipment manufacturersQuality AssuranceWe are adhering to the rigorous attitude seeking increasing perfection like scientists, and all of our fittings are procured from trusted suppliers. We have almost demanding quality testing so as to be perfect in every detail and provide you high-quality fitness equipment.Manufacturing AdvantageWe have a complete array of production equipment, including the laser cutting machine, automated robot welding machine and various types of CNC machines, such as CNC router. Standardized methods are utilized for high-end processing procedures. Rust removal is achieved through a combination of sand and electrostatic-spraying techniques. The reiteration of the spraying technique allows us to optimize surface treatment. The stress-test laboratory ensures the integrity of processed components. Never satisfied with the status quo, we are always trying to improve our product quality.Human ResourcesOur R&D team always perseveres in the highest standards within this industry. As a high-quality team, our R&D department is composed of mechanical engineers, biomechanical experts, and industrial modeling engineers, among others.Over 60% of technical workers have rich work experience in the same field for more than 3 years. They are committed to increasing the technical index during practice, for the purpose of making our customer satisfaction far ahead of others in this industry. Actually, the goal we are focusing on is always higher than the customer standards.Our DesignOur fitness equipment have a wide range in order to achieve a unified appearance and functionality, combine the user-friendly design and advanced technology, create the theme of healthy fitness equipment, and lead the fashion trend of fitness equipment, Different colors, materials, and products use the latest digital technology to ensure that we walk in the forefront of international design trends.Cost ControlWe are a direct fitness equipment factory, with advanced production equipment for mass production. Under the guidance of our proficient management personnel, production costs are effectively optimized, so can provide the most reasonable price.Logistics AdvantageWe are located in DeZhou City, ShanDong Province, China, which makes transportation extremely convenient. Our products have found export destinations in more than 70 countries and regions worldwide including the Americas, Europe, Africa, Asia, Oceania, etc.
- Home >
- Catalog >
- Business >
- Report Template >
- Home Inspection Checklist >
- Inspection Report Template >
- inspection report template for rental property >
- Inspection Report Form (Field Use