The Guide of drawing up Candidate Evaluation Form (Sample Online
If you take an interest in Tailorize and create a Candidate Evaluation Form (Sample, here are the easy guide you need to follow:
- Hit the "Get Form" Button on this page.
- Wait in a petient way for the upload of your Candidate Evaluation Form (Sample.
- You can erase, text, sign or highlight as what you want.
- Click "Download" to keep the materials.
A Revolutionary Tool to Edit and Create Candidate Evaluation Form (Sample
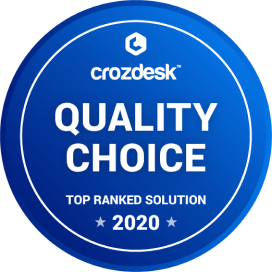
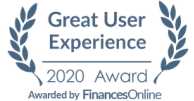
How to Easily Edit Candidate Evaluation Form (Sample Online
CocoDoc has made it easier for people to Modify their important documents via online website. They can easily Tailorize through their choices. To know the process of editing PDF document or application across the online platform, you need to follow this stey-by-step guide:
- Open the website of CocoDoc on their device's browser.
- Hit "Edit PDF Online" button and Import the PDF file from the device without even logging in through an account.
- Add text to PDF by using this toolbar.
- Once done, they can save the document from the platform.
Once the document is edited using the online platform, the user can easily export the document according to your ideas. CocoDoc ensures to provide you with the best environment for implementing the PDF documents.
How to Edit and Download Candidate Evaluation Form (Sample on Windows
Windows users are very common throughout the world. They have met a lot of applications that have offered them services in managing PDF documents. However, they have always missed an important feature within these applications. CocoDoc aims at provide Windows users the ultimate experience of editing their documents across their online interface.
The procedure of modifying a PDF document with CocoDoc is easy. You need to follow these steps.
- Select and Install CocoDoc from your Windows Store.
- Open the software to Select the PDF file from your Windows device and go ahead editing the document.
- Modify the PDF file with the appropriate toolkit showed at CocoDoc.
- Over completion, Hit "Download" to conserve the changes.
A Guide of Editing Candidate Evaluation Form (Sample on Mac
CocoDoc has brought an impressive solution for people who own a Mac. It has allowed them to have their documents edited quickly. Mac users can create fillable PDF forms with the help of the online platform provided by CocoDoc.
For understanding the process of editing document with CocoDoc, you should look across the steps presented as follows:
- Install CocoDoc on you Mac to get started.
- Once the tool is opened, the user can upload their PDF file from the Mac in seconds.
- Drag and Drop the file, or choose file by mouse-clicking "Choose File" button and start editing.
- save the file on your device.
Mac users can export their resulting files in various ways. Downloading across devices and adding to cloud storage are all allowed, and they can even share with others through email. They are provided with the opportunity of editting file through multiple methods without downloading any tool within their device.
A Guide of Editing Candidate Evaluation Form (Sample on G Suite
Google Workplace is a powerful platform that has connected officials of a single workplace in a unique manner. If users want to share file across the platform, they are interconnected in covering all major tasks that can be carried out within a physical workplace.
follow the steps to eidt Candidate Evaluation Form (Sample on G Suite
- move toward Google Workspace Marketplace and Install CocoDoc add-on.
- Upload the file and Press "Open with" in Google Drive.
- Moving forward to edit the document with the CocoDoc present in the PDF editing window.
- When the file is edited at last, save it through the platform.
PDF Editor FAQ
Is an PMP certificate helpfull in getting good employment opportunities?
There are several roles that comprise the project teams. These project teams work together under the hem of the project manager to successfully accomplish the project objectives. These objectives are in line with the organizational objectives and hence drive the business. Therefore it is very important for the leadership and top management to build a team as a recipe for success.In order to have this project team, companies prefer to engage in various roles that work together based on their job requirements. This also means that these team roles have clearly defined job descriptions and these job descriptions are also aligned with the project requirements. Therefore this is necessary that the project team has a good understanding of the project so that they can fulfill their job requirements in an aligned and effective manner. So it is not only the project manager role who should focus on PMP certification. Other project team roles must also focus on the PMP skill set. For instance, if your role requires to know project planning and if you lack this PMP skill set, then, you should consider attending a Microsoft Project training.Even for the sake of the PMP Exam application, it is not mandatory for the candidate to have a project management role. Rather, the candidate may have professional experience of three years along with a graduate degree. Most interestingly, candidates need to have experience of working in the project management process areas in any role: Initiating, Planning, Executing, Monitoring and Evaluating, and Closing. Hence the candidate is eligible for PMP Exam if they are working in any of the relevant roles contributing towards the project. This is one of the reasons that PMP aspirants prepare themselves to obtain certification and suit themselves for the project manager role.Project Management and Team RolesGenerally, teams have a variety of roles which can vary from project to project. Some of these roles include but are subject to the variation:Project managersAssociate/Asst. Manager – ProjectsTeam leads/ManagersProject Executives/EngineersSoftware DevelopersTechnical Project ManagersProject Delivery ManagerBusiness AnalystThese roles may have a different proportion of the required skill set with respect to their contribution to the project process area. For example, software developers are mostly working on project execution activities like software development. Whereas project managers look at the overall progress of the development activities and resolve any collaboration requirements among the stakeholders to ensure delivery. But both of these roles contribute towards the project execution.Likewise, the Assistant Project Manager will be assisting the project manager in various tasks like scheduling and collaboration. But with less authority and responsibility as compared to that of Project Manager. The team leads will be more towards managing their team members and their assignments. So every role is contributing towards the project in its own capacity.PMP Certification Jobs and Skill Set requirementIn this section, we give an overview of the skill set required by the project management and affiliated roles. According to an article in CIO, the high-performance projects require a certain set of skills to effectively execute the projects. The required skill set includes:Technical project management skillsLeadership abilitiesStrategic and business management mindsetChange management and organizational development expertiseTop-notch communication skillsTeam building and conflict resolution capabilitiesAdaptable and unflappable qualitiesExceptional facilitation skillsSince effectively executing projects has become more complicated, therefore, it makes sense that project managers who possess these skills, along with project management training (e.g. Microsoft Project Course) and experience, will become highly in-demand.Generally, the employers and recruiters look for the project managers with this skill set. As a project management professional, you have already demonstrated these skills and therefore this places your profile on top of the list of the recruiters during the project manager interview, screening and short-listing.According to the surveys, there will be 700,000 new project management jobs in the United States by 2020. This gives a heads-up to polish your skills and showcase to grab the opportunities with your PMP certification. Here are some of the key skills and PMBOK knowledge areas covered in the PMP certification exam. Project Management Professionals can:Lead and direct cross-functional teams to successfully deliver complex projects.Complete projects within the constraints of schedule, budget, and scope.Understand advanced project management concepts and processes.Apply PM methodologies and best practices to complete projects.Adhere to the code of ethics and professional conduct.Jobs for PMP Certification HoldersSince Project Management Professional (PMP) certification demonstrates the knowledge and experience to bring business and IT projects to successful completion, therefore, it is globally accepted that PMP certified professionals have the project management and managerial skills to complete projects on time, within the scope and budget.The market is very much aware of the positioning of PMI certifications and PMI is best known for its Project Management Professional (PMP) credential and the Project Management Body of Knowledge (PMBOK). PMBOK is a collection of best practices and standards for project management.Having more than 470,000 members in 207 countries, PMI is the world’s largest project management association and has certified more than 740,000 PMPs globally. This is the mere fact to understand the importance of PMP and the indicator of PMP certified professional induction trends in the market.We have listed some sample jobs posted by various companies on LinkedIn to hire project managers and alike roles. You can see in these examples that the PMP certification is one of the specified requirements which gives an added value while the recruitment process.PMP Certification Jobs Sample #1While there are no specific “PMP certification Jobs”, you will see that most of the project management jobs require PMP certification. That is why sometimes project managers look for PMP certification jobs. For instance, there is an available project management job in the San Francisco Area. The details of a project manager vacancy from NVIDIA are also listed.For the ones who do not know NVIDIA, they are an American Fortune 500 technology company incorporated in Delaware and based in Santa Clara, California. NVIDIA designs graphics processing units (GPUs) for the gaming and professional markets (source: Wikipedia). See below the project management job description of NVIDIA.While they mention several project management skills, the company seeks PMP certification as a “must to have” in the applicants applying for this position. This is just an example from the several PMP certification jobs that are available in the market.PMP Certification Job Sample #2Here is another example of the Integration project specialist form West Corporation.The focus is on the relevant experience with the primary preferred qualification of in-depth understanding of project management methodologies highlighting the PMP methodologies.PMP Certification Job Sample #3In this example, we have specifically picked a job posting for Business Analyst role in 7-Eleven in Plano, Texas.This is a single vacancy with multiple hats, in the job requirements, PMP certification marked with a plus in the criteria.PMP Jobs and Recognition of PMP within organizationsYour resume gets more eye-catching and hence selected as part of the displayed profiles of the organization. You are ranked higher to be picked up for projects that are more challenging and rewarding. This also motivates you to be an efficient and effective part of the management team.The PMP credentials are not the hot cake only for the technology departments, but also the other departments are aware of this fact. The Business Development department understands that the certification is the golden key to open the opportunities at the very first level. The Human Resource department also recognizes the importance of this fact. They are the ones who set the job requirements in collaboration with the technology department.The training and development department also realizes the value of the PMP trainings and Certifications. PMP trainings are sponsored by the organizations to advance the skills of the existing personnel. Some of the companies arrange their in-house PMP training either by the existing PMP employee or by outsourced training workshops.The recent decades have gone through the organizational structures trending form Functional to Projectized organizations. This trend has flourished many new players across the globe in addition to the big market players and there are more consulting organizations on the map. These consulting organizations do not target the functional or day to day tasks. These are working on the more challenging nature of business services for the clientele.PMP Certification Jobs and Global MarketThe internet and the digital era has not only given birth to new ventures but also expanded the horizon of the job market. The players who have enhanced and marked their global footing have increased their market share. This fact has been a great motivator for the organizations to keep abreast with the new trends and technologies.Companies are working continuously to improvise the skills of their employees and train them to meet the global requirements. By virtue of this competitive market, these companies train and certify their employees. And also the hiring requirements are being focused to get the best out of the market who is already skilled and have proved records. These criteria also impose the need of the certified professionals and so is the case with the Project Management Professionals (PMP). If you view the job postings of project management or senior project management, you will see the value of the certified professionals and PMPs.PMP credential is the dire need of these market players. They look forward to hiring talent with displayable skills. Therefore your PMP certification is a value-adding tool to showcase your ability to become a prominent member of this globally challenged market.Even the implementing organizations consider credentials like PMP certification while setting out criteria for vendor selection. Management and project management capabilities are also assessed while evaluating the best vendor. These criteria are helpful to assess the expertise and sustainability of the consulting organization.Read the full post: 2020 PMP Jobs - #1 Project Management Jobs for PMP Holders
How can a nuclear weapon penetrate the ground to create an underground burst?
Nuclear weapons cannot penetrate deep enough to make an underground burst. They don’t need to go very deep to get the maximum coupling effect of the weapons energy into the earth.Multi Megaton Weapons Now ObsoleteFootnotes take you to another answer of mine this was taken from for referencesWhat has changed that the world no longer is building megaton weapons? The need for multi-megaton weapons was the result of low accuracy of warhead delivery on target…. we needed a sledgehammer approach to take out hardened targets and the way that was done was through very high yield bombs >=5 MT typically. The average nuclear weapon size today in 2016 is about 443 KT at full yield but a large portion of those bombs can be adjusted in the field to a very small fraction of their potential yield.Today the accuracy of on target delivery has improved significantly ..we hit what we aim for. Making a weapon twice as accurate has the same effect on lethality as making the warhead eight times as powerful. Phrased another way, making the missile twice as precise would only require one-eighth the explosive power to maintain the same lethality. [3] This means we need less hammer to do the same job. In the 1980’s the development of earth penetrating rounds was another game changer. Not only were we on target but now we could penetrate hundreds of feet of earth and concrete before detonating the warhead. This allowed a 100 KT weapon to do the damage of a >1 MT surface detonation. This is the primary method now for targeting hardened targets and is the final driver for smaller yield bombs. (Note that conventional warheads can penetrate 100’s of feet through concrete, nuclear warheads are usually limited to less than 30 ft in concrete due to the complexity of the warhead not surviving further penetration. Soil penetration depth varies with composition but to get full ground coupling of energy only 4 or 5 meters is required).Penetration DepthThe technology exists to send warheads through over 200 feet of hardened reinforced concrete. [1] At mach 3.5 the metal slices through the concrete like butter, the concrete actually flows like a liquid at that insane level of pressure. However, all that is needed to get the most destructive ground coupling to a nuclear detonation is a dozen feet or so of penetration. So earth penetrating nuclear warheads are designed to detonate only a dozen feet underground or a dozen feet within a concrete structure.While the penetration depth increases as the impact velocity is increased, the penetrator will destroy itself if it strikes the ground at too high a speed. Empirical data obtained by firing solid steel projectiles into concrete suggests that the maximum impact velocity in this case is roughly one kilometer per second (mach 3) and the maximum achievable penetration depth of such a projectile in concrete is roughly four times its length. [2]The warheads complex assemblies remain in precision integrity even when impacting concrete at speeds greater than mach 3. The maximum penetration depth in concrete of a three-meter long EPW is less than 12 meters. Penetration depths will be larger in dry soil than concrete or rock. The integrity of the weapon would be in question if they had to go deeper than 20-40 feet.Super deep penetrations of +200 feet are done with conventional weapons and the use of conventional weapons is preferred over nuclear in those situations even in an all out nuclear war. [3] Winning a war is about attaining political goals not the maximum level of destruction.The net effect of the use of EPW’s (Earth Penetrating Weapons) is a reduction in the number of casualties as compared with the number of casualties from a surface burst. This is primarily due to a 96% reduction in the weapon yield needed using an EPW. The greater coupling of the released energy to the ground shock for a buried detonation is the same as a surface burst with 25 times the explosive energy. For rural targets, the use of a nuclear earth-penetrator weapon is estimated to reduce casualties by a factor of 10 to 100 relative to a nuclear surface burst of equivalent probability of damage.[4]To exploit that efficiency, in 1997 the US replaced its aging 9-megaton bombs with a lower-yield but earth-penetrating 300-kt model by putting the nuclear warhead from an earlier bomb design into a strengthened alloy-steel casing and a new nose cone. [5]To fully appreciate this evolution consider a targeting scenario as it was in the 1970’s as compared to 2020. In the 1970′s a hardened silo target required multiple megaton bombs to destroy a 1000 psi rated silo. Since weapons accuracy was no better than 200–300 yards you needed surface burst weapons greater than 1 megaton to take out the target. Now advance to the early 2000’s. That same target can be destroyed with a 70 kt EPW with a 100 yard accuracy. Fast forward to 2020 and that target can be taken out with a 1 kt EPW weapon with an accuracy of 10 meters. [6]REFERENCE SECTIONDevelopment of EPW technologyAn earth-penetrator weapon (EPW) is designed to detonate below the ground’s surface after surviving the extremely high shock and structural loading that result during impact and penetration. As discussed in more detail in Chapter 4, detonating the weapon beneath the surface greatly increases ground-shock effects, making the weapon more effective in destroying hard and deeply buried targets (HDBTs).EARTH-PENETRATOR TECHNOLOGY BACKGROUNDEarth-penetration technology in the United States dates to the early 1950s. The Mark 8, a nuclear bomb with the capability to penetrate soil and rock as well as concrete targets, entered the stockpile in January 1952. The Mark 11 bomb, a safety upgrade that replaced the Mark 8 in May 1957,1 was removed from the stockpile in 1958. Sandia National Laboratories (SNL) initiated an earth-penetration (EP) technology program in 1960.2The Department of Energy (DOE)/Department of Defense (DOD) programs, now the DOE’s National Nuclear Security Administration (NNSA) national laboratories, and DOD laboratories have maintained continuous EP technology development programs and testing, at various levels of activity, since that time. Of the more than 3,000 EP tests conducted, there are currently 1,084 representative tests recorded in the SNL Earth Penetration Database. Complete characteristics of the penetrators—physical characteristics, impact velocity, impact angle, impact angle of attack, penetrator path length, penetrator rest angle, test location, target site, target material, date of test, and associated programs—are documented in this database. Geologic materials penetrated include sand, silt, and clay soils, frozen soil, ice, and rock. Penetration tests into concrete targets have also been conducted. Target sites were located in Alabama, Alaska, California, Florida, Kansas, Nebraska, Nevada, New Mexico, Texas, and Utah.Important Parameters of Earth-Penetrator WeaponsPenetration tests have been conducted at various impact angles, angles of attack, and velocities into undisturbed geologic targets to provide insight into how the physical properties of a penetrator affect its performance. Data in the SNL database were obtained from weapon-sized penetrators instrumented to measure axial and lateral penetrator acceleration, strain in the EP case, and the structural response of internal components. Based on these data, Box 3.1 lists and defines physical properties of an EPW and impact conditions that are important in the design of an EPW. Figure 3.1 shows a typical EPW case configuration.The ogive nose shown in Figure 3.1 is a ballistic shape that is formed by rotating an arc of radius Ro, tangent to the cylindrical body around the centerline of the body. A 6 caliber radius head (CRH) ogive nose is generally used on an EPW that is designed for the penetration of hard material at velocities of less than 900 meters per second. For higher velocities, a 3 CRH (blunter) is recommended in order to maintain penetrator stability. For impact velocities less than 300 meters per second into hard or frozen soil, a 9.25 CRH nose or a length-to-diameter ratio of 2 for cone-shaped-nose penetrators (sharper noses) can be used, since nose tip heating is not a problem at lower velocities. The flare on the rear of the penetrator in Figure 3.1 is important for penetrator stability if the length-to-diameter ratio of the EPW is less than 6.BOX 3.1Important Earth-Penetrator Weapon ParametersPhysical CharacteristicsN: nose shaped: body diameter, mL: total penetrator length, mm: total penetrator weight, kgA: cross-sectional area, m2m/A: cross-sectional density, kg/m2Impact ConditionsV: impact velocity, m/sθ: impact angle between velocity vector (trajectory angle) and target surfaceα: angle of attack, angle between velocity vector (trajectory angle) and earth-penetration axisFIGURE 3.1 Typical earth-penetrator weapon case.Earth-Penetrator Weapons Design MethodologyThe national laboratories conducted two nuclear EPW engineering development programs between 1975 and 1990, using the SNL EP technology program design experiences and test database. The first program involved the W86 EPW payload for the Pershing II (P II) missile. Weapons-system-level EP tests that included warhead electrical system components and inert nuclear system components were conducted in soil, low-strength rock, and medium-strength rock at the Tonopah Test Range near Tonopah, Nevada. Missiles with system-level test units were also impacted into the 50 mile target area at White Sands Missile Range. The Los Alamos National Laboratory also conducted underground nuclear detonation tests of candidate nuclear systems. Engineering development of the W86 EPW was completed, and the design was put on the shelf. No weapons were produced.In 1986 a feasibility study was completed on a strategic earth-penetrator weapon (SEPW) to hold deeply buried targets at risk. Shortly after the study was completed, an advanced development SEPW program was initiated. Los Alamos National Laboratory and Lawrence Livermore National Laboratory were tasked to design nuclear systems and hardware for penetration tests and to support underground tests. SNL was tasked to provide systems engineering support to each nuclear laboratory’s effort. SNL was also tasked to design and develop the EP cases, hardened electrical components, and subsystems; to evaluate penetrator performance; and to investigate potential countermeasures. Approximately 60 penetration tests were conducted by the two laboratory teams. SEPW inert test units were impacted into a series of in situ (undisturbed) soil and rock targets at varying impact angles and velocities. A small number of underground nuclear tests were also conducted at the Nevada Test Site.The programs described above are examples of programs in which nuclear weapons have been designed and developed to counter the uncertainties of an earth-penetration event and to enhance the survivability of an EPW. The important parameters of these weapon designs and the maximum impact velocity recorded in the SNL database are used in the calculations described below to predict the maximum depth of penetration that can be expected in soil, low-strength rock, and medium-strength rock media.Target GeologyThe greatest uncertainty in predicting EPW depth of penetration and structural survival of the weapon until detonation is due to the inherently heterogeneous nature of earth materials. Rock formations typically are composed of layers of materials of different strength such as the formations shown in Figure 3.2. They can also include joints and fractures as well as layers of different strength and sloping layers, as shown in Figure 3.3.The type of massive, relatively homogeneous formation with few cracks and fissures that is shown in Figure 3.4 is rare. Even areas expected to have soil to extended depths may include areas of unexpectedly hard material. These uncertainties can be countered to some degree by designing an EPW to be as rugged as possible, consistent with mission and system requirements. Rugged EPWs have the highest cross-sectional density possible so as to enhance penetration depth, and a length-to-diameter ratio of 8 to 10 for stable trajectory; thus, lateral loading is minimized during penetration. A one-piece EP case fabricated from the best available high-strength, high-fracture-toughness steel is recommended in order to withstand the high lateral loading that occurs when the EPW encounters heterogeneous formations. Internal components and subassemblies must be designed and packaged to survive high-frequency structural loading. The maximum impact velocities and hardest expected target materials determine the selection of nose shape.FIGURE 3.2 Limestone formations near Nashville, Tennessee, exhibiting layers of materials of different strengths. Photo courtesy of William J. Patterson.FIGURE 3.3 Sandstone syncline in New Mexico showing sloping layers. Photo courtesy of William J. Patterson.FIGURE 3.4 Massive sandstone in New Mexico showing relatively homogeneous rock. Photo courtesy of William J. Patterson.EMPIRICAL EQUATIONS FOR PREDICTING PENETRATION CAPABILITYMany equations predictive of earth-penetrating capabilities of EPWs have been developed over the past 40 years. In early 2000, two of the more widely used empirical equations were evaluated, and calculated depths were compared with large-scale tests of penetrators impacting into two different types of in situ rock formations at the Tonopah Test Range. Both of the equations predicted depths that agreed well with the Antelope Tuff and the Sidewinder Welded Tuff rock penetration data documented in the SNL Earth Penetration Database.3 One equation, developed by C.W. Young, was published in 1967.4 The most recent update was in 1997.5 The other equation was developed by M.J. Forrestal and published in 1994.6Presented here (Box 3.2), Young’s equation illustrates the use of EP parameters to calculate maximum depths of penetration achievable in soil, low-strength rock, and medium-strength rock, as shown in Table 3.1.The following sample calculation with Young’s equation uses the SEPW parameters and an impact velocity of 1,220 meters per second in low-strength rock.BOX 3.2Young’s Empirical EquationWhere D = depth of penetration in meters, α = 0.0000175, Ks = scaling factor, S = empirical target constant, N = penetrator nose coefficient, m = penetrator mass in kilograms, A = penetrator cross-sectional area in square meters, and Vs = impact velocity in meters per second.For soil the scaling factor Ks is defined asandFor rock and concrete the scaling factor Ks is defined asandThe nose coefficient N for a tangent ogive is defined aswhile the nose coefficient for a conical nose is defined byIn the nose coefficient equations, Ln is the length of the penetrator nose in meters, and d is the diameter of the penetrator body in meters.The constant S is an empirical value, which depends on the target material. Its value is determined by measuring the depth of penetration for a given penetrator tested in a given geologic material and applying the equation to compute the value of S. A reasonable value of the empirical constant for a given geologic material is obtained by averaging several of the values for Sobtained from several penetration tests. Once S has been determined experimentally for a given target material, the other variables in the equation may be altered to estimate depth of penetration into the same target material.TABLE 3.1 Empirically Estimated Maximum Credible Depths of Penetration of Earth-Penetrator Weapons in Three Types of Rock and Soil MediaGivenwhere α = 0.0000175, S = 1.3, nose CRH = 3, m = 411 kg, d = .274 m, and V = 1,220 m/s, then Ln/d = (CRH − .25) 1/2 = (3 − .25) 1/2 = 1.66, N = (.18 × 1.66) + .56 = .85, A = (.274) 2/4 = .059 m2, and (m/A)0.7 = (411/.059) 0.7 = 492.HenceBased on data for deceleration versus time from a large number of tests, the best estimate of peak rigid body deceleration is 1.5 times the average deceleration:MAXIMUM CREDIBLE DEPTHS OF PENETRATIONTable 3.1 presents empirically estimated maximum depths of penetration in three typical geologic materials. These depths were calculated using Young’s empirical equation. In order to add credibility to these estimates, the following data were used in the calculations: the physical properties of the W86 P II EPW and SEPW designs, penetrability numbers for the geologic media supported by test data, and impact velocities no greater than the highest velocities documented in the SNL Earth Penetration Database. The results of an EPW bomb optimized with the highest m/Afeasible, within a 2,700 kilogram weight limit, are also shown to illustrate the ability of a robust EPW to minimize axial deceleration.The 10,000 g peak deceleration capability of the SEPW and W86 P II EPW was the limiting factor in medium-strength rock. The impact velocity used in the calculations in low- and medium-strength rock was limited by the 10,000 g peak deceleration capability of the SEPW and W86 P II EPW. Also, impact velocity was limited to 1,525 meters per second, since no test data exist above 1,525 meters per second. The heavy weight of the EPW bomb limits the delivery system to aircraft only; therefore, the impact velocity for the EPW bomb was based on a reasonable maximum velocity obtainable from a high-altitude airdrop.The heavy, high-cross-sectional-density bomb impacting at 500 meters per second achieved the maximum calculated depth in medium-strength rock, and the peak axial deceleration did not exceed 2,500 g. The low-yield EPW impacting at 1,500 meters per second achieved the maximum depth in low-strength rock and silty clay soil. Peak axial decelerations were no greater than 9,000 g and 1,500 g, respectively.It must be kept in mind that these calculations assume that the penetrated medium is homogeneous; thus, these are the minimum expected depths. The maximum depth in soil could vary by ±20 percent based on the accuracy of Young’s equation.7This would give a maximum depth of penetration for the low-yield EPW of approximately 140 meters in soil. The depths in rock could show even greater variability due to the nonhomogeneity of rock formations. Depths up to 50 percent greater than pretest estimates have been observed. The maximum depth in low-strength rock could be approximately 30 meters, and approximately 12 meters in medium-strength rock. Designers and test engineers are usually most interested in estimates of minimum depth since minimum depth results in the highest expected axial EPW deceleration.W61 SYSTEMThe W61 EPW was intended to be an interim weapon to provide an EPW capability until the SEPW was fielded. The B61-7 was selected for conversion into an EPW because its internal components were required to survive relatively high axial and lateral acceleration loads. The B61-7 had to survive loading from an impact velocity of approximately 30.5 meters per second onto hard surfaces—impact conditions resulting from low-level, high-speed aircraft release and parachute-retarded lay-down. Detonation time was set for a safe aircraft separation time.W61 predevelopment engineering began in 1987. Engineering development began in 1990, and the program was terminated in 1992. The W61 was designed to be a rapidly deployable system. The delivery system had the capability of delivering the W61 to the target surface at optimum impact conditions. For the targets of interest, optimum conditions were impact angles within 10 degrees of target normal, an angle of attack (angle between velocity vector and EPW centerline) of less than 2 degrees, and impact velocities around 245 meters per second.Following are the initial basic guidelines from the DOD for the conversion of the B61-7 bomb into a W61 EPW:8Minimize new component development,Maximize the use of existing hardware, andMinimize changes to the B61-7 electrical system.A one-piece, cone-nosed penetrator case was designed to house the nuclear system and the warhead electrical system. The case was fabricated from high-strength steel with high fracture toughness. Since changes to components of the nuclear system and warhead electrical system were not allowed, the W61 EPW survivability limit was governed by the deceleration capability of the internal components. The system survivability level was determined by testing. Tests conducted during engineering development demonstrated that the W61 had the capability to survive penetration of 0.3 meter of concrete, hard soil, and low-strength rock at specified impact conditions. The W61 had an airburst and a contact-burst capability as well as subsurface-burst capability.B61-11 EARTH-PENETRATING BOMBThe B61-11 was developed to replace the B53 gravity bomb, which had entered the stockpile in 1962. In 1988 an interim nuclear safety modification was made, resulting in the B53-1. However, even with the modification, the B53 did not completely meet standards for modern weapons safety, security, and reliability. Figure 3.5 and Table 3.2 show the final design and delineate the properties of the B61-11.Following are the initial basic guidelines from the DOD for conversion of the B61-7 into an earth-penetrating bomb and the resulting actions:Carry out a rapid development program.The program was authorized on September 15, 1995.Major assembly release occurred on December 30, 1996.Minimize new component development.EP case forgings from the cancelled W61 program were http://used.No changes were made to the B61-7 nuclear Domenenavnet er parkert hos UniWeb.no changes were made to the B61-7 electrical system.FIGURE 3.5 Final design of the nuclear, earth-penetrator (EP) B61-11. SOURCE: Sandia National Laboratories. 2003. B61-11 Final Weapon Development Report (U), SAND 2003-2344, Albuquerque, N.Mex. (Classified).Because changes to the nuclear system and warhead electrical system were not allowed, the survivable deceleration level of the B61-11 was limited to the deceleration limits of the B61-7 internal components. Penetration tests with functional warhead electrical-system components and simulated nuclear assemblies were conducted at different impact velocities into hard soil and frozen soil to demonstrate B61-11 capability in the targets of interest.The classified military requirements for the B61-11 include limits for soil penetration capabilities, yield, center of gravity, reliability, stockpile quantities, and ballistic characteristics.The B61-11 was developed to ensure a capability to continue to hold selected deeply buried targets at risk.CURRENT ROBUST NUCLEAR EARTH PENETRATOR PROGRAMThe Robust Nuclear Earth Penetrator program is an engineering feasibility study. It was initiated in May 2003 with the intention of its being a 2-year study, with two teams working on the study: a Los Alamos National Laboratory (LANL) and Sandia National Laboratories Albuquerque (SNLA) team, and a Lawrence Livermore National Laboratory (LLNL) and Sandia National Laboratories Livermore (SNLL) team. The purpose of the program is to determine if, using the major components of an existing weapon system, an earth-penetrator system can be designed that can hold at risk a significantly larger number of targets than the B61-11 can. The LANL/SNLA team’s focus is the B61-7, and the LLNL/ SNLL team is addressing the B83. The basic approach is to increase the cross-sectional density of these. No changes in the parent weapon yield are allowed. The study is allowed to address potential changes to internal components, as long as the changes do not require any nuclear certification tests. Owing to budget constraints the study is now limited to the robust nuclear earth penetrator (RNEP) being studied by the LLNL/SNLL team. At this time there is no decision on when or if the LANL/SNLA team will restart its study.Following are general guidelines from the DOD for the RNEP under study by the LLNL/SNLL team:9The RNEP weapon is required to be able to do the following:Survive penetration and not rebound from the target;Reach a certain depth in a specified geology (the “threshold”);Preserve or improve original weapon functionality; andPreserve or improve original weapon safety, security, and reliability.Regarding the compatibility of the RNEP with delivery aircraft:The maximum weight, length, and diameter of the EPW case are to be determined by delivery aircraft requirements.Modifications to the Arming, Fusing, and Firing (AF&F) system are allowed.The AF&F capability level is to be determined by structural testing.Modification of the nuclear system is allowed provided no nuclear certification testing is required.The properties of the LLNL/SNLL RNEP are as follows:Mass, including tail kit—1,379 kg,Diameter—0.53 m, andPenetrator length (may be extended by tail kit)—2.54 m.Following are guidelines from the DOD regarding the RNEP guidance system:RNEP is to be a guided and controlled weapon system. Its guidance system will do the following:Allow for precise targeting,Allow for optimization of angle of attack and incidence control, andMinimize the stresses on the EPW system.RNEP system capability will be determined by experimentation, test, and analysis.The RNEP survivability level is set by the structural limit of the nuclear system and the arming, fusing, and firing system.NOTES1. F.C. Alexander. 1967. History of Gun Type Bombs and Warheads Mark 8, 10, 11 (U), SC-M-67-658, Sandia National Laboratories Library, Albuquerque, N.Mex., May (Classified).2. W.N. Caudle and A.Y. Pope. 1962. Project Trump: Progress Report No. I, SCTM 56-62 (71), Sandia Program for Earth Penetrating Systems, Sandia Corporation, Albuquerque, N.Mex., April.3. W.J. Patterson and R.S. Baty. 2003. “Comparison of Two Empirical Equations with Large Scale Penetrator Tests into In Situ Rock Targets,” 11th International Symposium on Interaction of the Effects of Munitions with Structures, Mannheim, Federal Republic of Germany, May 5-9.4.C.W. Young. 1967. The Development of Empirical Equations for Predicting Depth of an Earth Penetrating Projectile, SC-DR-67-60, Sandia National Laboratories, Albuquerque, N.Mex., January.5. C.W. Young. 1997. Penetration Equations, Contractor Report, SAND 97-2426, Sandia National Laboratories, Albuquerque, N.Mex., October.6. M.J. Forrestal, B.S. Altman, J.D. Cargile, and S.J. Hanchak. 1994. “An Empirical Equation for Penetration Depth of Ogive-Nose Projectiles into Concrete Targets,” International Journal of Impact Engineering,Vol. 15, No. 4, pp. 395-405.7. W.J. Patterson and R.S. Baty. 2003. “Comparison of Two Empirical Equations with Large Scale Penetrator Tests into In Situ Rock Targets,” 11th International Symposium on Interaction of the Effects of Munitions with Structures, Mannheim, Federal Republic of Germany, May 5-9.8. Sandia National Laboratories. 1992. W61 Weapon Development Report (U), SAND 91-2243, RS 3151/91/00024, Albuquerque, N.Mex., March 1 (Classified).9. Sandia National Laboratories. 2003. B61-11 Final Weapon Development Report (U), SAND 2003-2344, Albuquerque, N.Mex. (Classified).[1]Footnotes[1] 3 Earth-Penetrator Weapons
- Home >
- Catalog >
- Miscellaneous >
- Evaluation Form >
- Interview Evaluation Form >
- Interview Assessment Form >
- candidate evaluation form sample interviewer >
- Candidate Evaluation Form (Sample