The Guide of editing Save In The Heating Expenses, Reduce Moisture Risks Online
If you are curious about Edit and create a Save In The Heating Expenses, Reduce Moisture Risks, here are the simple ways you need to follow:
- Hit the "Get Form" Button on this page.
- Wait in a petient way for the upload of your Save In The Heating Expenses, Reduce Moisture Risks.
- You can erase, text, sign or highlight of your choice.
- Click "Download" to save the documents.
A Revolutionary Tool to Edit and Create Save In The Heating Expenses, Reduce Moisture Risks
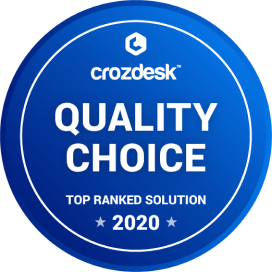
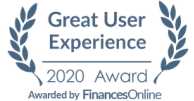
Edit or Convert Your Save In The Heating Expenses, Reduce Moisture Risks in Minutes
Get FormHow to Easily Edit Save In The Heating Expenses, Reduce Moisture Risks Online
CocoDoc has made it easier for people to Customize their important documents across online website. They can easily Alter through their choices. To know the process of editing PDF document or application across the online platform, you need to follow these simple steps:
- Open the official website of CocoDoc on their device's browser.
- Hit "Edit PDF Online" button and Choose the PDF file from the device without even logging in through an account.
- Edit the PDF for free by using this toolbar.
- Once done, they can save the document from the platform.
Once the document is edited using online website, you can download or share the file according to your ideas. CocoDoc ensures that you are provided with the best environment for implementing the PDF documents.
How to Edit and Download Save In The Heating Expenses, Reduce Moisture Risks on Windows
Windows users are very common throughout the world. They have met thousands of applications that have offered them services in managing PDF documents. However, they have always missed an important feature within these applications. CocoDoc aims at provide Windows users the ultimate experience of editing their documents across their online interface.
The steps of editing a PDF document with CocoDoc is very simple. You need to follow these steps.
- Choose and Install CocoDoc from your Windows Store.
- Open the software to Select the PDF file from your Windows device and proceed toward editing the document.
- Customize the PDF file with the appropriate toolkit provided at CocoDoc.
- Over completion, Hit "Download" to conserve the changes.
A Guide of Editing Save In The Heating Expenses, Reduce Moisture Risks on Mac
CocoDoc has brought an impressive solution for people who own a Mac. It has allowed them to have their documents edited quickly. Mac users can fill forms for free with the help of the online platform provided by CocoDoc.
In order to learn the process of editing form with CocoDoc, you should look across the steps presented as follows:
- Install CocoDoc on you Mac firstly.
- Once the tool is opened, the user can upload their PDF file from the Mac simply.
- Drag and Drop the file, or choose file by mouse-clicking "Choose File" button and start editing.
- save the file on your device.
Mac users can export their resulting files in various ways. They can either download it across their device, add it into cloud storage, and even share it with other personnel through email. They are provided with the opportunity of editting file through various methods without downloading any tool within their device.
A Guide of Editing Save In The Heating Expenses, Reduce Moisture Risks on G Suite
Google Workplace is a powerful platform that has connected officials of a single workplace in a unique manner. While allowing users to share file across the platform, they are interconnected in covering all major tasks that can be carried out within a physical workplace.
follow the steps to eidt Save In The Heating Expenses, Reduce Moisture Risks on G Suite
- move toward Google Workspace Marketplace and Install CocoDoc add-on.
- Select the file and tab on "Open with" in Google Drive.
- Moving forward to edit the document with the CocoDoc present in the PDF editing window.
- When the file is edited completely, download and save it through the platform.
PDF Editor FAQ
What happened to TWA Flight 800?
The answer is simple and it will make you think twice about flying. Throw away your conspiracy theories, the simplest answer is almost always the right one. I was involved in the commercial and military programs that were partially ignited by TWA 800. The issue was known but TWA 800 made it a priority. All this falls under what is termed “ The Aging Aircraft Wiring Systems” initiatives., which were launched in earnest by multiple organizations once the severity was understood. The aviation industry in general was caught off guard. The FAA, AFRL, NAVAIR/ NAVSEA, DARPA, NASA, NTSB, Sandia, major universities and all the airframe OEM’s, all had major programs launched. We had no technology to assess how bad things had become but the initial findings were very bad, I mean scary bad. In many cases, it was starting to look like it would be cheaper to scrap some aircraft than trying to fix them.What they discovered is that the wiring insulation lost a lot more of its insulation properties over time than what was anticipated and that wire clamping and routing had to be re engineered in many cases . All this is especially true in aircraft fuel tanks. Jet fuel isnt explosive unless it is a vapor. The last place you want a bare wire where arcing could take place is in a fuel tank. The more aircraft they inspected the red flags were hoisted ever higher. It was so bad that the FAA issued directives on certain model aircraft, restricting them to not fly below a certain fuel level in the tanks. This was to assure that the bare wire areas were always submerged in fuel, especially during takeoffs and landings.Since then a lot has been done, but it is still a big problem. The OEM’s and the FAA have been working towards fuel tank inerting systems. Systems that siphon off the fuel vapor and replace it with nitrogen, eliminating the explosion risk.Just dig around a bit on the FAA’s website to see the details and you will think twice about boarding an old aircraft.A final note. One of the big engineering mistakes identified as the likely cause of such an explosion was that the wiring harness bundles were not segregated by what the wires were doing. The fuel level indicator sensors in the fuel tanks are low voltage and low current. They are designed not to spark. During these investigations and research initiatives, the original wiring harness designs were reviewed for potential problems. Sure enough there were plenty.The biggest risk came from bundling high power and high voltage wires together in the same harness as the low voltage sensor wires. Anyone who has ever worked on cars as a hobby can tell you about being zapped by the ignition coil through the wire insulation. In an aircraft, its the perfect storm for catastrophe. So common sense seemed to have been left out of the design meetings on a lot of this. This was one of the first things that they started to fix with Airworthiness Directives from the FAA.The final words from flight 800 right before the explosion, the captain was recorded as saying, “Look at that crazy fuel flow indicator there on number four, see that? The likely spark that ended the flight.Inside a 747 center wing tank .. size of a roomwalkthrough the fuel tanks in below video to appreciate the volumeAdditional notes …I have added information on what has happened in the industry, due to the many comments on maintenance, in the sections below.An NTSB presentation from back when i was involved with this ntsbfueltanks.pptA couple of slides from the above NTSB presentation from 2007 ….lots of people asked if other planes have had the issue…here are severalJUST ADDED - For those who want the hard core details on the latest environmental testing on wires : http://www.tc.faa.gov/its/worldpac/techrpt/ar082.pdfUSA Today http://usatoday30.usatoday.com/news/washdc/2001-05-02-faa.htm05/01/2001 - Updated 11:31 PM ETFAA to issue strict fuel-tank safety rulesBy Alan Levin, USA TODAYNearly five years after TWA Flight 800 exploded, federal aviation officials plan within days to issue tough new fuel-tank safety standards. The Federal Aviation Administration's final regulations would apply new standards to the entire fleet of about 7,000 commercial aircraft, several aviation sources told USA TODAY. The agency has estimated the changes will cost airlines about $170 million.The long-awaited rules address safety recommendations from the TWA 800 accident, which killed 230. The rules will require more inspections of tanks and revamped designs.The FAA estimated that without any changes the world's airlines could expect a fuel-tank explosion once every 4½ years. Officials hope the new fuel-tank rules will stretch the time between explosions to about 15 years.Instead of settling the issue, however, the new rules are intensifying the debate over what additional steps are needed to prevent fuel-tank blasts.The FAA last year proposed injecting tanks with inert gas to prevent explosions. But airline officials in recent weeks told an FAA advisory group that inert gas will not be necessary with the new standards, several aviation sources say. The airline industry contends the risks are so small that the estimated $1.6 billion cost of using inert gas would be better spent solving other safety problems.This contradicts findings by the National Transportation Safety Board last year that the only way to eliminate fuel explosions is by using inert gas.Three jets have been destroyed by center fuel tank explosions since 1990. On March 3, one person died when a Thai Airways International jet parked at a terminal in Bangkok was destroyed. Investigators for the National Transportation Safety Board say preliminary evidence shows the jet's center fuel tank exploded.Among the steps being taken to reduce the risks is an effort to get airlines to decrease use of on-board air conditioners, which heat fuel tanks. Last week, the FAA also issued an emergency order to shut off pumps in empty 737 tanks.USA Today Air-cooling gear can heat tanks05/01/2001 - Updated 10:00 PM ETAir-cooling gear can heat tanksBy Alan Levin, USA TODAYEvery day this summer, thousands of jets will take off with fuel tanks holding a heated, explosive mix of gases.Despite dozens of safety measures enacted since TWA Flight 800 exploded in 1996, officials continue to debate whether fuel tanks are safe enough. In the wake of another deadly fuel tank explosion aboard a jet in Bangkok, Thailand, in March, USA TODAY sought to determine how airlines in this country are following one suggestion to help reduce the heat in fuel tanks.In some Boeing jets, tanks sit next to air-conditioning systems that blast them with heat. At normal temperatures, jet fuel is difficult to ignite. But when fuel vapors get hot enough, a single spark can set off an explosion capable of breaking a jet apart in flight. Three such fatal explosions have destroyed jets since 1990.In a change from just a few years ago, many jets now use cold air piped in from the airport terminal instead of using the aircraft's own air conditioning, USA TODAY found.But roughly half of all flights in summer months still use the jets' air-conditioning systems, according to information from pilots, airline spokesmen and government officials."I think the running of the air-conditioning packs on the ground is the most important contributor to the development of (explosive) vapor," says Bernard Loeb, the recently retired head of the National Transportation Safety Board's aviation accident investigation team.After the TWA explosion, which killed 230 people, the NTSB recommended that air conditioning from the terminal be used.Explosions are rare, but the FAA estimates that on the average jet, fuel tanks are flammable 35% of the time. That could be reduced to 25% with mandatory use of alternative air-conditioning sources. Most of that risk occurs on the ground or shortly after takeoff. Cooler air at high altitudes cools fuel tanks.Spokesmen for Boeing, which built the three jets that exploded, and airlines say the tanks are safe. "We don't believe that the carriers who continue to run the (air-conditioning) packs have created an unsafe condition," Boeing spokesman Tim Neale says.One year ago, Boeing issued a letter to its customers suggesting that, "when available," airlines pipe cool air in from the terminal rather than run the on-board air conditioners. Airline officials say they have increasingly begun using "ground-conditioned air" in recent years, but more for economic than safety reasons. Cooling a jet with a system on the ground is cheaper than running a jet's air conditioners.Large carriers such as American Airlines and United Airlines direct pilots to switch off on-board air conditioners at terminals with an alternative source of cool air, spokesmen said.Airlines say that virtually all the nation's large hub airports are now equipped with air-conditioning systems at terminals. Southwest Airlines, which often flies to alternative destinations, uses ground air conditioning at about half of its most popular destinations, and the number is growing, spokeswoman Beth Harbin said.Alternative air conditioning can help only so much, however. Pilots report that some widebody jets are too big to be cooled exclusively by outside air, so they must continue to run on-board conditioners. And many outlying airports do not offer air conditioning.Because a jet's interior heats up so quickly in the sun, pilots say they sometimes have no alternative but to operate on-board conditioners. "I'm going down to Cancun, Mexico, this afternoon," airline pilot David Heekin said recently. "You better believe I'm going to have the air-conditioning packs going full swing."On jets made by McDonnell Douglas, such as the MD-11 and MD-80, the air conditioners were not placed next to the fuel tank. (Boeing now owns McDonnell Douglas.) Airbus placed air-conditioning packs next to tanks on its jets, but the company insulated the tanks and vented the area to reduce heat.see footnote link for overview of industry best practice and regulations on aircraft wiring from the FAA as a direct result of these activities.[1]Analysis of wreckage by Rendon GroupDisasters waiting to happen ……Photo of Arc-through of In-tank Fuel Pump Housing representative of post-accident inspection program (not from TWA 800) More aircraft would have shared the same or similar fate as TWA 800. We got lucky and fixed the problems first.Further ReadingAircraft Maintenance -The Inspection Process from http://www.coopind.com/news_AvMaint-WireMaintenance.htmOngoing wiring inspection is part of any aircraft’s regular safety check process. “In various checks (A/C/D-check) wiring is controlled visually for cleanness, cracks, chafing, color change and installation,” Arntz said. “This is done according to Original Equipment Manufacturer Standard Practice Manuals and EWIS (Electrical Wiring Interconnection System) tasks incorporated into the Aircraft Maintenance Program.”Still, unless something obvious happens—shortly before the explosion on TWA Flight 800, the captain was recorded as saying, “Look at that crazy fuel flow indicator there on number four, see that?”—electrical problems can go unnoticed. This is why such problems may not be found until the C- or D-Check, when “an aircraft is pretty much disassembled down to its bones,” said Frank Correro, StandardAero’s avionics manager in Springfield, Ill. “This is when technicians have their best opportunity to look at all of the aircraft’s wiring, to spot and rectify problems.” The only exceptions are self controlling systems built into an aircraft system that identify faults through BITE (Built-in Test Equipment) tests, and power wires that are specifically monitored with load control units (circuit breakers) to indicate system failure and protect wiring.Sometimes equipment manufacturers can help when aircraft wiring problems are identified in the shop. “Recently, HARCO was asked to look at a harness that had been in service for 20 years,” Gannon said. “The harness, which measured exhaust gas temperatures mated to probes, required exposed ring terminals to be fastened to the probe stud.” Now such an exposed ring terminal can invite moisture, which can reduce the insulation resistance of a wire harness. To address this, “Harco introduced some features to prevent the harness from absorbing water that improved the insulation resistance properties of the harness, and prevented false warning indicators from being triggered in the cockpit,” he said.What to Look ForUnfortunately for aircraft maintenance technicians, there is no advanced handheld device that can be waved over aircraft wires, to detect faults quickly and reliably. Instead, it takes careful visual inspections of wiring bundles, along with manipulation of wires for flexibility and signs of cracking, to detect problems before they become serious.“The problem is that most mechanics are not given extensive training in wiring inspection,” said Paul Sneden. He is an instructor at Global Jet Services. Based in Weatogue, Conn., Global Jet Services offers a range of professional development and continuing educations courses for aircraft technicians, including a week-long course in wiring inspection and maintenance that is used by MROs such as StandardAero. “They need extra hand-on training to identify and deal with the many signs of deteriorating aircraft wiring.”So what should mechanics be looking for when inspecting aircraft wiring? In general, anything that doesn’t look like factory-standard, Sneden replied. Ideally, wiring bundles should be secure but not under stress, with all clamps in place and properly locked. Exterior insulation should be unbroken and uncracked, and it should continue to be when flexed by hand to spot any hidden damage.Aging, faulty wiring is also thought to have contributed to the cockpit fire on Swissair 111 on September 2, 1998. While suggestive, the Canadian TSB investigation was unable to confirm if arcing from wiring of the in-flight entertainment system was the main event that ignited the flammable covering on insulation blankets that quickly spread across other flammable substances.Any form of staining is bad news. It could point to fluid leaking onto the wires, or deterioration of the wire’s insulation. “Similarly, any sign of chafing, charring, burning or arcing is not to be dismissed,” said Sneden. “The bundle needs to be removed and inspected, and if need be replaced.”That’s not all. Any signs of damage on wiring could be evidence of failures in other parts of the aircraft’s systems and airframe. The causes for wiring damage need to be tracked back to the source, so that these problems can be dealt with as well.A rule of thumb is the older and/or more used the aircraft, the more likely that the wiring is suffering from age-related deterioration. Since aircraft 20 years or older fall into the ‘aging’ category, mechanics need to be extra-vigilant when working on anything made in 1993 or earlier.Unfortunately, until the current wave of airline fleet renewals is over, MROs will find themselves coping with an increasing number of aging aircraft on a daily basis. The problem of wire deterioration is thus considered to be so serious, that “EWIS has been incorporated as a preventive measure to monitor wire aging,” said SR Technics’ Arntz. “Therefore it can be stated that on condition maintenance has been changed to a more preventive maintenance concept for wiring.”So far, “a complete re-wiring of aged wires is not yet a part of the rulemaking agenda,” he added. But this might change as active air fleets get older and if more aging wire issues emerge.Vigilance is VitalIf there is a moral to this tale, it is that aircraft wiring is a difficult-to-service element that must be monitored, inspected and maintained as rigorously as engines and avionics. The losses of TWA Flight 800 and Swissair Flight 111 point to the devastating consequences that can occur should this not happen.from An overview of the aircraft wiring issueBy David Evans, Editor Aviation Maintenance- Reprinted courtesy of Aviation Maintenance/Access IntelligenceThe potential hazard posed by bad aircraft wiring has generated a tremendous amount of activity in the industry. Some operators now treat wiring as a system, meriting attention during maintenance equivalent to the black boxes and other electrical components to which the wire is attached. The Federal Aviation Administration (FAA) proposal for fleetwide inspection of wiring in zones containing combustable materials or wiring within two inches of hydraulic, mechanical or electric flight controls could well involve a whole new - albeit necessary - burden on aircraft maintainers.The National Transportation Safety Board (NTSB) lent added urgency to the need for wiring inspections with its late June press conference, timed shortly before the 10 th anniversary of the TWA Flight 800 disaster, to reinforce and restate the Board’s concern about fuel tank safety and aging, cracked and deteriorated wiring. Recall that the accident airplane, an old B747-100, blew up shortly after takeoff from New York’s JFK International Airport on July 17,1996, for an overnight flight to Paris.All 230 aboard were killed when flammable vapors in the center wing fuel tank exploded. Electrical arcing in a bundle of wires outside the fuel tank produced a surge of current that passed down a fuel quantity indication system (FQIS) wire. As the Board noted in its press release of June 29, “The ignition of the flammable fuel/air mixture in the tank was attributed to an electrical failure.”Chafing the Dominant ProblemTo be sure, numerous airworthiness directives (Ads) have been issued since the TWA disaster, mandating wiring and other modifications to ensure electrical system safety. While the FAA does not have good records on the incidence of wire failures in the commercial industry, the U.S. Navy has amassed considerable information and insight. Navy data suggests that as many as one million man hours are spend annually in troubleshooting, isolating, locating and fixing wiring faults. Naval Air Systems Command (NAVAIR) data suggests that nearly as many hours are spent on unscheduled wiring maintenance as on scheduled maintenance.Further, the data collected by NAVAIR indicated that chafing contributed to more than a third (37%) of all wiring failures on Navy aircraft during the period 1980-1999. Moreover, despite the fact that chafing, or the erosion of insulation and the exposure of conductor, is a known problem, and the tools to resolve it are available, analysis of data from the years 2000 to 2004 show that chafing remained the leader of all wire failure modes on Navy aircraft.Perhaps the closest to an industry wide measure for the commercial side comes from the fleet wide inspections mandated by the FAA for fuel system wiring on the B737 fleet in 1998. The inspections were directed after fuel was observed leaking from a conduit for wiring that had been opened by electrical arcing. All B737 operators were required to report their findings to the FAA. The inspections revealed a clear relationship between aircraft age and the severity of the severity of the problems found. Fully 30% of aircraft with more than 70,000 hours were found with severe chafing and bare wires.That is twice the percent found on B737s with fewer than 70,000 hours. Some commercial operators have raised awareness of good wiring husbandry and practices to be avoided. For example, United Air Lines has widely distributed a poster outlining the do’s and don’ts for wiring maintenance.United’s laudable effort notwithstanding, we offer below a somewhat broader perspective of the aircraft wiring issue, including a contrarian view to the search for ever thinner and lighter wire insulation.Wiring 101The amount matters. Modern jets contain 100-200 miles of wiring running into every nook and cranny of the airplane. To borrow a biological metaphor, the wiring is akin to the body’s nervous system.The trend matters. New jets feature more wiring carrying more current (the advent of wireless systems is reversing this trend). The cabin area of a new-production jet, for example, features wiring for such things as in-flight entertainment systems. A measurement the electric power generating capacity of 1st, 2nd, and current generation jets of comparable passenger-carrying capability would show a steady increase in aircraft electric power generating capability.Protection matters, Fire detection and suppression is inadequate. Enough electric power for a medium-size office building is concentrated in the electrical and equipment (E&E) bay located under the cockpit. The E&E bay has neither fire detection nor suppression. A runaway electrical fire downed Swissair Flight 111 in Sept. 1998; a month later a Delta Airlines L-1011 experienced an electrical fire behind the flight engineer’s panel, in a location where hand extinguishers were virtually useless. With about 100 miles remaining on a flight from Hawaii to California, the crew effected an emergency landing at San Francisco. This airplane could easily have been “another Swissair,” involving an airplane of U.S. registry.Age matters. Wiring is not immortal; it ages in service. Over time, the insulation can break, exposing conductor. Exposed conductors create a fertile field for ticking faults, spurious signals and, worse, full-blown electrical arcing. Any carrier with a significant population of its aircraft having 10 or more years’ service has an aging wire problem.Location matters. Wiring is subject to changes in temperature, moisture, vibration and chafing. In some areas of the aircraft, such as in the leading/trailing edges of the wing, the landing gear wheel wells, etc., the physical stresses are higher than in more protected areas (e.g., the cabin)Installation matters. Sharp bend radii, improperly supported wire bundles, mixed insulation types in the same bundle, routing high and low power circuits in the same bundle, to name a few sins, can exacerbate the known environmental effects. Arcing in a vertically oriented bundle is more hazardous than in one running horizontally. One might suggest the large wire bundles indicate an electrical wiring philosophy based on ease of installation during manufacture, not necessarily ease of maintenance for the operator.Type matters. Certain types of wire insulation, notably aromatic polyimide, have known properties of hardness, vulnerability to cracking, and the tendency to arc spectacularly. Indeed, the carbonized insulation under arcing conditions itself becomes a conductor, spreading the danger literally with the speed of lightning.Maintenance matters. Wiring can be damaged during maintenance of other aircraft components, largely because technicians are unaware of the potential hazard created by stepping on a bundle or yanking it in such a way that brittle insulation is damaged further. Another major problem is unrelated maintenance damaging the wire. For example, drilling into aluminum structure creates shavings, called swarf. If those bits of swarf fall onto wire, they can eventually cut or wear through insulation, giving rise to intermittent (or worse) electrical failures. To be sure, it takes time to put a cover over the wires while drilling, then folding up the covers and removing them from the airplane. But it may take less time than involved in finding swarf-related faults in the wiring weeks or months later.The military’s experience matters. Some industry officials believe the U.S. military’s experience is not relevant jets are exposed to higher maneuvering loads and to harsher operating environments. On the other hand, the military’s experience with a jet designed with a 6,000 hour service life may be highly relevant to an airliner with a design service goal of 60,000 hours. The airliner is exposed to lower extremes over an order of magnitude longer period of time. In this respect, the military’s experience may be considered a form of accelerated aging from which the commercial side of the aerospace industry could learn much.Inspection types matter. Visual inspections are not enough. Eyeballing the wiring in a jet may uncover only a third or less of the insulation breaches exposing conductor. Yet technologies can be mobilized to quantify the state of wiring in an airplane, and to assess the amount of life remaining. These techniques can be used to target a cost-effective program of selective wire replacement.A Broad ViewThe airline industry may be at a place with respect to wiring that it was a decade ago with aging structure. The physical structure of an airliner now is built to be damage tolerant. That is, the airplane is designed such that structural components feature sufficient residual strength to withstand the weakening effects of fatigue cracking, say; from a tiny flaw that may lurk unseen somewhere in the structure from the day it leaves the factory. Recall that when damage tolerant structure was being debated, the manufactures worried the added weight would drive them out of the airplane building business and into the manufacture of railroad rolling stock.As it turned out, damage tolerant design added about 1,000 lbs. (454 kg) to the weight of a DC-10 while greatly extending its service life. Damage tolerant structure is now considered the norm.Wiring however, is not damage tolerant. As a weight saving measure, the thickness of the insulation has been shaved to minimum. In some wires, the insulation is about the thickness of four human hairs laid side-by-side. Or, as one expert observed, the industry is about “four hairs from electrocution.” Indeed, many of the problems of chafing, etc. elucidated above would not be the threats they are if the insulation was about four times thicker. Admittedly, this is kind of a brute-force approach, but by one estimate thickening the insulation would add about 200 pounds (91 kg) to the weight of wiring in a widebody jet.That’s about the equivalent weight of magazines and catalogues in the seat-back pockets. Perhaps a philosophy of damage tolerant electrical system design is only a matter of time—and certainly it is within the current state-of-the-art.Other potential improvements are numerous. Heavier insulation could be made an available option during manufacture. High power and low power wires could be better segregated. Connectors could be better separated, too and not all bunched together so that an electrical arc can jump from one to another. Longer- life circuit breakers could be installed as original equipment, saving considerable money over the long haul.Fire detection and suppression in the electronics and equipment (E&E) bay, and other unprotected areas where electrical systems are concentrated, could be insisted upon. The reduced maintenance costs, higher dispatch reliability, and fewer precautionary landings would, over the life of the airplane, more than offset the purchase cost of such features and protections.Brief Timeline on Flight 800 and the Fuel Tank Inerting FAA initiatives as a direct resultJuly 17, 1996 At about 2031 EDT, TWA flight 800, a Boeing 747-13, broke up in flight with a loss of life of all 230 passengers and crew. The crash debris fell into the Atlantic Ocean south of East Moriches, Long Island, NY. The accident investigation was one of the longest and most expensive in the NTSB's history. A substantial fraction of the aircraft was recovered and reconstructed, and numerous studies were carried in the effort to determine the probable cause. The Explosion Dynamics Laboratory at Caltech was asked by the NTSB to participate in the investigation and lead a group of researchers to examine the issues of fuel flammability, ignition, and flame propagation. EDL staff were involved from the fall of 1996 until the final hearing in August 2000.December 13, 1996 Safety Recommendation Letter A-96-174 published.TO THE FEDERAL AVIATION ADMINISTRATION: Require the development of and implementation of design or operational changes that will preclude the operation of transport-category airplanes with explosive fuel-air mixtures in the fuel tank: (a) significant consideration should be given to the development of airplane design modifications, such as nitrogen-inerting systems & the addition of insulation between heat-generating equipment & fuel tanks. Appropriate modifications should apply to newly certificated airplanes &, where feasible to existing airplanes.May 20, 1997 Added fuel tank flammability reduction to the Ten-Mosted Wanted List of Transportation Safety Improvements:"Reduce the potential for explosive fuel-air mixtures in fuel tanks of transport category aircraft. The NTSB has urged the FAA to make operational changes. They include refueling the center wing tank from cooler ground fuel tanks before flight, monitoring temperatures and maintaining a proper minimum amount of fuel in the tanks."December 8-9, 1997 NTSB Investigative hearing.August 22 and 23, 2000 Final hearing by NTSB and announcement of probable cause.2002 Fuel-tank inerting added to Ten-Most Wanted List (removed in 2008)Feb 17, 2004 The FAA announced that it is considering issuing a Notice of Proposed Rulemaking (NPR) requiring a fuel tank inerting system to be installed on existing aircraft with center wing tank flammability hazards.Feb 15, 2005 The FAA issued the special conditions for the certification of the flammability reduction means (FRM) or fuel tank inerting system proposed by Boeing for the 747 family of aircraft. This system will use hollow fiber membranes to generate "nitrogen enhanced air" to fill the vapor space of the center fuel tank in order to reduce the O2 concentration below 12% for a sufficient duration of the flight that the center fuel is not flammable for greater than 3% of the fleet operational time.Nov 15, 2005 The FAA has finally put on public display the Notice of Proposed Rulemaking on fuel tank inerting.November 23, 2005 The (NPRM) was published in the Federal register.March 21, 2006 The FAA has extended the deadline for comment on the NPRM to May 8, 2006.July 12, 2006 From the NTSB website: "The investigation into a wing fuel tank explosion on a Transmile Airlines B-727 airplane in Bangalore, India, on May 4, 2006, is ongoing. The evidence indicates that an explosion in the left wing fuel tank destroyed the structural integrity of the wing."July 21, 2008 The FAA has issued the the final rule: "Reduction of Fuel Tank Flammability in Transport Aircraft." The rule requires retrofitting of certain aircraft with heated center wing tanks and use of flammability reduction means (inerting systems) or ignition mitigation means (foam) on future aircraft to meet a target flammability exposure of 3% fleet average flammability and specific risk of 3% during ground operation and climb out on warm day, above 80 F. The present value of the total compliance cost is estimated by the FAA to be 1 billion USD. Boeing has developed and placed into production inerting systems based on hollow fiber membrane technology for the 747 and 737 typeOctober 16, 2008 Safety Recommendation A-96-174 closed as an acceptable action.More detailsFAA Lessons LearnedNASA Analysis https://sma.nasa.gov/docs/default-source/safety-messages/safetymessage-2011-01-09-twa800inflightbreakup.pdf?sfvrsn=4http://pe.org.pl/articles/2013/7/5.pdfhttps://www.faa.gov/documentLibrary/media/Advisory_Circular/AC%2025_981-1.pdfFootnotes[1] https://www.faa.gov/training_testing/training/air_training_program/job_aids/media/ewis_job-aid_2.0_printable.pdf
In HVAC, how can an energy recovery wheel be more than "50%" efficient?
The use of porous materials in Enthalpy Wheels allows energy transfer, both heat (sensible) energy and moisture (latent) energy, without any wastage of expensive conditioned indoor air. To increase the latent transfer, the matrix core material is coated with a desiccant, such as Silica Gel or other molecular sieves. This reduces the cost of removing moisture, which represents 0% to 50% of the cost of conditioning air, leading to the savings of a similar amount of energy.Many enthalpy wheel manufacturers use 3Å molecular sieve desiccant coating, which limits the risk of desiccant cross-contamination, restricting the transfer of exhaust air pollutants and water vapor to the fresh air stream, increasing the wheel’s efficiency. The wheel also utilizes a four-pass labyrinth seal to ensure optimum performance under high pressure conditions.The coated Enthalpy Wheel is rotated between exhaust air and the incoming fresh air, while being exposed to both heat and moisture. The wheel switches between two modes, heating and cooling. In the heating mode, heat and humidity pre-condition the incoming dry, cold air, whereas the incoming air is pre-cooled and dehumidified in the cooling mode.Most energy recovery devices transfer heat (sensible) energy only. An Enthalpy Wheel allows both heat (sensible) energy and moisture (latent) energy to be exchanged. Enthalpy Wheels are usually made of porous materials to increase surface area, which aids in energy transfer.If you are looking for reliable, expert HVAC services in New Jersey, visit: https://hvac4nj.com/services/
Why is a recycling service so expensive?
Kai, This question brings into the focus the economics and the necessity of recycling what would otherwise be accumulating waste generated by human activity.I’m going to do something a little different, if for no other reason than to write something that might be interesting and even entertaining for some. I’m going to talk not only about the recycling of conventional waste but also something that is often overlooked, yet it is substantial, and that is the recycling of human excreta.Recycling SewageSo let’s discuss the recycling of sewage.I once entered a competition and put to a local council a proposal to recycle sewage that is presently treated by Sydney Water. It was unsuccessful. In fact it lost to another proposal that involved recycling concrete waste. I think mine was far more interesting but then I’m biased.To construct my proposal, I collaborated with:Sydney WaterSchool of Microbiology, UNSWMurray Cod Hatcheries – Wagga WaggaSchool of Microbiology, UNSWSchool of Mechanical and Manufacturing EngineeringCSIRO Division of EntomologyCSIRO Division of Water Resources and Land SciencesThe idea involved using a mixture of sewage and vegetable matter to feed a vermiculture operation. The worms from this would then be processed and fed to an aquaculture operation with the worm castings being dried, bagged and sold to farmers as fertiliser. Alternatively, if the biomass in which the worms were grown still had usable product left in it after the worms had been harvested, it could be washed with the washings becoming a liquid fertiliser and the remaining biomass being further processed for feeding to fish and later disposal as a fertiliser as well.There are a number of challenges concerning the processing of sewage with the end objective being to feed an aquaculture operation, some of which are:Effective treatment of feedstock to eliminate heavy metal and micro-biological contamination.Secondary processing of biomass to produce useful feedstock for fish, eg, production of yeasts or algae from biomass which can then be mixed with the worms to form a balanced nutritious fishfood.Automation of the vermiculture operation.Automation of the aquaculture operation.Automation of the fish processing.Selection of the correct species of fish to make a commercially viable operation.Minimisation of energy costs and the cost of capital works to sustain this operation.Inquiries and ResearchSchool of Microbiology - University of New South Wales. I approached and successfully enlisted the support of the School of Microbiology at the University of New South Wales, as represented by Professor Nicholas Ashbolt. The school had carried out PhD research into ways for breaking down sewage biomass. The School saw some potential in this project, not only because of the benefit it could do for society, but also because it could give rise further interesting PhD projects for the School’s students.Sydney Water. Accompanied by Professor Ashbolt, I had talks with Mr Peter Hope, Residuals Manager, of Sydney Water. The outcome of these talks was that:A new tertiary treatment works being built at Cronulla will provide around 80,000 tons of sewage cake per annum. This plant would also produce 250,000 tons of sterilised fresh water per annum which could be used for this operation.On the basis of what was known about the project, Sydney Water indicated they would support this enterprise provided there was no additional cost incurred by Sydney Water and preferably that there were cost savings in the present treatment and disposal of sewage.Waste management facilities on the Southern region of Sydney were able to provide a similar quantity of vegetable waste.CSIRO. The Division of Land Sciences, CSIRO, in Adelaide, at that time, was studying the beneficial effect of worms on agriculture. The person heading this study was Dr John Buckerfield. In discussions with him the following information was obtained:Worm castings have been found to have a significant beneficial effect on crops of all descriptions. Chemical analysis indicates castings do not contain a great quantity of conventional nutrient (ie, phosphate and nitrate) from a chemical point of view. It would appear that their beneficial effect derives from the bacteria they contain and which worms promote. Washings of worm castings appear to have a similar beneficial effect but obviously do not have the added benefit of worm casting in keeping moisture in the soil.The CSIRO had done tests spreading worm castings on vineyards and cotton plantations. In the case of the vineyards a 35 to 50% improvement in crop yield was experienced. The tests with the cotton plantations had also been carried out and the results showed that the trees had significantly more fruit and blossoms on them. The optimum spreading rate for worm castings was found to be 7 tonnes per hectare. One of the cotton plantations under test had an area of 52,000 hectares. It was evident from this that the demand for this worm casting would easily outweigh the capacity of proposed production facility to supply. There was no danger of being left with unused worm castings.One of the objectives of the CSIRO’s research at that time was to determine the commercial value of worm castings.Earthworm Recycling of Australia. ERA was a company in Melbourne specialising in breeding and selling earthworms. My research revealed that:About 50 tonne of organic matter is required to create 1 tonne of worms.8.6 kgs of worms will occupy 0.243 cu m of biomass.1 kg of worms consumes about 1 kg of material per day.Worms grow rapidly in size during their first 10 to 20 days of life. After that their consumption of material and their growth drops dramatically.Murray Cod Hatcheries. Murray Cod Hatcheries assisted me with my research into aquaculture. Fresh water fish provide a yield of between 0.7 and 1.7, that is, 0.7 tonnes of food can, with some species, produce 1 tonne of fish.Promotion of this Concept is not DifficultThis project has a number of laudable aims which will make it acceptable to government and constitute good public relations which, in turn, means a good probability of general acceptance by the wider community. These are:To provide employment, not only for young engineers and technicians, but also for the general community.To provide an opportunity for PhD research by students of the University of New South Wales.To develop environmentally friendly and economical ways of disposing of organic waste products.To establish a potentially lucrative industry which will reduce the stress presently being put upon the ocean ecology through the over-exploitation of fish stocks.Generate an export income from the application of high technology which could assist Australia’s balance of payments.Export of expertise to other countries in need of this technology; especially as part of Australia’s foreign aid programme.Some DeductionsPotential Output of the Farm. The fishfarm has the potential to produce the following:Fish Produce. On the basis of what is presently known, 160,000 tonnes of biomass should produce 3,200 tonnes of worms. If these are mixed with some form of cereal to provide a balanced fishfood, the resultant feedstock should be of the order of 7,000 tonnes. Working on a yield of 1.5:1 this should produce 4,600 tonnes of fish per annum. If the average wholesale price of fish is US$7.00 per kilogram then this equates to around US$32.0 million per year of revenue.Fertiliser. It is not expected that the worms will substantially decrease the size of the biomass. As a consequence, it is expected that there will be around 160,000 tonnes of fertiliser produced per year unless some of the biomass can be reprocessed such it is consumed as fishfodder. The fish excreta will also be useful as a fertiliser. It may be possible to mix the spent biomass with waste water to form a liquid fertiliser which could be sprayed on farmland. This potentially will produce around 400,000 tonnes of liquid fertiliser per annum. The CSIRO has confirmed and quantified the usefulness and value of this product as fertiliser. If one assumes it is sold for US$20 per tonne, the value of this product could be as much as US$8 million per annum.Facility Size. The size of the facility can be calculated by taking into account the amount of biomass that has to be held at any one time and the number of fish which will be held in the farm to produce an output of 12.6 tonnes of fish per day. For example, there will be a need to hold around 30 days of biomass at any one time. This amounts to 13,150 tonnes or about 13,150 cubic metres of waste. Spread to a depth of 0.5 metres this would occupy a space of about 2.6 hectares. Once offices, processing plant and fish tanks are taken into account, around 10 hectares should be needed to carry out this activity.Commercial Viability. This project appeared to be commercially attractive because:Cities are already burdened with the cost of treating sewage from which no income is generated. This project would treat sewage to the highest possible ecological standard whilst, at the same time, generating a substantial income and ameliorating other environmental concerns such as the depletion of natural fishstocks in the oceans.The biomass which will produce the worms for feedstock could be provided at very low cost and possibly free of charge.250,000 tonnes of fresh water from the sewage works could be provided free of charge as it is produced, with or without the this project, as a part of the necessary process of treating sewage.The land upon which the facility could be built should be cheap and may be obtainable by way of a government grant.The demand for fish for human consumption is increasing. There will always be a ready market for this produce.The waste-load created by the fish is high in phosphate and can be sold as fertiliser as can the worm waste.Conventional Treatment of Household Waste for the Purposes of RecyclingNow, onto the more mundane.There are now a number of facilities operating around the world that treat what is called a “multi-waste” stream and output electricity and useful products that can be economically recycled.This involves no sortation of household waste by householders and, being so, does not require multiple bins at domiciles, separate collection systems and it does not impose on householders the chore of separating their waste (which in community housing projects especially, they never do properly!). The elimination of sortation of waste saves the community and the municipality a great deal of time and money.In a multi-waste stream system, sortation is performed using automated systems such as:magnetic removal of ferrous metals,induction removal of diamagnetic metals,robotised visual recognition systems,gravimetric removal of glass and plastics, andhydrodynamic separation of sand and other heavy materials.Once economical separation has occurred, the remaining waste is dewatered and forced into a tube lined with manganese dioxide; the latter acting as a catalyst for oxidisation. The tube is heated to around 600C and during this process all carboniferous waste is reduced to CO and H2. This gas is then cooled with the heat energy being recycled into the process and the gas is used to drive engines which drive generators creating base-load electricity. The end product is a carbon and ash waste which can be used in tyre and cement manufacture respectively.These systems of waste treatment have been found to be economical and are significantly ecologically superior to dumping waste in landfill where there is always the risk of contamination of the water table and the gradual emission of toxic gases, such as dioxins, from the restored land which is often used for recreational facilities or housing.Final CommentIn this paper, I have covered two of the major areas of waste associated with humans and how this waste might be economically recycled.Humans, through the use of their intelligence, have grown in number far beyond what the natural environment would have allowed without the intervention of medicine, industrialisation, transportation, electricity, sewage, water treatment and reticulation, the rule of law and building construction.It is very important for the health of this planet and the continued existence of the human race that this same intelligence be directed to devising ways by which the waste streams may be closed so that there is, in the end, nil accumulating waste. If this is not done, then eventually the biosphere will not be able to cope and human life will be seriously impacted.
- Home >
- Catalog >
- Business >
- Letter Template >
- Authorization Letter Sample >
- Sample Financial Authorization Letter >
- simple authorization letter >
- Save In The Heating Expenses, Reduce Moisture Risks