How to Edit The Fire Department Inventory Forms easily Online
Start on editing, signing and sharing your Fire Department Inventory Forms online with the help of these easy steps:
- click the Get Form or Get Form Now button on the current page to make access to the PDF editor.
- hold on a second before the Fire Department Inventory Forms is loaded
- Use the tools in the top toolbar to edit the file, and the edited content will be saved automatically
- Download your modified file.
A top-rated Tool to Edit and Sign the Fire Department Inventory Forms
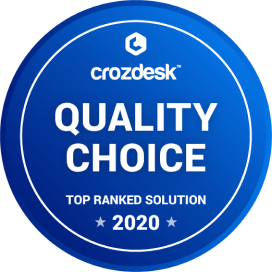
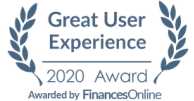
A clear direction on editing Fire Department Inventory Forms Online
It has become very simple presently to edit your PDF files online, and CocoDoc is the best free PDF editor for you to make a series of changes to your file and save it. Follow our simple tutorial to start!
- Click the Get Form or Get Form Now button on the current page to start modifying your PDF
- Add, modify or erase your content using the editing tools on the toolbar on the top.
- Affter editing your content, add the date and draw a signature to complete it.
- Go over it agian your form before you click to download it
How to add a signature on your Fire Department Inventory Forms
Though most people are in the habit of signing paper documents by writing, electronic signatures are becoming more regular, follow these steps to sign documents online for free!
- Click the Get Form or Get Form Now button to begin editing on Fire Department Inventory Forms in CocoDoc PDF editor.
- Click on the Sign icon in the tool menu on the top
- A box will pop up, click Add new signature button and you'll have three options—Type, Draw, and Upload. Once you're done, click the Save button.
- Move and settle the signature inside your PDF file
How to add a textbox on your Fire Department Inventory Forms
If you have the need to add a text box on your PDF for customizing your special content, do the following steps to accomplish it.
- Open the PDF file in CocoDoc PDF editor.
- Click Text Box on the top toolbar and move your mouse to carry it wherever you want to put it.
- Fill in the content you need to insert. After you’ve typed in the text, you can use the text editing tools to resize, color or bold the text.
- When you're done, click OK to save it. If you’re not settle for the text, click on the trash can icon to delete it and do over again.
An easy guide to Edit Your Fire Department Inventory Forms on G Suite
If you are seeking a solution for PDF editing on G suite, CocoDoc PDF editor is a suggested tool that can be used directly from Google Drive to create or edit files.
- Find CocoDoc PDF editor and establish the add-on for google drive.
- Right-click on a chosen file in your Google Drive and click Open With.
- Select CocoDoc PDF on the popup list to open your file with and allow access to your google account for CocoDoc.
- Make changes to PDF files, adding text, images, editing existing text, annotate in highlight, fullly polish the texts in CocoDoc PDF editor before saving and downloading it.
PDF Editor FAQ
What is something a truck driver has done that traumatized you.?
Caution: This is a sad tale.I run a large used operation for a big dealership with about a dozen locations. We sell a ton of trucks. I employ old retired drivers to move these trucks around from location to location. These are great older guys that are multiple million mile drivers. They know their stuff. Most everything is moved "bobtail". No trailers are being pulled. It's just inventory moving from location to location. I sent 3 drivers to the eastern part of the state to retrieve trucks. It was bitter cold. The trucks were in an icy lot and in some cases the brake drums were frozen. So the 3 drivers all worked together to free the trucks up that needed to be transported. One walked off to warm up the 3rd truck. After a few minutes the other drivers heard the big diesel wind up to a high RPM and they couldn't observe their fellow driver in the cab. These guys are in their late 70's one was 80. When they got to the truck they found their fellow driver slumped over, turning blue. It was beyond their ability to get him out of the truck. By the time the fire department arrived my driver was probably brain dead but they were able to revive his heartbeat. I got the call and drove 3 hours to the hospital. That was the worst. I had to call his wife and son. I was very close to this man as he is under my direct supervision and we had become friends. We had taken several motorcycle trips together. To see him hooked up on life support was horrible. To be there with his wife and son while the doctor explained that he couldn't function without a respirator and they saw no brain activity was worse. That he was going to retire full time in less than 3 months and he and his wife were going to start traveling was sobering.I know I am off subject and taking a different angle with this question. But it was the worst thing ever done to me by a truck driver. Anything else is peanuts. That he had his massive stroke while in the lot was a blessing for if he had been on the highway someone else might have been hurt.I have a strong affinity for the professional driver. They pay my bills and feed my family. That every item you use is delivered by truck should not go unnoticed.God bless you old friend. I know you'll be at the reception when it becomes my day.
Do firemen just sit around at work waiting for a fire to happen? Do they still get paid if there's no fires one day? What do they do all day long in this instance?
YOU CAUGHT US! Our secret is out.I can give you a full break down of a typical day or just summarize.We start shift promptly at 0730. That means in uniform, gear on the truck (or at least out by the truck) by 0730. Every day the truck and equipment get checked. That means under the hood and everything behind all 7 roll up doors. IF it can be started, it is. All safety equipment is checked. That’s about 1 hour for the front line trucks. If we have spare trucks at the station they must be checked daily too.My department is 4 stations with 5 companies (suppression apparatus and rescue/ambulance) and we run about 14000 calls per year. That’s 8–10 calls per day per crew. The average EMS call (from initial tones to ambulance in quarters) is about 1 hour. Fires, accidents, etc can be longer.We also are required 2 hours (minimum) of training each shift. If we are doing our annual burn trainings, that can be 3–4 hours.Yes we eat meals, but there are no “meal breaks”. We eat as close to normal time as we can, but we are always on the clock and, from experience, most good foods don’t reheat well 2–3 times.We are also “strongly suggested” some type of physical activity per shift (work out). But due to Covid, only 1 in the gym at a time makes it a challenge for 5 to 6 different people to get in there.First of the month is a complete drug inventory and equipment inventory on each and every apparatus. That can take several hours and is spread over the first 3 days. We sweep and mop daily, Mondays are “deep cleans” with mattress covers, shower curtains, etc cleaned.Wednesday is airpack checklist day (in addition to daily) as well as inventory of EMS supply closet. Friday is detail truck check. Not just check fluids, but tilt cab to check hoses and belts, tire pressures, and bleed air tanks. This adds about an hour to the regular truck check. Fridays we scrub the garage floors and doors. Decobweb the walls too.Then, according to SOG 200.11.09“Weekly and Monthly Schedule 200.11.09Monday Schedule:.01 Complete daily schedule.02 Complete assigned training and any specialized training or projects.03 Perform preplans, area familiarization, check FD connection locations, visit new construction sites, perform driver training, flow hydrants, or test hose.04 Weekly clean-up.01 Kitchen/Dining Area:.01 Clean & dust the top of all appliances and cabinets.02 Clean (shift) refrigerator inside and out, throw away all spoiled/out of date food.03 Clean stove/oven thoroughly inside and out.04 Clean & wipe down all the cabinets, countertops, sinks and small appliances.05 Clean & wipe down the table and chairs.02 Offices, dayroom, reception/lobby, conference areas, and training/report rooms:.01 Dust off the tops of all furniture and cabinets.02 Clean & wipe down (fronts/sides) all furniture and cabinets.03 Cloth recliners/chairs can be vacuumed/brushed off and leather recliners/chairs can be wiped down with a wet cloth and mild detergent if needed.04 Clean & wipe down table and chairs.03 Bunkroom/Sleeping Areas.01 Dust off the tops and sides of all furniture, cabinets, and ¾ walls.02 Clean & wipe down (fronts/sides) all furniture and cabinets.03 Clean & vacuum under beds.04 Wash & dry bedspreads and mattress covers.04 Restroom/Shower Areas.01 Clean & wipe down all fixtures, mirrors and cabinets.02 Wash all shower curtains.05 Exercise Room.01 Clean & wipe down all gym equipment, drinking fountains and the mirrors.02 Ensure all equipment has been stored in its proper place. Routine Daily Operations.06 Logistics side of Station 11.01 Empty the trash can in EMS Lab.02 Clean & wipe down all cabinets, fixtures, and furnishing in EMS Lab.03 Sweep and mop tile area in the hallway, break-room, and EMS Lab.04 Logistics personnel will clean and vacuum their offices, empty their trash cans, keep the break-room and bathroom cleaned and wiped down.07 Miscellaneous – Throughout the station.01 Clean & wipe down/off all doors and hardware (handles/knobs).02 Clean & wipe down all TVs.03 Clean & dust off all ceiling fans.04 Clean & wipe off all hanging items (pictures, maps, etc.).05 Janitorial closet to be cleaned & all fixtures wiped down.05 Third Monday of each Month.01 Check station inventory.01 Inventory Station Training Library.02 Stove Hood:.01 All stove hoods will be cleaned from top to bottom including the underside; the aluminum filter screen needs to be removed, cleaned and replaced back in the hood.02 Station 11 hood system will need to be cleaned from top to bottom including the underside; the filter baffles need to be removed, cleaned and replaced back in the hood.06 Third Monday of each quarter (January, April, July, October).01 Kitchen/Dining Area:.01 All refrigerators and stove(s) – the floors under will be mopped, the walls behind will be cleaned and wiped down.02 All refrigerator cooling coils and motor area will be vacuumed or brushed to remove dust/cobwebs.02 Clean all station windows inside and out except for the bay doors.01 Mini blinds should either be vacuumed or dusted.02 When cleaning the outside of the windows you may need to wash off the heavy dirt first and for reach purposes you may want to use a flat-mopI could go on and on with each day, but you get the point. We are the only department in the city that does its own cleaning. All of city hall has a third party cleaning service.Everything except running calls is done within the first 12 hours. Other than occasional “night training”, after business hours, down time is ours. There is no “bed time” prior to 1730 (though with social distancing being in bunks has been a bit relaxed). If the sun is up, you are up.This doesn’t include the paperwork etc, that must be done for every run as well as the officer’s daily reports and paperwork.
Why did the wings fall off of the C-130 Tanker plane while it was dropping water on a California forest fire?
The 2002 Walker, California crash of C-130A, N130HP, Tanker 130 has often been attributed to structural failure (the simplest ‘correct’ answer), a design flaw (partially correct) and human factors (incorrect when referring to this crew). Like most accidents simple answers only are sufficient for the simple.This C-130’s history is an important part of the story. Specifically, it was one of the original 1957 production models and among only a few still considered airworthy in 2002. Tail 56–0538, the original USAF designation, had seen service in Europe, Southeast Asia and the Americas. Like all USAF aircraft it possessed a detailed flight and maintenance history in archive that accompanied the aircraft throughout its service life. Except… in the late 1960’s the aircraft’s library showed a break in records keeping of over four years. 56–0538 had been released from the USAF to a program that “partnered” with “industry”. The particular company for this partnering, Southern Air Transport. Southern Air Transport was a front company for the CIA.This aircraft spent four years without any documented details on its maintenance history. There is nothing available as to the use, environment and employment of the airframe. It is unknown if the aircraft experienced overloading, over-g or any other potential airframe compromising damage or use.Once returned to the USAF the plane was placed in the USAFR inventories and used by a number of squadrons. Maintenance was performed and documented but this was during the “hollow force” era and attention to detail was not as much of a priority for understaffed and underfunded units. Deferments of depot level activity and other heavy work occurred. Add to this the arrival of the C-130H models, the presence of C-130E models, and the attention to the C-130A simply wasn’t there. This was most obvious in the USAF’s decision to not replace the center wing box of the A-models when Lockheed advised it as a recommended upgrade (late 70’s, early 80’s). C-130E and H1 were modded but not the A-models. Most of the A-models were turned over to the boneyard by 1988.56–0538 was sold as surplus to other USG entities in 1986. Renamed N130HP it was taken on by the General Service Administration and released to the the Department of the Interior after modding for fire suppression. It was successfully used for years. Crews performed many, many water drops using established procedure without complaint.That all changed on 17 June, 2002. Tanker 130 had completed the water release and was pulling up when the wing-to-fuselage connection (center wing box) failed. The NTSB determined structural fatigue from decades of use caused a fatal propagation of cracks associated with rivet holes. These cracks compromised the stringers (think ribs of a reinforced box) and resulted in catastrophic failure at a g-load well within designed parameters. The crew was found to have had no part of the blame.The reason I brought up the CIA period of service is other C-130A associated with Southern Air Transport showed higher degrees of compromise than C-130A that had remained in the military. We will never know if improper use and loading by Southern Air Transport contributed to the failure.Like most tragedies some good came out of it. The DoD implemented a fleet wide examination C-130 wing boxes of all types. The inspections found multiple problems. Some similar, some only by coincidence. But the result was significant programmed maintenance changes and use restrictions until changes were accomplished.
- Home >
- Catalog >
- Business >
- Inventory Template >
- Equipment Inventory >
- Fire Department Inventory Forms