How to Edit The All Hazards Risk Assessment Template easily Online
Start on editing, signing and sharing your All Hazards Risk Assessment Template online following these easy steps:
- Push the Get Form or Get Form Now button on the current page to direct to the PDF editor.
- Wait for a moment before the All Hazards Risk Assessment Template is loaded
- Use the tools in the top toolbar to edit the file, and the change will be saved automatically
- Download your completed file.
The best-rated Tool to Edit and Sign the All Hazards Risk Assessment Template
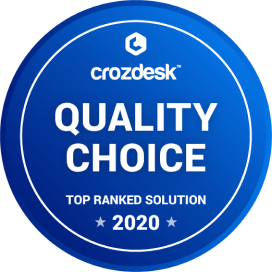
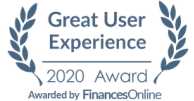
A quick direction on editing All Hazards Risk Assessment Template Online
It has become quite easy in recent times to edit your PDF files online, and CocoDoc is the best free app you have ever seen to make some editing to your file and save it. Follow our simple tutorial to start!
- Click the Get Form or Get Form Now button on the current page to start modifying your PDF
- Add, change or delete your content using the editing tools on the toolbar above.
- Affter altering your content, add the date and create a signature to finish it.
- Go over it agian your form before you click and download it
How to add a signature on your All Hazards Risk Assessment Template
Though most people are adapted to signing paper documents with a pen, electronic signatures are becoming more usual, follow these steps to add an online signature!
- Click the Get Form or Get Form Now button to begin editing on All Hazards Risk Assessment Template in CocoDoc PDF editor.
- Click on the Sign tool in the tools pane on the top
- A window will pop up, click Add new signature button and you'll be given three choices—Type, Draw, and Upload. Once you're done, click the Save button.
- Drag, resize and settle the signature inside your PDF file
How to add a textbox on your All Hazards Risk Assessment Template
If you have the need to add a text box on your PDF for customizing your special content, do the following steps to carry it throuth.
- Open the PDF file in CocoDoc PDF editor.
- Click Text Box on the top toolbar and move your mouse to position it wherever you want to put it.
- Write in the text you need to insert. After you’ve put in the text, you can select it and click on the text editing tools to resize, color or bold the text.
- When you're done, click OK to save it. If you’re not happy with the text, click on the trash can icon to delete it and do over again.
A quick guide to Edit Your All Hazards Risk Assessment Template on G Suite
If you are looking about for a solution for PDF editing on G suite, CocoDoc PDF editor is a commendable tool that can be used directly from Google Drive to create or edit files.
- Find CocoDoc PDF editor and establish the add-on for google drive.
- Right-click on a PDF document in your Google Drive and click Open With.
- Select CocoDoc PDF on the popup list to open your file with and allow access to your google account for CocoDoc.
- Modify PDF documents, adding text, images, editing existing text, highlight important part, erase, or blackout texts in CocoDoc PDF editor before saving and downloading it.
PDF Editor FAQ
How do you do investment risk assessment?
How to do Risk Assessment for Investments?In this case, it’s all about managing the chances you will not get a Return on Investment, or not within the estimated time needed. A good way to assess risks of an investment, is by making a Risk Assessment Matrix.This way, you are already thinking about risks and measures to control them. A general risk assessment helps you to identify and prevent issues from happening. You can easily make a Risk Assessment Matrix in Excel or Word, together with your Management Team or other stakeholders.It’s important to work with a Risk Assessment Template that meets your company or industry needs. Check out the Risk Assessment Template in order to find a better way to understand and manage risks. The following columns are important in a Risk Assessment template:Potential hazard;Who is at risk?;Existing control measures;Risk rating;Preventive measures;Responsibilities.How important is it to manage the risk?To define the importance of the risk, and the chance of happening, you can rate the risks according the RAG system. R stands for the Red color (danger), A stands for Amber color (be careful) and G stands for the Green color (low importance). stands The RAG status can be defined by making an analysis of two variables:1) Likelihood, for example different grades:Almost certain (e.g. >90% chance)Likely (e.g. between 50 and 90% chance)Moderate (e.g. betweem 1-% amd 50% chance)Unlikely (e.g. between 3% and 10% chance)Rare (e.g. < 3% chance2) Consequences:Insignificant (Minor problem easily handled by normal day to day process)Minor (Some disruption possible, e.g. Damage equal to $500K)Moderate (Significant time/resources required e.g. Damage equal to $ 1 MLN)Major(Operations severely damaged, e.g. Damage equal to $ 10 MLN)Catastrophic (Business survival is at risk damage equal to $ 25 MLN)After filling in the blanks in your Investment Risk Assessment Template and defining the impact of the risks, you are able to keep a better control over your risks and are challenged to find control measures.Source: Risk Assessment Template
How do you take action to remedy a risk or eliminate a hazard?
First you do a risk assessment and then do a hierarchy of of controls to reduce or eliminate the risk. You must factor in the costs though. There must be a viable Return of Investment or you won’t get support from management.Know that it is nearly impossible to eliminate all risks, but we can attempt to manage them. There will always be a human factor.Now then, this may be above your paygrade, but if you are a worker there are things you can do. First, if you have identified a hazard then do what you can to fix it. Wet or oily floor? Grab a mop or absorbents and clean up the area. Or barricade the effected area and notify your supervisor. If you see a risky behavior, such as misusing a ladder, stop the person and fix the problem. Use the ladder properly, get a proper ladder, or use a working platform. If that is not possible, stop work and notify your supervisor.15+ Risk Assessment TemplatesHierarchy of Controls | NIOSH | CDC
How important is the traceability matrix in the medical device industry?
Traceability matrices are critically important to an FDA submission, as well as to sane, professional project management. Traceability matrices are effectively the tool the FDA expects to be used as a checklist, showing that you followed your process to complete your product. Note: don’t mistake “matrix” for an Excel spreadsheet, however.FDA regulations are not technical regulations in the same sense as DoD or FAA technical requirements are in their respective industries. The FDA uses a set of meta-design process models which it expects to be detailed in each company’s QMS/design process procedures. The key models on the device side are:Plan/Requirement/Protocol/Data/Report. This structure is the default, a plan, prepare, execute record of development activity.Good Manufacturing/Clinical/Laboratory Practices. GMP/GLP/GCP is all about repeatable results and is the basis of the original FDA regulation of the medical device/pharma industries. You see it in the formal language of the agency, i.e. a violation or serious breach.Hazard/Risk Assessment/Mitigation/FMEA. Quality risk management focuses on identifying specific hazards, identifying the level of risk, mitigating, or redesigning where necessary, then reviewing the design implementation for hazards that went unrecognized in the initial analysis. This becomes a measure of robustness in the design - if a fault occurs that was not identified and mitigated in the design, then there is a design fault. If the fault and mitigation is identified, then you can probably say the design worked as expected, even if the situation is not desirable.Process design, IQ, OQ, PQ quality process.Mitigation, quality and manufacturing processes, process measures and data, monitoring. Quality process monitoring is a significant part of the design effort. Many faults should be identified here, before a deviceCorrective and Preventive ActionEach of those systems in a company has a role in documenting your thinking, implementation, and problems that come up. A key principle is that no one expects the development to be problem-free. Everyone should expect that problems, changes, and proof that the problem was corrected should be documented. Conversely, a clean, waterfall documentation chain with no changes or problems should be treated as a clear flag that the design history is a fraud.So for every part of product design, electrical, software, hardware, chemical, and material, there should be a characteristic record. Starting with design standards, appropriate templates, drawings, and revisions are created and stored in an appropriate repository. A snapshot of the repository should give you a complete change history with descriptions to that point in time.Every part of the design history should be a time-stamped, revision-controlled document that can be compared to past and future versions of the documentation meaningfully to produce red-lines and drawings with a demonstrable relationship to products.Traceability is the general language used to refer to maintaining documented relationships in the development process.Requirements for V&V test protocols.Requirements to implementation.Requirements to completed testing.Test failures, requirements changes, and observations to design changes.Revision to implementation or product.Effectively tying the paperwork together in the corporate documentation system. Traceability acts to tie a design history together with the physical result, evidence that a set of goals or requirements were met, and quality control history.QSIT “Quality System Inspection Technique”, the auditing approach used extensively by the FDA, uses the traceability relationships to drive an audit. Starting virtually anywhere, but often with a problem or design change, the auditor can use the traceability to drill down into the design history. In a perfect world, the auditor will find a well-described history, problem discovery, analysis, design change, testing and introduction, and monitoring in manufacturing. The traceability matrixes make that information discoverable, and everything discoverable should be complete, and consistent with your documented processes, no more or less.Internally traceability should solve a number of project management challenges. A hazard assessment and requirements drawing define the goals of the design, the traceability defines a complete set of deliverables. The completion, review and release of the elements in the traceability matrix is the only important, visible measure of progress and the only important measure of objective completion.
- Home >
- Catalog >
- Business >
- Corporate Document >
- Risk Assessment Template >
- All Hazards Risk Assessment Template