How to Edit Your Oshas New Confined Space Training For Construction Online Free of Hassle
Follow the step-by-step guide to get your Oshas New Confined Space Training For Construction edited with the smooth experience:
- Select the Get Form button on this page.
- You will enter into our PDF editor.
- Edit your file with our easy-to-use features, like adding text, inserting images, and other tools in the top toolbar.
- Hit the Download button and download your all-set document for reference in the future.
We Are Proud of Letting You Edit Oshas New Confined Space Training For Construction Seamlessly
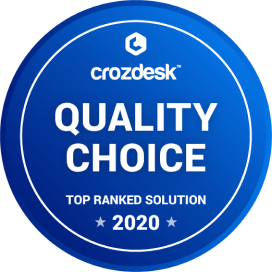
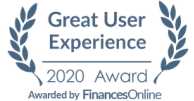
Take a Look At Our Best PDF Editor for Oshas New Confined Space Training For Construction
Get FormHow to Edit Your Oshas New Confined Space Training For Construction Online
When you edit your document, you may need to add text, put on the date, and do other editing. CocoDoc makes it very easy to edit your form fast than ever. Let's see the easy steps.
- Select the Get Form button on this page.
- You will enter into our online PDF editor webpage.
- Once you enter into our editor, click the tool icon in the top toolbar to edit your form, like highlighting and erasing.
- To add date, click the Date icon, hold and drag the generated date to the field you need to fill in.
- Change the default date by deleting the default and inserting a desired date in the box.
- Click OK to verify your added date and click the Download button when you finish editing.
How to Edit Text for Your Oshas New Confined Space Training For Construction with Adobe DC on Windows
Adobe DC on Windows is a popular tool to edit your file on a PC. This is especially useful when you have need about file edit without network. So, let'get started.
- Find and open the Adobe DC app on Windows.
- Find and click the Edit PDF tool.
- Click the Select a File button and upload a file for editing.
- Click a text box to adjust the text font, size, and other formats.
- Select File > Save or File > Save As to verify your change to Oshas New Confined Space Training For Construction.
How to Edit Your Oshas New Confined Space Training For Construction With Adobe Dc on Mac
- Find the intended file to be edited and Open it with the Adobe DC for Mac.
- Navigate to and click Edit PDF from the right position.
- Edit your form as needed by selecting the tool from the top toolbar.
- Click the Fill & Sign tool and select the Sign icon in the top toolbar to make you own signature.
- Select File > Save save all editing.
How to Edit your Oshas New Confined Space Training For Construction from G Suite with CocoDoc
Like using G Suite for your work to sign a form? You can integrate your PDF editing work in Google Drive with CocoDoc, so you can fill out your PDF with a streamlined procedure.
- Add CocoDoc for Google Drive add-on.
- In the Drive, browse through a form to be filed and right click it and select Open With.
- Select the CocoDoc PDF option, and allow your Google account to integrate into CocoDoc in the popup windows.
- Choose the PDF Editor option to begin your filling process.
- Click the tool in the top toolbar to edit your Oshas New Confined Space Training For Construction on the target field, like signing and adding text.
- Click the Download button in the case you may lost the change.
PDF Editor FAQ
What training is required for confined space?
4 New Defined Roles for Confined Space WorkersYou should also be aware that OSHA's construction standard defines four roles for employees involved in working in permit-required confined spaces.These roles are:Authorized entrants to the space.These are any employees who are authorized by the employer to enter a permit space and perform the work. Entrants will be trained in all the safe procedures for working in confined spaces, including the proper use of personal protective equipment (PPE) and how to monitor the air quality while inside a confined space. Because communication is so important between entry team members, entrants will also be trained to use communication equipment such as walkie-talkies to stay in touch with attendants.Attendants.These are employees that are designated to continuously maintain an accurate count of all authorized entrants in the permit space. An attendant's job is to stay by the entrance and monitor what goes on both inside and outside the space. Attendants must make quick, informed decisions about whether it's safe for the entry to continue, or if the work should be stopped and the entrants should be evacuated.The entry supervisor.Before any worker enters a permit space, the entry supervisor must certify that all of the required safety tests have been made, and that all needed required procedures and equipment are in place. The supervisor will also make certain that rescue services are standing by, and that the systems used to contact them are working, too. When satisfied, the supervisor will sign off on the confined space's entry permit, and the work can proceed.Entry supervisors will also monitor the progress of the work in the space, to ensure that it proceeds within the guidelines established by the Permit.Emergency and rescue personnel.These personnel are responsible to assist in evacuating the confined space in the event of an emergency. Employees who conduct rescues must be provided with proper PPE and rescue equipment, while also being trained in the proficient use of that equipment. Employers must inform each rescue team of the hazards they may confront when called to perform a rescue. You must also provide the rescue team access to all permit spaces in which rescue may be necessary so that the team can develop appropriate rescue plans and practice rescue operations.
Does the mixing element in a cement mixer ever break? If/when it does, how long until the cement hardens?
Most concrete mixing trucks just use a flat piece of metal welded in a spiral shape to the inside of the drum. By rotating the drum one way the concrete is mixed. By rotating it the other way the spiral forces the cement out of the drum.I think that in the history of concrete trucks the mechanism to turn the drum must surely have broken at least once. If that happens the concrete will harden in about an hour (sometimes more, sometimes less depends a lot on temperature and mix).There are a few things that you could do. First would be throw some retarder in the mix. This will give you more time to remedy the problem. You could also flood it with water. This will also help. However you still face the problem of mixing these things through the concrete that is in there.First thing I think most would do is head back to the yard and start shoveling the concrete out before it hardens or find someway to rotate the drum to eject the concrete. If you fail at this, the concrete will harden and need to be jack-hammered out or the drum can be replaced.Oh, and along with that jackhammering comes a lot of paperwork:The ProblemReady-mixed concrete trucks are equipped with a rotating mixing drum mounted on the truck chassis. During loading, transport, and delivery to the construction site, the mixing drum is constantly rotated to prevent concrete hardening within the drum. The cleaning of the mixing drums becomes necessary as the drum interior becomes coated with hardened concrete. Workers are required to enter the mixing drums periodically to remove the hardened concrete. This cleaning operation presents many hazards to the workers including confined space, hazardous energy, respiratory hazards, and noise, all of which require the employer to implement comprehensive programs to address each hazard.The PurposeThe purpose of this publication is to inform you of the primary hazards associated with the cleaning operation so that you and your fellow workers can protect yourselves.SECTION IPermit-Required Confined SpaceThe Occupational Safety and Health Administration (OSHA) considers ready-mixed concrete mixing drums "permit-required confined spaces". According to OSHA, a permit-required confined space (permit space) "means a confined space that has one or more of the following characteristics:1. Contains or has a potential to contain a hazardous atmosphere;2. Contains a material that has the potential for engulfing an entrant;3. Has an internal configuration such that an entrant could be trapped or asphyxiated by inwardly converging walls or by a floor which slopes downward and tapers to a smaller cross-section; or4. Contains any other recognized serious safety or health hazard."Entry into permit spaces is generally governed by a comprehensive program that includes provisions for detailed hazard evaluation, written entry permits, employee training, and emergency planning.Employers requiring workers to enter ready-mixed concrete mixers must comply with all requirements set forth in 29 CFR 1910.146 "Permit-Required Confined Spaces" even if this work is contracted to a third party.The OSHA standard requires that the employer:1. Implement measures to prevent unauthorized entry into the drum;2. Identify and evaluate the hazards of the drums before employees enter them;3. Develop and implement the procedures and practices necessary for safe permit space entry operations;4. Provide the following equipment at no cost to employees:Testing and monitoring equipment;Ventilating equipment;Communications equipment;Personal protective equipment;Lighting equipment;Barriers and shields;Equipment for safe ingress and egress (ladders);Rescue and emergency equipment; andAny other equipment necessary for safe entry into and rescue from the drum.5. Evaluate conditions inside the mixing drum when entry operations are conducted prior to entry and during entry;6. Provide at least one attendant outside the drum for the duration of the operation;7. Include in the permit program the means and procedures to enable an attendant to respond to an emergency affecting one or more of the drums being monitored without distraction from the attendant's other responsibilities as outlined in the standard;8. Designate the persons who are to have active roles (for example, authorized entrants, attendants, entry supervisors, or persons who test or monitor the atmosphere in the drum) in entry operations, identify the duties of each employee, and provide each employee with the training required;9. Develop and implement procedures for contacting rescue and emergency services.Just dialing 911 is not sufficient! The employer must have a system set up with a local emergency service with confined space rescue capabilities and training;10. Develop a system for the preparation, issuance, use, and cancellation of entry permits;11. Develop procedures to coordinate entry operations when employees of more than one employer are working simultaneously as authorized entrants in a drum. This will prevent accident and injury due to a lack of communication and coordination;12. Develop and implement procedures (such as closing off a drum and canceling the permit) necessary for concluding the entry after entry operations have been completed;13. Review entry operations when the employer has reason to believe that the measures taken under the permit space program may not protect employees;14. Review the permit space program, using the canceled permits retained within one (1) year after each entry and revise the program as necessary, to ensure that employees participating in entry operations are protected from hazards within the drum.-Entry Permit-Before entry into a drum is authorized, the employer must document the completion of measures required by the standard by preparing an entry permit.The entry permit must identify:The permit space to be entered;The purpose of the entry;The date and authorized duration of the entry permit;The authorized entrants by name;The personnel, by name, currently serving as attendants;The individual, by name, currently serving as entry supervisor, with a space for the signature or initials of the entry supervisor who originally authorized entry;The hazards of the drum to be entered;The measures used to isolate the drum and to eliminate or control hazards before entry;The acceptable entry conditions;The results of initial and periodic tests performed, accompanied by the names or initials of the testers and by an indication of when the tests were performed;The rescue and emergency services that can be summoned and the means for summoning those services (911 is not sufficient);The communication procedures used by authorized entrants and attendants to maintain contact during the entry;Equipment, such as personal protective equipment, testing equipment, communications equipment, alarm systems, and rescue equipment, to be provided for compliance with the standard;Any other information whose inclusion is necessary, given the circumstances of the particular confined space, in order to ensure employee safety; andAny additional permits, such as for hot work, which have been issued to authorize work in the drum.The employer must also provide training so that all employees whose work is regulated by the standard have the understanding, knowledge, and skills necessary for the safe performance of the duties assigned.Training must be provided to each affected employee.The training must establish employee proficiency in the duties required and shall introduce new or revised procedures.The employer must certify that the training is being conducted.SECTION IIControl of Hazardous Energy (Lockout/Tagout)The OSHA Lockout/Tagout standard (29 CFR 1910.147) covers the servicing and maintenance of equipment and machinery that could cause injury to employees if unexpectedly started or energized.Employees performing cleaning activities inside mixing drums are covered by this standard because unexpected startup of the mixer can cause serious injury or death to the worker.Employers requiring workers to enter ready-mixed concrete mixers must comply with all requirements set forth in 29 CFR 1910.147 "Control of Hazardous Energy" even if this work is contracted out.Under the Lockout/Tagout standard, employers are required to:Develop an energy control program consisting of energy control procedures, employee training, and periodic inspections to ensure that procedures are being followed;Use locks when equipment can be locked out;Ensure that new equipment or overhauled equipment can accommodate locks;Use additional means to ensure safety when tags rather than locks are used;Identify and implement specific procedures (usually in writing) for the control of hazardous energy including preparation for shutdown, equipment isolation, lockout/tagout application, release of stored energy, and verification of isolation;Institute procedures for releasing isolated equipment including machine inspection, notification and safe position of employees, and removal of the lockout/tagout device;Obtain standardized locks and tags which indicate the identity of the employee using them;Ensure the locks and tags used are of sufficient quality and durability;Require that each lockout/tagout device be removed only by the employee who applied the device;Conduct inspections of energy control procedures at least annually; andAdopt procedures to ensure safety when equipment must be tested during servicing, when outside contractors are working at the site, when a multiple lockout is needed for a crew servicing equipment, and when shifts or personnel change.The employer must also provide training so that all employees whose work is regulated by the standard have the understanding, knowledge, and skills necessary for the safe performance of the duties assigned.The following lockout/tagout procedures should be used as a guide to preparing the truck for work inside the mixer drum:Do not enter the mixer drum until all of the mixer controls are disconnected or tagged out and the truck's engine is locked out! Simply removing the key from the ignition can lock out the engine.Tell everyone who may be affected by the work (foreman, mechanics, drivers) that the truck will be out of service.Park the truck, set the brakes, and chock the wheels. Place an "Out of Service" poster on the truck.Remove the ignition key and keep it in your pocket; or disconnect the batteries; or relieve the air pressure on trucks that use an air starting system.Lock or tag all of the mixer controls on the truck and in the cab.Secure the drum to prevent it from rotating or turning.SECTION IIIRespiratory HazardsOSHA's Respiratory Protection standard (29 CFR 1910.134) requires that the employer provide respirators when necessary to protect the health of workers. The standard also requires that the employer establish and maintain a respiratory protection program. Employers requiring workers to enter concrete mixers to chip them out must comply with all requirements set forth in the Respiratory Protection standard even if this work is contracted out.The primary respiratory hazard associated with chipping operations inside mixing drums is crystalline silica. Silica is an ingredient of ready-mixed concrete that becomes airborne during jackhammering operations. Exposure to silica causes silicosis, a disabling, nonreversible and sometimes fatal lung disease caused by overexposure to respirable crystalline silica. More than one million U.S. workers are exposed to crystalline silica, and each year more than 250 die from silicosis. There is no cure for the disease, but it is 100 percent preventable if employers, workers, and health professionals work together to reduce exposures. OSHA has established a Permissible Exposure Limit (PEL) for silica. When working at concentrations above the PEL, all employees are required to wear respiratory protection if the hazard cannot be controlled through other means.Employers requiring workers to enter ready-mixed concrete mixers must comply with all requirements set forth in 29 CFR 1910.134 "Respiratory Protection".The Respiratory Protection Program must include the following provisions:Procedures for selecting respirators for use in drum cleaning;Medical evaluations of employees required to use respirators;Fit testing procedures for tight-fitting respirators;Procedures for proper use of respirators in routine and reasonably foreseeable emergency situations;Procedures and schedules for cleaning, disinfecting, storing, inspecting, repairing, discarding, and otherwise maintaining respirators;Training of employees in the respiratory hazards to which they are potentially exposed during routine and emergency situations;Training of employees in the proper use of respirators;Procedures for regularly evaluating the effectiveness of the program.In addition to establishing a Respiratory Protection Program that specifically addresses mixer drum cleaning operations, the employer must provide a medical evaluation to determine the employee's ability to wear a respirator.The employer must also provide effective training to those employees required to wear respirators. The training must be comprehensive, understandable, and recur annually, and more often if necessary.The employer must provide a variety of choices of respirators for employees so that each employee can select a respirator that fits properly and comfortably.According to the National Institute for Occupational Safety and Health (NIOSH), assuming that all atmospheric testing requirements have been satisfied, it is recommended that the workers wear any air-purifying, full face-piece respirator with a high-efficiency particulate filter, preferably a powered air-purifying respirator, for adequate respiratory protection during the drum cleaning operation .SECTION IVNoise HazardsNIOSH studies have shown that drivers involved in mixer chipping operations are at risk for noise-induced hearing loss. Chipping operations inside the concrete mixing drum using a jackhammer pneumatic chipper can reach sound levels of to 113 decibels. OSHA's Occupational Noise Exposure standard (29 CFR 1910.95) requires that an employer implement a hearing conservation program when employees are exposed to sound levels in excess of 85 decibels when averaged over an 8-hour work shift.Employers requiring workers to enter ready-mixed concrete mixers must comply with all requirements set forth in 29 CFR 1910.95 "Occupational Noise Exposure" if the workers are exposed to noise above the OSHA action level of 85 dBA.The hearing conservation program consists of noise monitoring, noise control, audiometric (hearing) tests, hearing protection, employee training and education, and record keeping.Noise monitoring - Actual noise exposure measurements must be collected so that workers will be identified for audiometric testing purposes and so that proper hearing protectors can be selected. Employers must allow employees or their representatives to observe the noise monitoring procedures.Noise control - Noise control in chipping operations is probably most easily obtained through the use of hearing protection such as earplugs or earmuffs. It is very difficult to control the noise at its source or along its path inside a mixing drum.Audiometric testing - Audiometric testing is the only way to evaluate whether or not the hearing conservation program is working. The goal of audiometric testing is to identify workers who are beginning to lose their hearing and to intervene before the hearing loss becomes worse.Hearing protection - If workers performing chipping operations are exposed to noise levels in excess of 85 dBA over an 8-hour work shift, then the employer is required to provide hearing protection. The employer must provide a variety of choices of hearing protectors for employees to choose from so that each employee can select a device that fits properly and comfortably.Employee training and education - This involves teaching workers the effects of noise, the advantages and limitations of hearing protectors, and the purpose of audiometric testing. Workers who understand the mechanism of hearing loss will be more motivated to protect themselves.Record keeping - The employer must keep each worker's exposure records and audiometric test results on file for future reference and in the eventuality of a workers compensation case.
How is technology changing in construction work?
New technologies in construction are being developed at a breakneck pace. What seemed like future tech 10, 20 years ago like connected equipment and tools, telematics, mobile apps, autonomous heavy equipment, drones, robots, augmented and virtual reality, and 3D printed buildings are here and being deployed and used on jobsites across the world.Here’s a look at some of the major areas where technology is impacting and improving the construction industry:Software & Mobile AppsToday there are software and mobile solutions to help manage every aspect of a construction project. From preconstruction to scheduling, from project management and field reporting to managing your back office, there’s a software solution out there to help streamline your processes and improve productivity. Most software solutions are cloud-based, allowing changes and updates to documents, schedules, and other management tools to be made in real time, facilitating better communication and collaboration.More and more software providers are forming strategic partnerships to allow you to seamlessly integrate your data with your other software solutions, making it easier than ever to run your business.Offsite ConstructionOffsite construction is typically used on projects with repetitive floorplans or layouts in their design such as apartment buildings, hotels, hospitals, dormitories, prisons, and schools. Offsite is performed in a controlled environment and it works similar to an auto manufacturing plant. At each station, workers have all the tools and materials to consistently perform their task, whether that be constructing a wall frame or installing electrical wiring. This assembly plant method of construction reduces waste and allows workers to be more productive.AI & Machine LearningConstruction firms are now using data to make better decisions, increase productivity, improve jobsite safety and reduce risks. With artificial intelligence (AI) and machine learning systems, firms can turn the mountains of data they have collected over the years on projects to predict future outcomes on projects and gain a competitive advantage when estimating and bidding on construction projects.AI can improve worker productivity by reducing the amount of time wasted moving about the construction site to retrieve tools, materials, and equipment to perform certain tasks. Workers are tracked throughout the day using smartphones or wearables.Sensors installed on materials and equipment track how everything else is moving about the construction site. Once enough data sets are collected, AI can analyze how workers move about and interact with the site to come up with solutions to reorganize the placement of tools and materials to make them more accessible to workers and reduce downtime.Robots and artificial intelligence (AI) are also being used to monitor jobsite progress with real-time, actionable data to improve jobsite productivity. Autonomous drones and rovers are equipped with high-definition cameras and LiDAR to photograph and scan the construction site each day with pinpoint accuracy. AI then uses those scans to compare against your BIM models, 3D drawings, construction schedule, and estimates to inspect the quality of the work performed and to determine how much progress has been made each day.Deep-learning algorithms are then used to identify and report errors in work performed. This can be anything from the excavation and site work to the mechanical, electrical and plumbing systems. The AI can recognize a building component based on its shape, size and location even if only a portion of the component is visible.By classifying and measuring quantities installed, these systems can tell you how much work was done each day, which it can then compare against your construction schedule and alerts you if your project is falling behind. The AI also detects deviations between installed components and onsite work with models so you can quickly identify errors and avoid costly rework.Safety & TrainingAs technology adoption continues to ramp up in the construction industry, one area getting a lot of attention is improving safety. Worker safety should be the number one priority of every construction company and technology solutions are making it easier to properly train and monitor workers to prevent accidents and reduce the rate of serious injuries and worker deaths.Augmented & Virtual RealitySafety training and equipment operator training are two areas where virtual reality (VR) could have a strong impact on the construction industry. With VR, workers could get exposure to environments such as confined spaces or working at height in a safe, controlled environment.VR simulators have been used for years to train soldiers, pilots, and surgeons and could be used in the same way to train workers on everything from operating cranes and excavators to doing welding and masonry work.Augmented reality (AR) is another technology that can greatly improve safety on the construction site. Whether it’s allowing for a more detailed safety plan to be developed or providing training on heavy equipment using actual equipment on real sites with augmented hazards, there are a number of ways that AR can be deployed on the jobsite.WearablesConstruction wearables are being outfitted with biometrics and environmental sensors, GPS and location trackers, Wi-Fi, voltage detectors, and other sensors to monitor workers’ movements, repetitive motions, posture, and slips and falls. Geofencing allows site or safety supervisors to establish restricted or hazardous areas that will alert workers with a combination of alarms and lights that they have entered an area that is off limits.Smart clothing, or e-textiles, that can monitor vital signs like respiration rate, skin temperature, and heart rate will also make their way to the construction site. These wearables will be able to monitor a worker’s posture, track movements, determine if they are suffering from fatigue and whether they are intoxicated or under the influence of narcotics. Keeping a watchful eye on workers can help predict an accident before it occurs.Site SensorsSite sensors that can be deployed across a construction site to monitor things like temperature, noise levels, dust particulates, and volatile organic compounds to help limit exposure to workers.The sensors are mounted throughout the construction site and can alert workers immediately when they are at risk from permissible exposure levels being reached. Data from the sensors are collected and can be analyzed to mitigate exposure levels and keep workers safe and stay compliant with OSHA regulations.Labor ShortagesDemand for workers in construction is expected to grow significantly through the next decade. The Bureau of Labor Statistics project construction employment growth to be 11% from 2016 through 2026. Younger workers, who lack the skills and experience of their veteran peers, can benefit from the technology being deployed on jobsites today.DronesDrones are being used on jobsites in a number of ways. Drones can be used to quickly conduct jobsite inspections and identify potential hazards each day. They can also be used to monitor workers throughout the day to ensure everyone is working safely. Drones are being used to take photos of as work progresses to create as-built models of jobsites to keep everyone informed of the changing work conditions each day.Drones are also being used to tackle more dangerous jobs, like bridge and building inspections. This won’t eliminate the need for workers, but it will mean that workers will need to be trained on how to use the technology to perform these tasks.RobotsCurrent robots are good at doing simple, repetitive tasks which is why we are seeing things like bricklaying robots or rebar tying robots. Once set up, these robots can work continuously to complete tasks faster than human workers without needing to take breaks or go home for a good night’s sleep. Robots don’t get tired from lifting bricks, applying mortar and setting them in place or constantly bending over to tie rebar.In both these examples, humans are still needed to perform some of the work. Both still require workers to set up the robots and get them started. For the bricklaying robot, a mason is needed to oversee the work, ensure bricks are correctly placed and clean up the mortar after they’ve been set. The rebar tying robot still needs humans to correctly place and space the rebar before it gets set in motion.Instead of replacing workers, most construction robots are there to aid and augment a worker’s performance, enabling them to be more productive.Autonomous Heavy EquipmentAutonomous heavy equipment, using similar technology for self-driving cars, is currently being used on jobsites to perform excavation, grading, and sitework. This type of technology allows operators to be completely removed from the machine, allowing companies to do the same amount of work with fewer workers.These machines use sensors, drones, and GPS to navigate the construction site and conduct sitework based on 3D models of the terrain to accurately excavate and grade the site. Augmented GPS, a combination of onsite base stations and satellites, can be used to geofence the site and allow autonomous equipment to move around the site with precision accuracy.CollaborationAs we mentioned earlier, a major issue in construction projects today is a highly fragmented industry. With workers, engineers, and equipment distributed around a jobsite, plus offsite stakeholders, including project managers and the customer, it can be hard to get everyone on the same page when a decision needs to be made.Mobile TechnologySmartphones and mobile apps have made communication and collaboration on projects easier. Instead of driving to the office for impromptu meetings, firms can use mobile technology to facilitate a meeting of the minds that lead to definitive conclusions without interrupting the day’s work.BIMBuilding Information Modeling (BIM) is a process that incorporates digital representations of buildings in 3D models to facilitate better collaboration among all stakeholders on a project. This can lead to better design and construction of buildings.Changes to the BIM model occur in real time, so any changes or updates to the model are instantly communicated to all team members when they access the model. Everyone is working with the most up-to-date information at all times. Because the schedule can be simulated, a visual representation of the construction process allows team members to plan out each phase of construction.The type of immersive visualization made possible by VR paired with BIM will lead to better collaboration and communication. Virtual reality will also lead to greater acceptance and implementation of BIM. Most virtual reality applications being developed for the AEC industry are using BIM models as the basis to create virtual environments.
- Home >
- Catalog >
- Business >
- Employee Form >
- Osha 300 Form >
- Oshas New Confined Space Training For Construction