How to Edit The Concrete Placement Work Order Construction Contract easily Online
Start on editing, signing and sharing your Concrete Placement Work Order Construction Contract online with the help of these easy steps:
- click the Get Form or Get Form Now button on the current page to make access to the PDF editor.
- hold on a second before the Concrete Placement Work Order Construction Contract is loaded
- Use the tools in the top toolbar to edit the file, and the change will be saved automatically
- Download your modified file.
A top-rated Tool to Edit and Sign the Concrete Placement Work Order Construction Contract
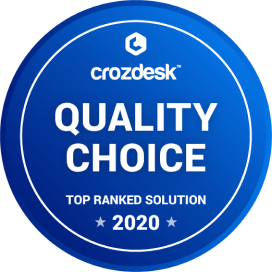
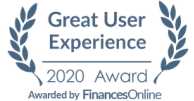
Start editing a Concrete Placement Work Order Construction Contract in a second
Get FormA clear direction on editing Concrete Placement Work Order Construction Contract Online
It has become quite easy lately to edit your PDF files online, and CocoDoc is the best online tool for you to make some changes to your file and save it. Follow our simple tutorial to start!
- Click the Get Form or Get Form Now button on the current page to start modifying your PDF
- Add, modify or erase your content using the editing tools on the tool pane above.
- Affter editing your content, add the date and draw a signature to bring it to a perfect comletion.
- Go over it agian your form before you click to download it
How to add a signature on your Concrete Placement Work Order Construction Contract
Though most people are in the habit of signing paper documents with a pen, electronic signatures are becoming more accepted, follow these steps to add a signature!
- Click the Get Form or Get Form Now button to begin editing on Concrete Placement Work Order Construction Contract in CocoDoc PDF editor.
- Click on the Sign icon in the tools pane on the top
- A box will pop up, click Add new signature button and you'll have three options—Type, Draw, and Upload. Once you're done, click the Save button.
- Move and settle the signature inside your PDF file
How to add a textbox on your Concrete Placement Work Order Construction Contract
If you have the need to add a text box on your PDF for customizing your special content, do the following steps to get it done.
- Open the PDF file in CocoDoc PDF editor.
- Click Text Box on the top toolbar and move your mouse to carry it wherever you want to put it.
- Fill in the content you need to insert. After you’ve inserted the text, you can utilize the text editing tools to resize, color or bold the text.
- When you're done, click OK to save it. If you’re not settle for the text, click on the trash can icon to delete it and do over again.
An easy guide to Edit Your Concrete Placement Work Order Construction Contract on G Suite
If you are seeking a solution for PDF editing on G suite, CocoDoc PDF editor is a commendable tool that can be used directly from Google Drive to create or edit files.
- Find CocoDoc PDF editor and establish the add-on for google drive.
- Right-click on a chosen file in your Google Drive and click Open With.
- Select CocoDoc PDF on the popup list to open your file with and allow access to your google account for CocoDoc.
- Make changes to PDF files, adding text, images, editing existing text, annotate in highlight, polish the text up in CocoDoc PDF editor before pushing the Download button.
PDF Editor FAQ
What is the difference between reinforced concrete and prestressed concrete?
Every Civil Engineer must know the answer of this question because it is considered to be the most important question for Civil Engineer.Prestressed Concrete is one of the most important part of construction and you should and you must have proper knowledge about it. Let us understand it in detail.A prestressed concrete structure is different from a conventional reinforced concrete structure due to the application of an initial load on the structure prior to its use. The initial load or prestress is applied to enable the structure to counteract the stresses arising during its service period.Prestressing of structures was introduced in late nineteenth century. The concept of prestressing existed before the applications in concrete.Two examples of prestressing before the development of prestressed concrete are providedForce-fitting of metal bands on wooden barrels The metal bands induce a state of initial hoop compression, to counteract the hoop tension caused by filling of liquid in the barrelsPre-tensioning the spokes in a bicycle wheel. The pre-tension of a spoke in a bicycle wheel is applied to such an extent that there will always be a residual tension in the spokeFor concrete, internal stresses are induced (usually, by means of tensioned steel) for the following reasons.The tensile strength of concrete is only about 8% to 14% of its compressive strength. Cracks tend to develop at early stages of loading in flexural members such as beams and slabs. To prevent such cracks, compressive force can be suitably applied in the perpendicular direction.Prestressing enhances the bending, shear and torsional capacities of the flexural members. In pipes and liquid storage tanks, the hoop tensile stresses can be effectively counteracted by circular prestressing.The following sketch explains the application of prestress.Place and stretch mild steel rods, prior to concretingRelease the tension and cut the rods after concretingFigure- Prestressing of concrete beams by mild steel rodsMild steel rods are stretched and concrete is poured around them. After hardening of concrete, the tension in the rods is released. The rods will try to regain their original length, but this is prevented by the surrounding concrete to which the steel is bonded. Thus, the concrete is now effectively in a state of pre-compression. It is capable of counteracting tensile stress, such as arising from the load shown in the following sketch.But, the early attempts of prestressing were not completely successful. It was observed that the effect of prestress reduced with time. The load resisting capacities of the members were limited. Under sustained loads, the members were found to fail. This was due to the following reason. Concrete shrinks with time. Moreover under sustained load, the strain in concrete increases with increase in time. This is known as creep strain. The reduction in length due to creep and shrinkage is also applicable to the embedded steel, resulting in significant loss in the tensile strain.Forms of Prestressing SteelWires- Prestressing wire is a single unit made of steel.Strands- Two, three or seven wires are wound to form a prestressing strand.Tendon- A group of strands or wires are wound to form a prestressing tendon.Cable- A group of tendons form a prestressing cable.Bars- A tendon can be made up of a single steel bar. The diameter of a bar is much larger than that of a wire.Nature of Concrete-Steel InterfaceBonded tendon- When there is adequate bond between the prestressing tendon and concrete, it is called a bonded tendon. Pre-tensioned and grouted post-tensioned tendons are bonded tendons.Unbonded tendon- When there is no bond between the prestressing tendon and concrete, it is called unbonded tendon. When grout is not applied after post-tensioning, the tendon is an unbonded tendon.Stages of Loading The analysis of prestressed members can be different for the different stages of loading.The stages of loading are as follows.1) Initial : It can be subdivided into two stages.a) During tensioning of steelb) At transfer of prestress to concrete.2) Intermediate : This includes the loads during transportation of the prestressed members.3) Final : It can be subdivided into two stages.a) At service, during operation.b) At ultimate, during extreme eventsAdvantages of PrestressingThe prestressing of concrete has several advantages as compared to traditional reinforced concrete (RC) without prestressing. A fully prestressed concrete member is usually subjected to compression during service life. This rectifies several deficiencies of concrete. The following text broadly mentions the advantages of a prestressed concrete member with an equivalent RC member. For each effect, the benefits are listed.Section remains uncracked under service loads.Reduction of steel corrosion Increase in durability.Full section is utilisedHigher moment of inertia (higher stiffness)Less deformations (improved serviceability).Increase in shear capacity.Suitable for use in pressure vessels, liquid retaining structures.Improved performance (resilience) under dynamic and fatigue loading.High span-to-depth ratios Larger spans possible with prestressing (bridges, buildings with large column-free spaces)Typical values of span-to-depth ratios in slabs are given below.Non-prestressed slab 28:1 Prestressed slab 45:1 For the same span, less depth compared to RC member.Reduction in self weight.More aesthetic appeal due to slender sectionsMore economical sections.Suitable for precast constructionThe advantages of precast construction are as follows.Rapid constructionBetter quality controlReduced maintenanceSuitable for repetitive constructionMultiple use of formwork.Reduction of formwork.Availability of standard shapes.Post-tensioningPrestressing systems have developed over the years and various companies have patented their products. Detailed information of the systems is given in the product catalogues and brochures published by companies. There are general guidelines of prestressing in Section 12 of IS 1343: 1980. The information given in this section is introductory in nature, with emphasis on the basic concepts of the systems. The prestressing systems and devices are described for the two types of prestressing, pre-tensioning and post-tensioning, separately. This section covers post-tensioning.Pre-tensioning Systems and Devices, covers pre-tensioning. In posttensioning, the tension is applied to the tendons after hardening of the concrete. The stages of post-tensioning are described next.Stages of Post-tensioningIn post-tensioning systems, the ducts for the tendons (or strands) are placed along with the reinforcement before the casting of concrete. The tendons are placed in the ducts after the casting of concrete. The duct prevents contact between concrete and the tendons during the tensioning operation. Unlike pre-tensioning, the tendons are pulled with the reaction acting against the hardened concrete.If the ducts are filled with grout, then it is known as bonded post-tensioning. The grout is a neat cement paste or a sand-cement mortar containing suitable admixture.In unbonded post-tensioning, as the name suggests, the ducts are never grouted and the tendon is held in tension solely by the end anchorages. The following sketch shows a schematic representation of a grouted post-tensioned member.The profile of the duct depends on the support conditions. For a simply supported member, the duct has a sagging profile between the ends. For a continuous member, the duct sags in the span and hogs over the support.The various stages of the post-tensioning operation are summarised as follows.Casting of concrete.Placement of the tendons.Placement of the anchorage block and jack.Applying tension to the tendons.Seating of the wedges.Cutting of the tendonsReinforced concrete (RC) is a composite material in which concrete's relatively low tensile strength and ductility are counteracted by the inclusion of reinforcement having higher tensile strength or ductility. The reinforcement is usually, though not necessarily, steel reinforcing bars (rebar) and is usually embedded passively in the concrete before the concrete sets. Reinforcing schemes are generally designed to resist tensile stresses in particular regions of the concrete that might cause unacceptable cracking and/or structural failure. Modern reinforced concrete can contain varied reinforcing materials made of steel, polymers or alternate composite material in conjunction with rebar or not. Reinforced concrete may also be permanently stressed (in tension), so as to improve the behaviour of the final structure under working loads. In the United States, the most common methods of doing this are known as pre-tensioning and post-tensioning.For a strong, ductile and durable construction the reinforcement needs to have the following properties at least:High relative strength.High toleration of tensile strain.Good bond to the concrete, irrespective of pH, moisture, and similar factors.Thermal compatibility, not causing unacceptable stresses in response to changing temperatures.Durability in the concrete environment, irrespective of corrosion or sustained stress.Use in constructionRebars of Sagrada Família's roof in construction (2009)·Many different types of structures and components of structures can be built using reinforced concrete including slabs, walls, beams, columns, foundations, frames and more.Reinforced concrete can be classified as precast or cast-in-place concrete.Designing and implementing the most efficient floor system is key to creating optimal building structures. Small changes in the design of a floor system can have significant impact on material costs, construction schedule, ultimate strength, operating costs, occupancy levels and end use of a building.Without reinforcement, constructing modern structures with concrete material would not be possible.Key CharacteristicsThree physical characteristics give reinforced concrete its special properties:The coefficient of thermal expansion of concrete is similar to that of steel, eliminating large internal stresses due to differences in thermal expansion or contraction.When the cement paste within the concrete hardens, this conforms to the surface details of the steel, permitting any stress to be transmitted efficiently between the different materials. Usually steel bars are roughened or corrugated to further improve the bond or cohesion between the concrete and steel.The alkaline chemical environment provided by the alkali reserve (KOH, NaOH) and the portlandite (calcium hydroxide) contained in the hardened cement paste causes a passivating film to form on the surface of the steel, making it much more resistant to corrosion than it would be in neutral or acidic conditions. When the cement paste is exposed to the air and meteoric water reacts with the atmospheric CO2, portlandite and the calcium silicate hydrate (CSH) of the hardened cement paste become progressively carbonated and the high pH gradually decreases from 13.5 – 12.5 to 8.5, the pH of water in equilibrium with calcite (calcium carbonate) and the steel is no longer passivated.As a rule of thumb, only to give an idea on orders of magnitude, steel is protected at pH above ~11 but starts to corrode below ~10 depending on steel characteristics and local physico-chemical conditions when concrete becomes carbonated. carbonatation of concrete along with chloride ingress are amongst the chief reasons for the failure of reinforcement bars in concrete.The relative cross-sectional area of steel required for typical reinforced concrete is usually quite small and varies from 1% for most beams and slabs to 6% for some columns. Reinforcing bars are normally round in cross-section and vary in diameter. Reinforced concrete structures sometimes have provisions such as ventilated hollow cores to control their moisture & humidity.Distribution of concrete (in spite of reinforcement) strength characteristics along the cross-section of vertical reinforced concrete elements is inhomogeneousReinforcement and terminology of beamsTwo intersecting beams integral to parking garage slab that will contain both reinforcing steel and the wiring, junction boxes and other electrical components necessary to install the overhead lighting for the garage level beneath it.A beam bends under bending moment, resulting in a small curvature. At the outer face (tensile face) of the curvature the concrete experiences tensile stress, while at the inner face (compressive face) it experiences compressive stress.A singly reinforced beam is one in which the concrete element is only reinforced near the tensile face and the reinforcement, called tension steel, is designed to resist the tension.A doubly reinforced beam is one in which besides the tensile reinforcement the concrete element is also reinforced near the compressive face to help the concrete resist compression. The latter reinforcement is called compression steel. When the compression zone of a concrete is inadequate to resist the compressive moment (positive moment), extra reinforcement has to be provided if the architect limits the dimensions of the section.An under-reinforced beam is one in which the tension capacity of the tensile reinforcement is smaller than the combined compression capacity of the concrete and the compression steel (under-reinforced at tensile face). When the reinforced concrete element is subject to increasing bending moment, the tension steel yields while the concrete does not reach its ultimate failure condition. As the tension steel yields and stretches, an "under-reinforced" concrete also yields in a ductile manner, exhibiting a large deformation and warning before its ultimate failure. In this case the yield stress of the steel governs the design.An over-reinforced beam is one in which the tension capacity of the tension steel is greater than the combined compression capacity of the concrete and the compression steel (over-reinforced at tensile face). So the "over-reinforced concrete" beam fails by crushing of the compressive-zone concrete and before the tension zone steel yields, which does not provide any warning before failure as the failure is instantaneous.A balanced-reinforced beam is one in which both the compressive and tensile zones reach yielding at the same imposed load on the beam, and the concrete will crush and the tensile steel will yield at the same time. This design criterion is however as risky as over-reinforced concrete, because failure is sudden as the concrete crushes at the same time of the tensile steel yields, which gives a very little warning of distress in tension failure.Steel-reinforced concrete moment-carrying elements should normally be designed to be under-reinforced so that users of the structure will receive warning of impending collapse.The characteristic strength is the strength of a material where less than 5% of the specimen shows lower strength.The design strength or nominal strength is the strength of a material, including a material-safety factor. The value of the safety factor generally ranges from 0.75 to 0.85 in Permissible stress design.The ultimate limit state is the theoretical failure point with a certain probability. It is stated under factored loads and factored resistances.Thank you.
How long should a new concrete driveway cure?
First and foremost, be mindful of the edges of your driveway. They are most likely to fail if you happen, for instance, to gun it up the driveway too early and don’t take it slow, right down the middle, as would be a prudent choice.Some people think it’s so odd to put sprinklers, in the spring/esp. summer/fall, on top of concrete. I mean, is it going to grow more concrete? Haha.But, hopefully, plastic was put down underneath at the time of the concrete placement (i.e., a vapor barrier), and then watering the top by oscillating sprinklers provides the barrier on the top. — This is just good sense for concrete placement during warm months. If it’s snowing outside, you may not want to do this. In fact, you may not want to put in the driveway then at all. Good things come for those who wait.Okay, the next part of the question deals with what type of concrete mix design is being used. In many cases, you’re dealing with a concrete contractor; that is your intermediary with the concrete plant. The “ready-mix” concrete plant should have mix designs, with end strengths measured and included, upon demand.The cheapest contractor may be significantly cheaper because he’s buying the cheapest concrete. Then again, if he’s familiar with the local concrete manufacturer and deliverer, he may know that what he is paying for, which local-market-wise costs less, is a better product. — You’re within your rights to ask for these mix designs and strength tests.In fact, you may be better off paying the plant itself for the concrete and then hiring your concrete contractor just for the labor. Yes, you need steel reinforcement, but you can decide who buys that per your contract.A sort of industry-standard concrete is known as 3000psi. That means it should not fail so long as no more than a ton-and-a-half is rested on one square inch of a slab made from it. — Now, that’s pretty dang strong. But, implicitly, the concrete plant is likely only going to guarantee that level of strength after 28 days. If not that, then 56 days. — As someone else says, yes, in the right conditions, concrete will continue to gain strength into the decades after it was placed.But, let me tell you something.I used to run a concrete plant. It was not uncommon for me to get a contractor for a big-box store, like Lowe’s, who said: “Yeh, I need to pour concrete today that cars and trucks can drive over tomorrow.” — Once I ruled out he didn’t mean tractor-trailer combinations or other large trucks, I might shoot back: “3500 straight cement should work.”I had people call me who said: “We’re on a new (oil or gas) well location, and I need to pour some concrete that 18-wheelers can drive over tomorrow.” — In response, I might say, “That’s fine. 5000psi straight cement should work.”In short: Can I make your driveway accessible for car and truck traffic tomorrow by what I deliver you today? → Yes, I’m sure.But those are very expensive concrete mixes. — Whether “5000psi straight cement” mixes, in the Texas summer heat, should even be poured (or delivered in my trucks) — well, that’s a risk and a guess.The size gravel you use, in ratio to sand, is important.I send out concrete from the plant with a specific water-to-cement ratio, but those mixer trucks carry 100 to 150 gallons on them. The water is primarily there to allow the concrete mixer truck drivers to have the ability to wash off their trucks before re-entering the highway; the return home.In reality, though, contractors work the controls and can add a few gallons of water to your concrete, or they could add the full amount: 100 to 150 gallons, if they chose. Drivers are taught to watch for this, if not for the best outcome of your concrete, but because they need water to wash the truck down at the end, lest they throw sand, rocks, and cement-filled water onto the road, cars following them, etc.The more water your contractor adds on-site, the less strength you can expect in the end. — They add large amounts of water, sometimes, because it’s easier to place runny concrete than it is to place properly manufactured concrete.So, even if the concrete plant tells you a mix design will give you the strength you need, within some period of time of your choosing, that guarantee only exists if the concrete contractor you hired follows the rules and respects the elements of the design (i.e., how much water would be permissible for him to add on-site).As a general rule, wait two weeks to drive on your driveway if you’ve cast the driveway using regular 3000psi concrete.Sometimes, contractors will call 3500psi (a stronger concrete) “5-sack;” you may be able to use your driveway sooner.Unless you order a special design, and you mention how quickly you need to be able to drive over it, then drive down the middle; don’t drive off the sides of it.Those are the places most likely to fail (i.e., break off) during the initial hydration/curing period.Working in general construction, and having been GM of a ready-mix concrete plant for so long, sometimes I’m amused that customers build the house first, and then come back and put in a backyard swimming pool; right before that, they put in a driveway. After all of this, they want to add sidewalks in the front.There may be financial reasons (e.g., bank requirements) for this to happen in this order, but from my concrete-hat point of view, you should put the pool in first; then, cast the front sidewalks; then, pour the slab for the foundation of the new home; and, only after that, put in the driveway.It’s amazing how often customers don’t do it this way. And, you have to remember —We, the plant, only guarantee the concrete mixer truck while it’s on the roadway. If it breaks off part of your new concrete, that’s your business.If it leaves ruts in the ground around your house because you asked for it to go to the back, it’s not our problem, because you just ordered upwards of 25 tons of material, and that’s not even including the weight of the truck.Once the truck is off the roadway, the liability shifts to you. So, think smartly about how you build your dream homeplace.We’re in the construction business, not the destruction business (usually), and we will do whatever is safe to work with you, but if you don’t think this through, and you ask us to do foolish things, the results of those foolish orders lie on the shoulders of customers. — You asked us to something. We agreed, and it didn’t work out.I’m sorry (really) that’s such a big mistake for you. But, you still have to pay.
Is an intercontinental train feasible?
Some have taken the cute approach of connections between Europe and Asia. Let’s address the 2,629-mile gorilla in the corner.Imagine a railroad bridge from Canso, Nova Scotia, Canada, to Brest, France. Why these two places? They're on prominences that jut out into the North Atlantic Ocean, making them arguably the closest two points of mainland between North America and Europe. Plus they are near established railroads so that’s one less thing to build.Why not Natal, Brazil, to Freetown, Sierra Leone, which are only 1,800 miles apart? Or Alaska to Siberia? Given that the EU is the US’s largest trading partner and that freight needs to be the backbone of this boondoggle, this bridge should connect the US and Europe. But maybe the bullet train will fill the gap between those that will not fly and those that don’t have six days to cross by passenger ship.Among the concerns that we will ignore for now will be the difficulty of designing for a railroad’s live and dead load over long spans, thermal expansion and contraction of the bridge spans and rails, impact loads of ships, icebergs and whales, building a stiff structure across a fault line, designing a structure with a 100-year design life in a hostile, salt water environment with freezing temperatures and horrible weather, and operations and maintenance of a railroad and its huge structure out in the middle of the North Atlantic.Let’s budget a highway bridge first and then upscale it to a railroad bridge after we clear that hurdle.Let’s first look at a small scale real world project for cost and feasibility - the Confederation Bridge across Northumberland Straight connecting Prince Edward Island and New Brunswick, Canada. The 8-mile long structure was completed in 1997 after four years of construction and a decade of planning and design. Total cost for that structure was $963M US. The structure is 131 feet above water level and maximum water depth is about 80 feet. The structure is essentially 44 820-foot long spans on concrete piers.I picked my route partly because of the distance the continental shelf extends out from both shorelines. For the first 650 miles from Canada and the last 275 miles coming into France, the water depth is about 500 feet or less. Base cost for this 922 miles of shallow water bridge would be on the order of $110,985M US. This ignores the up-charge for the bridge piers needing to be 10 times taller because the water depth is 10 times deeper than in our base design. Let’s add $1M each for this added height for the 4,868 piers needed on this 922 miles, totaling $4,868M.Now for the interesting part. The ocean water depth beyond the continental shelf varies between 10,000 feet and 16,000 feet deep for a distance of 1,277 miles. $153,719M cost. Again, this is just the base price and ignores the cost of bridge piers 10,000 feet to 16,000 feet tall as compared to 80 feet.Now let us consider our ability to build tall things. Crossing the ocean, we will be building a tall structure down to the ocean floor. The worlds tallest structure in 2019 (Burj Khalifa in Dubai) is 2717 feet high, but the top floor (eliminating towers and other flourishes) is at 1,918-foot elevation; let’s round up to 2,000’. It would take eight of these buildings stacked one on top of the other to reach 16,000 feet. When building a bridge pier versus a building, obviously you do not need the architectural skin, interior walls, ventilation, elevator, etc. Let’s assume that half of the building is the structural framework and the rest is cosmetic and creature comfort. So let’s say $750,000,000 times eight structures high equals $6B per structure. If we somehow stretch the spans to 1,000’, we need 6,742 deep-water structures at $6B each totaling $40,452,000M.It took five years to top out (complete the structural steel work) for Burj Khalifa. Does that mean 40 years for something eight times taller? Eighty years because working at depth will take at least twice as long? How many can be built simultaneously?The base dimensions for the World Trade Center twin towers were 200’ x 200’. The 16,000-foot towers will have a much larger foundation, meaning the towers spaced 1,000’ apart will result in a nearly continuous concrete foundation for the 1,277 miles of deep-water construction. The excavation of the sea floor for the foundation work will be incredibly difficult. Placement of the concrete forms, reinforcing steel and concrete equally so. Remember when we first saw the remains of the Titanic on the bottom of the Atlantic in 1985? The Titanic lies on the sea floor at a depth of 12,500 ft. We will be more than 3,000 ft deeper than this. We need 13,881 foundations, at say $10M for each, which is probably way too little cash. That’s an additional $138,811M.Working below sea level is difficult, to say the least. Recreational SCUBA divers generally stay within 100’ of the surface. An atmospheric diving suit is essentially a one-person submersible with a working depth of about 2,300’, so is useless at 16,000’, where the water pressure hits 7,000 psi. Likewise is the Pisces V, a 3-person scientific submersible good to about 6,500’, or 40% of the depth we need. So all of this work will be remote control with unmanned submersibles yet to be designed.Bullet train concepts mean straight as an arrow trackage. The bridge beam system somehow needs to be stiff enough to not be sway-back like riding the wires from tower to tower on a high-tension power line or like Tarzan riding his vines. Otherwise your passengers are going to be seasick for thousands of miles.Furthermore, there will have to be several segments with 200-foot under clearance to allow passage of the tallest sailing vessels, particularly near the coast of France for vessels traveling the coastline and near Nova Scotia for ship traffic to and from the St Lawrence Seaway. This 79-foot increase in elevation will need to be held to around 1% grade to keep the trains moving. This adds complication to design, construction and operation.A significant design concern is sway. The 2,717-foot Burj Khalifa sways about five feet in high winds. How much will it sway if it’s now eight times taller? Hold a stack of 10 Dixie cups firmly on a table top with one hand and use your other hand to move the top around as if it’s windy. That’s your paper Burj Khalifa. Now add 70 more cups to that stack and sway it with your hand. That’s your 16,000-foot high pier. Even with a bare steel frame and no skin, water pressing against the steel structure will move it more than the wind. Wind blowing against the side of the bridge spans 131’ above the ocean surface will move it some more, sometimes in the opposite direction. Icebergs, which can exceed 200 feet in height, heading south from Greenland will press on piers or bridge spans. This bridge is going to sway. Trains hate sway. With the wheels locked on the rails of the track, shoving the train or the bridge left and right will cause the train to topple.SummarySo I think I’ve awfulized this enough already. Let’s summarize what we know.$110,985M for 922 miles of shallow-water bridge less than 500-foot depth$153,719M for 1,277 miles of deep-water bridge without piers$40,452,000M for 6,742 deep-water piers up to 16,000’ tall$4,868M for 4,868 shallow-water piers ~500’ tall$138,811M for foundationsGrand total - $40,860,383,000,000$40,860,383 million$41 million million$41 trillionThis is 317 times more expensive than the cost to build the entire 42,795-mile Interstate system. To be used by a tiny portion of the World’s population.Given the many uncertainties, we should probably double it and then round up to $100 trillion.That’s the long answer to your question. That’s a lot of train tickets.The short answer? No.Or more accurately, Hell No.
- Home >
- Catalog >
- Business >
- Order Template >
- Work Order Template >
- Contractor Work Order Template >
- construction work order template >
- Concrete Placement Work Order Construction Contract