How to Edit The Virginia Stop Loss Requirements easily Online
Start on editing, signing and sharing your Virginia Stop Loss Requirements online with the help of these easy steps:
- Click on the Get Form or Get Form Now button on the current page to make your way to the PDF editor.
- Give it a little time before the Virginia Stop Loss Requirements is loaded
- Use the tools in the top toolbar to edit the file, and the edited content will be saved automatically
- Download your edited file.
The best-reviewed Tool to Edit and Sign the Virginia Stop Loss Requirements
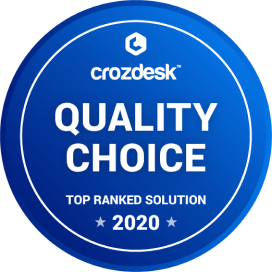
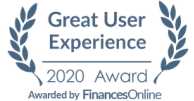
A simple direction on editing Virginia Stop Loss Requirements Online
It has become very easy just recently to edit your PDF files online, and CocoDoc is the best free PDF editor for you to make changes to your file and save it. Follow our simple tutorial to start on it!
- Click the Get Form or Get Form Now button on the current page to start modifying your PDF
- Create or modify your content using the editing tools on the toolbar on the top.
- Affter changing your content, add the date and draw a signature to complete it perfectly.
- Go over it agian your form before you click the download button
How to add a signature on your Virginia Stop Loss Requirements
Though most people are accustomed to signing paper documents by writing, electronic signatures are becoming more regular, follow these steps to sign documents online for free!
- Click the Get Form or Get Form Now button to begin editing on Virginia Stop Loss Requirements in CocoDoc PDF editor.
- Click on Sign in the tool menu on the top
- A popup will open, click Add new signature button and you'll be given three options—Type, Draw, and Upload. Once you're done, click the Save button.
- Drag, resize and position the signature inside your PDF file
How to add a textbox on your Virginia Stop Loss Requirements
If you have the need to add a text box on your PDF for customizing your special content, do the following steps to carry it out.
- Open the PDF file in CocoDoc PDF editor.
- Click Text Box on the top toolbar and move your mouse to drag it wherever you want to put it.
- Write down the text you need to insert. After you’ve input the text, you can use the text editing tools to resize, color or bold the text.
- When you're done, click OK to save it. If you’re not satisfied with the text, click on the trash can icon to delete it and do over again.
A simple guide to Edit Your Virginia Stop Loss Requirements on G Suite
If you are finding a solution for PDF editing on G suite, CocoDoc PDF editor is a suggested tool that can be used directly from Google Drive to create or edit files.
- Find CocoDoc PDF editor and establish the add-on for google drive.
- Right-click on a PDF file in your Google Drive and click Open With.
- Select CocoDoc PDF on the popup list to open your file with and allow access to your google account for CocoDoc.
- Edit PDF documents, adding text, images, editing existing text, annotate with highlight, fullly polish the texts in CocoDoc PDF editor before saving and downloading it.
PDF Editor FAQ
What are the recent trends in concrete technology?
The need for innovation in the construction industry has long been stressed from both within and outside the industry. Changes in global markets, increased customer expectations, and government pressure have all led to innovation becoming a key focus for the construction sector. There is increasing pressure on the construction industry to become more environ-mentally sustainable. As the construction industry is a major energy user as well as contributer to the greenhouse gas emissions and waste levels, the government is pushing hard to the construction sector to come up with more and more innovative technologies in concrete since concrete is the mother constituent of any construction.Developing and maintaining world’s infrastructure to meet the future demands of industrialized and developing countries has become necessary to economically grow and improve the quality of life. The quality and performance of concrete plays a key role for most of the infrastructure including commercial, industrial, residential and military structures, dams, power plants and transportation systems. Concrete is the single largest manufactured material in the world and accounts for more than 6 billion metric tons of materials annually. In United States, federal, state, and local governments have nearly $1.5 trillion dollars in investment in the U.S. civil infrastructure. The worldwide use of concrete materials accounts for nearly $780 billion in annual spending. The industrialized and developing world is facing the issues related to new construction as well as repair and rehabilitation of existing facilities. Rapid construction and long term durability are requirements on most projects. Initial and life-cycle costs play a major role in today’s infrastructure development. There have been number of notable advancements made in concrete technology in the last fifty years. Some of these advances have been incorporated in routine practices. But, in general, the state-of-practice has lagged far behind the state-of-art. This is particularly true for public sector projects. There is an increasing concern in most parts of the world that it takes unduly long time for successful concrete research products to be utilized in practice. Even though some advances have been made in quick implementation of new concrete technology, significant barriers to innovation and implementation remain. Continued coordination of ongoing inter- national research and educational pro-grams is needed.Numerous advances have been made in all areas of concrete technology including materials, mixture proportioning, recycling, structural design, durability requirements, testing and specifications. Throughout the world some progress has been achieved in utilizing these innovations but largely these re-main outside routine practice. The high performance concrete (HPC) for transportation structures, e.g., bridges and pavements, are gaining wider acceptability in routine practice. HPC provides enhanced strength and durability properties and contributes towards long lasting structures and pavements. The constructability can also be enhanced by proper mixture proportioning and testing. Most HPC mixture include re-cycled materials e.g. fly ash, ground granulated blast furnace slag (GGBFS), Metakaolin (MK) or silica fume. The use of recycled materials in construction is an issue of great importance in this century. Utilization of fly ash and GGBFS in concrete addresses this issue. The replacement of Portland cement by fly ash or GGBFS reduces the volumes of Portland cement used is a major benefit. The reduction of Portland cement production will reduce carbon dioxide (CO2) emissions, reduce energy consumption and reduce the rate of global warming. Utilization of fly ash and GGBFS usually provides cost savings as well as improved concrete properties. The case histories discussed demonstrate the practical uses of supplementary cementitious materials. fly ash, GGBFS and silica fume for various types of bridges and pavements in wide ranging environ- mental conditions. The successful utilization of supplementary cementitious materials requires proper mixture pro-portioning, testing, placement and curing. Lack of widespread transfer of developed and available new concrete technology is a major problem in most countries. The practicing engineer’s (user) involvement through re-search, development and technology transfer stages is a key to successful application of new concrete technology in routine design and practice. The past experience has shown that successful technology transfer occurs when there is a pressing national need, champions of technology are created, champion and organizations involved persist, practical demonstrations of technology are conducted to demonstrate benefits, and regulatory requirements are implemented. The new concrete technology must fulfill a need to be successful. The user’s (owner/designer/construction engineer) involvement is vital to success. The user starts and ends the techno-logy process. Examples of successful concrete technology transfer efforts are discussed.Some Emerging Trends and Innovations in Concrete1. Green Cements2. Blended Cements3. High Performance Concrete (HPC)4. Smart Concrete5. Self-Consolidating Concrete (SCC)6. Use of Recycled Tire Rubber in Concrete7. Smog Eating Concrete8. Reactive Powder Concrete (RPC)9. Translucent Concrete10. Pervious Concrete11. Low Temp. Concrete Admixture12. Prepacked Shotcrete Admixture13. Steel-Free Concrete Bridge Deck14. Pavemend – Rapid Repair Products15. Suntreat – Concrete Restoration & Protection System16. Precast Inverted T Beam17. Conductive Concrete18. Corrosion Inhibitors for Reinforced Concrete19. Shrinkage Reducing Admixture for Concrete20. Mellose non-dispersible Under-water Concrete AdmixtureGreen CementsResearch has been carried out to develop non-clinker “green” cement using two industry wastes: cement kiln dust (CKD) and fly ash (FA). CKD contains partially calcined materials with some hydraulic and cementitious properties. It also has high alkali, chloride, and sulfate content, which may cause problems in cement performance.Blended CementsAn important concept of concrete technology innovation is blended cements. It makes use of industry by pro-ducts like fly ash and blast furnace slag, which otherwise would have required land for its disposal. The concept also gives lesser natural lime stone and lesser emission of CO2 to atmosphere. Common ternary blends includes, 50% Portland cement + 30% slag cement + 20% fly ash, to improve concrete performance, qualify for tax credits with re-cycled content.High Performance Concrete (HPC)Normal Strength Concrete (NSC) is heavy and lacks the required work-ability in some large concrete structures, such as high-rise buildings, bridges, and structures under severe exposure conditions. By increasing concrete strength and performance, the required thickness of concrete members and the cost of concrete structures can both be reduced. In the U.S., a major move to-ward HPC is underway, especially in the manufacturing environment of precast concrete. A major demonstration precast concrete bridge is under construction in Texas. High Performance Concrete (HPC) is the latest development in concrete. It is not just High-Strength Concrete (HSC) and has replaced HSC developed in the early 1980’s. HPC can be defined as a concrete made with appropriate materials (superplasticizer, retarder, fly ash, blast furnace slag and silica fume) combined according to a selected mix design and properly mixed, transported, placed, consolidated, and cured to give excellent performance in some properties of concrete, such as high compressive strength, high density, low permeability and good resistance to certain forms of attack.Smart ConcreteConcrete has been widely used for many years as a composite material for various types of structures. One of the weaknesses of concrete is that it cannot withstand tension which can cause cracks easily. There has been a huge demand to monitor concrete structures cracking and preventing them from propagating further. These efforts are important for timely repair, safety and long-term durability of critical structures. Non-destructive evaluations, such as attaching or embedding sensors into structures, have been used in many ways to accommodate the demand, yet the tests are considered expensive. Smart concrete was developed by Dr. Deborah D.L. Chung from State University of New York at Buffalo. Smart concrete is reinforced by carbon fiber as much as 0.2% to 0.5% of volume to increase its sense ability to strain or stress while still has good mechanical properties. By adding small amount of short carbon fiber into concrete with a conventional concrete mixer, the electrical resistance of concrete increases in response to strain or stress. As the concrete is deformed or stressed, the contact between the fiber and cement matrix is affected, thereby affecting the volume electrical resistivity of the concrete. Strain is detected through measurement of the electrical resistance. So, the smart concrete has the ability to sense tiny structural flaws before they become significant, which could be used in monitoring the internal condition of structures and following an earthquake.Self-Consolidating Concrete (SCC)It has brought about “Revolution” in the precast industry. No compaction required in SCC still it results in no segregation and shows excellent flow-ability. It eliminates vibration and yields smooth surface finish with no voids.Use of Recycled Tire Rubber in ConcreteMore than 250 million scrap tires weighing more than 3 million tons are generated each year in the United States (Naik and Siddique 2002). This is considered as one of the major environ-mental challenges facing municipalities around the world because waste rubber is not easily biodegradable even after a long period of landfill treatment. One of the solutions suggested is the use of tire rubber particles as additives in cement-based materials.Smog Eating ConcreteCement treated with titanium oxide. Photocatalytic reaction with UV light takes place, it accelerates natural oxidation process and decomposes pollutants to clear air. The reaction prevents bacteria and dirt from accumulating on a surface. It is easily removed with water or rain and keep concrete clean and white.Reactive Powder Concrete (RPC)Reactive Powder Concrete is an ultra high-strength and high ductility composite material with advanced mechanical properties. Developed in the 1990s by Bouygues’ Laboratory in France. It consists of a special concrete where its micro structure is optimized by precise gradation of all particles in the mix to yield maximum density. It uses extensively the pozzolanic properties of highly refined silica fume and optimization of the Portland cement chemistry to produce the highest strength hydrates. RPC represents a new class of Portland cement-based material with compressive strengths in excess of 200 MPa range. By introducing fine steel fibers, RPC can achieve remarkable flexural strength up to 50 MPa. The material exhibits high ductility with typical values for energy absorption approaching those reserved for metals.Translucent ConcreteIt changes the perception of concrete’s opaque mass, it is prepared with optical glass fibers.Previous ConcreteIt possesses little or no sands and has open pore structure. It Reduces storm water run-off.Low Temperature Concrete AdmixturePerforming construction processes under the cold weather condition requires construction engineers to plan operations considering low temperature condition. Especially, since the quality of concrete is sensitive to temperature, costly cold weather protection has been required to prevent damage due to in-appropriate weather environment. Concrete admixtures, mostly chemically, interact with the constituents of concrete and affect the properties and characteristics of the fresh and hardened concrete and its durability. The purposes of the admixtures include water reduction, high strength, corrosion protection, crack control, finish enhancement, flowability, etc. One of the interesting and useful purposes is protection against freeze. Accelerating admixture is to increase the rate of early strengthdevelopment or to shorten the time of setting, or both. Some of these accelerating materials have properties effective to avoid free-zing. Pozzutec® 20+ developed by Master Builders, Inc. is a multicomponent, non-chloride, water reducing and accelerating admixture formulated to accelerate concrete setting time and increase early and ultimate strengths across a wide range of ambient temperatures.Prepacked Shotcrete AdmixtureOver the past 10 years, the wet shotcrete method has become increasingly used in the repair of vertical and over-head concrete surfaces. This is due, in part, to advances inmaterials such as the introduction of silica fume (microsilica), fibers and super-plasticizers, which not only make shotcrete easier to place, but also improve its durability. Batching all these materials in the right proportions with sand and cement can be difficult, so many manufacturers have developed pre-packed shotcrete repair mortars to which con-tractors add only water. The prepacked materials simplify batching and provide more consistent quality. But packaging all the dry materials increases their cost. Gemite Products Inc. Amherst, NY developed prepacked products (called “concentrates”), which include all the admixtures but require contractors to provide their own sand and cement. The material costs of concentrates mixed with sand and cement are considerably lower when compared with complete packaged systems, while maintaining the same quality.Steel-Free Concrete Bridge DeckSteel-free concrete replaces rein-forced concrete in bridge decks and similar structures in marine environments and in northern climates having snow and ice. It is to eliminate the source of deterioration, the steel reinforcing bars in slabs exposed to deicing salts. Eliminating corrosion makes concrete deck slabs virtually maintenance free, which makes life cycle costs of steel-free concrete decks much lower than reinforced concrete decks. Shear connectors make the steelfree concrete deck composite with the steel girders that support it. Top flanges of girders attempt to displace outward when a truck drives across the deck. External transverse steel straps below the bridge deck and between the bridge girders prevent this outward displacement by providing a lateral restraining force to the girder and concrete deck. In res-ponse, compressive membrane forces develop in the concrete deck. Ultimate load can be greater than the load at which the same deck would fail if it were reinforced conventionally. In fact, the tension capacity of the steel straps in the steel-free deck replaces conventional reinforcing steel. The external steel straps can be inspected and maintained in a similar fashion to steel girders.Status:Two versions are available:1. The cast-in-place version2. The pre-cast Arch Panel version.The cast-in-place deck slab is now in the Canadian Highway Bridge Design Code (CHBDC), currently in the press. Japan is reviewing the technology. Meet- ing with American Association State High- way Transportation Officials (AASHTO) Code Committee is in progress.Pavement – Rapid Repair ProductsRepair of concrete continues to be a major maintenance item in the budget of many agencies. There are many circumstances in which a rapid repair is highly desirable. Ceracrete Technologies, Inc. (CTI) is a Richmond, Virginia-based small business. CTI focuses on the manufacture of commercial products for construction applications using non- hazardous inorganic recovered raw materials to replace conventional virgin raw materials. Ceracrete technology is a chemical bonding process that uses very high percentages of coal ash, municipal solid waste ash, foundry sand residue, dredge material, flue gas desulferization by-products, etc. to create rapid concrete repair products. The initial Ceracrete rapid concrete repair product, PaveMend, reaches 3670 psi at one hour and 4400 psi at three hours, easily qualifying it as a very rapid pavement repair material. The twenty eight day comprehensive strength levels operate at around 6,000psi. This ge-nerally means that field users can mix, pour/place and open the area to traffic quickly without special curing or protection measures.Suntreat – Concrete Restoration & Protection SystemReinforcing steel corrosion is the most common cause of failure of concrete structures. Once started, rebar corrosion cannot be stopped by simply waterproofing the surface of the concrete. The corrosion process is influenced and promoted by penetration of air, water, chloride and an acid environment. Surtreat can be used to prevent contamination and decomposition of concrete surfaces in hostile, chloride and acid containing environments. Surtreat is a proprietary concrete restoration and protection system. The system includes sequential application of chemical treatments to improve the properties of the deteriorating concrete and protect new structures. Surtreat proprietary chemical formulations penetrate into the concrete microstructure in liquid and vapor state to combine with the cement phase of concrete and deposit on steel components. Surtreat increases the ability of concrete to resist deterioration by in-creasing compressive strength, reducing permeability, inhibiting corrosion of the reinforcing steel components and improving concrete’s resistance to acid attack. Surtreat is used in the widest variety of applications and every owner /manager/operator of structures that include concrete components can benefit from the installation of Surtreat. All tests were conducted at the NASA Kennedy Space Center laboratories and in compliance with applicable ASTM Standard Test Methods. The evaluation methods employed by NASA specialists included measurement of halfcell potential, corrosion current and polarization resistance. The most direct measure of the corrosion rate, polarization resistance was increased by 300% after application of Surtreat. Halfcell potential and corrosion current measurements also reflect a significant decline in corrosion rates after application of surtreat corrosion inhibitors.Precast Inverted T Beam:Current systems are either costly or time consuming to erect and have limitations. Cast-in-place slabs have become too expensive and time-consuming due to extensive field formwork. Precast solid slabs aren’t economical for spans longer than 9 meters. I-girders with concrete deck slab topping can span longer than other systems, but require field formwork and significantly higher clearance. The new precast concrete product for short to medium span bridges was developed by the University of Nebraska. The Nebraska Inverted Tee (IT) can span up to 26 meters with a total structural depth of 725 mm. Most U.S. highway bridges have short to medium span lengths. And most bridges needing rehabilitation or replacement are short-span. A recently developed type of pre-stressed concrete beam is helping slash 20% off the weight of a bridge being built in Florida between the cities of Boynton Beach and Ocean Ridge.Conductive Concrete:Concrete has been used for many years as a composite material that has excellent mechanical properties and durability for construction. However, concrete is a poor electrical conductor, especially under dry conditions. Concrete that is excellent in both mechanical and electrical conductivity properties may have important applications in the electrical, electronic, military and construction industry (e.g. for deicing road from snow). Traditional methods can warm roads, but installation cost is high and the procedure is complicated. The principle behind it is the use of cement to bind together electrically conductive materials such as carbon fiber, graphite and ‘coke breeze’ – a cheap by-product of steel production – to make a continuous network of conducting path- way. The design formulation is based on the ‘electrical percolation’ principle by which the composite conductivity increases dramatically by several orders of magnitude when the content of the conductive phase reaches a critical ‘threshold’ value. Further increases in the conductive phase content boost composite conductivity only slightly. The design specifies an amount just over the threshold content, assuring high conductivity and mechanical strength as well as good mixing conditions.Corrosion Inhibitors for Reinforced ConcreteSteel corrosion in reinforced concrete structures has been a major problem across World today. Steel-rein-forced concrete structures are continually subject to attack by corrosion brought on by naturally occurring environmental conditions such as carbonation and the introduction of chlorides from sources such as salt water, deicing salts, and accelerating admixtures. Corrosion inhibitors available in the market can be mixed with ready mixed concrete or applied over the old concrete greatly reduces the overall corrosion activity (up to 65% reduction). Such products normally do not affect the properties of hardened concrete, such as compressive strengths, permeability, etc. One demerit of such pro-ducts are that it reduces corrosion but cannot stop it. A combination of this product with other protective systems is required if the level of durability of the concrete structure needs to more than double.Shrinkage Reducing Admixture for ConcreteConcrete shrinkage cracking is a common problem in all types of concrete structures, especially for structures and environments where the cracks are prevalent and the repercussions are most severe. Examples of these are bridge decks, parking garages, marine structures, containment structures, and high performance floors. A liquid shrinkage reducing admixture for concrete, developed by Grace Construction Products and Arco Chemical Company, that reduces significantly the shrinkage during concrete drying and potentially reduces overall cracking over time. The product can be easily dissolved in concrete mix water or dispersed in concrete during mixing. The admixture works by reducing the surface tension of the water, decreasing the force pulling in on the walls of the pores, resulting in a reduction of the shrinkage strain.Mellose Non-dispersible Underwater Concrete AdmixtureMany under-water civil engineering structures are affected not only by the presence of water or salt but also by water pressure; flow of water, and by the different material’s density. These factors could cause cracks, corrosion, and dispersion of concrete particles. Mellose is a viscose agent based on under water Cellulose (Hydroxy Propyl Methyl Cellulose). It is commonly referred to as a self-leveling agent that increases viscosity when is dissolved in water. It can be also described as an anti-wash-out concrete or non-dispersible concrete mixture. When Mellose is added, it prevents the loss of cement in the mortar and the separation of the concrete particles due to its increased viscosity. It combines first with the water than with the cement and the other concrete particles.Benefits include: Mellose increases the viscosity of suspended concrete but decreases the viscosity of flowing con-crete. Therefore, it increases the work-ability of the concrete, while there is no separation of its aggregates. It prevents the segregation of aggregates as well as the bleeding when used for under water construction. The product comes in the form of a powder that is added as a concrete admixture.Barriers are: Mellosecan not be used with Naphtalene Sulphonate because of chemical reactions.ConclusionThe cement and concrete industry has some inherent problems that re-strict the rate of adoption of new technologies to meet these challenges. These include:– Expensive manufacturing infra-structure– Low margin product– Proliferation of formula based technical standards– Industry culture tied to the orthodox belief that “it has always been done this way”These excuses will not impress an institutional investor that has a myriad of investing opportunities to choose from and is ready to move millions of dollars of capital to anywhere in the world at the press of a button. Neither is a user trying to overcome a problem such as cement shrinkage or corrosion or a politician who is being pressured by community concern over environ-mental degradation going to be Interested in the problems of the industry. Cement manufacturers need to ask themselves the same questions.Cements and concretes are changing to better meet the needs of customers ahead of the competition. The construction industry is conservative and the changes have been slow, such as the increase in thealite/belite ratio over the last twenty years and the incorporation of supplementary cementitious materials and various fibres. Cements and concretes probably need to change much more quickly to meet the challenges of the future. Challenging the traditional construction paradigm is robotics. In the USA and elsewhere in the world researchers are looking at using robots to literally print buildings. It is all quite simple from a software, computer hardware and mechanical engineering point of view. The difficulty is in developing new construction materials with the right Bingham plastic rheology so they can be squeezed out like tooth-paste; yet retain their shape until hardened. The main inhibiters to evolution in the industry are the formula-based app-roach to standards which grew out of the industrial environment of the early twentieth century. Standards are important for society’s protection, but to allow creativity and innovation, standards would be a much better servant to society if they were performance-based rather than formula-based.Source - Masterbuilder
- Home >
- Catalog >
- Life >
- Citizenship And Immigration Form >
- I 765 Form >
- Form I-130 >
- i-130a form >
- Virginia Stop Loss Requirements