The Guide of completing Software Configuration Management Plan - U.S. Department Of Energy Online
If you are looking about Customize and create a Software Configuration Management Plan - U.S. Department Of Energy, here are the simple ways you need to follow:
- Hit the "Get Form" Button on this page.
- Wait in a petient way for the upload of your Software Configuration Management Plan - U.S. Department Of Energy.
- You can erase, text, sign or highlight through your choice.
- Click "Download" to download the documents.
A Revolutionary Tool to Edit and Create Software Configuration Management Plan - U.S. Department Of Energy
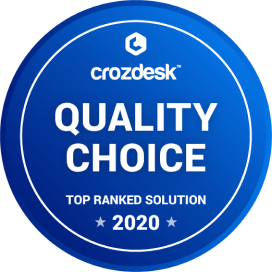
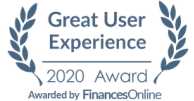
Edit or Convert Your Software Configuration Management Plan - U.S. Department Of Energy in Minutes
Get FormHow to Easily Edit Software Configuration Management Plan - U.S. Department Of Energy Online
CocoDoc has made it easier for people to Fill their important documents through online website. They can easily Tailorize through their choices. To know the process of editing PDF document or application across the online platform, you need to follow these steps:
- Open CocoDoc's website on their device's browser.
- Hit "Edit PDF Online" button and Select the PDF file from the device without even logging in through an account.
- Edit your PDF forms online by using this toolbar.
- Once done, they can save the document from the platform.
Once the document is edited using online browser, the user can export the form of your choice. CocoDoc ensures that you are provided with the best environment for implementing the PDF documents.
How to Edit and Download Software Configuration Management Plan - U.S. Department Of Energy on Windows
Windows users are very common throughout the world. They have met millions of applications that have offered them services in managing PDF documents. However, they have always missed an important feature within these applications. CocoDoc aims at provide Windows users the ultimate experience of editing their documents across their online interface.
The process of editing a PDF document with CocoDoc is simple. You need to follow these steps.
- Pick and Install CocoDoc from your Windows Store.
- Open the software to Select the PDF file from your Windows device and move toward editing the document.
- Fill the PDF file with the appropriate toolkit appeared at CocoDoc.
- Over completion, Hit "Download" to conserve the changes.
A Guide of Editing Software Configuration Management Plan - U.S. Department Of Energy on Mac
CocoDoc has brought an impressive solution for people who own a Mac. It has allowed them to have their documents edited quickly. Mac users can fill PDF forms with the help of the online platform provided by CocoDoc.
To understand the process of editing a form with CocoDoc, you should look across the steps presented as follows:
- Install CocoDoc on you Mac in the beginning.
- Once the tool is opened, the user can upload their PDF file from the Mac quickly.
- Drag and Drop the file, or choose file by mouse-clicking "Choose File" button and start editing.
- save the file on your device.
Mac users can export their resulting files in various ways. Not only downloading and adding to cloud storage, but also sharing via email are also allowed by using CocoDoc.. They are provided with the opportunity of editting file through various methods without downloading any tool within their device.
A Guide of Editing Software Configuration Management Plan - U.S. Department Of Energy on G Suite
Google Workplace is a powerful platform that has connected officials of a single workplace in a unique manner. When allowing users to share file across the platform, they are interconnected in covering all major tasks that can be carried out within a physical workplace.
follow the steps to eidt Software Configuration Management Plan - U.S. Department Of Energy on G Suite
- move toward Google Workspace Marketplace and Install CocoDoc add-on.
- Attach the file and Click on "Open with" in Google Drive.
- Moving forward to edit the document with the CocoDoc present in the PDF editing window.
- When the file is edited ultimately, share it through the platform.
PDF Editor FAQ
I have just completed my 12th grade studies. I am good at calculation and logical thinking. Should I pursue an engineering career?
When you talk about numbers, some of the certain careers comes to my neurons are:1. Actuarial , One of the highest paid career, though you have to be absolute good at maths.2. Theoretical Physics | Economics3. Theoretical Computer Science4. Financial Modelling & Statistics course(stats course can help you5. Financial Engineering { 2015 Financial Engineering Rankings } 16-20 months course.6. Simulation based tools used in Industry of mechanical based industries such as Oil & Gas, Heavy Industries viz Transformer manufacturing, Pharmaceutical Industries.Some More number intensive research field evolved in recent years are:1. Computational Neuroscience.2. Bio-InformaticsNow Comes for you the most exhaustive explanation, find yourself what you want to do with number based careers.<--------------------A List of Professions -------------------------->The following list briefly describes work associated with some mathematics-related professions :actuary-- assemble and analyze statistics to calculate probabilities of death, sickness, injury, disability, unemployment, retirement, and property loss; design insurance and pension plans and ensure that they are maintained on a sound financial basismathematics teacher-- introduce students to the power and beauty of mathematics in elementary, junior high, or high school mathematics coursesoperations research analyst-- assist organizations (manufacturers, airlines, military) in developing the most efficient, cost-effective solutions to organizational operations and problems; this includes strategy, forecasting, resource allocation, facilities layout, inventory control, personnel schedules, and distribution systemsstatistician-- collect, analyze, and present numerical data resulting from surveys and experimentsphysician-- diagnose patient illnesses, prescribe medication, teach classes, mentor interns, and do clinical research; students with a good mathematics background will find themselves being admitted to the best medical schools and discover that mathematics has prepared them well for the discipline, analysis, and problem- solving required in the field of medicineresearch scientist-- model atmospheric conditions to gain insight into the effect of changing emissions from cars, trucks, power plants, and factories; apply these models in the development of alternative fuelscomputer scientist-- interface the technology of computers with the underlying mathematical principles of such diverse applications as medical diagnoses, graphics animation, interior design, cryptogrraphy, and parallel computersinventory strategist-- analyze historical sales data, model forecast uncertainty to design contingency plans, and analyze catalog displays to make them more successful; analyze consumer responsesstaff systems air traffic control analyst-- apply probability, statistics, and logistsics to air traffic control operations; use simulated aircraft flight to monitor air traffic control computer systemscryptologist-- design and analyze schemes used to transmit secret informationattorney-- research, comprehend, and apply local, state, and federal laws; a good background in mathematics will help a student get admitted to law school and assist in the understanding of complicated theoretical legal conceptseconomist-- interpret and analyze the interrelationships among factors which drive the economics of a particular organization, industry, or countrymathematics professor-- teach mathematics classes, do theoretical research, and advise undergraduate and graduate students at colleges and universitiesenvironmental mathematician-- work as member of interdisciplinary team of scientists and professionals studying problems at specific Superfund sites; communicate effectively across many academic discilplines and be able to summarize work in writingrobotics engineer-- combine mathematics, engineering, and computer science in the study and design of robotsgeophysical mathematician -- develop the mathematical basis for seismic imaging tools used in the exploration and production of oil and gas reservoirsdesign -- use computer graphics and mathematical modeling in the design and construction of physical prototypes; integrate geometric design with cost-effective manufacturing of resulting productsecologist -- study the interrelationships of organisms and their environments and the underlying mathematical dynamicsgeodesist -- study applied science involving the precise measurement of the size and shape of the earth and its gravity field (courtesy of Bruce Hedquist)photogrammetrist -- study the applied science of multi-spectral image acquisition from terrestrial, aerial and satellite camera platforms, followed up by the image processing, analysis, storage, display, and distribution in various hard-copy and digital format (courtesy of Bruce Hedquist)civil engineer -- plan, design, and manage the construction of land vehicle, aircraft, water, and energy transport systems; analyze and control systems for land vehicular traffic; analyze and control environmental systems for sewage and water treatment; develop sites for industrial, commercial and residential home use; analyze and control systems for storm water drainage and storage; manage construction of foundations, structures and buildings; analyze construction materials ; and surface soils and subterranean material analysis (courtesy of Bruce Hedquist)geomatics engineer -- once known as "surveying engineer", includes geodetic surveying : takes into account the size and shape of the earth, in order to determine the precise horizontal and vertical positions of geodetic reference monuments; cadastral surveying : establishes and reestablishes the reference monuments for the U.S. Public Land Survey System, i.e., township and section corners; topographic surveying : determines the detailed configuration or contour of the natural earth's surface and the position of fixed objects thereon or related thereto; hydrographic surveying : similarly determines underwater contours and features; land surveying : is the location of existing parcel and new land subdivision lines, road and utility rights-of-way and easement lines, and determination of the location of existing and new reference monuments, which mark property lines and parcel corners; land surveying : also involves the preparation of legal descriptions for officially recorded land ownership conveyance deeds and other land title documents; construction surveying : is the determination of the direction and length between and the elevations of reference points for fixed private and public works, as embraced within the definition and practice of civil engineering, and the labeling of reference markers containing critical information for the construction thereof; design, operation and management of advanced Geographic Information Systems (GIS and Land Information Systems (LIS), as well as other sophisticated computer mapping and CAD based geospatial applications (courtesy of Bruce Hedquist)EmployersThere are many public and private employers who hire some of the above-mentioned professionals. Besides schools, colleges, universities, and many state and federal agencies, some specific employers include the Internal Revenue Service, U. S. Census Bureau, Ford Motor Co., Transamerica Insurance Co., Jet Propulsion Laboratory, L. L. Bean, IBM Corporation, Center for Communications Research, Sandia National Laboratories, A. C. Nielsen Co., American Airlines, U. S. Department of Energy, Exxon Production Research Co., United Airlines, Bureau of Labor Statistics, Prudential Securities, International Computer Science Institute, National Security Agency, Silicon Graphics, Control Data Corporation, U. S. Geological Survey, Renaissance Software, Goddard Space Flight Center, Los Alamos National Laboratory, and U. S. Department of Agriculture.In India central and state government employ statisticianshttp://mospi.nic.in/Mospi_New/site/home.aspx
How do you see a smart factory being used in the future?
Here is an in-depth analysis from online literature that I had done on smart factories. Hope this helps:INTRODUCTION -Big Data, IOT, Cloud Computing and Machine learning, these are some of the innovations of digitization that are transforming manufacturing practices across countries and industries. The onset of digitization and the so called 4th industrial revolution or Industry 4.0 is shifting manufacturing from a largely process driven industry to an innovation driven industry. Nowadays people are surrounded by many things that are called smart. South Korea’s government in collaboration with the local industry has even launched the project to build the smart city [1]. Smart Factory has been achieved by: digitalization data from analog systems, increasing use of flexible structures, strategies (scenarios) and also use of artificial intelligence (smart solution). Below you will find some of these technologies to develop the framework of a smart factory.The term "Industry 4.0" originates from a project in the high-tech strategy of the German government, which promotes the computerization of manufacturing. [2] Many have compared Industry 4.0 with the Fourth Industrial Revolution. However, the fourth industrial revolution also encompasses the effect of digitization on the whole society and not just solely on economic/manufacturing ramifications. The first industrial revolution mechanized production systems with water and steam power; the second industrial revolution, led by Ford introduced the concepts of mass production with the help of electric power, followed by the digital revolution and the use of electronics in the form of CNC systems to automate production. [3]Industry 4.0 is the inclusion of automation and data exchange in manufacturing technologies. It includes cyber-physical systems, IoT, cloud computing and other such technologies. Industry 4.0 can help create a "smart factory". Within such integrated smart factories, cyber-physical systems monitor all physical processes, create a virtual copy of the physical world and make live and decentralized decisions. Over the Internet of Things, such systems communicate and cooperate with each other and with humans in real time, and via the Internet of Services, both internal and cross-organizational services are offered and used by participants of the value chain. [4]What is a SMART FACTORY?A Smart Factory relies on interoperable and dynamic systems; multi-scale dynamic modelling and simulation; intelligent automation; scalability, high cyber security; and network of sensors. Such companies use data and information throughout the entire product life cycle with the objective of creating flexible manufacturing processes that respond rapidly to changes in demand at very low costs to the organization, as well as to the environment. These processes allow the easy flow of information across all business functions inside the organization and manage the connections to suppliers, customers, and other stakeholders outside it.Smart factories will revolutionise how we perceive manufacturing by -1. Bringing about a revolution in the development and application of smart manufacturing concept to every aspect of business.2. Providing flexible and adaptable production process3. Bring about a sensitivity to manufacturing, where volumes are dictated by a pull based demand instead of the current push based demand.What are the enabling technologies?The broad definition of smart manufacturing can cover many different technologies. Some of the key technologies in the smart manufacturing movement include big data and data analytics; inter connectivity devices and services, and smart robotics. [6]a) Internet of Things and machine-to-machine communicationIoT is used to connect any type of object having a virtual representation or identity in the internet. Machine-to-machine (M2M) communication or integration refers to the set of technologies and networks that provide connectivity and inter-operability between machines to allow them to interact. The concept of Machine to Machine integration in industrial and manufacturing applications overlaps with IoT to a large extent, so that both the terms can be used interchangeably, as both refer to the impact that such interconnected devices will have in the industrial world. Sensors are becoming significantly more performative and less expensive, enabling manufacturers to embed smart sensors in an increasing number of sophisticated devices and machines. These machines and devices are collecting and communicating more information than ever before. [5]b) Cloud-based application infrastructure and middlewareCloud computing is Internet-based computing that provides shared resources for computer processing and data to computers and other devices as demanded. It is a model for enabling ever present and on-demand access to a shared pool of configured computing resources (networks, storage, servers, applications and services),[7][8] which can be quickly provided and released with minimum effort. Cloud computing and storage solutions provide users and organizations with various capabilities to store and use their data in data centres owned privately or by third parties [9] that may be located far from the user–either from across a city to across the world. Such systems can serve as the IT backbone for factories of the future and for entire supply chains, especially when the systems enable seamless intra- and inter-factory integration and facilitate dynamic scaling of device integration and computing power according to the changing needs of the manufacturer. [8]c) Data AnalyticsBoth IoT and cloud-based technologies increase data generation and availability in manufacturing environments. For the manufacturing domain, this data will allow organizations to monitor and control all processes at a much higher level of detail. Previously unknown sources of incidents in shop floor processes will be identified, anticipated and prevented. The ad-hoc availability of such a large amount of data opens amazing new opportunities for new and innovative types of live analysis and visual representation. Batch-generated static reports are no longer state-of-the-art, as it becomes possible for users to view, chart, drill into and explore data flexibly in close to real-time, and as automated reasoning algorithms can now be applied to provide decisions that have in-process impact on manufacturing operation and optimization. [5]d) Smart RoboticsThe emergence of IT in the manufacturing domain not only introduces new solutions, such as IoT technologies, to this field of application, but also changes existing automation and control systems, especially robotics. For instance, human-robot co-working, which is possible by integrating safety sensors and safety mechanisms into robotic systems, combining the inherent flexibility of humans with the accuracy, precision, repeatability and performance of robots. In present production systems, work cell or line production is practiced commonly, in which individual workers or small teams operate various tasks in a bounded area using well-formed fixtures. Since recent market demands for simultaneous application of efficiency, agility and reliability are not satisfied by such systems, which are either operated solely by human ability or on fully automated lines. Robot cells, in which robot’s support humans in the execution of production tasks, are being developed to overcome this issue. [5]e) Additional factory of the future technologiesBesides these technologies, various other fields of research and development exist which might provide relevant solutions for the factory of the future, such as 3D printing, cognitive machines, augmented reality, wearable computing, exoskeletons, smart materials, advanced and intuitive programming techniques, or knowledge management systems. [5]SMART FACTORY FrameworkThe roadmap to making a smart factory can include several lines of actions named as smart solutions. Some of these as used in different areas are explained below.From Stores to machines via Cloud:Current logistics involve physical entry of raw material or BOP (Bought out Parts) in the stores, manual entry into ERP systems and formation of Master production of Schedule and CNC program installation on machines after every batch change. A smart solution would encompass1. Tagging of items on entry by RFID2. Updating of the ERP system3. MPS and WorkCentre scheduling by the ERP4. Information is passed on to respective WorkCentre’s by wireless communication.5. Auto sequencing of CNC program on the machine as per MPSAll the above information is stored on Cloud, which can also be linked with supplier database to keep updated.Benefits Associated—-The above solution will get rid of much of the headache associated with WorkCentre scheduling and cut costs by reducing the manpower required for production planning and control department. It will also reduce much non-value added work from planning so that they can focus on other issues much better.The automatic sequencing on the machine will also reduce setup times and improve productive.Automated Guided Vehicles:An automated guided vehicle (AGV) is a mobile robot that is based on a line follower concept using wires in the floor, or vision, magnets, or lasers for navigation. They are most often used in industrial applications to move materials around a manufacturing plant or warehouse. [10]The AGV’s can be used for raw materials, Work in progress (WIP) and finished goods requiringMovement of materials for long distancesRegular delivery of consistent loadsWhen on-time delivery is critical and late deliveries are causing inefficiencyProcesses where tracking of material is importantBenefits Associated—-An AGV system based on call system will implement E-Kanban with lean inventories. Inventories are a necessary evil which all industries focus on reducing, so a decreased inventory level will reduce the capital cost tied up. The inventory replenishment will also be better and chances of line starvation will reduce, improving available time for operations.Six Sigma with IOTThe Internet of Things (IoT) promises entirely new worlds of opportunity in many industries, but chief among them is the role that IoT and the machine-to-machine revolution is playing in manufacturing. The streamlined process, the end-to-end visibility, and the cost savings they deliver now and in the future means that technology is a small part of the story. In the big picture, the real change is visible in the approach to process. From hand-held devices to robotics and other innovations, the IoT advances deliver connectivity in an experiential framework that sets the customer at the centre of the operations, but also connects an organization’s employees. [12]The application of IoT, or machine to machine interaction can be done for automated quality inspections for critical parameters can provide live and constant feedback to the process for improvement and alignment towards the required process capabilities. Such seamless integration through IoT also keeps the subsequent machine sensitive to input parameters.Benefits AssociatedMachine to machine interaction ensures tighter control on output parts and realisation of achieving Six Sigma QualityDigital Utilities and Predictive MaintenanceIn the traditional factory, only a handful of key performance indicators were manually picked to be monitored. Then, a rule-based set of rigid threshold alerts was pre-calibrated by process control engineers. There’s a wealth of data that’s generated between these pre-fixed thresholds – data that could help you see what happens with your machines always, notice when things are starting to go south, and do something about it before you lose machine uptime. But this wealth of data gets ignored and discarded.Considering the number of assets that utilities are responsible for — machines, turbines, transformers, pumps, vehicles, kilometres of pipes and cables — and the risks associated with failure of such assets, a reliable maintenance strategy is a priority for them.In a quest to ensure reliability of such assets, utilities have progressed from primarily a reactive, break and fix and “repair” approach, toward a preventive maintenance approach. The basic principle of a smart factory is that by connecting machines, components and systems, we create intelligent, interlinked networks along the entire supply chain, which can control each other autonomously.The algorithms in a smart factory obtain a combination of health information from various sensors. They determine the condition of in-service equipment, and predict when maintenance work needs to be performed. Alerts about required maintenance tasks are triggered at optimal times, promising significant cost saving.In other words, transitioning from the traditional factory to the smart factory means no more preventive maintenance, which often requires significant, unnecessary expenses. No more replacing perfectly good parts when it’s not actually required, just because it’s on the schedule.Transitioning to a smart factory means letting intelligence systems with a deep understanding of every machine in your fleet, and the relationship between them, make predictions and prescribe courses of action. [13]Power and utility costs are one of the biggest part of running expenditure of any plant or factory.Going one step further digitizing all utilities and using cloud computing and data analytics to control them, gives tremendous opportunity to autonomously cut excessive loads in electricity, compressed air and water. This can result in huge savings in energy costs.It will also render greater control, flexibility and adaptability of plant’s energy resources.In INDIA :The government’s ‘Make in India’ campaign is aimed at facilitating investments, encouraging innovation and building high-class manufacturing infrastructure is expected to boost manufacturing activities in key sectors.[15]India's first very own smart factory, is under progress at the Indian Institute of Science's (IISc) Centre for Product Design and Manufacturing (CPDM) with seed funding from The Boeing Company at Bangalore. [16]CONCLUSION -The factory of the future will deliver customized products on pull demand with better quality, while still taking advantage of the economies of scale and offering human-centered jobs, along with cyber-physical systems to enable smart manufacturing. New manufacturing processes will address the challenges of sustainability, flexibility, innovation, and quality requirements in human-centric manufacturing. Future infrastructures will support access to information everywhere and always without the need for any specific installation of parameterization. Production resources will manage themselves autonomously and will connect to one another (M2M), while products will know their own appropriate production systems. This is where the digital and real worlds will merge. [5]REFERENCES[1] D.-H. Shin, Ubiquitous city: Urban technologies, urban infrastructure and urban informatics, Journal of Information Science, vol.35, no.5, Sage Publications, pp.515–526, 2009.[2] Kagermann, H., W. Wahlster and J. Helbig, eds., 2013: Recommendations for implementing the strategic initiative Industrie 4.0: Final report of the Industrie 4.0 Working Group[3] BMBF-Internetredaktion (2016-01-21). "Zukunftsprojekt Industrie 4.0 - BMBF". Bundesministerium für Bildung und Forschung - BMBF. Retrieved 2016-11-30.[4] Hermann, Pentek, Otto, 2016: Design Principles for Industrie 4.0 Scenarios, accessed on 4 May 2016[5] White Paper on Factory of the Future by IEC[6] On the Journey to a Smart Manufacturing Revolution". IndustryWeek. Retrieved 2016-02-17.[7] Hassan, Qusay (2011). "Demystifying Cloud Computing" (PDF). The Journal of Defense Software Engineering. CrossTalk. 2011 (Jan/Feb): 16–21. Retrieved 11 December 2014.[8] Peter Mell and Timothy Grance (September 2011). The NIST Definition of Cloud Computing (Technical report). National Institute of Standards and Technology: U.S. Department of commerce. doi:10.6028/NIST.SP.800-145. Special publication 800-145.[9] M. Haghighat, S. Zonouz, & M. Abdel-Mottaleb (2015). CloudID: Trustworthy Cloud-based and Cross- Enterprise Biometric Identification. Expert Systems with Applications, 42(21), 7905–7916.[10] Automated guided vehicle - Wikipedia[11] Industrial Manipulators and Material Handling Solution[12] Six Sigma and IoT Brings Opportunity - business.com[13] Article on The digital utility: New opportunities and challenges By Adrian Booth, Niko Mohr, and Peter Peters ( Mckinsey & Company)[14] http://www.genewsroom.com/press-releases/ge-introduces-digital-power-plant-steam-enhance-efficiency-and-reduce-emissions-coal[15] Digitalisation and smart manufacturing: The way ahead to a sustainable India[16] Industry 4.0: IISc building India’s 1st smart factory in Bengaluru - Times of India[17] The Dawn of the Smart Factory
What are the United States kinetic ASAT capabilities?
Kinetic Energy Anti-Satellite (KE ASAT) program was intended to provide the United States with the capability to interdict hostile satellites. The KE ASAT consisted of missile and weapon control subsystems. The major components of the missile subsystem are the booster, kill vehicle, shroud, and launch support system. The weapon control subsystem is composed of a battery control center and a mission control element which perform readiness and engagement planning, command and control.The objective of this program was to define, develop, integrate and test the necessary Kill Vehicle (KV), weapon control subsystem component and subsystems technologies to demonstrate hit to kill performance, with debris mitigation, against hostile satellites. The government awarded a contract to Boeing North American, Incorporated, Rocketdyne Division, Canoga Park, CA as a follow-on effort to a contract which was competitively awarded in 1990. The contract exploits prior effort by a phase which will include prototype hover testing and an option for flight testing. The purpose of the effort was to directly pursue development work of the contractor hardware and software together with testing since 1990, via a follow-on development phase.This effort consisted of a hover test of the prototype KV; hardware-in-the-loop (HWIL) testing of all elements of the KE ASAT system; upgrades to tactical performance and flight qualification of the prototype KV subsystems; and debris mitigation and system integration testing to validate the system elements. Data to support the DOD Space Control Architecture study will also be provided through simulation runs and system performance estimates. Testing of the KV seeker on an airborne platform was investigated to gather seeker performance data that would normally be demonstrated during flight testing.A hover test of the prototype KV was conducted in August 1997 at the National Hover Test Facility to demonstrate the full-up KV free flight performance. Air bearing testing of the flight qualified KV will be conducted to allow validation of the closed-loop operation of the complete KV with actual flight software. The Weapons Control Subsystem (WCS) will be upgraded at the Army Space Operations Center (ARSPOC) to include: a Mission Control Element (MCE), Battery Control Center (BCC), and Communications Network (CN).The production of additional kill vehicles and purchase of additional boosters was to be undertaken in 1998 and 1999. As a result, by 2000, the United States was intended to have a User Operational Evaluation System (UOES) contingency capability of 10 KE-ASATs ready for use if needed, at a total cost of $205 million for the 4 years from FY96 through FY99. Projected funding is $30 million for FY96, $50 million for FY97, $80 million for FY98, and $45 million for FY99.On 28 February 2000, the Army informed Boeing that it was the intention of the government to restructure and redirect the efforts on the KE-ASAT program, incuding a halt om the fabrication, assembly, and test of the kill vehicles at a logical stopping point. However, by mid-March 2000 the February directive had been rescinded, with no no decision by the government to restructure or redirect the KE-ASAT program.As of mid-2001 three prototypes had been built, and all three remained in storage at a Boeing facility in Anaheim, CA.As of mid-2001 there were reports that the program might be transferred from the Army to the Navy.The Department of Defense invested about $350.0 million in KEASAT technology throughout the 1990s and substantial progress was made in the development of KEASAT hardware and software.The Kinetic Energy Anti-Satellite (KE-ASAT) Program had been under technology development since 1989 using various configuration architectures to better counter the enemy satellite threat. Over the course of technology development and the continuous evolution of the threat, the KE-ASAT Program has undergone numerous changes in vehicle design, vehicle hardware development, software design and development, and the overall mission requirements. The program was transferred to the Aviation & Missile Research, Development, and Engineering Center (AMRDEC) in 2002. Work activities are performed by Davidson Technologies Inc. (DTI) in Huntsville, Alabama in direct support to the AMRDEC KE-ASAT Program Office.The contractor supports an ASAT Ground and Flight Test utilizing Real-time simulations (RTSims) and/or Hardware-in-the-loop (HWIL) to represent elements in the KE-ASAT system. The contractor will conduct the test in an integrated real-time configuration, through the use of simulated real-time environments. The contractor provides a Launch Ground Support Subsystem (LGSS) to support flight tests. The contractor provides the support services in the initiation of tests, display of air vehicle events, monitoring of the countdown sequence, generate engagement data for launch, and receive data from the Test Range assets. The contractor performs flight test analyses and supporting all test range activities to include site selection, safety analysis, and trajectory analysis.Miltec Corp.*, Huntsville, Ala., was awarded on May 24, 2004, a $4,000,000 increment as part of a $12,382,520 firm-fixed-price contract for an Army counterspace technology testbed. Work will be performed in Iuka, Miss. (65 percent) and Huntsville, Ala. (35 percent), and is expected to be completed by May 30, 2006. Contract funds will not expire at the end of the current fiscal year. There were five bids solicited on April 8, 2004, and one bid was received. The U.S. Army Aviation and Missile Command, Redstone Arsenal, Ala., is the contracting activity (W31P4Q-04-F-R019).The Space Control Test Capability (SCTC) contractor provides specialized engineering tasks and products to the Space Control Test Capability (SCTC) Initiative Office, Applied Technology Initiatives Directorate, US Army AMRDEC (Aviation and Missile Research, Development and Engineering Center, US Army Aviation and Missile Command). The contractor supports the government office by participating in an IPT (Integrated Product Team) management structure to assist in monitoring SCTC work progress. The contractor utilizes the existing System Integration Framework (SIF) to develop and maintain a counter space system planning capability to study effectiveness and interoperation of potential counter space technologies. The contractor will provide support for tests and exercises necessary to evaluate the capability of candidate counter space technologies to support wartime operations.
- Home >
- Catalog >
- Life >
- Parenting Chart >
- Baby Feeding Chart >
- Baby Feeding Schedule >
- baby feeding schedule solids >
- Software Configuration Management Plan - U.S. Department Of Energy