How to Edit Your Nm Substitute W-9 Form Online Free of Hassle
Follow the step-by-step guide to get your Nm Substitute W-9 Form edited for the perfect workflow:
- Hit the Get Form button on this page.
- You will go to our PDF editor.
- Make some changes to your document, like signing, highlighting, and other tools in the top toolbar.
- Hit the Download button and download your all-set document into you local computer.
We Are Proud of Letting You Edit Nm Substitute W-9 Form With a Streamlined Workflow
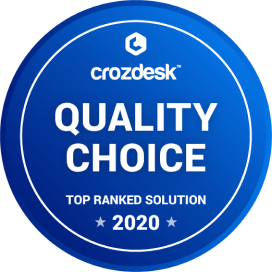
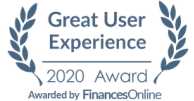
How to Edit Your Nm Substitute W-9 Form Online
If you need to sign a document, you may need to add text, put on the date, and do other editing. CocoDoc makes it very easy to edit your form into a form. Let's see the easy steps.
- Hit the Get Form button on this page.
- You will go to our online PDF editor webpage.
- When the editor appears, click the tool icon in the top toolbar to edit your form, like inserting images and checking.
- To add date, click the Date icon, hold and drag the generated date to the target place.
- Change the default date by changing the default to another date in the box.
- Click OK to save your edits and click the Download button to use the form offline.
How to Edit Text for Your Nm Substitute W-9 Form with Adobe DC on Windows
Adobe DC on Windows is a useful tool to edit your file on a PC. This is especially useful when you prefer to do work about file edit in the offline mode. So, let'get started.
- Click the Adobe DC app on Windows.
- Find and click the Edit PDF tool.
- Click the Select a File button and select a file from you computer.
- Click a text box to optimize the text font, size, and other formats.
- Select File > Save or File > Save As to confirm the edit to your Nm Substitute W-9 Form.
How to Edit Your Nm Substitute W-9 Form With Adobe Dc on Mac
- Select a file on you computer and Open it with the Adobe DC for Mac.
- Navigate to and click Edit PDF from the right position.
- Edit your form as needed by selecting the tool from the top toolbar.
- Click the Fill & Sign tool and select the Sign icon in the top toolbar to customize your signature in different ways.
- Select File > Save to save the changed file.
How to Edit your Nm Substitute W-9 Form from G Suite with CocoDoc
Like using G Suite for your work to complete a form? You can integrate your PDF editing work in Google Drive with CocoDoc, so you can fill out your PDF to get job done in a minute.
- Go to Google Workspace Marketplace, search and install CocoDoc for Google Drive add-on.
- Go to the Drive, find and right click the form and select Open With.
- Select the CocoDoc PDF option, and allow your Google account to integrate into CocoDoc in the popup windows.
- Choose the PDF Editor option to open the CocoDoc PDF editor.
- Click the tool in the top toolbar to edit your Nm Substitute W-9 Form on the specified place, like signing and adding text.
- Click the Download button to save your form.
PDF Editor FAQ
Why does my Tio2 coating on mild steel come off after drying?
ABSTRACTIn this work carbon steel plates were dip-coated with a composite film obtained from a colloidal suspension of Ni-TiO2. Suspensions with different solids contents were used to evaluate the adherence of the film and the microstructural features. The samples were characterized using both optical and scanning electron microscopy, energy dispersive spectroscopy and microhardness. The microstructural analysis revealed that the films have high porosity at the surface. However, an interfacial region was observed demonstrating that there was good adhesion between both materials. This region shows an increased hardness that can be attributed to diffusion mechanism of nickel from the composite film to the steel matrix. Besides the interface, there was an abnormal grain growth, followed by a region of smaller grains of austenite and at longer distances near the center of the plate some colonies of pearlite appear.Keywords: Rheology; Metal oxide composite coatings; DippingBackgroundThe processing of materials from powders has several advantages over deformation methods such as the easy tailoring of the microstructure, the adequate control of chemical composition and the possibility to produce ceramic-metal composites. However, the production steps comprising the preparation of raw materials (powders + additives), forming, sintering, calibration, and limitations regarding with the size and geometry of the components makes powder processing to be a complex process with enhanced cost at any stage, which limits the choice of this route1. Within this context, there are several techniques for obtaining metallic and ceramic components, the main being pressing, extrusion, forging and other metallurgical techniques that are performed under dry conditions. However, another feasible route for the production of complex parts with uniform microstructures is those based on colloidal routes2, 3.Colloidal processing comprises the preparation of a homogeneous mixture of powders in a liquid medium (organic or preferably water) to form a stable suspension where the repulsive forces impede the tendency to agglomerate due to van der Waals forces keeping the particles well dispersed in the suspension. Some popular techniques for shaping powders into bulk bodies, substrates, and coatings include slip casting, tape casting and dipping, respectively2-9. The components produced by these routes can have a great variety of shapes and sizes and meet the requirements for a broad number of applications in many sectors like microelectronics, structural, biological and photocatalysis, to mention only a few10. The deposition of thin films of nanocomposites with colloidal particles is commonly performed by dip-coating. Dipping allows us to produce coatings with thicknesses of an order of magnitude of few microns and permits a desirable control of composition, density and hardness after sintering5,9,10.The coating of nickel matrix composites with high density and tailored microstructures having new interesting properties has been studied recently using different approaches, one of the most interesting being the use of colloidal routes11,12. Several works have reported the rheology, the electrolytic properties and the interactions between phases in metal-ceramic composites with oxides as ceramic reinforcing phase, mainly Al2O3, SiO2, ZrO2and TiO2for applications as electrodes13for fuel cells and structural components14. Among the nanoparticles of the second phase mentioned above, titania is widely used as a photocatalytic agent, in biomedical devices, as well as hardening of a metallic matrix to enhance the strength and stiffness of structural components15-18. In this context, this work aimed to evaluate the production of composite coatings of nickel reinforced with titania nanoparticles produced by immersion in aqueous suspensions of Ni-TiO2mixtures without additives.METHODSA micron sized powder of nickel (T110, INCO, Canada) and a nanotitania suspension (Aerodisp W 740X, Degussa-Evonik, Germany) with mean particle sizes of 2.5 µm and 40 nm and densities of 8.7 and 4.2 Registered & Protected by MarkMonitor-3respectively, were used. Aqueous suspensions of Ni/TiO2mixtures with concentrations of 1.0, 3.0, and 5.0 vol.% (0.5, 1.5, and 2.5 wt%, respectively) of nanotitania were prepared to final solids contents of 30 vol.% using deionized water. According to previous studies2suspensions were stabilized with 1 wt% commercial polyacrylic acid based polyelectrolyte (Duramax D-3005, Rohm and Haas, USA) adding tetramethyl ammonium hydroxide (TMAH) up to pH 10 to prevent degradation of the powder. Suspensions were prepared by ultrasonic mixing using a 400 W sonication probe (Dr. Hielscher U400S, Germany) for 3 min and further stirring for 1 h. Rheological characterization was carried out using a rheometer RS50 (ThermoHaake, Germany) with a double-cone/plate sensor configuration (DC60/2°, ThermoHaake, Germany) and a testing temperature of 25°C. Flow behavior was measured under controlled rate conditions employing a measuring program in three stages; first a linear increase of shear rate from 0 to 1000s-1in 3 min; a plateau at the maximum shear rate (1000s-1) for 30s, and a decrease to zero shear rate in 3 min.Commercially available sheets of low carbon content steel AISI 1020 were used as coating substrates. The microstructure of the carbon steel sheet used as substrate material of the composite layer of Ni-TiO2is shown in Figure 1. It can be seen that it has a homogeneous microstructure with little variability in grain size comprising predominantly ferritic matrix with a few colonies of pearlite in the grain boundaries with a random distribution.Figure 1 Steel sheet substrate before any heat treatment.Single coatings of Ni-TiO2were obtained by dipping at a withdrawal rate of 10 mm⋅s-1. Every formed layer was weighted after 24h drying in air at room temperature. Green samples were sintered under Ar/5% H2flowing atmosphere using a two-step heat treatment, with a first ramp from room temperature to 500°C in 40 min to allow deflocculant burnout and a second step from 500°C to 900°C in 1 h. The final microstructure of the sintered bodies was observed by optical and scanning electron microscopy SEM (Leica DM4000M, Germany, and Phillips XK30, respectively, Netherlands). Sintered samples were observed on polished surfaces after chemical etching (Nital reagent). Present phases in the composite coating layer were identified by X-ray diffraction using a X’Pert (Philips, Netherlands) apparatus with a Cu (λ = 1.54 Å) target and a Ni filter at 0.02° (2θ/s) scanning speed. For analysis at different depths, the material was removed using fine sandpaper (1200 particles per square). Vickers hardness was determined for the coating and matrix samples using a microdurometer (Shimadzu HMV–2, Japan). The results were obtained from an average of 10 measurements.RESULTS AND DISCUSSIONSFigure 2 shows the flow curves obtained from the rheological measurements of the suspensions with a solids content of 30 vol.% and different concentrations of TiO2. The results show that the suspensions have a pseudoplastic behavior with the presence of a negligible yield stress, which indicates that a very good dispersion condition. Another important feature is the absence of thixotropy, which allows us to assume that the deflocculation process has been successful to prevent attraction interactions (van der Waals forces) among the particles. These results are characteristic of well-dispersed suspensions with high solids concentration.Figure 2 Flow curves of 30 vol.% suspensions of Ni-TiO2 mixtures with different TiO2 contents (vol.%).From the flow behavior the influence of the concentration of nanoparticles of titania on the viscosity of the suspensions can be drawn, as shown in Figure 3 for viscosity values taken at a shear rate of 50s-1. Observing the figure it is noted that increasing amounts of TiO2nanoparticles lead to a square root increase of the viscosity values. The viscosity values increase can then be attributed to the lack of affinity between the ammonium polyacrylate and organic compounds components of the titania suspension. These nanoparticles remain in the liquid medium, promoting thickening of the suspension, as it increases the concentration of nanoparticles.Figure 3 Apparent viscosity of the suspensions of Ni-TiO2 mixtures with different TiO2 contents.Steel substrates were dip-coated with these suspensions and further sintered at 900ºC/1h. After sintering, nanostructured coatings were obtained. Homogeneous, crack-free coatings with a relatively high porosity (Figure 4) were obtained in which titania nanoparticles are very well distributed around the surface of Ni particles. The microstructure may be divided into three well-defined regions as shown in the SEM pictures presented in Figure 5. The outer surface consists of a porous layer of the Ni-TiO2coating. The second region shows the existence of a connection interface between the composite coating and the substrate. This presents a clear path for diffusion of nickel atoms in the grain boundaries of the steel substrate during sintering. The maintenance of the sample for increasing times in the furnace enabled atoms of nickel to penetrate into the crystal lattice of iron forming the third region of the microstructure.Figure 4 Microstructure of Ni-TiO2 composite coatings at different magnification. (a,b) Ni-1%TiO2; (c, d) Ni-3%TiO2 and; (e, f) Ni-5%TiO2.Figure 5 Microstructure distribution of the Ni-1%TiO2 composite. (a) First, second and third regions of the superficial microstructure. (i) Ni-TiO2 composite coating, (ii) Diffusion zone and; (iii) Large grains; (b) Full Ni-1%TiO2 composite microstructure. (iv) Ferrite grains and; (v) Ferrite-Pearlite grains.The substrate showed significant microstructural changes after sintering of the composite coating. As can be noted, there was an increase in grain size in the first layer of the substrate microstructure attributed to the formation of austenite (Fe-γ), characterized by coarser and polyhedral grains. The formation of this microstructure is due to the typical nickel atoms diffusion process into the iron lattice crystalline, which is accelerated by high temperature. Nickel is gammagene element which enables the presence of austenite at room temperature. Furthermore, the inferior layers of the microstructure also underwent changes due to the migration of nickel into the steel. The austenite is able to absorb carbon atoms in their crystal structure about 2.0wt%. This means that colonies of pearlite dissolve the free carbon migrate to the surface and saturate the austenite. Consequently, it can be observed an intermediate region of ferrite (Fe-α) and a combination of ferrite-pearlite composing the original microstructure of the steel19,20.The high viscosity of the Ni-TiO2suspensions, influenced the adhesion during the formation of the coating. This effect is shown in Figure 6. Despite their high porosity the coatings with concentrations of nanoparticles of up to 3.0 vol.% showed a good adherence to the substrate (Fig. 6 (a) and (b)). However, the addition of 5.0 vol% of nanoparticles led to poor adherence and the layer peels out (Fig. 5 (c)). This lack of adherence can be explained primarily by the greater viscosity of the Ni-5%TiO2suspension that leads to thicker coatings and faster drying, thus affecting the anchoring on the steel surface.Figure 6 Influence of the nanotitania content on the adhesion of the coating and the final porosity of the Ni-TiO2 composites. (a) Ni-1%TiO2; (b) Ni-3%TiO2; (c) Ni-5%TiO2 and; (d) porosity evolution according to the nano-TiO2 content.Microhardness measurements were performed in different regions of the microstructure: within the coating and at the interface with the substrate. Table 1 shows the correlation between the microhardness values profile and the titania content in the Ni-TiO2composites for the three distinct regions of the microstructure after sintering. The first column presents measurements from the surface where the coating is situated. It is evident that the increase of the values is due to the increasing concentration of nanoparticles, since the coating has high porosity and influence of this factor is already being considered in the measurement. The second column refers to the intermediate layer adhered to the substrate. The results show that there was a tendency of the hardness to decrease with increasing titania content. This can be explained correlating the amount of coverage provided to the nanoparticles over nickel particles. These results suggest that the higher the concentration of nanoparticles promotes a thicker nanotitania coating and consequently, the lowest rate of diffusion of nickel into the steel matrix carbon. Finally the results obtained for the substrate show that it was not affected by the composite coating.Table 1 Vickers microhardness values of the Ni-TiO2 composites.TiO2content(vol. %)Vickers hardness (GPa)CoatingInterfaceSubstrate10.77 ± 0.031.77 ± 0.201.05 ± 0.0130.80 ± 0.081.70 ± 0.481.04 ± 0.0150.89 ± 0.051.63 ± 0.241.07 ± 0.01To identify the phases present in the microstructure the sintered samples were analysed by X-ray diffraction following this methodology: first, the surface layer was scanned and made some removal of material by grinding and new scans were further made. The results are shown in Figure 7. Figure 7a shows all grouped diffractograms. The peaks of Fe and Ni are mixed with each other because they are very close. The sintering process promoted the composite coating consolidation and performs a mechanism of homogenization and formation of intermediate phases. Firstly, in the first layer, peaks were identified as pure nickel and a nickel-rich intermetallic compound FeNi3(Figure 7b). In a lower region, between the coating and the substrate, the formation of a stoichiometric compound rich in iron, Fe0,64Ni0,36(Figure 7c), which is not present in the equilibrium phase diagram can also be identified. With further grinding only Fe peaks were observed (Figure 7d). Finally, the peaks of pure nickel show a slight enlargement. This can be attributed to the formation of substitutional solid solution from the migration of iron atoms to the crystalline lattice of the nickel.Figure 7 X-Ray diffraction. (a) Whole sample; (b) Surface coating; (c) Second layer; and (d) Substrate.CONCLUSIONSA study of the dip-coating process of low carbon steel plated with Ni-TiO2composite by colloidal route was made. The results obtained from the rheological behavior showed that the viscosity of the suspensions increases in the presence of nanoparticles. The final microstructure obtained was divided into three regions: the coating showed the TiO2nanoparticles covering the Ni particles. The formation of an interface comprising Fe-Ni was formed during sintering. In this case, the nanoparticles promote a reduction in the diffusivity of atoms of nickel to the substrate during the sintering step. In the third region, i.e. the substrate, the observed formation of a layer of coarse grains suggests that it is formed by austenite. This region has absorbed carbon contained in the pearlite microstructure of steel, changing the final microstructure of the substrate, which shows coarse grains, a ferritic region and finally again the presence of perlite. The microhardness value obtained slightly changed between the different regions. The coating obtained the lowest results, the substrate showed intermediate values similar to those of uncoated substrates, whereas the highest values were obtained at the interface, which is related to the formation of a compound of the Fe-Ni substitutional solid .
How does global warming affect humans?
SNOWFALL Will Signal The Death Of The Global Warming MovementSadly this is now a theoretical question as the evidence increases that there is no global warming underway and the past 100 years has just been natural climate variability. Snowfall is according to the UN models evidence of cooling not warming and the world sees early winters that last longer with record snowfall.While warming causes more precipitation the warming does not cause freezing necessary to turn rain into snow. Freezing is the driver of snowfall.What Models Say:♦ IPCC TAR (2001): “Milder winter temperatures will decrease heavy snowstorms“♦ Kunkel et al., 2002: “Surface conditions favorable for heavy lake-effect snow decreased in frequency by 50% and 90% for the HadCM2 and CGCM1 [models], respectively, by the late 21st Century. This reduction was due almost entirely to … an increase in average winter air temperatures.”♦ IPCC AR4 (2007): “Snow season length and snow depth are very likely to decrease in most of North America“♦ Kapnick and Delworth, 2013: “In response to idealized radiative forcing changes, both models produce similar global-scale responses in which global-mean temperature and total precipitation increase while snowfall decreases. … By using a simple multivariate model, temperature is shown to drive these trends by decreasing snowfall almost everywhere” (press release) “In North America, the greatest reductions in snowfall will occur along the northeast coast, in the mountainous west, and in the Pacific Northwest. Coastal regions from Virginia to Maine … will get less than half the amount of snow currently received.”Defying IPCC Models, U.S. Blizzard Frequency Has Nearly Quadrupled Since 1960, As U.S. Continues CoolingVERY MUCH POSITIVE EFFECT. Unless you deny climate history and natural variation the evidence is obvious that warming is always superior to cooling. The earth’s climate is chaotic and non-linear and has always changed from hot to cold over long time lines measured in millions of years.There are only two alternatives for climate on the earth - a HOT BOX or an ICE BOX.Surely there is no debate about the very positive effects of global warming when compared to the alternative of surviving an Ice age as our ancestors have done? and most species prosper when the climate blows hot and suffer horribly when the climate blows cold. In fact our civilization today has been possible only because of global warming blowing us out of the Little Ice Age.HOW GLOBAL WARMING MADE CIVILIZATION POSSIBLEIn fact increased Co2 from our fossil fuels although small compared to the whole atmosphere has been entirely beneficial. There is no evidence that Co2 has any effect on the climate as the so called greenhouse effect is false.Earth’s temperature rises in the past have always preceded a rise in CO2 by a few hundred years, not as Al Gore would have you believe, caused it.In an El Nino year, Water vapour is 4% of the atmosphere can rise to 5% and CO2 from 0.39 to 0.42. Human made CO2 would remain about the same in that year.Don't Tell Anyone, But We Just Had Two Years Of Record-Breaking Global Cooling5/16/2018Inconvenient Science: NASA data show that global temperatures dropped sharply over the past two years. Not that you'd know it, since that wasn't deemed news. Does that make NASA a global warming denier?Writing in Real Clear Markets, Aaron Brown looked at the official NASA global temperature data and noticed something surprising. From February 2016 to February 2018, "global average temperatures dropped by 0.56 degrees Celsius." That, he notes, is the biggest two-year drop in the past century."The 2016-2018 Big Chill," he writes, "was composed of two Little Chills, the biggest five month drop ever (February to June 2016) and the fourth biggest (February to June 2017). A similar event from February to June 2018 would bring global average temperatures below the 1980s average."https://www.investors.com/politics/editorials/climate-change-global-warming-earth-cooling-media-bias/The temperature has been cooling for the past 7000 years with its saw tooth up and down progress. There was a nice warming after the Little Ice Age but that has stopped for the past two decades. The wavy jet stream in 2019 has brought freezing winters with massive snowfall here Japan and Asia.Tourists are amazed to see 52 feet of fresh snow in the mountains in Japan.There is no correlation between gobal temperatures over the past 40 years and Co2 demolishing the Al Gore fear mongering of a climate crisis from the planet getting too hot.Co2 is the air we breath out at 35,000 ppm with every breath. It is necessary for life on the planet through the process of photosynthesis converting radiant energy to chemical.Figure 2.3: Photosynthesis: In the process of photosynthesis, plants convert radiant energy from the sun into chemical energy in the form of glucose - or sugar.Water (6H2O) + carbon dioxide (6 CO2) + sunlight (radiant energy) = glucose (C6H12O6) + Oxygen (6O2).Credit: Energy Explained Penn State University.Photosynthesis is the transformation of radiant energy to chemical energy.Plants take in water, carbon dioxide, and sunlight and turn them into glucose and oxygen. Called photosynthesis, one of the results of this process is that carbon dioxide is removed from the air. It is nature's process for returning carbon from the atmosphere to the earth.The "fossil fuels" we use today (oil, coal, and natural gas) are all formed from plants and animals that died millions of years ago and were fossilized. When we burn (combust) these carbon-rich fuels, we are pulling carbon from the earth and releasing it into the environment.Radiant to ChemicalBenefits of more atmospheric CO2:1. Higher agricultural yields2. Richer biodiversity3. Faster growth rates of crops and forests4. More phytoplankton (responsible for marine photosynthesis)5. More diatoms, the “base” of the marine food chain6. More reef-building coral7. More and healthier crustaceans and mollusksBy HARRISON H. SCHMITT AND WILLIAM HAPPERMay 8, 2013 6:37 p.m. ETOf all of the world's chemical compounds, none has a worse reputation than carbon dioxide. Thanks to the single-minded demonization of this natural and essential atmospheric gas by advocates of government control of energy production, the conventional wisdom about carbon dioxide is that it is a dangerous pollutant. That's simply not the case. Contrary to what some would have us believe, increased carbon dioxide in the atmosphere will benefit the increasing population on the planet by increasing agricultural productivity.The cessation of observed global warming for the past decade or so has shown how exaggerated NASA's and most other computer predictions of human-caused warming have been—and how little correlation warming has with concentrations of atmospheric carbon dioxide. As many scientists have pointed out, variations in global temperature correlate much better with solar activity and with complicated cycles of the oceans and atmosphere. There isn't the slightest evidence that more carbon dioxide has caused more extreme weather.The current levels of carbon dioxide in the earth's atmosphere, approaching 400 parts per million, are low by the standards of geological and plant evolutionary history. Levels were 3,000 ppm, or more, until the Paleogene period (beginning about 65 million years ago). For most plants, and for the animals and humans that use them, more carbon dioxide, far from being a "pollutant" in need of reduction, would be a benefit. This is already widely recognized by operators of commercial greenhouses, who artificially increase the carbon dioxide levels to 1,000 ppm or more to improve the growth and quality of their plants.Using energy from sunlight—together with the catalytic action of an ancient enzyme called rubisco, the most abundant protein on earth—plants convert carbon dioxide from the air into carbohydrates and other useful molecules. Rubisco catalyzes the attachment of a carbon-dioxide molecule to another five-carbon molecule to make two three-carbon molecules, which are subsequently converted into carbohydrates. (Since the useful product from the carbon dioxide capture consists of three-carbon molecules, plants that use this simple process are called C3 plants.) C3 plants, such as wheat, rice, soybeans, cotton and many forage crops, evolved when there was much more carbon dioxide in the atmosphere than today. So these agricultural staples are actually undernourished in carbon dioxide relative to their original design.At the current low levels of atmospheric carbon dioxide, rubisco in C3 plants can be fooled into substituting oxygen molecules for carbon-dioxide molecules. But this substitution reduces the efficiency of photosynthesis, especially at high temperatures. To get around the problem, a small number of plants have evolved a way to enrich the carbon-dioxide concentration around the rubisco enzyme, and to suppress the oxygen concentration. Called C4 plants because they utilize a molecule with four carbons, plants that use this evolutionary trick include sugar cane, corn and other tropical plants.Although C4 plants evolved to cope with low levels of carbon dioxide, the workaround comes at a price, since it takes additional chemical energy. With high levels of carbon dioxide in the atmosphere, C4 plants are not as productive as C3 plants, which do not have the overhead costs of the carbon-dioxide enrichment system.That's hardly all that goes into making the case for the benefits of carbon dioxide. Right now, at our current low levels of carbon dioxide, plants are paying a heavy price in water usage. Whether plants are C3 or C4, the way they get carbon dioxide from the air is the same: The plant leaves have little holes, or stomata, through which carbon dioxide molecules can diffuse into the moist interior for use in the plant's photosynthetic cycles.The density of water molecules within the leaf is typically 60 times greater than the density of carbon dioxide in the air, and the diffusion rate of the water molecule is greater than that of the carbon-dioxide molecule.So depending on the relative humidity and temperature, 100 or more water molecules diffuse out of the leaf for every molecule of carbon dioxide that diffuses in. And not every carbon-dioxide molecule that diffuses into a leaf gets incorporated into a carbohydrate. As a result, plants require many hundreds of grams of water to produce one gram of plant biomass, largely carbohydrate.Driven by the need to conserve water, plants produce fewer stomata openings in their leaves when there is more carbon dioxide in the air. This decreases the amount of water that the plant is forced to transpire and allows the plant to withstand dry conditions better.Crop yields in recent dry years were less affected by drought than crops of the dust-bowl droughts of the 1930s, when there was less carbon dioxide. Nowadays, in an age of rising population and scarcities of food and water in some regions, it's a wonder that humanitarians aren't clamoring for more atmospheric carbon dioxide. Instead, some are denouncing it.We know that carbon dioxide has been a much larger fraction of the earth's atmosphere than it is today, and the geological record shows that life flourished on land and in the oceans during those times. The incredible list of supposed horrors that increasing carbon dioxide will bring the world is pure belief disguised as science.Mr. Schmitt, an adjunct professor of engineering at the University of Wisconsin-Madison, was an Apollo 17 astronaut and a former U.S. senator from New Mexico. Mr. Happer is a professor of physics at Princeton University and a former director of the office of energy research at the U.S. Department of Energy.*****************************************************************************************Effects of increased CO2 on plants and cropsA 1993 review of scientific greenhouse studies found that a doubling of CO2concentration would stimulate the growth of 156 different plant species by an average of 37%. Response varied significantly by species, with some showing much greater gains and a few showing a loss. For example, a 1979 greenhouse study found that with doubled CO2 concentration the dry weight of 40-day-old cotton plants doubled, but the dry weight of 30-day-old maize plants increased by only 20%. [70 [71]In addition to greenhouse studies, field and satellite measurements attempt to understand the effect of increased CO2 in more natural environments. In free-air carbon dioxide enrichment (FACE) experiments plants are grown in field plots and the CO2 concentration of the surrounding air is artificially elevated. These experiments generally use lower CO2 levels than the greenhouse studies. They show lower gains in growth than greenhouse studies, with the gains depending heavily on the species under study. A 2005 review of 12 experiments at 475-600 ppm showed an average gain of 17% in crop yield, with legumes typically showing a greater response than other species and C4 plants generally showing less. The review also stated that the experiments have their own limitations. The studied CO2 levels were lower, and most of the experiments were carried out in temperate regions.[72]Satellite measurements found increasing leaf area index for 25% to 50% of Earth's vegetated area Earth over the past 35 years, providing evidence for a positive CO2 fertilization effect.[73] [74] W.C02 Toxicity ResearchCarbon dioxide (CO2) is one of the inputs of photosynthesis and as such CO2plays an important role in increasing crop productivity (Hand 1993, Rijkdjik and Houter 1993). Optimal CO2 concentrations for the greenhouse atmosphere fall with the range of between 700 to 900 ppm (parts per million) (Romero-Aranda et al 1995, Tremblay and Gosselin 1998). Crop productivity depends not only on efficiency of interception of light but also on the efficiency with which light is converted to chemical energy in photosynthesis. Carbon dioxide enrichment to 1200 ppm increases the maximum conversion efficiency by a substantial amount (between 28 to 59%) (Wilson et al 1992). Photosynthetic efficiencies appear never to exceed about 22 % of the absorbed light energy in the 400 to 700 nm range, the maximum efficiency is obtained at relative low light intensities, not in brightest sunlight (Salisbury and Ross 1978). Considering the supply of light to available land area on which a crop is growing, the overall yield efficiencies are always much below 22% (Salisbury and Ross 1978).The use of CO2 in greenhouses can give light use efficiencies exceeding those of field crops (Wilson et al 1992). Glasshouse crops with CO2 enrichment achieve maximum efficiency of light energy utilization between 12-13% (Wilson et al 1992). The ability of plants to utilize CO2 is dependent upon the presence of light, for this reason it is only useful to supplement CO2during the daylight hours (Styer and Koranski 1997).http://www1.agric.gov.ab.ca/$dep...Seeing is Believing289,504 viewsco2sciencePublished on 9 Apr 2010Isolated for 42 days in chambers of ambient and elevated CO2 concentrations, we periodically document the growth of cowpea plants (Vigna unguiculata) via time-lapse photography.Submarine crew are reported to be the major source of CO2 on board submarines (Crawl 2003). Data collected on nine nuclear-powered ballistic missile submarines indicate an average CO2 concentration of 3,500 ppm with a range of 0-10,600 ppm, and data collected on 10 nuclear-powered attack submarines indicate an average CO2 concentration of 4,100 ppm with a range of 300-11,300 ppm (Hagar 2003).Thus, CO2 at 40,000 ppm for 2 weeks did not affect performance on multiple tests of cognitive function in physically fit young airmen, a population probably not unlike submariners.https://www.quora.com/At-what-CO...GOVERNMENT ACTION IS TALK ONLY WITH NO IMPACTTHE CLIMATE IS COOLING WHY TRY TO MAKE IT COLDER?It is obvious that government action is terribly wasteful and useless assuming Co2 matters to the climate as renewables and carbon taxes are having zero impact on reality.Do we really want to go back in history to low levels of Co2 and low life expectancy? Now of course the above graph only shows correlation between increasing Co2 levels and increasing life expectancy. Obviously simple correlation does not prove causation. However as to causation the connection is that Co2 is essential to all plant and animal life on the planet through photosynthesis.Even the politically driven UN IPCC recognized that government plans to reduce Co2 levels could be disastrous to plants and have a devastating impact on life expectancy. As a result the PARIS ACCORD specifies in ARTICLE 2(b) that if reducing Co2 ‘threatens FOOD PRODUCTION’ the reductions and targets should be cancelled. Yes a full exemption is allowed for governments against action on lowering Co2 levels from human emission, THANKFULLY!The real issue is the earth cooling so much that we are heading for another brutal little ice age. Many research papers predict this.MINI ICE AGE TO HIT NEXT YEARAS Britain shivers through the coldest Easter ever, experts say we could be heading for a new Ice Age.Their frosty prediction comes as the Met Office has warned that temperatures will remain up to 10C below average until about April 20 – not just the UK, but in the rest of the world as well.Experts have declared the start of 2013 the coldest for 208 years, and they reckon it could become a whole lot colder.Again quoting Russian scientist Dr Habibullo Abdussamatov from the St Petersburg Pulkovo Astronomical Observatory who claims that it is proof we are heading for a mini ice age.“We are now on an unavoidable advance towards a deep temperature drop.” According to Dr Abdussamatov, the Earth cools and warms in 200-year cycles.The last big freeze, known as the Little Ice Age, ended in 1805. And he claims the next freezing period for the Earth will begin next year.The German Herald also quotes (or possibly misquotes) Dr Habibullo Abdussamatov (link)Chicago after jet stream goes South bringing numbing Arctic air and record cold temperatures.The climate is getting colder as sunspots decline and yet the Paris Agreement hopes to make the climate even colder yet. WHY? This madness must stop.
- Home >
- Catalog >
- Business >
- Chart Template >
- Roster Template >
- Soccer Lineup Template >
- soccer team sheet template >
- Nm Substitute W-9 Form