The Guide of finalizing Case Study: Cleaners Remove Silicone From Online
If you are looking about Modify and create a Case Study: Cleaners Remove Silicone From, here are the simple ways you need to follow:
- Hit the "Get Form" Button on this page.
- Wait in a petient way for the upload of your Case Study: Cleaners Remove Silicone From.
- You can erase, text, sign or highlight through your choice.
- Click "Download" to keep the documents.
A Revolutionary Tool to Edit and Create Case Study: Cleaners Remove Silicone From
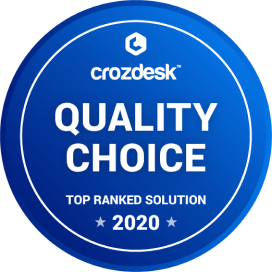
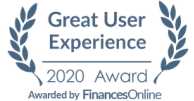
How to Easily Edit Case Study: Cleaners Remove Silicone From Online
CocoDoc has made it easier for people to Fill their important documents by the online platform. They can easily Tailorize of their choices. To know the process of editing PDF document or application across the online platform, you need to follow this stey-by-step guide:
- Open CocoDoc's website on their device's browser.
- Hit "Edit PDF Online" button and Upload the PDF file from the device without even logging in through an account.
- Edit your PDF document online by using this toolbar.
- Once done, they can save the document from the platform.
Once the document is edited using online browser, the user can export the form as you need. CocoDoc ensures the high-security and smooth environment for consummating the PDF documents.
How to Edit and Download Case Study: Cleaners Remove Silicone From on Windows
Windows users are very common throughout the world. They have met a lot of applications that have offered them services in modifying PDF documents. However, they have always missed an important feature within these applications. CocoDoc aims at provide Windows users the ultimate experience of editing their documents across their online interface.
The steps of modifying a PDF document with CocoDoc is simple. You need to follow these steps.
- Pick and Install CocoDoc from your Windows Store.
- Open the software to Select the PDF file from your Windows device and continue editing the document.
- Fill the PDF file with the appropriate toolkit showed at CocoDoc.
- Over completion, Hit "Download" to conserve the changes.
A Guide of Editing Case Study: Cleaners Remove Silicone From on Mac
CocoDoc has brought an impressive solution for people who own a Mac. It has allowed them to have their documents edited quickly. Mac users can make a PDF fillable online for free with the help of the online platform provided by CocoDoc.
To understand the process of editing a form with CocoDoc, you should look across the steps presented as follows:
- Install CocoDoc on you Mac in the beginning.
- Once the tool is opened, the user can upload their PDF file from the Mac with ease.
- Drag and Drop the file, or choose file by mouse-clicking "Choose File" button and start editing.
- save the file on your device.
Mac users can export their resulting files in various ways. Downloading across devices and adding to cloud storage are all allowed, and they can even share with others through email. They are provided with the opportunity of editting file through various methods without downloading any tool within their device.
A Guide of Editing Case Study: Cleaners Remove Silicone From on G Suite
Google Workplace is a powerful platform that has connected officials of a single workplace in a unique manner. While allowing users to share file across the platform, they are interconnected in covering all major tasks that can be carried out within a physical workplace.
follow the steps to eidt Case Study: Cleaners Remove Silicone From on G Suite
- move toward Google Workspace Marketplace and Install CocoDoc add-on.
- Attach the file and Push "Open with" in Google Drive.
- Moving forward to edit the document with the CocoDoc present in the PDF editing window.
- When the file is edited ultimately, save it through the platform.
PDF Editor FAQ
What are some ideas for a manufacturing mini-project for undergraduate mechanical engineering?
I can provide you a list of 1297 ideas and projects which you can make for your mechanical engineering projects. I had collected this list from so many friends of different colleges, and major topics are from my domain. I am collecting this from second semester of my college time. I am only providing the list of topics and not the details of each project as the answer would become more lengthy. and you have to do some effort to find out more about the topic you like and I can help you if found any difficulty. I had also arranged the list in alphabetical order.Project topics for final year mechanical students..………………………………………………by vaigyanik Atul Tripathi.1. automobile fuel indicator2. automobile braking systems3. spart distributor4. like other utilities.5. AEMS automotive engine management system using Meqa Squirt Kits6. Redesign of brake assembly of Formula SAE car7. Hydraulic car lift8. Lift for small recreational vehicles (˜Motor cycle jack™)9. Stair climbing hand cart10. Wheel chair accessible transfer seat base11. Paper towel dispenser12. Automatic labeling system13. 1st TYPES OF PRODUCTION14. 3 Axis Digital Accelerometer15. 3D Solar cells16. 3D-Kinematics Of Biological Joints17. 4d visualization in biomedical18. 4-Wheel Independent Suspension19. A Case Study Of Management20. A Clean Biodiesel Fuel Produced from Recycled Oils and Grease Trap Oils21. A Design Theory Based22. A DOUBLE-WALL REACTOER FOR HYDROTHERMAL OXIDATION WITH SUPERCRITICAL WATER FLOW ACROSS THE INNER POROUS TUBE23. A FLUID-SOLID INTERACTION MODEL OF THE SOLID PHASE Epitaxy In Stressed Silicon Layers24. A Hypersonic Hybrid Vehicle25. A Managtoreological Semi Active Isoolator to Reduce Noise and vibration transmissibility in Automobiles26. A Study Of A Displacement Amplifier27. A Theory Of Anharmonic Lattice Statics For Analysis Of Defective Crystals28. Ablative MAterials29. ABRASION WEAR CHARACTERISTICS OF SAND CAST Al-707530. Abrasive Blast Cleaning31. Abrasive Etching32. Abrasive Water Jet33. Flywheel energy storage device34. Automated MIG weld torch cleaner (all on the market are crap, million dollar idea)35. Temporary house stairs that can be folded up and meet safety standards (used when building houses)36. Cable recoil system that does not use a spring, recoil is on a rotating shaft. (like used on a rowing machine)37. Windmill blade automatic blade pitch system (low or no electricity).38. Automatic automotive block heater connection (just drive up to house and plugs in automatically and cycles on only when cold out)39. Shaft speed differential (different design but same idea as automotive axel differential)40. IC engine valve lift control mechanism (valve lift controlled engine instead of throttle plate) (Mercedes has a model) (investigate "jake brake" in diesel engines)41. ABS System42. ACC-Plus(Adaptive Crusie Control+) System43. Acoustic Emission Based Machining Tool Condition Monitoring “ An Overview44. acoustic parking system (APS)45. Acoustics in Engineering46. Active Control of Near-Wall Turbulent Flow47. Active Decoy Systems48. Active Electrically Controlled Suspension49. Active Electrically Controlled Suspension(16)50. Active Front Lighting System51. Active roll-over protection system in Automobiles52. Active Suspension System A Mechatronic System53. Adaptive air suspension54. Adaptive compensation of DTV induced brake judder55. Adaptive Cruise Control56. Adaptive Cruise Control For Modern Automobile57. ADVANCE IN CAR SAFETY58. Advance Systems In Two Wheelers59. Advanced Airbags60. Advanced Composite Materials61. Advanced Cooling Systems(18)62. Advanced Diesel Common Rail Systems for Future Emission Legislation63. Advanced Energy Conversion Systems64. Advanced In Mechanical Engg. Design And Manufacturing65. ADVANCED INTERNAL COMBUSTION ENGINE RESEARCH66. Advanced Off-set printing67. Advanced Plastics68. Advanced Propulsion Methods(8)69. ADVANCED QUALITY CONTROL TECHNIQUES70. Advanced Rocket Motors71. Advanced safety features in nuclear reactors72. Advanced trends in manufacturing technology-optical fiber sensor in medicines73. Advances in automobiles (Hybrid Vehicles)74. ADVANCES IN CAPILLARY FLUIDS MODELING75. Advances in cutting tool technology76. Advances in Gas Turbine77. AdvanCES Trends in manufacturing TECHNOLOGY optical Fiber sensors in medicine78. Aerodynamics79. Aerospace Flywheel Development80. Aerospace Propulsion81. Aerospikes82. AFFECT_AND_MACHINE_DESIGN_A83. Agile manufacturing84. AGP Evolving the Graphics Interface85. Air- Augmented Rocket86. Load tests and many other tests on composite material (for automobile industries).87. Design of pressure vessel to code specification.88. Heat recovery steam generator (HRSG)89. Variable speed transmission (line Nuvici bike hub)90. This would be very important when trying to make a good electric vehical.91. One way Clutch92. There are sprag and clicker type couplings. Sprag is hard to manufacture and the clicker style (bicycle hub type) are noisy and wear out. Come up with a new way and you are a millionaire93. High speed cutting of thin wall tube without making burr on the end. (low cost)94. Heat recovery system for internal combustion engine. (steam or likewise)95. Effecient pnumatic motor design (compressed air energy recovery system)96. Automated gray water recovery system97. Air Bearing Next Generation Bearings98. Air Bearings99. Air Bearings: - Next Generation Bearings100. Air Brithing Engine101. Air Casters102. Air Cushion Vehicles(21)103. Air pollution from marine shipping104. Air Powered Car105. Air Ship106. Air suspension system107. Airbags & ABS~108. Aircraft design109. Aircraft Egress110. Aircraft Maneuverability111. Aircraft Propeller~112. Airport management113. All- wing Technology114. Alternate Fuel Cells for Automobiles115. Alternative Abrasive To Diamond116. Alternative Fuel117. Alternative Fuel Vehicles118. Alternative Fuels Hydrogen in internal Combustion engines119. Alternative System To The Domestic Refrigerating System120. Aluminium Alloy Conductors121. Amoeba Organization122. Amphibious Army Surveillance Vehicle123. Amphibious Army Surveillance Vehicle124. AMRR125. AN ELECTRONIC SYSTEM FOR CONTROLLING AIR FUEL RATIO126. AN ELECTRONIC SYSTEM FOR CONTROLLING AIR/FUEL RATIO OF GASEOUS FUELLED ENGINE127. An expert System “ Based design of 3-Dof Robot128. AN EXPERT SYSTEM-BASED DESIGN OF 3-DOF ROBOT129. An overview of nano-manufacturing130. Analysis and Design Methods of Distributed Sensor131. Analysis And Design Methods Of Distributed Sensor Systems For Manufacturing Quality Improvement132. Analysis Of Material Using Digital Radioscopy133. Antilock Braking System134. antimatter135. Antimatter -the ultimate energy136. Antiroll suspension system137. Antiskid System Of Supersonic..138. Application Of Crvoi Reatmkm Fok Enhancement In Tool Like139. APPLICATION OF CRYOTREATMENT FOR ENHANCEMENT IN TOOL LIFE140. Application Of Cryotreatment..141. application of cryotreatment12142. Application of GPS in automobiles143. Application Of Laser Machining In Diamond Processing144. Applications Of Micro-Controller In Auotomobile145. Applications Of Nanotechnology146. Aqua Silencer - A Noise & Emission Controller147. Aque Fuel148. ArcJet Rocket149. Artificial Intelligence150. Artificial Intelligence (Modelling Air Fuel Ratio Control)151. Artificial Intelligence Future Around Us152. Artificial Intelligence In Mechanical Field153. Artificial Intelligence-Present And Future154. Artificially Engineered Material Composites155. Aspheric lenses156. Assembly Of Water Cooler157. Atkinson cycle engine158. ATOMIC BATTERY159. Atomistic Characterization of Dislocation Nucleation and Fracture160. Auto Drilling With Geneva161. Automated Anorectal Lymph Node Sampler162. Automated Assembly System163. Automated Highways164. Automatic Braking System165. AUTOMATIC TRANSMISSION System166. Automatic transmission tiptronic, 5-speed167. Automation And Robotics168. Automation in building construction, agriculture etc169. Automation Of Ultrasonic Testing Procedures170. AUTOMOBILE AC BY UTILISING WASTE HEAT & GASES171. Automobile Air Conditioning172. Automobile design173. Automobile Tires174. Automotive Infotainment175. Autonomous Submarines176. AUTONOMOUSLY GENERATIVE CMM Part177. Avionics178. Babbitt metal179. Balance Of Tool Holder180. BALL PISTON ENGINE181. Ball Piston Engine A New Development In Rotary Engines182. Ball Piston machines183. Ball valve184. Ballastic Particle Manufacturing185. Batch Production186. Battery Electric Vehicle187. Bearing Life Measurements188. Bench top wind tunnels189. Benchmarking190. Bike Of The Future- Pneumatic Bike191. Bio Diesel192. Bio-degradable polymers193. Bio-diesel - the next generation fuel source194. BIODIESEL & IT™S UTILITY195. Biodiesel From Jatropha196. Bio-ethanol As Fuel197. Biofiltration198. Biogas199. Biologically inspired robots200. Biomass as an Alternate Fuel for Diesel Engine201. Biomass As An Alternate Fuel For Diesel Engine202. Biomass Fuelled Power Plant203. Biomass Gasification204. Biomechanics205. Biomechatronic Hand206. BIOMETRIC IDENTIFICATION207. biometrics security208. Biomimetics209. Bioreactors210. biturbo211. Blasting cap212. Blended Winged Aircraft213. BlueTec214. Boimetrics: An Unparelled Security Check System215. Boosting Gas Turbine Energy Efficiency216. Bose suspension system217. Brake Assisting Systems218. Brake booster219. Breakthroughs in Engine Efficiency220. BUSINESS EXCELLENCE THROUGH QUALITY221. Business Process Analysis By BPR222. Business Process Re-Engineering223. Butterfly Valve224. Butterfly valvecatalytic converter225. cad226. CAD & CAE IN BIOMEDICAL FIELD227. Caged Ball Technology228. Cam less Engines229. Camless engine with elctromechanical valve actuator230. Can a ship fly?231. Car Handling232. Carbon Fibre On F1 Cars233. Carbon Foam-Military Applications234. Carbon nanotube cloths235. Carbonfibre On F1 Cars236. Cargo storage in space237. Catalytic Converters238. Catalytic lean Burn engield Engine With Two239. Cavitation shotless peening240. Cell Integration Into A Manufacturing System~241. Centrifugal Compressors242. Centrifugal Pump243. Ceramic fastners244. Ceramic Hybrid Ball Bearing245. ceramic Inserts246. CeramicLike Coatings247. CFD A Third Approach In Fluid Dynamics248. CFD Analysis Of A Simple Convergent Flow Using ANSYS FLOTRAN 10.0249. CFD In Weather Forecasting250. CFD/FEM/FEA/CAE251. CHALLENGES IN PLASMA SPRAY ASSEMBLY OF Nanoparticles To Near Net Shaped Bulk Nanostructures252. Characterization Of Microchannel Materials For Biochip Development253. Chloro Fluro Carbons254. Cleaning Of Metal255. CLIMATE CHANGE MITIGATION BY BIOMASS GASIFICATION256. Clutch Lining Testing Machine257. CNC SYSTEMS258. COAL GASIFICATION259. Coating Of Corbide Inserts260. Coded Modulation Techniques For Direct-Detection261. Collision warning system262. Combing Developments & Their Significance-Mech10263. Combustion Control Using Optical Fiber264. Combustion Research265. Combustion Stability In I.C.Engines266. Combustion Stability Of NG IC Engine267. Common Rail Direct Injection (Crdi) Engines268. COMPARISON OF EXPERIMENTAL AND FINITE ELEMENT Results For Elastic Plastic Stress269. Complex System Development270. Composite Materials271. Composite materials272. Composite materials for aerospace applications273. Compound Vortex Controlled Combustion(44)274. Compresed Air Cars Technology275. Compression Tube fittings276. Computational Fluid Dynamics277. COMPUTER AIDED DESIGN278. Computer Aided Analysis of Composite Laminates279. Computer Aided Process Planning (Capp)280. Computer Aided Production Engineering (CAPE)281. Computer Integrated Manufacturing-Building The Factory Of Future282. Computer Modelling283. Computer-Aided Geometric Design284. Concentrating Solar Power Energy From Mirrors285. Concept Cars286. Concept Of Flying Train287. ConCurrent Engineering288. Condenser Bushing289. CONDITION MONITORING OF BEARINGS BY ECHO PULSE METHOD290. Condition Monitoring Through Vibration Measurement291. Conditional monitoring & fault Diagnosis292. CONSOLIDATION BEHAVIOR OF Cu-Co-Fe PRE-ALLOYED Powers293. Constitutive Modelling of Shape Memory Alloy Using Neural Networks294. Contactless energy transfer system295. Continuously Variable Transmission296. Control of Cure Distribution in Polymer Composite Parts Made by Laminated Object Fabrication (LOF)297. Cooling And Lubrication Of Engines298. Cordless Tools299. Corrosion resistant gear box300. Corrugated Metals301. Cost Effective Safety Instrumented Systems302. crap & bipip303. Crew Exploration Vechicles304. Crop Harvester305. Crop Harvesting Machine306. CROSS HYBRID SOURCE ROUTING PROTOCOL FOR WIRELESS ADHOC NETWORKS307. Cruise missile technology308. Cryogenic Automotive Propulsion Zero Emission Vehicle309. Cryogenic Ball Valves310. Cryogenic Grinding311. Cryogenic Processing of Wear Control312. CRYOGENIC ROCKET ENGINE & THEIR PROPELANTS313. Crystaline Silicon Solar Cells314. Cummins Diesel Fuel System315. Cushioning Impact in Pneumatic Cylinder316. CVCC317. CVT318. Cybernetics319. Cylinder Deactivation320. Damage Detection By Laser Vibration Measurement321. Damage identification in aging aircraft structures with piezoelectric wafer active sensors322. DARK ROOM machining323. Data Fusion For Quality Improvements In Complex Solar Cell Manufacturing Processes324. Deformation-Assisted Transformations In Nanocrystalline And Amorphous Alloys325. Dendritic Solidification Using Phase-Field Method326. desert cooler327. Design And Development Of Automated328. DESIGN AND DEVELOPMENT OF MODIFIED OPERATIONAL CONTROLS ON SINGLE MOLD MACHINE329. DESIGN AND DEVELOPMENT OF WEEDING MACHINE330. Design And Fabrication Of Artifically Engineered Material Composites For Electromagnetic Systems331. Design for Manufacturing332. Design for manufacturing “ A giant lip in world class manufacturing333. Design of a medical device and its network for generating334. Design of an active car chassis frame incorporating magneto rheological fluid335. DESIGN OF AUTOMATED GUIDED VEHICLES FOR FLEXIBLE MANUFACTURING SYSTEMS336. Design Of Efficient Production337. Design of Efficient Production Systems Using Petri Net338. Design, Analysis, Fabrication And Testing Of A Composite Leaf Spring339. Design, Implementation, Utilization Of FEM340. Desktop Manufacturing341. Determination Of Transmission Specta Using Ultrasonic NDE342. Development & Application343. Development In Arc Welding Process Using Robot344. DEVELOPMENT OF AN AGV MATERIAL. Development Of High Performance345. Development Of An Ultrasound Sensor For High Energy Medical Applications346. Development Of Coated Elecrodes For Welding Of HSLA Steels347. Development Of High Performance348. Development Of Self Lubricating Sinterd Steels For Tribological Applicants349. Development Of Self Lubricating Sintered Steels For Termilogical Application350. Development Status Of Superconducting Rotating Machines351. Diamond Cutting Tool And Coatings352. Diesel Particulate Filter353. Different Types Of Injection Systems And Emission354. Diffusion Flame Shapes And Thin Filament Diagnostics355. Digital manufacturing356. Digital Manufacturing Using STEP-NC357. DIGITAL SIGNAL PROCESSING358. Digital Water Marking for color images using DWT and its applications359. Direct Injection Process360. Direct Manufacturing361. Direct Reduction Iron362. Direct shift gearbox (DSG)363. Directed Energy364. DISASTER EARLY WARNING SYSTEM365. Distribution Side Management For Urban Electric Utilities In India366. D-M-A-I-C MODEL IN SIX SIGMA367. Dose Evaluation In Moving/Deforming Anatomy: Methods And Clinical Implications368. Double-wishbone suspension369. Drag Racing370. Drive-By Wire Systems(23)371. Driver information system (DIS)372. DRY MACHINING373. DRY SLIDING WEAR STUDIES ON HYBRID MMC™S “ A Taguchi Technique374. Dual Clutch Transmission375. Ductile Mixed-Mode Fracture Criterion Development And Crack Growth Simulations376. Durability in Design377. Durable Prototyping378. DurAtomic Process379. Dynamic Ride Control (DRC)380. Dynamic shift program (DSP)381. Dynamics of Cutting Viscoelastics Materials382. Dynamics Of Cutting Viscoelastics Materials383. Dynamics Of Sport Climbing384. E85Amoeba Organization385. Eco-Freiendly Surface Treatments386. Ecofriendly rac387. Ecofriendly technology1388. Economical E-Beams389. Effect Of Catalytic Coating390. Effect Of Grash Of Number391. Effect Of Preload On Stability And Performance Of A Two-Lobe Journal Bearing392. Effect Of Pressure On Arc Welding Process393. Effect Of Stacking Sequence On Notch Strength In Laminates394. Efficiency In Boring395. E-gas396. Elasto-Capillary Thinning And The Breakup Of Complex Fluids397. Elecro Magnetic Flowmeters398. ElecroHydraulic Sawmills399. Elecromagnetic Valves400. Electric Automobiles401. Electric Cylinders402. electric power steering units403. Electric Rocket Engine404. Electric Vehicles405. Electrical Energy Generated in a Power Station406. Electricity From Ocean Waves407. Electrochemical Machining (ECM) & EBM~408. Electromagnetic Bomb409. Electromagnetic Brakes410. Electromagnetic Clutches411. Electronbeam Machining~412. Electronic Multipoint Fuel Injection System413. Electronic Road Pricing System~414. Electronically Controlled Air Suspension System415. Electronics For Better416. Electronics for Better Diesel Engine Management417. Electrostatic precipitator418. Embedded Applications Design Using Real-Time419. Embedded Computing in Mechanical Systems420. emergency caller421. Emission Control Techniques422. Energy Conservation Of Rubber Industry423. Energy Conversion and Management424. Energy efficient turbo systems425. Energy Engineering: Biodiesel426. Energy saving motors427. Energy-absorbing bumpers428. Engineering Applications of Nylon 66429. E-NOSE430. Ergonomics431. Esterfied Jatropha oil as bio fuel432. Ethanol433. ETHANOL an alternate fuel434. EURO V435. Evaluation Of A Gamma Titanium Aluminide For Hypersonic Structural Applications436. Evaluation Of High-Power Endurance In Optical Fiber Links437. EXPERIMENTAL ANALYSIS OF HEAT PIPE438. Experimental Analysis of Modified Machine Tools439. Experimental Characterization And Numerical Modeling Of A Float Glass Furnace440. Experimental Stress Analysis For Pipes441. Expert Technician System442. Explosive Welding443. External Nodes In Finite Element Analysis444. EYE READER445. F1 Track Design And Safety446. Facility Layout Design Using Genetic Algorithm447. FADEC - Full Authority Digital Engine Control(41)448. FADEC - Full Authority Digital Engine Control.449. FADEC - Full Authority Digital Engine Control.450. Failure Analysis of Lap & Wavy-Lap Composite Bonded451. Failure mode evaluation and criticality analysis452. Fast Boundary Element Calculation Of Acoustic Radiation From Vibrating Structures By Mortar Coupling453. Fast breeder reactor technology454. Fast Convergence Algorithms For Active Noise Controlin Vehicles455. Fiber-Optic Telecommunication And The Economic Benefits456. Finite Element Analysis457. Finite Element Analysis for an Effective cross-sectional Beam458. Finite Element Analysis Of Robotic Arm For Optimal Work Space Determination459. Flexible Manufacturing System460. Floating Power Stations~461. Floating Solar Power Station462. Floating Wind mills463. Fluid Energy Milling464. FLUID POWER A DOUBLE-WALL REACTOER FOR HYDROTHERMAL OXIDATION WITH SUPERCRITICAL WATER FLOW ACROSS THE INNER POROUS TUBE465. Flyash Utilisation466. Flying on Water467. Flywheel Batteries468. Flywheel Energy Storage469. FMS (Flexible Manufacturing Systems)470. Forge Welding471. Fractal Robot472. Fracture Mechanics In Design And Failure Analysis473. Free Electron Laser474. Free Form Modelling Based on N-Sided Surfaces475. Freezing Of Biological Tissues476. Friction Stir Welding477. Friction Welding478. Friction Welding Of Austenitic Stainless Steel And Optimizatin Of Weld Quality479. Frictionless Compressor Technology480. Frictionless Compressor Technology(48)481. Fuel Cell Airplane482. Fuel cell powered Go-Karts483. Fuel Cell Today484. Fuel Cells & Their Substitutes485. Fuel Cells on Aerospace486. Fuel Energizer487. Fuels from Plastic Wastes488. Full Colour 3D Modelling Using Rapid Prototyping489. Functional Nanocrystalline Ceramics490. Fundamental Aspects Of Micro/Meso-Scale Manufacturing And Micro-Scale Milling491. Fused Deposition Modelling492. Future Cars493. Future Electrical Steering System494. FUTURE OF BAG FILTER FOR REMOVAL OF PARTICULATE MATTER IN POWER STATION495. Future of FEA iN MAnufacturing496. Future of Portable Power497. Future Trends In Automobiles498. Fuzzy Logic499. FUZZY LOGIC AND ARTIFICIAL INTELLEGENCE500. Fuzzy logic in Aircraft stability501. Fuzzy Logic In Automotive Engineering502. Gas Hydrates503. Gas Hydrates: Alternative for Natural Gas in Future504. Gas Transfer Systems505. Gas Turbine506. Gaseous Pyrolysis507. Gasoline Direct Injection Or GDI508. gate valve509. Gauges510. Gear Box511. Gear Drives512. GEAR NOISE REDUCTION BY NEW APPROACHES IN GEAR FINISHING PROCESSES513. Genetic Algorithm Based Optimum Design Of Composite Drive Shaft514. Geothermal Energy Utilization515. Geo-Thermal Energy(19)516. Geothermal Power517. Glass Glue518. Glass Making519. Global Environment Problems520. Global Positioning System521. Global warming522. Globalization523. Globe Valves524. GPS525. Green Energy526. green engine527. Green Factory528. Green fuels529. Green Manufacturing530. Grid Generation And Simulation Using CFD531. Guided Missile532. HalBach array533. Handfree Driving534. Handheld Radiation detector535. HANS536. HANS-In F1 Racing(45)537. Harvesting Wave power538. Heat caps539. Heat Pipe540. HEAT PIPES FOR DEHUMIDIFICATION AND AIR CONDITIONING541. Heat Transfer542. Heat Transfer Along A Vertical Insulated Chimney543. HEAT TRANSFER AND FLOW CHARACTERISTICS FOR BUOYANCY INDUCED FLOW THROUGH TUBES544. Heat Transfer Enhancement By Forced545. Heavy duty Gasoline engines546. Helicopters547. HELIUM-A CRYGENICS FLUID548. Hexapod Machine Tool549. High Altitude Aeronautical Platforms550. High angle of attack aerodynamics551. High Efficiency Heat Exchanger552. High Performance Heat Sink Based On Screen-Fin Technology553. High Performance Microprocessor554. High Speed Precise Gear Boxes555. High speed Propellers556. High speed Railway coaches557. HIGH SPEED TRAINS558. Highly Productive And Reconfigurable Manufacturing System(Hiparms)559. High-Wire car560. Hologram561. Hovercrafts562. How To Increase Starting Torque Of A Locomotive.563. Human Artificial organs564. Human Transporter565. Humans and Energy566. HVDC Transmission567. Hybrid electric vehicles (HEVs)568. Hybrid energy Systems569. Hybrid Engine570. Hybrid Motorcycles*571. Hybrid Synergy Drive (HSD)572. Hybrid Wind Electrolysis System573. Hydraulic Analysis Of Hydrostatic Bearing Of Primary Sodium Pump Of A Fast Breeder Reactor574. Hydraulic Elevators575. Hydraulic free pistan engine576. Hydraulic railway recovery systems577. Hydro Drive578. Hydro Electricity579. Hydro Jetting580. Hydrodynamids & gas liquid581. HYDROFORMING582. Hydrogen583. Hydrogen Car584. Hydrogen Energy585. Hydrogen Fuel Tank586. Hydrogen Generation via Wind Power Electrolysis587. Hydrogen Production using Nuclear Energy588. Hydrogen the next generation fuel589. Hydrogen Vehicle590. Hydroplane591. Hydroplanning592. Hydro-Pneumatics593. Hydro-Pneumatics An Efficient Tool for Automation594. Hydrulic Launch Assist 21595. Hyperplane596. Hypersonic Space Planes597. HyperTech Engine598. Hy-Wire Car(43)599. IC Engine (Internal Combustion)600. Ic Engines601. ICE Blasting602. Iddq Testing For CMOS VLSI603. IGES CAD604. Image Processing Software To Detect Defects In Glass605. I-Mode606. Impact hammers607. Impact Of Fuel Quality608. Implication of Molecular nanotechnology technical performance parameters on previous defined space system architecture609. Improved efficiency of gas turbine610. IMPROVEMENT IN TOOL LIFE OF MILLING CUTTER BY APPLICATION OF CRYOTREATMENT611. Improving aerodynamic performance of an aerospace vehicle612. Improving Service Quality..613. In Mould Lamination Technique614. In View Of The High Commercial Gains Of A Commercial Place I615. Independent Wheel Vehicle Suspension616. Indian Manufacturing Scenerio617. Industrial Robots618. Industrial Team Behavior And Management Tools619. Influence of an iron fuel additive on the performance and emissions of a DI diesel engine620. Influence Of An Iron Fuel Additive On The Performance And Emissions Of A DI Diesel Engine621. Information Technology And The Analysis Of A Complex System622. Infrared623. Infrared Curing And Convection Curing624. Infrared Thermography625. INITIAL CURVATURE GENERATION FOR OBJECTIVE MIRRORS OF NEWTONIAN TELESCOPE626. Injection Molding627. INNOVATION IN AUTOMOBILE INDUSTRIES 1628. Instrument Landing System629. Integrated Web Enabled Information...630. Integration Of Reinforced631. Intelligent Braking And Vehicular632. Intelligent Compact drives633. Intelligent manufacturing634. Intelligent Vehicles and Automated Highways635. Inter-Continental Ballistic Missile (ICBM)636. Internal Combustion Engine637. Inverse Design of Thermal Systems638. Investigations On Laser Forming639. Iontophoresis640. IT Application in Complex Syatem Analysis641. Jack Hammer642. Jatropa oil- Alternative fuel643. JATROPHA CURCAS644. Jelly Filled Telephone Cables645. Jet Engine646. Jet Powered Boat647. Jet Stream windmill648. Jetex Engine649. Jetropha based biodiesel650. JKJ651. Job Scheduling Using Neural652. Job Scheduling Using Neural Network Foe Rapid Manufacturing653. Just In Time654. Kaizen655. Kaizen Culture656. Kalina cycle657. KANBAN-AN Integrated JIT System658. Knowledge Based CAD for Technology Transfer659. Laminated Object Manufacturing660. Laod Sensing Hydraulics661. LASER 3_D SCANNER662. Laser Beam Delivery Through663. LASER BEAM MACHINING664. Laser Machining (Case study: Stereolithography)665. Laser Micromachining666. Laser radar Guns667. Laser Shot Peening668. LASER Sintering669. Latest in hitech petrol fuel injection GDI (Gasoline direct Injection)670. Latest Trends in Automotive Engg.& Technology671. Launching Space Vechicles from Moon672. Lean Burn Spark Ignition Engine673. Lean engineering674. Lean Manufacturing675. Lean to Steer Concept676. Lenoir cycle677. Level Measurement Of Bulk Solids678. Light weight material-Carbon fibre679. Liquid Engineering680. Liquid Hydrogen as an Aviation Fuel681. Liquid Injection Thrust Vectoring (LITV)682. Liquified Natural Gas683. Lng Vehicles684. Load Cells685. Logistics and supply chain management686. Logistics In A Competitive Milieu687. Long Term Mine Reconnaissance System688. Low Cost Spacecraft Simulator689. Low emission gas turbine690. Low Gloss ABS system691. Low inertia dics clutches692. Low-Power, High-Speed CMOS VLSI Design693. Lubrication Of A Ball Bearing- A Review694. Machine Phase Fullerene695. Machine tools vibration, Noise & condition monitoring696. Machine Vision697. Machining Technology For698. Machining Technology Of Leaf Spring699. Macromolecular Hydrodynamics700. Magnegas-The Fuel Of Future701. Magnetic Bearing702. Magnetic Launching703. Magnetic Levitation704. Magnetic Nanocoposites705. Magnetic refrigeration706. Magnetic Resonance Imaging707. Magneto Abrasive Flow Machining (5)708. Magnetorhilogical Semi-isolator to reduce noise and vibration transmibility to automobile709. Managerial710. Manufacturing Of Leaf Spring711. Manufacturing Through Electro Chemical Machining712. MAP Sensor713. Marine electric propulsion714. Mass Airflow Sensor715. Mass Production716. Mass Rapid Transit System (MRTS)717. Master Planning For College Campus718. MATERIAL BALANCES IN THE MISSILE719. Material Requirements Planning720. Material science including Nano-science721. Materials Of The Future722. Mechanical Behavior of Filament-Wound Pipes723. Mechanical Behavior Of Filament-Wound Pipes724. Mechanical Design Education At WPI725. Mechanical Model Of The Finger726. Mechanical Properties Of Mmc™s- An Experimetnal Envestigation727. Mechanical Seal728. Mechanical torque limitors729. Mechanics Of Composite Materials730. Mechanisms of heat transfer in nanofluids731. Mechanosynthesis732. Mechatronic733. Mechatronic Strategies for Torque Control of Electric Powered Screwdrivers734. Mechatronic Strategies For Torque Control Of Electric Powered Screwdrivers735. Medical Application Of Nano Tech.736. MegaSquirt737. MEMS “ a pollution free option for power generation738. MEMS & APPLICATION739. MEMS (New)740. MEMS In Industrial Automation741. MEMS(Micro Electro Mechanical Systems)742. Mesotechnology743. Metal Deposition744. Metal Matrix Composites745. Metal Nanoshells746. Metal-Matrix Composite Processing747. Metal-Matrix Composite Processing(49)748. Metamorphic Robots749. Methanol Vehicles750. Methods In Accelerator-Driven System Dynamics751. MHD submarine752. Micro- And Nano-Mechanics Of Surface Contact Plasticity753. Micro Batteries754. Micro Electro Mechanical System 123755. Micro Fluidic Chips756. Micro Gravity757. Micro Heat Exchangers758. Micro Hydraulics759. Micro Machines760. Micro Moulding761. Micro Pumps762. Micro scale regenerative Heat Exchanger763. Micro Turbine764. Micro/Meso-scale Manufacturing765. Microair Nozzles For Precision766. Microbial Fuel Cells767. Microcellular Foam Technology10768. Micro-Electromechanical Systems769. Microengines for microprocessors770. Microfinishing Of Rollers In Roller Bearings771. Microfluidics772. Micromanipulating Micromachines773. Micromixers774. Microscale Breaking Waves And Air-Sea Gas Transfer775. Micro-Scale Milling776. MicroTopography777. MICROTURBINE778. Military Radars779. Miller Cycle780. Miller Cycle Gas Engine781. Minimum Quantity Lubrication782. Mission Of Mars783. Modeling And Optimization Of Electron Beam Wealing Proces Using ANOVA784. Modeling and simulation785. Modeling of circulatory system and adventure in computer786. MODELLING OF CIRCULATORY SYSTEM787. Models And Methods In The Neutronics Of Fluid Fuel788. Models Of Random Damage789. Modern Air Pollution Control Technologies790. Modern Centrifugal Compressors791. MODERN TRENDS IN AUTOMOBILE ENGINEERING792. Modified four stroke engine793. Modular Cam Locks794. Modular conveyor Belts795. Modular Gear motor796. Modular workstations797. Molecular Engineering798. Molecular hinges799. Molecular Manufacturing800. Molten oxide electrolysis801. Monitoring of bearings802. Mordern Prototyping Methods803. Motors Without Mechanical Transmissions804. Motronic Engine Management805. Moulds in Casting of Plastics and Thermoforming806. Multi Valve Engine(50)807. Multifunction Control System For Robotic Fire Detection808. MultiJack Bolt Tensioners809. Multiple material milling platform810. MULTI-PURPOSE WHEELCHAIR CUM STRETCHER811. Namotechnology future perfect812. Namotechnology Shaping the future813. Nano in navy814. Nano Robotic Manipulation System815. Nano Robotic Manipulation System816. Nano Spreader Cooling817. Nano Technology818. Nano Technology Binding Experiment With Biosensor819. Nano Technology It's Small, Small, Small, Small World820. nanobatteries821. Nanocrystalline Thin-Film Si Solar Cells822. Nanomaterial Based Catalyst823. Nanorobotics824. Nanoscale Armor825. Nanoscale Fractals826. nanoTechnology827. Nanotechnology & Mechanical Engineering828. Nanotechnology A Deep Insight829. NANOTECHNOLOGY FOR CANCER THERAPY830. Nanotechnology future perfect831. Nanotechnology-shaping the future832. Nanoventions Micro-Optic Modeling And Control Of Micro-Scale Systems833. NAUTICUS MACHINE CALCULATONS834. NAUTICUS_MACHINARY_CALC835. Navigation836. Near Net Shape Fabricatons Via Vacuum Plasma Spray Forming837. Near Net Shape Memory838. New Age Tyres(9)839. New Finite Element Analysis for Unsteady 3D Natural Convection840. New rolling technique for texturing841. New Rolling Techniques842. New trends in Automobile Design843. Night Vision844. NIGHT VISION SYSTEM845. Noise Analysis For Optical Fiber Communication Systems846. Non Destructive Evaluation Techniques847. NON DESTRUCTIVE TESTING OF WELDS848. Non-conventional Energy Sources849. Nono Fluidics850. Nuclear & Radiological Engineering & Medical Physics Program851. Nuclear fuel reprocessing852. Nuclear Power Potential as Major Energy Source853. Nuclear Space Craft854. Nuclear's Next Generation855. Ny-Tran - Alternative To V Belts856. Ocean Thermal Energy857. Oil Shear brakes858. Oil well drilling859. Online Analytical Processing860. Optical trapping and manipulation of small particles861. Optimal Design And Analysis Of Automotive Composite Drive Safety862. Optimal utilization of renewable energy sources in remote areas863. Optimisation of Mechanical Systems864. Optimizing Centrifugal Pump865. Options & Accessories Of Car866. Opto-Electronic Sensor System867. Orbit Forming868. Orbital Welding869. Orbital/Space Mechanics870. Over-the-wing Engine mount configration871. Packaging872. Para-Gliding-Landing With Cygnus Airbag Safety System873. Particle Reinforced Aluminium Matrix Composites874. Pasteurization875. PC Controlled Gear Manufacturing876. Pendolina system for railway passenger comfort877. Performance evaluation of methanol Blended fuels in S. I. engines878. Performance Analysis of Manufacturing Systems879. Performance And Evaluation880. Performance Characteristics Of Pump Handling881. Performance Evaluation of solar Still Thermo Electric Mode882. Permanent Magnet Generator883. Perpetual Motion Machines884. Personal Transporters885. PHENOME-NERVE886. Photoacoustics Of Small Gas Clouds887. Photomechanics888. Photonic Crystals889. PICO SAT890. Piezoelectric Actuators891. Pint Sized Power Plants892. Piston less dual chamber rocket fuel pump893. Piston Ring894. Plasma Arc welding895. Plasma Science896. Plastic Welding897. Plastics In Automobile898. Plug-In-Hybrid Cars899. Pneumatic Bike900. Pneumatic Circuit1901. Pneumatic forming902. Pneumatics Control Systems903. Pnuematics904. Poka Yoke - Japanese Tech905. Polymers castings906. Porous Burner Technology907. Portable Power908. Portable X-RaY Fluorescence Analyser909. POWDER METALLURGY910. Power frequency magnetic fields911. Power From Space For Use On Earth912. Power Generation By Compressed Air Final913. Power Generation By Using Road Speed Breakers914. Power Hump915. Power System Contingencies916. Practical Fuel-Cell Vehicles917. Precision Engineering and practice918. Precision Engineering and practice919. Precision manufacturing and Inspection920. Probabilistic design of mechanical components921. Problems And Control Of Backfire For Hydrogen922. Process Automation Techniques923. PROCESS QUALITY MODEL IN SCM PERFORMANCE MEASUREMENTS924. Process Steam Generation.......925. Processing And Tribo Behaviour Of Nylon CLAY Nanocomposites Under Abrasive Wear Mode926. Product Definition And ..927. Programmable keyless entry928. Programming Self-Recovery In The Humanoid929. Propulsion Subsystems930. Protein Encapsulation Using U.V PEG Hydrogels931. Proton Exchange Membrane Fuel Cell932. Pseudoelasticity and Shape Memory in Metal Nanowires933. PTFE AS LUBRICANT1934. Pulse Detonation Engine (1)935. Pulse Tube Refrigerator936. PULSE WELDING A NEW WAVE IN WELDING937. Pulsed Plasma Thruster938. Pump Noise level reduction methods939. PVD Film Method940. Pyrometers941. Quality Circle942. Quality Control943. QUALITY CONTROL TECHNIQUES OF THE KANBAN SYSTEM944. Quality function deployment945. Quality Function Deployment (QFD) For Total Quality Management946. Quality in maintenance through TPM947. Quantum Chromo Dynamics948. Quantum Computing949. Quasi turbine950. Quasi-turbine Future Trends In Automobile Engine951. Quieter Fans For HVAC952. RAC953. Radar Guns954. Radar Guns and Laser radar Guns955. RADIANT ENERGY WELDING PROCESS11956. Random vibrations957. Rapid Design for Lean Manufacturing958. Rapid Injection Moulding959. Rapid Prototyping960. Rapid Prototyping “ Slicing Strategies961. Rapid Prototyping Technique Based On 3d Welding962. Rapid Re-Usable Tooling963. Rapid Tooling964. Recent Advances In Statistical Quality Control965. RECENT TRENDS IN AUTOMOBILES966. Recent Trends in Quality Management967. Recycling Of Plastics968. Redesign Of Plant Layout Using Travel Chart Technique (A Case Study)969. REDUCTION OF IDLE TIME THROUGH TPM-A CASE STUDY ON JUTE MILL970. Reduction Technology971. Re-Entry Of Space Vehicle972. Refined IC Engines973. Regenerative Brake974. Regenerative braking975. Regenerative Fuel Cells976. Reliability and risk analysis977. Reliability Redundancy Design-Using Simulation978. Remote Engine Starting..979. Remote Signal Acquisition And Interface Unit For Focal Ultrasound Surgery Procedures980. Remote Signal Acquisition And Signal Processing For Focal Ultrasound Surgical Procedures981. RENESIS ROTARY ENGINE982. Renewable Energy Design Application In Water Cooler983. REPORT984. Research Activities On Radio On Fiber Communication Network In TAO985. Research Aircrafts986. Research and Materials of Armor Design987. Research On Modified Layers Of Material Surface For Cr12 Mov Cold Die988. Resistojet Rocket989. Responsive manufacturing990. Return Of Two Stroke Engine1991. Reusable Launch Vehicles992. Reverse Engineering993. Reverse Engineering in Mechanical parts994. Reverse Engineering In Mechanical Parts 1995. Reverse Osmosis996. REVIEW OF LASER MICROMACHINING IN CONTRACT MANUFACTURING997. Rheology998. Rijke Tube999. RISK MANAGEMENT1000. Risks of Nano Engineered Particles1001. Robonaut1002. Robot driven cars1003. Robotic Assistants For Aircraft Inspectors1004. Robotic Pioneering1005. Robotic roller coasters1006. ROBOTICS1007. Robotics & AI1008. Robotics for Performing Surgical Operations1009. Robotics For Performing Surgical Operations1010. Robotics~1011. Robots In Radioactive Environments1012. Rocket Powered Aircraft1013. ROLE OF SATELLITE IN MOBILE SYSTEMS1014. Rotating Parallel Grippers1015. Rotating Scroll Power Compressor1016. Rubber1017. Rubber Products by Calendaring1018. SAFE HANDLING OF HC1019. Safety features of railway rolling stock1020. Safety Systems1021. SCADA1022. Scope of MEMS in Space1023. SCRAM JET1024. Sc ramjet engine1025. Scrubber Tech.1026. Scrubber.1027. Scuderi Split Cycle Engine1028. Sea Power1029. search engine optimization1030. Secure User Authentication Using Automated Bio-metrics1031. Selective Catalytic Reduction (SCR)1032. Selective Plating1033. Self Activated Single Use Switch1034. Self Aware Robots1035. Self Extinguishing PVC's1036. Self Healing Space crafts1037. Self Monitoring Pneumatic systems1038. Self Repairing Composites1039. Self Replicating System1040. Self-Assembly For Nano And Micro Manufacturing1041. Self-Healing Polymer Technology1042. SELF-REPLICATING SYSTEM1043. Selling Price Decision Support System For A Job Order Based Manufacturing Unit1044. Semi automatic transmission1045. Semi solid Casting1046. Seminar on Oil Drilling1047. Semi-synthetic cutting fluids1048. Sensotronic Brake Control System1049. Sensotronic Braking System1050. SEQUEL THE CONCEPT CAR1051. Set Up For Small Scale Industry1052. SHAPE DEPOSITION MANUFACTURING (SDM)1053. Shape Memory Alloys1054. SHED1055. Shock Absorber Testing System1056. Shock Waves & Shock Diamonds1057. Simple Constitutive Models For Linear And Branched Polymers1058. Simulation of Fuel Injection System of A Diesel Engine1059. Single Crystal Turbine Aerofoil1060. Six - Stroke Hybrid Engine1061. Six Sigma1062. Six Sigma - A Quality Control Tool In Industry1063. SIX SIGMA “ EFFECTIVE PROCESS IMPROVEMENT TOOL1064. SIX SIGMA AS A QUALITY CONTROL MEASURE “ A CASE STUDY IN DAIRY INDUSTRY1065. Six stroke engines1066. Size Reduction Of Window Air Conditioner1067. Skid Steer Loader And Multi terrain Loader1068. Sky Rocket1069. Small Satellites1070. Smart aerospace structures1071. Smart Ammunition1072. Smart Autoreeling mechanism1073. Smart Bombs1074. Smart Cards1075. Smart Combustors1076. Smart Fluids In Automotive Devices1077. SMART MATERIAL1078. Smart material actuators1079. Smart Materials1080. Smart Pnuematics1081. Smart Tire1082. Snake robots1083. Snake Well Drill1084. Snaps To Replace Screws1085. Software Based Re engineering..1086. Solar Aircraft1087. Solar Cells and Solar Cell Modules1088. Solar Chimney Power Generation System1089. Solar Energy Conservation To Hydrogen 1121090. Solar Heat Energy Storage In Phase Change Materials1091. SOLAR HEAT ENERGY STORAGE IN PHASE CHANGE MATERIALS1092. Solar photo voltaic cell- Alternative fuel1093. Solar Photo-voltaic Cells An Alternative Fuel1094. Solar Ponds1095. Solar Power Satellites (SPS)1096. Solar power Tower1097. Solar Powered Refrigerator1098. Solid Base Curing1099. Solid carbide end mills1100. Sonic Rain Gauge1101. Sono bouys1102. Sowing Machine1103. Space Craft Propulsion1104. Space Elevator (3)1105. Space Elevator Modified Again Boss Agn1106. Space Robotics1107. Space Shuttle1108. Space Shuttle Boosters1109. Space Shuttles And Its Advancements1110. Space ShuttleSemisolid Casting1111. Space stations1112. Space Transportation System1113. Spacecraft Propulsion1114. Spark Sintering1115. Special materials for high temperature applications1116. Special materials for ultra low temperature applications1117. Speech Recognition1118. Sports Plane1119. Springage1120. Spring age1121. Static Analysis Of Self-Recoverable Humanoid1122. Stealth Fighter1123. Stealth Radar1124. Stealth Technology1125. Steam Cars1126. Steam Engine1127. Steer- By -Wire1128. STEP CAD1129. Stereoscopic Projection Systems1130. Stirling Engine1131. Stirling Engine For Co-Generation1132. Strategies For Product1133. Stratified Charge Engine1134. Structural Applications Of Glass-Fiber Reinforced Concrete1135. Studies On Freezing Time Of Foodstuffs1136. Studies On Phosphoric Irons For Concrete Reinforcement Applications1137. STUDY AND DESIGN OF WAVE GUIDE NOTCH FILTER FOR A FREQUENCY OF 28 GHz.1138. Study Of Bio degradation Of Polyesters1139. Study Of High Temperature Crack Initiation In Single1140. Super Air Nozzles1141. Super Charging1142. Super Flat Nano Films1143. Supercase Hardening process1144. Supercavitation1145. Supervisory Control1146. Supervisory Control And Data Acquisition1147. Supervisory Control And Data Acquisition SCADA1148. Supply Chain1149. Supply chain management1150. Supply chain management and internet1151. Sustainable Engineering1152. Swing Bowling1153. Symmetrical All Wheel Drive1154. Synthesis Of Planar Mechanism With Variable Topology “ Review1155. Synthetic Aperture Radar1156. System Improvements Through TQM1157. Systems for Manufacturing Quality Improvement1158. Systems Modeling and Simulation1159. Tabletop Thermoacoustic Refrigerator For Demonstrations1160. Technical Development In Car1161. Technology-Based Entrepreneurship1162. Telematics1163. Temperature Resistant Alloys1164. Tension Control Brake1165. TERRA-FORMING MARS1166. Test Ranges / Facilities/Readiness1167. Testing of Welds1168. The Atomic Battery1169. The chaff box or cutter was a simple but ingenious device for cutting straw chaff1170. The Challenge Of Intelligent Systems1171. THE CHALLENGE OF INTELLIGENT SYSTEMS101172. THE DESIGN OF CELLULAR.....1173. The Effects Of Precipitate Distributions On HSLA Grain Structure1174. The Engineering Research Role in Environmental Noise Control1175. The Gyro Machine1176. The Gyro Machine : Using Non Planar Mechanism1177. The Hy-Wire Car1178. The Present Status Of The Domestic Nuclear Power Industry1179. The Role Of Software In Nuclear Engineering1180. The solar chimney power plant1181. Thermal Conductivity Of Porous Material1182. Thermal Plastic Composites1183. Thermo Acoustic Refrigeration1184. Thermo electric Technology1185. Thermo Hygrometer1186. Thermoacoustic Refrigerator1187. Thermostatic Refrigerator1188. Therrmophoresis1189. Thin Vacuum Conveyors1190. Thread Locking Device For Handling Thread At Flexible Endoscopy1191. Thread less Couplings1192. Tidal technology1193. Tip Tronic Gear transmission1194. tire & wheel without pneumatic1195. Tool Management System1196. Topographic Characterization And Modeling Of The Precision Surface Grinding Process1197. Torque And BHP1198. Total quality Management1199. TOTAL PRODUCTIVE MAINTENANCE (TPM)1200. Total Quality Management1201. Touch trigger probes1202. Towards A Customer Driven Enterprise : "Search On 3D Parts In Large Repositories1203. Towards New Platform Technology For Sustained Observations1204. TQM A Successful Journey (A Case Study)1205. TQM Implementation Learning Form Indian Organizations1206. Traction control1207. Transfer Machines1208. Transient Thermal Analysis Of Railway1209. Transient Thermal Analysis of Railway Wheel & Axle1210. Tran sonic aircraft1211. Trench less Technology1212. Trends in welding1213. Tribological Characteristics Of Cutting Fluid Groups1214. Tribology 121215. Tribology Of IC Engine1216. Tribology Of Sealing1217. Tribometer1218. Triptronic Automatic Gear Transmission1219. Turbine Technology In Automobile1220. Turbine Technology In Car1221. Turbines in silicon1222. Turbofan Engines1223. Two Stage Fuel Injection System1224. Types Of Bearing1225. Types Of Tires1226. Tyre Pressure Monitoring System Ad1227. Tyre Monitoring System “ 11228. Tyre Re Treading1229. Tyre Threading1230. Ultra Nano Crystalline Diamond1231. Ultrasonic NDE And Characterization Of Aerospace Materials1232. ULTRASONIC NONDESTRUCTIVE TESTING1233. Ultrasonic Phased Array For Defect Cartlization1234. Ultrasonic and Acousto-Optics for the Nondestructive Testing of Complex Materials1235. Underwater Acoustic Data Communication1236. Underwater Welding1237. Underwater wind mill1238. Unmanned Mine Spotter1239. USE OF DIFFERENT CONDITION MONITORING TECHNIQUE FOR PLANT1240. USE OF RICE HUSK AS AN ALTERNATIVE FUEL IN BOILERS “ A CASE STUDY ON RICE MILL1241. UTILIZATION OF WASTE POLYETHYLENE1242. Vacuum Braking System (4)1243. Vacuum Chuck1244. Vacuum Work holding1245. Value Engineering1246. Valve tronic1247. Valvetronic Engine Technology1248. VANOS (Variable Nockenwellen Steuerung)1249. VARIABLE CAM1250. Variable compression ratio engine1251. Variable Length Intake Manifold (VLIM) (7)1252. Variable Speed Drives1253. Variable Valve Timing In I.C. Engines1254. Vehicle Control And Information Systems For Safe Driving1255. Vehicle Dynamics1256. Vehicular Emission Control1257. VENDOR RATING1258. Vertical Landing and takeoff engine1259. Vertical Shaft Brick Kiln (VSBK)1260. Vertical takeoff and landing aircraft's1261. Vibration Analysis Of Flywheel Using Finite Element Analysis1262. Vibration control Techniques1263. Vibratory stress relief process1264. Virtual Manufacturing System1265. Virtual Prototyping1266. Virtual Reality Simulation1267. Virtual Reality Visualization1268. Virtual Reality1269. Visualization and Computer-Aided Design1270. VTEC1271. VVT-I1272. WANKEL ENGINE1273. Warm Gas Thruster Development Using Gaseous Hydrogen And Oxygen With Catalytic Ignition1274. Waste Heat Driven Refrigeration And Chilling Systems.1275. Water Diesel Emulsion With High Injection Press1276. Water jet cutting technology1277. Water Jet Technology1278. WATER JET TECHNOLOGY AS ADVANCED MANUFACTURING PROCESS1279. Water Rocket1280. Wave Springs1281. Weapon Engineering / Design1282. WEB AUTOMATION FOR INTEGRATION OF POWER SYSTEM APPLICATION1283. Web Based E-Commerce Shopping System1284. Weber Carburetors1285. Weld flaw detectors1286. Welding Robots1287. What Is A Nuclear Reactor1288. When Upgrading Tool Holders1289. Wind diesel System1290. Wind Energy Conversion System 101291. Wind engineering1292. Wind From The Sun-Power Plant1293. Wireless Energy Transmission1294. Wireless factories1295. WORLD CLASS MANUFACTURING1296. Written-Pole Technology1297. ZERO EMISSION NITROGEN PROPULSION SYSTEMfor further query feel free to mail me. or up vote and comment your topic in answer.
Which ingredients should you avoid when choosing a shampoo/conditioner?
The Hateful Eight Seed Oils Which Can Be Toxic For The BodyI’ve actually been doing a lot of research on this topic recently. I was watching a news program about inflammation-promoting high-PUFA seed oils which get stored in body fat and cause all types of inflammatory conditions.Whether we eat the seed oils or apply it to our body, it’s been proven that our skin and scalp absorb much of what we put on it and what we used to clean with it.Dr. Cate Shanahan has identified what she refers to as The Hateful Eight seed oils that we should never eat or apply to our bodies.Note: I have no relationship, financial or otherwise, with Dr. Cate Shanahan or with sales or promotion of her book.While researching the seed oils that should be avoided for food as well as hair and beauty treatments, I looked into the ingredients we should avoid when choosing a shampoo/conditioner.Are All Sulfates, Silicones And Alcohols Really As Bad As Their Press?One of the things I’ve learned is that sulfates, silicones, and alcohols are some of the common ingredients found in hair products.These ingredients have gained popularity amongst brands given consumers’ increased interest in whether their products are made with them because of their “harmful properties”.Some ingredients which are now being used in consumer hair and beauty products were originally made for industrial or commercial use such as rocket ships, anti-freeze, insect repellents and even oven cleaner.Keep in mind that not all ingredients considered toxic are really as bad as their general reputations.That’s because there is a much lower percentage of potentially toxic ingredients in the products than most people know. There is usually much less than necessary to cause any type of problems.See: Safe Cosmetics.Not everyone will agree with me and what works for one, may or may not work for others.Listed below are the ingredients I avoid when choosing a shampoo and/or conditioner for my hair:1. ParabensParabens can be found in most personal care products including your shampoo and conditioner to prolong shelf life. In essence they are a family of preservatives.Even the food we eat have preservatives.There are several types of parabens, so look out for anything that ending with ‘parben’ like butylparaben, ethylparaben and methylparaben.Propylparabens have been linked in some cases to breast cancer.Some people can tolerate parabens better than others, but it has been linked with skin and scalp irritations, reproductive issues and neurotoxicity in some cases. It’s even been linked to hair loss.Parabens may cause an imbalance of hormones and cause problems with regrowing lost hair.Many hair industry suppliers are continuing to work on providing a range of alternatives to parabens.Although companies are constantly working on introducing new and less concerning ingredients, many companies don’t believe there is a serious danger to the chemicals in the products.Some people believe the dangers are only related to what they might do to the hair, scalp or skin.Part of the issues with preservatives such as DMDM Hydantoin (a formaldehye-releasing ingredient) or Kathon (synthetic) is that they may have other potential safety issues than the ingredients they are designed to potentially replace.Although testing has been done using grapefruit seed extract, it has different challenges.Testing with tocopherol (vitamin E), vitamin A (retinyl) and vitamin C (ascorbc acid) is that they really don’t work as effectively as the traditional preservatives which are essential for containing the growth of bacteria, yeast, mold and other worse contaminants.2. TriclosanTriclosan is added to many hair care products to reduce or prevent bacterial contamination. Unfortunately this particular ingredient is known to be a skin irritant and suspected carcinogen.It’s also known to be an endocrine disruptor which can be associated with infertility, depression and weight gain in some.3. Formaldehyde-releasing preservativesYou can find formaldehyde-releasing preservatives is in many hair care products. It’s crazy that this chemical is a known carcinogen, yet still allowed to be used in personal care products!Not only has formaldehyde been linked to cancer, but it also can cause toxicity and asthma if inhaled.Some of the most common formaldehyde-releasing preservatives known to be carcinogenic includes, but is not limited to:DMDM hydantoinimidazolidinyl ureadiazolidinyl ureapolyoxymethylene ureasodium hydroxymethylglycinate2-bromo-2-nitropropane-1,3-diol (bromopol)glyoxalNote: For additional references review the following:Investigation on Formaldehyde Release From Preservatives in Cosmetics - PubMed4. Polyethylene Glycol aka PEGsPEGs are included in most hair care as a thickening agent. They tend to strip the hair of it's natural moisture and then need to add a silicone to make the hair feel soft again.It's been classified as a “developmental toxicant,” which means that it may interfere with human development.5. SulfatesSome people actually cringe at seeing the word “sulfate” in their products since they are famously known to be a drying agent to the hair.The truth?Not all sulfates are drying. Cleansing products are designed to cleanse hair. Others are specifically designed to strip the hair of product build-up.Sodium Lauryl Sulfate (SLS) / Sodium Laureth Sulfate (SLES)Sulfate can come in a couple of different forms, the worst offenders being Sodium Lauryl Sulfate (SLS) and Sodium Laureth Sulfate (SLES).These are bad guys of the sulfate family are SLS and SLES because they are known for being overly drying and sometimes actually stripping hair of natural oils. SLS and SLES are definitely the most common offenders.They are generally found in more than 90 percent of personal care and haircare products. Known as SLS’s for short, sulfates can be irritants to our skin, lungs and eyes.SLS and SLES sulfates are added to cleansing/shampoo formulas because they increase foaming.Unfortunately marketing has convinced us that sudsing and foaming is critical to demonstrate that our shampoos are working. Polydimethylsiloxane - Wikipedia That’s not necessary true.Some hair care experts believe that SLS is not really dangerous, it’s just irritating, drying and frizz producing. Others believe that SLES or Sodium Laureth Sulfate is fine and much better than SLS.Although lesser known, Sodium C14-16 olefin sulfonate, TEA-lauryl sulfate, TEA-dodecylbenzene and Alkyl sodium sulfate are considered more troublesome than either Sodium Lauryl Sulfate and Sodium Laureth Sulfate.SLS & SLES Might Be Okay If You Want A Deep Clean FeelingSLS and SLES might not be a big problem if you use a shampoo with them in it if you really enjoy a deep clean feeling, but beware, this should only be done once in a blue moon.Yes, it may leave your hair squeaky clean. Unfortunately it may also strip your hair of natural oils. Also, it’s very drying, which can lead to damage, rips, tears, splits, frizz and brittleness.One of the major concerns with SLS is its potential to interact and combine with other chemicals to form carcinogens. These combinations can lead to a host of other issues like kidney damage.Squalene - WikipediaThe Journal Of The American College Of Toxicology Warns About The SLS IngredientsAccording to the Journal of the American College of Toxicology, sulfates can cause damage to the immune system, cause separation of skin layers, rashes on the skin and scalp and inflame your skin leaving it dry and irritated.At minimum, just like any detergent, they will strip your hair of the essential oils they need to stay healthy as well as break down protein and retard healthy hair growth.The Good Guys In The Sulfate FamilyThe good guys within the sulfate family aren’t traditional “sulfates”, as they do the exact opposite and condition the hair.One of the best ones is Behentrimonium Methosulfate (BTMS). It is incredibly gentle and is one of the mildest detangling ingredients around, providing slip in a lot of your favorite conditioners. IBTMS is not irritating to the scalp, doesn’t cause buildup, and is derived from ingredients you likely have in your kitchen (rapeseed aka canola oil).Other sulfates which may also be much less toxic include Centrimonium Chloride, Polyquaternium 11, 57, 10, 37 and similar.Also Stearamidopropyl Dimethylamine is considered by some to be okay when used in the proper dosage amounts.Essential Oils May Also Trigger Reactions In Some PeopleEssential oils may be a problem, especially if they are present in large amounts, such as peppermint, menthol, lemon, lavender, and lime oils. Also, fragrant plant extracts may be irritating to some segments of the population.6. PhthalatesAre a cluster of chemicals used in hundreds to increase the flexibility and softness of plastics. The main phthalates in haircare are dimethyl phthalate often found in hair spray.It's often present in fragrance, but it’s not always listed in an obvious way on the ingredients list. Be careful since you may not see it on the ingredients list.It's a known endocrine disruptor. There have been links shown to an increased risk of breast cancer, early breast development in girls as well as reproductive birth defects in males and females.The Difficulty in Avoiding Phthalates:All U.S. cosmetics and personal care products are required to list their ingredients in order of their relative quantity, with the most frequently used ingredient listed first.However, any ingredients used in fragrances or mixtures are considered trade secrets and are exempt from these requirements.Phthalates are frequent components of fragrances, which often contain dozens of chemicals. The entire mixture simply appears as “fragrance” on the ingredient list. Thus, a product may include phthalates that are not listed on its label.This fragrance and trade secret loophole gives consumers little power to avoid phthalates when purchasing their personal care products.Consumers who are concerned about phthalates should e-mail or call the company who carries they products they buy to ask whether their products contain phthalates.Note: For more information on phthalates read:"Green Beauty" by Palliser, Janna - Science Scope, Vol. 34, Issue 4, December 20107. SiliconesNot all silicone ingredients are considered problematic. Yes, there are some like Dimethicone, but there are others which are not nearly as toxic.Silicones are very often found in both shampoos and conditioners. They create the illusion of healthy hair by coating the hair shaft to make it appear smooth and shiny.Some of the less toxic silicones or cones could actually be good for the hair. Certain silicones are incredible performers that provide bounce, slip, detangling, and even heat protection which are very important.Many styling products contain silicones especially those which protect hair from heating equipment such as straightening or curling irons.In these types of products, they are okay as long as they are applied to the ends of the hair and kept away from the scalp.The downside? Some also coat the scalp, clogging your pores and drying your hair from the inside out. These should be avoided at all costs in shampoos and conditioners.Of course It’s important to be weary of certain silicones which can lead to buildup in the hair.There are wash-off silicones that have even been banned in some parts of the world because of their environmental risks to the water system.Whereas non-rinse off products are allowed since they’re applied to the skin or hair, posing a lesser environmental risk since the ingredients evaporate once dried, not leading to water risk.Just remember, not all silicones are created equally. Do your research and ask questions about products with cones to understand all the various benefits versus risk factors.8. DimethiconeSome silicones are considered much worse than others. Dimethicone is considered a bad one along with D4, D5 and D6.Dimethicone Is a synthetic polymer and a form of silicone with two methyl groups attached (hence the name Di-methicone). It's present in most haircare products as it's cheap and creates synthetic softness and smoothing.Not only will it most likely dry out your hair long term. but it can build up causing greasy roots and very heavy ends. There have also been cases where it causes an itchy, burning scalp.Dimethicone is considered to have bad side effects. The Canadian Government has recently classified it as a potential toxin that requires further study.9. TriethanolamineIs used to alter the pH of the products and act as an emulsifier to help other ingredients mix together better.It's highly absorptive and can lead to irritation of the skin and eyes. Continuous exposure has also been linked to asthma and allergic reactions.10. AlcoholAlmost all hair-care products contain some form of alcohol as it's used for it's evaporation qualities. Short chain alcohols are the ones to steer clear of - SD Alcohol 40, Ethanol, Propyl, Porpanol, IsopropylIt can really dry out your hair causing split ends and breakage.11. PVP/ VA CopolymerIs a synthetic vinyl polymer used in hair care as a filler or binder.It’s another toxic chemical derived from petroleum and is used as it's considered the ‘ideal’ styling aid.12. Cocamide DEAFound in shampoos, it has an innocent sounding name and it is derived from coconut oil.Unfortunately it’s a modification of the natural form of coconut oil. It’s an unnatural toxin. The State of California deemed it a known carcinogen in 2012.13. Behentrimonium ChlorideAlso known as Docosyltrimethylammonium chloride this chemical can be found in some conditioners. This chemical is harsh enough to cause skin and eye irritation in many people.14. Diethanolamine and TriethanolamineProducts containing Diethanolamine (DEA) and Triethanolamine (TEA) can cause scalp irritation or bad allergic reactions.They have also been known to destroy important components of your hair such as the keratin, making your hair dry, brittle, and lifeless.15. Isopropyl AlcoholIsopropyl alcohol is found in some conditions. It is also used in antifreeze, wood finish and shellac - which should give you some indication of how bad it is for you. It is known to strip your hair of its natural oils and can cause damage to your hair.All alcohols should in fact be avoided in large quantities. As a guide you should avoid any shampoo or conditioner which has any alcohol or alcohol derivative in the first four ingredients listed on their label.16. Polyethelyne GlycolAlso called PEG, Polyethelyne or Polyoxyethelyne, this ingredient is included in shampoos as a thickening agent. It strips hair and skin of their natural moisture.Lastly, you should also watch out for synthetic colors and fragrances which many people have reactions to, particularly causing irritation of the scalp.Please remember that your body (and scalp) is your temple. In next week’s article we will be looking at the nutrients you should be using to clean your hair.Animal Derived IngredientsSome consumers who are strict vegans and/or vegetarians may have a problem with animal derived ingredients and will avoid products with the following common ingredients:LanolinMuskCollagenSqualeneThis includes some oils which are known to be taken from animals such as Emu Oil.Not All Ingredients Are Necessarily Toxic Or Need To Be Avoided When Choosing A Shampoo/ConditionerYes, there are some ingredients in shampoo and conditioners which may be toxic. However not all of them are.Should you freak out about it? Probably not. If the chemicals in hair, scalp and skin products are worrisome, just imagine the ingredients in our the food chain?Please keep in mind that some ingredients actually offer a benefit to the scalp, hair and skin.As long as you use them as they were created to be utilized, there may not be any risk factor. When in doubt always check with your trusted physician.Just because shampoo and conditioners may have some ingredients in them with a bad reputation, it may not necessarily be bad for you, your hair or the goals you are trying to achieve for your hair.Be Mindful Of Your Own Personal Hair Care GoalsBe mindful of what your hair needs and goals are. Maybe you need some type of cone product to keep your hair smooth and prevent breakage. If that is the case you may also need a product which periodically require a more cleansing product to remove product and/or cone build-up.Also be aware that there is a lot of fear mongering about shampoo, conditioner and other hair product ingredients. In some cases you need certain ingredients to prevent the growth of fungus or make sure the products has a minimum level of sudsing action.Manufacturers have become a lot more savvy about substituting harmful ingredients for safer one. When in doubt do your homework and research. Talk to a trusted hair professional about which products and ingredients are best for you.Finally, remember, that what may work for you and your hair may not work for anyone else in the hair Universe.Best wishes to all.References:Effects of Several Cosmetic Preservatives on ROS-Dependent Apoptosis of Rat Neural Progenitor CellsInvestigation on Formaldehyde Release From Preservatives in Cosmetics - PubMed"Green Beauty" by Palliser, Janna - Science Scope, Vol. 34, Issue 4, December 2010Amended Safety Assessment of Formaldehyde and Methylene Glycol as Used in Cosmetics - Ivan J. Boyer, Bart Heldreth, Wilma F. Bergfeld, Donald V. Belsito, Ronald A. Hill, Curtis D. Klaassen, Daniel C. Liebler, James G. Marks, Ronald C. Shank, Thomas J. Slaga, Paul W. Snyder, F. Alan Andersen, 2013Safe Cosmetics
How were the "top quality" swords made in the 15th and 16th century in Europe, from iron ore to a finished blade?
Luca Nic thanks for asking me this!I should preface this answer by noting that I only had high school chemistry (and disliked it), no academic background in this area and that a lot of the chemistry and research is still new.To understand what iron ore you want it is important to know what a bar of steel does when it is forged by a smith.Oxygen is in the air all around us and it is a pretty oxidising substance. If you place a piece of iron or steel outside or in a room with moisture the moisture will facilitate the oxidisation of the steel. Oxygen will bind itself to iron (Fe) and form an iron oxide named rust.As per wikipediaRust consists of hydrated iron(III) oxides Fe2O3·nH2O and iron(III) oxide-hydroxide (FeO(OH), Fe(OH)3).Now there are a lot of different Iron oxides each with a different chemical formula (see: Iron oxide - Wikipedia) and many of them are involved in the forging of a iron/steel object. The inclusions in steel or iron commonly called slags also consist of various Iron oxides and silicon dioxide but we will get to that later.If a smith puts a bar of steel in the forge to heat it up something to similar to rusting happens. With a working temperature of several hundred degrees the steel or iron will react with oxygen much more readily than at room temperature. Every time the smith takes the bar or object out of the forge it will already be covered in a layer of iron oxides called Hammerscale - Wikipedia. Modern chemists still haven’t figured out exactly which one it is which shows how arcane this subject can be for a species that put a man on the moon.Now since you do not want to forge an object with iron oxides all over it smiths use a brush to brush it off before they start to hammer away. If you were to hammer a piece without brushing you would end up forcing the layer of iron oxide into the material which is bad.A modern smith using a steel brush to remove the hammerscale on a red hot billetThe high temperature of the steel will also allow oxygen to bind with the carbon (C) atoms in the steel to form carbon dioxide (C02) which is a gas and escapes through the chimney. What this means is that with repeatedly heating and hammering a piece of metal you will end up lowering the carbon percentage of the steel bar and you will reduce the weight of the steel bar because much of it disappears as iron oxides. Just how much weight is lost and how how much the carbon percentage is lowered depends on a wide variety of factors. From what we know weight loss of 50% to 90% wasn’t out of the ordinary if you look at extremes like going from a bloom produced in a bloomery to finished product.From an economic point of view it would be best to forge an object in as few heatings as possible because that would allow for minimal wastage of material.In practice a smith of the day would have to start with a bar of steel that weighed more than the finished product and contained a higher carbon content.A common procedure of blacksmiths to this day is called Forge welding - Wikipedia. It involves heating two pieces of metal to a very high temperature before joining them together and beating it. It allows for two pieces of metal to be welded together in a solid state and forms the bread and butter of blacksmithing.There is however one complication in this procedure. As mentioned above heating the steel or iron results in a layer of iron oxide/hammerscale forming on the surface. Iron oxide forms an impediment to welding and even if a weld succeeds you will have a welded piece with iron oxide sandwiched between the layers. That’s not something you really want because that iron oxide inclusion forms a weak point or a fault line. You’ve basically introduced a critical weakness in the material. Brushing it off with a brush like is done normally isn’t the whole solution though.The solution is to add a Flux (metallurgy) - Wikipedia.late 14c., "abnormally copious flow," from Old French flus "a flowing, a rolling; a bleeding" (Modern French flux), or directly from Latin fluxus (adj.) "flowing, loose, slack," past participle of fluere "to flow" (see fluent). Originally "excessive flow" (of blood or excrement), it also was an early name for "dysentery;" sense of "continuous succession of changes" is first recorded 1620s. The verb is early 15c., from the noun. Origin and meaning of flux by Online Etymology DictionaryAn early 17th century Dutch song actually uses this word a pun when it describes Spanish soldiers fleeing quickly (Dutch: vlug) by pronouncing it as flux; something to the effect of shitting themselves/having the runs and literally running for their lives.That aside modern fluxes such as borax are well known but in the past they used various silicate sands. When you sprinkle this on the surface you want to weld while it is in the forge it screens the metal surface from the oxygen containing air thus reducing iron oxide/hammerscale formed on the surface. Furthermore is reacts with the iron oxide that is formed to produce… an iron chrysolite named Fayalite - Wikipedia. This iron molecule differs from the typical iron oxide formed on the surface in one important aspect; it is liquid rather than solid at welding temperatures. What this means is that it allows a smith to hammer from one side to the other or from the core to the edges and while he does that the liquid fayalite is squeezed out between the weld producing a much cleaner weld.The one caveat is that even with the usage of a flux some of the iron oxide/chrysolite (be it Fayalite or hammerscale) still remains in the weld. Skill of the smith and proper usage of flux makes forge welding viable but at the end of the day its still going to result in “slag” inclusions which forms a weakness (the weld lines or seams aren’t usually visible to the naked eye and require a microscope to see). Modern readers might ask why bother with forge welding at all?Some forged objects simply require forge welding to give them the desired shape and there is really no way around it. Some complex hilts/guards found on 16th century European swords simply require forge welding and so do many domestic products.Sometimes, or rather quite often, blacksmiths didn’t have a single lump of steel/iron large enough to make the object they wanted. This might seem odd but it is important to realise most modern researchers argue the European Plate Armour was only possible because the production of steel/iron in large blooms only became a thing in the Late Middle Ages. Other types of armour such as scale, lorica segmentata, mail, coats of plate and brigandines are largely a compromise that was needed because large sheet metal simply wasn’t around before then.The historical price of steel was also a lot higher than that of the iron which had a lower carbon content. Many swords were simply made with an iron ‘body’ while only the cutting edges or the tip were made from steel welded onto the iron body. Aside from pure economics some sword designs also have this because the different qualities of steel and iron made for a good compromise. The Japanese Katana features a very hard and high carbon edge on a medium steel or iron body. Making the entire blade out of the hard edge material would simply result in a sword to brittle to use.The fourth reason for forge welding is one of the most important and an often overlooked one. The “starting” material will be a piece of iron or steel that is heterogeneous in composition. Bloomery iron/steel isn’t brought to a molten state in the smelter but rather has a spongy/runny consistency. The excess carbon in the bloomery is going to carburize the outside of a bloom more than the inside (see; Carburizing - Wikipedia). The carbon content isn’t going to be equally distributed throughout it which means the hardness and ductility are going to be all over the place. One part might be of a high carbon content and is quite hard while another part is nearly carbon free and thus very soft. Making a sword out of this would result in having soft and hard spots throughout, something which is compounded by heat treating which only acts on steel with carbon in it.A small bloom straight from the smelter being consolidated by repeated hammer blowsAside from the unequal carbon distribution iron/steel of the day also contained slag. Most forms of iron ore are basically various iron oxides like rust being trapped in a rock and the process of smelting is melting this rock so that the oxygen is stripped from the iron oxide while the surrounding rock dissolves. The iron will coalesce in a spongy lump known as a bloom will other materials will either exit in gaseous form through the flue or run down as a liquid to the bottom of the furnace.Steel is the name for an alloy of iron which has carbon dissolved in it, a process which naturally occurs inside a bloomery but can be controlled by a skilled smelter. Iron has a crystalline microstructure due to the way iron atoms align. When carbon is dissolved in this it will alter the microstructure(s) and result in different microstructures which each have a different name and the existence of which depends on the amount of carbon dissolved. Furthermore heating steel and rapidly cooling it with result in a special microstructure. The different microstructures and the degree to which they are present each alter the quality of the steel and influence hardness and ductility.That’s a really elementary explanation but I will get back to it later.Slag resulting from the original smelting process is a mix of iron oxides and silicon dioxides. The iron oxides are molecules from which the oxygen wasn’t stripped and the silicon dioxides is the “rock” which didn’t get removed. Both these types of slag sit in lumps inside the bloom and this is a problem. A lump of slag doesn’t dissolve into iron like carbon does. Carbon atoms readily dissolve into the matrix formed by iron atoms but slag is a whole molecule. The presence of these lumps of slag is delirious because it forms a weak point or fault line. When stresses are applied the steel will first split or rupture along these lumps. If you take a bar or sword of steel or iron with a lot of slag in it and hit it with a hammer it might shatter.Chemically pure, or near enough pure, iron is a soft material that can bend quite a bit before it breaks. If slag is present in small quantities it can actually make the iron harder but when it comes in quantities too large it will actually make iron brittle; more brittle than very high carbon steel. This isn’t a theoretical concern either because absolutely slag saturated pieces of iron armour survived. Alan Williams examined Roman armour made of near carbon free iron with so much slag in it the resulting metal was actually worse than bronze.Aside from smelting in such a way as to include as little slag as possible and trying to get an equal carbon distribution one can remedy the faults introduced by slag and unequal carbon distribution with repeated folding. The procedure is most famously known from the forging of the Japanese katana but the process was really universal in pre-industrial times. If you fold a piece of metal onto itself the carbon will be spread more equally and if you fold an already folded piece you will now have four folds. It increased exponentially from there one which means you can have 1024 folds in a piece of metal by merely folding it onto itself eleven times. Sometimes they initially stacked pieces of different carbon contents using a high and low carbon piece resulting in a mixed/average carbon content.A stylised diagram showing the exponentially increasing layers in a piece of steel repeatedly folded onto itselfThus the carbon will be spread throughout the billet/bar of steel but this procedure will also remedy slag inclusions to a degree. Rather than having large lumps of the stuff inside your bar of metal these procedure will draw them out, squish them and then draw them out again. In effect a round lump will be turned into a long piece of string running throughout the entire bar; imagine glass fiber strings running from one end to the other. Rather than a large critical defect you now have tiny bits of slag which are much less debilitating.But wait Pieter!Didn’t you say something about the forge welding with flux being imperfect and introducing new slag into the material?Yes I did!Every time you fold that piece of metal onto itself you will produce a weld line or seam consisting of iron oxides from hammerscale of fayalite not being squished out during welding and hammering. In effect you are using a method that introduces flaws/slag into the bar to homogenise the carbon content and fix problems resulting from the original slag in it. As mentioned before the repeated heating and hammering will also result of a loss of weight, due to oxidisation of the iron, and a lowering of the carbon content. That’s simply the way of pre-industrial smithing; one fault introducing method to fix faults in a heterogeneous metal.In most swords with an ordinary mirror or satin polish you wouldn’t actually see these weld lines. The one famous exception is swords polished in the Japanese manner. Using a grit that does polish some metal/slag of one hardness but not that of a higher hardness will bring out the contrast for the naked eye to see.A modern structural engineer would see shitty welds and potentially layers of high and low carbon but you can’t deny the aesthetic appeal.The layered structure (hada) on a Japanese KatanaA 7th century saex polished in the same manner; the pittig is due to corrosion, and one weld seam is very dramatic (i.e. poor) but the horizontal layered grain can be discernedAside from carbon and slag that are found in steel some trace elements are also important.A common modern elements introduced into carbon steel is chromium. This has the effect of making the steel much more resistant to rust formation; we know this alloy as stainless steel. The addition of chromium does however alter the characteristics of the steel making it unsuitable for modern appliances such as springs or bicycle chains and historical objects like swords and armour, not that the latter mattered much as stainless steel was only produced from the industrial era onward.Much more common in historical steels and irons are sulphur and phosphorous both originating from the ores used and the smelting process. Phosphorous is often found in iron/steel made from so called bog ore. In small quantities it might make iron low in carbon content a little harder but it also introduces a thing called cold shorting; meaning that if the temperature gets low the steel/iron becomes more brittle. Depending on the content this can occur at temperature ranges in which people fought and could result in a lot of cracked or broken blades. In historical pattern welded blades the contrast showing the figures seems to have been achieved by alternating normal iron and phosphorous containing iron rather than different carbon content steels as in modern reproductions. Same have taken this to mean that pattern welding wasn’t really all that functional but more decorative.The opposite to cold shorting is called hot shorting which means the metal gets brittle in high temperatures; sulphur is commonly said to cause this. While the temperatures at which this occurs means that the wielder of a sword wouldn’t have an issue with it unless he takes it into Dante’s Inferno it causes problems for blacksmiths. One might hit a red hot piece of metal to forge it into the desired shape only to fracture it. Furthermore sulphur seems to increase brittleness at all temperatures and thus is seen as a bad thing to have.The third important element is Manganese which confers a host of beneficial qualities on the steel in which it is. For one it tends to counteract the negative effects of sulphur in steel.As per wikipediaManganese is essential to iron and steel production by virtue of its sulfur-fixing, deoxidizing, and alloying properties, as first recognized by the British metallurgist Robert Forester Mushet (1811–1891) who, in 1856, introduced the element, in the form of Spiegeleisen, into steel for the specific purpose of removing excess dissolved oxygen, sulfur, and phosphorus in order to improve its malleability. Steelmaking, including its ironmaking component, has accounted for most manganese demand, presently in the range of 85% to 90% of the total demand.The last is somewhat important for people testing reproductions of historical weapons. As I have hopefully shown above pre-industrial steel was quite a bit different. Slag inclusions and unequal carbon distribution are hallmark features of bloomery steel but are often absent in modern steel. Even if one accepts that fact manganese should also be taken into account. Today even plain carbon steel, additive free as we might call it, still contains Manganese added in extra during the production process because it is so useful. Getting your hands on modern steel without it or in lower quantities might prove difficult. Some historical steel did indeed contain this most helpful element but it much did not.Taking all the above into account a smith seeking to make a top quality blade in the 15th or 16th century would want the following;A starting material that was high enough in carbon content. For one having a decent carbon content is necessary for good durable cutting edges or proper armour. A decent carbon content would also make the oxidation of carbon during the forging process less debilitating. An added benefit is that the carbon content in bloomery steel/iron tended to have an inverse relation with the slag content. Alan Williams only recently got around to writing about this but the procedure that smelters used to produce high carbon blooms also resulted in a much lower slag content. This procedure revolves around temperature and air control, ratio of fuel (charcoal) to ore and the length of time which a bloom was left in the bloomery,A starting material that contained very little slag to begin with as mentioned above. The lack of slag is a very important factor in historical steel and iron being almost as important as carbon content and heat treatment. Furthermore a low slag content would reduce the need for folding especially if the starting material already had decent carbon distribution. Not having to fold means less material wasted, less carbon leeching and fewer folding/welding procedures.A starting material large enough to forge a sword out of as this eliminates the need to forge weld two or more pieces together. An exception does exist in that swords were also constructed with a high carbon edge or mantle wrapped around a low carbon core. Furthermore some swords had a tang and lower edge made out of lower carbon steel with most of the sword extending beyond the hilt being of higher carbon steel.A starting material with a lack of ‘bad’ elements in it like Sulphur or Phosphorous and perhaps some ‘good’ elements like Manganese.*Exceptions apply depending on the type of sword you want to forgeA starting material like that is basically close to modern industrially produced carbon steel. It represents the best steel a bloomery could produce for European sword making and when heat treated properly matches some of the more exotic swords.It allows a smith to produce what is, in pre-industrial terms, a monosteel sword; a sword forged entirely out of one piece of steel, with few slag inclusions, having no or very few weld lines between different pieces of steel and having a very homogeneous carbon percentage throughout. There is the mistaken belief that all medieval swords from the High Middle Ages were of this sort, quite the contrary, but they did exist.These steels were rarely hypereutectoid steel (carbon percentage of 0.8% or more) and when that was produced it seems like they considered it a mistake. I know of a 15th century piece of armour that was hypereutectoid and it looks like the smith actually tried to anneal it to reduce the hardness. At such a high carbon percentage hardness can actually become a fault in armour and in swords you would need to built it like a katana to compensate.With the preferred carbon percentage at but mostly below 0.8% a heat treated and tempered sword forged from a single ingot would show a uniform tempered martensite structure throughout the entire blade with (very) little slag. A hardness of around 450–570 VPH could be achieved and the sword would have a spring like quality. If a weld seam does show it can actually be hard to tell if that was because two very good ingots were welded together or whether it was due to folding a single ingot onto itself. Occasionally a monosteel with a core and edge being of similar makeup was forged onto an iron or lower carbon tang.The type of heat treatment varied with both quenching and tempering, slack quenching, time quenching and other methods being employed. The exact type employed can often be deduced from the microstructure in the edge and core.Another common type consisted of a steel outside and a iron or low carbon core. The lower carbon was sandwiched between a higher carbon jacket; the resulting billet would then be drawn out and forged into a sword shape. This is different from the pure ‘monosteel’ sword or monosteel blade forged onto an iron tang because the low carbon steel/iron actually runs through the core of the blade.Inserting a low carbon core into a harder jacket; the billet will then be forged into a swordLike the ‘monosteel’ sword a sword like this could be heat treated to get a martensite microstructure on the edge.Some cheaper edged weapons are entirely forged out of iron/low carbon steel and then given a steel edge by carburizing it. Such a type could also be heat treated on the edges though the entire body would not be. One could also take an iron body and insert only little bits of steel on the edges.This diagram of the cross section of an early medieval seax gives some idea of what things can be identifiedA mostly iron body with slag inclusions and the steel edge has been welded. The welded on edge was then heat treated and achieved a respectable hardness.I would content that a ‘monosteel’ blade with a uniform carbon content and microstructure throughout the edge and core is at least from a modern perspective the most advanced one. Whereby a monosteel blade made from a single ingot is more ‘advanced’ than one made out of more monosteel bits welded together. Though allowance should be made for the fact that good welding and bad welding are two world apart. Whether an entirely monosteel sword or a monosteel blade forged onto a softer tang is better I would not know.A good quality sword made with an iron core wrapped in a steel jacket would also make for a good sword and it seems blades like those of Toledo were made like that. I cannot say whether that or a monosteel blade was the ultimate form and I very much suspect both types of manufacture led to some of the highest quality blades. Both at least better than iron bodies with carburized edges or steel edges forge welded on.Part 2All of what mentioned above doesn’t directly tell you what is actually considered a good sword. Eric Lowe could probably tell you quite a bit more about this but here are some of the essentials.Many of the qualities of a sword arise from the weight, balance and general shape and there really is no ‘best’ design in that regard. Peter Johnsson has recently started to research whether or not medieval swords were designed according to strict rules of geometry so common in Medieval Art, architecture and occasionally naval design.http://www.peterjohnsson.com/higher-understanding-and-deeper-reckoning/The blade of a sword is a complex three dimensional shape. You can make it long or short and wide or thin; the point can taper right from the hilt onward to form the pointed swords of the Late Middle Ages. The taper can be acute or gradual or it might even be absent until the last third of the blade. You can also taper the sword in the other dimensional plane so that it isn’t as thick at the center of percussion as it is near the hilt.Distal and profile taper in a common kitchen knifeUnderstanding Blade PropertiesIf you take the length, profile taper and distal taper into account you can imagine a large number of different designs are possible which affect the balance of the blade, it’s cutting capacity and how well it will stab something.Cross sections of swords, which only represents the cross section of the sword at one particular point, illustrate this.On Late medieval swords you will often find the profile tapers very acutely to make for a sharp point. To compensate for that fact the center is often raised as in the diamond cross section example and distal taper is kept to a minimum. This will result in a spike like tip that is very acute but still has stiffness so that the blade doesn’t flex when it hits resistant material.However this acute profile tapers means that the blade isn’t that thick at the portion of the sword with which you would usually cut which is detrimental to cutting ability. Furthermore the raised ridge on the center of the blade and minimal distal taper means the edge angle is very obtuse. As the edge meets meat the thickness rapidly increasing also increases the resistance the blade meets.Two Japanese swords show the concept of the edge angle; generally the more obtuse it is the less well suited it is for cutting. It also illustrates that a single edge sword has the potential for a much more gradual angle than a doubled edged sword of similar profile widthBlade design is really a study on itself but here are some of the general ideas;1.A straight sword is better for stabbing as the point aligns with the direction of the force applied. A curved sword is general reckoned to be better as cutting while less adapted for thrusting.2. For maximised cutting potential you want a wide profile at the point of impact and a gradual edge or one that terminates quickly as on the broad fullered ‘viking’ swords.3. For maximised stabbing potential you want an acute profile taper and a strong central ridge to provide stiffness, ideally a double edged sword as two edges can more easily penetrate resistant material.Aside from the hundreds of other blade design considerations it becomes evident that many features suited for cutting aren’t good for stabbing and the other way around. Therefore a blade smith really has to ask whether he wants a middle of the road kind of design or one that tends to specialise more.Then, even when the blade is finished, the mounting of the hilt and pommel can alter the balance of the blade and the grinding or sharpening of edges will give different kinds of performance.None of this actually has much to do with the metal quality or way of forging a sword. Some designs certainly favour certain types of steel and certain forging techniques but the metal qualities are vitally important when it comes to edges and blade failure.Edge blunting, edge failure and blade failure are things I want to look at.Edge angle or geometry has already been discussed as a design but sharpness is more something that has to do with maintenance and metal quality. Some factors are visible with the eye but others require a microscope to actually see.Here is the edge of a stropped blade; the edge is neat and the surface on either side is smoothWhen this blade hits something, basically anything, the edge will start to wear down. That straight edge is going to have microscopic notches, the edge might be folded or bent slightly and the surface around the edge will grow rougher.Sharpening involves using stones or grit to grind away the folded over edge, the notches (bringing back the angle) and giving the surface on either side of the edge a smooth polish.The key thing here is that a hard material will be sharp for longer than a softer one. A softer edge material will fold or chip faster on a microscopic level and the surface will grow rough faster. This isn’t an academic concern either as blunting occurs very fast. The reason your razor blade is made from very hard steel is that it would blunt after a couple of shaving strokes if it was soft. Keep in mind that a sword would hit weapons flesh, bone, textile, shields and armour all the time during battle. Losing that edge while in combat is normal which is why you sharpen a blade after every usage. A steel with a high carbon content will be harder than steel or iron with a lot carbon content. Furthermore the process of heat treating carbon steel with give it a martensite microstructure which is much harder than untreated steel. Some materials like glass and obsidian are even harder than steel and will keep a good edge much longer.Edge failure is something much more visible to the naked eye, you don’t need a microscope to see it when it happens.The edge is visible folded over in the two swords belowThe sword below has notches cut into itWhen period accounts mention saw toothed blades this is what was meant. In some cases the edge folds over on a macroscopic scale. In others blade contact or contact with hard surfaces results in notches being cut into the edge.This is what we might call plastic deformation of the edge. Plastic, as opposed to elastic, deformation means that once the force applied to the material disappears the shape will still remain changed. Plastic deformation occurs more in softer materials. What this means is that soft edges both blunt earlier than hard edges and have a greater risk of being notched or folded over.However harder edges can also suffer from damage due to brittle failure or chipping. Hard materials such as obsidian, glass or very high carbon steel tend to be a bit more brittle which means that the material cannot have much plastic deformation. It will form hairline fractures and simply shatter rather than bend.This bronze sword shows chipped notches, the metal wasn’t folded or pressed aside but just broke off.The presence of sulphur, slag, weld lines or pockets of high carbon resulting from improper homogenisation creates these brittle areas.Aside from such considerations as the ability to maintain a sharp edge and having an edge that doesn’t fail there is the entire blade itself. Again things like plastic deformation (bending) can occur in soft blades while brittle blades can snap.Ritually bend swordGuess what happened to the sword Narsil from Lord of the Rings;Holy Sh*t under stress it didn’t just shatter in one place but it was actually shattered into six pieces. Evidently Narsil is a very brittle blade pointing to a carbon percentage that is too high (through out it or in some places), major slag inclusions or very poor weld seams. Rather than tossing it away they actually kept the thing for a very long time and then repaired it by means of forge welding with all potential issues that might bring with it.I am pretty sure Elrond wanted to get Aragon killed because the least he could do for a friend was make another sword.All this said and done two identical shaped swords of which one is made out of fantastic quality steel while the other is craptastic would cut reasonable well for the first time. It’s just that the crappy sword would dull much much faster, get a warped edge much faster and has a significantly higher risk of breaking or bending in battle.Even modern replica’s still face these problems and more than a few well made swords produced with industrial steel have simply broken. High quality blades like those produced by Albion still occasionally snap or bendObvious brittle failureFor people in the past the highest quality swords weren’t necessarily light sabers that would slice through everything but rather reliable blades that kept an edge well during a fight and had a low chance of breaking in battle.Part 3Will be written soon…
- Home >
- Catalog >
- Miscellaneous >
- Manual Sample >
- Instruction Manual Sample >
- Toshiba Instruction Manual Sample >
- Case Study: Cleaners Remove Silicone From