How to Edit The Article-International Project Work Breakdown and make a signature Online
Start on editing, signing and sharing your Article-International Project Work Breakdown online following these easy steps:
- click the Get Form or Get Form Now button on the current page to direct to the PDF editor.
- hold on a second before the Article-International Project Work Breakdown is loaded
- Use the tools in the top toolbar to edit the file, and the added content will be saved automatically
- Download your modified file.
A top-rated Tool to Edit and Sign the Article-International Project Work Breakdown
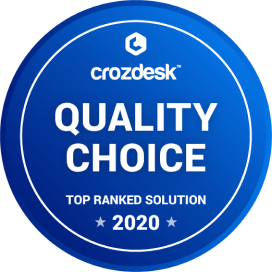
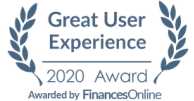
A clear tutorial on editing Article-International Project Work Breakdown Online
It has become very easy these days to edit your PDF files online, and CocoDoc is the best free PDF editor you have ever seen to make some editing to your file and save it. Follow our simple tutorial to start!
- Click the Get Form or Get Form Now button on the current page to start modifying your PDF
- Add, modify or erase your text using the editing tools on the top tool pane.
- Affter editing your content, put on the date and create a signature to finalize it.
- Go over it agian your form before you click and download it
How to add a signature on your Article-International Project Work Breakdown
Though most people are in the habit of signing paper documents by handwriting, electronic signatures are becoming more accepted, follow these steps to add a signature for free!
- Click the Get Form or Get Form Now button to begin editing on Article-International Project Work Breakdown in CocoDoc PDF editor.
- Click on the Sign icon in the tool box on the top
- A box will pop up, click Add new signature button and you'll be given three choices—Type, Draw, and Upload. Once you're done, click the Save button.
- Move and settle the signature inside your PDF file
How to add a textbox on your Article-International Project Work Breakdown
If you have the need to add a text box on your PDF so you can customize your special content, take a few easy steps to finish it.
- Open the PDF file in CocoDoc PDF editor.
- Click Text Box on the top toolbar and move your mouse to carry it wherever you want to put it.
- Fill in the content you need to insert. After you’ve writed down the text, you can take use of the text editing tools to resize, color or bold the text.
- When you're done, click OK to save it. If you’re not settle for the text, click on the trash can icon to delete it and start afresh.
An easy guide to Edit Your Article-International Project Work Breakdown on G Suite
If you are seeking a solution for PDF editing on G suite, CocoDoc PDF editor is a recommended tool that can be used directly from Google Drive to create or edit files.
- Find CocoDoc PDF editor and install the add-on for google drive.
- Right-click on a chosen file in your Google Drive and select Open With.
- Select CocoDoc PDF on the popup list to open your file with and allow CocoDoc to access your google account.
- Make changes to PDF files, adding text, images, editing existing text, highlight important part, give it a good polish in CocoDoc PDF editor before hitting the Download button.
PDF Editor FAQ
I've heard Prince Harry was hired by BetterUp to be their Chief Impact Officer. What exactly is a Chief Impact Officer? What qualifications and experience are required?
I've heard Prince Harry was hired by BetterUp to be their Chief Impact Officer. What exactly is a Chief Impact Officer? What qualifications and experience are required?It seems no one knows the answer to this, so I thought I’d ask it… and answer it?In the introductory message announcing Harry as the new Chief Impact Officer at BetterUp, a job description is given by Prince Harry himself. [1] What it boils down to really is two main components;External – this is public speaking engagements on behalf of BetterUp, outreach programs, creating videos and interactives, factsheets, bringing together groups of people and organisations, starting new initiatives, and generally using his ability to network for the cause, generally advocacy, raising awareness, starting conversations.Internal – this is working with the executive team to make decisions about the overall vision, mission and strategy of the organisation with a focus on maximising impact.ExternalPrince Harry has been the driving force behind several large-scale initiatives which demonstrate his ability to fulfil the external part of the job.Not only is outreach and starting conversations one of the few things that members of the Royal Family can actually do for an organisation they patronise, it’s also a key area that Harry excels in.In the case of Travalyst, it’s a non-profit that has brought together half a dozen large international travel companies to tackle environmental and social issues caused by travel and tourism. HeadsTogether is a similar concept, except that it brings together mental health charities to deliver programs such as Mentally Healthy Schools and Mental Health at Work.Invictus is an international multi-disciplinary competitive event for veterans, encouraging physical activity, sportsmanship, and regaining a sense of purpose after medical discharge. HeadFIT for Life is an app created to help veterans improve their mental health, which rolled out early last year.These experiences fit pretty neatly with the first point above about ‘starting conversations’, networking, and creating outreach programs (digital and personal).InternalThe strategic direction, vision and mission of the organisation are all very ‘big picture’, which is a level that Prince Harry has worked on several times before as a principal or director of the various organisations and groups that he has been a part of.This includes The Royal Foundation, SussexRoyal & Archewell, Sentebale, Travalyst, Invictus Games Foundation, Endeavour Fund Awards and so on, each of which he has had a key role in, or at least ensuring the right people are hired to execute it. If there’s one thing he has ever done almost naturally, it’s developing a vision and finding and motivating the right people to execute it.Anthony Painter, Chief Impact Officer at the Royal Society of ArtsThe title of ‘Chief Impact Officer’ is relatively rare at the moment, so there aren’t a lot of resources about it, or people you can ask. However, there is a Chief Impact Officer at the Royal Society of Arts in London, with that role currently filled by Anthony Painter.It seems likely that there will be some parallels between Painter’s job and Prince Harry’s. Painter was interviewed about his job by the Telegraph, with relevant excerpts below.The job description at the RSA;Painter, who has been in post since December 2019, oversees projects through which the RSA, in its words, finds practical solutions to social challenges.A recent example of Painter’s work for the RSA is the Cities of Learning project, in which the society has teamed up with coders and councils to create an app that helps members of the public find learning opportunities that might lead to employment.That kind of project, which helps individuals improve their circumstances, is in some ways similar to the work of Prince Harry’s new employer. BetterUp, which is said to be worth $1.73 billion, offers personal coaching to people seeking “meaningful, vibrant lives”.Breakdown of how Painter spends his time:1/4 Building and maintaining external relationships, including funding partnerships.1/4 Devising strategy – the details of and vision for their projects.1/2 Research into helping others in the team develop their own ideas.Qualifications, experience, and personal qualities:Painter, 46, has previously directed the Independent Review of the Police Federation and is the author of books about politics and media.“My observation of Harry is that he’s someone who is clearly committed to impacts. I mean, he's behind the Invictus Games and so on. I get a sense that he's got a high degree of emotional intelligence.Whether he can translate that into success remains to be seen. It’s hard and it’s tough. I’m very happy to help him think it through if he wants to get in touch. But other than that, I think he's probably got a lot of what matters to begin with. And I'm sure he can lead on networks of expertise and resources, and so on, to help him make a difference.To succeed in the role you need resilience and the ability to find focus in a broad remit. You need the ability to understand perspectives beyond your own expertise, and you need to be able find ways of communicating diplomatically.”You can read the full article at the link.[2]Overall the role looks like a paid position similar to the big picture advocacy work that Prince Harry was already doing, and has been doing for several years.Footnotes[1] Prince Harry, The Duke of Sussex joins BetterUp as Chief Impact Officer[2] What exactly does a chief impact officer do? We asked a chief impact officer
What are the best corporate video productions, video production websites, and blog sites?
Hiring a dedicated producer is often not possible, so it’s important to find the right software solutions for your video production management instead. Choosing the right tools can be difficult, but you’ll need to carefully choose the ideal tool for your projects to succeed.Here are few options, starting with a few of the best general video production project management software, and then moving onto the specialized options.General video production software can often be a great choice, given that these tools strongly emphasize usability. As an added bonus, these tools can be adjusted to fit your exact needs.1. FilestageFilestage is a tool for the review and approval of content. It makes it easy for video teams to share their important planning and organization documents with each other. Within seconds, creative professionals can spin up new projects and establish a review and approval workflow.In terms of key features for video production management, you’ll be sure to appreciate the simplicity of this tool. So internal and external team members can rapidly join and start leaving in-context feedback right away.Pros+ It’s easy to use.+ It’s easy to access.+ It allows quick tracking.Con– Its mobile app is still in development.2. AsanaAsana is another project management tool that helps creative teams generate tasks in a shared space. Since this tool offers a range of project views that can reveal dependencies, it can be particularly useful for planning.Thanks to the various project views it offers, Asana is a useful option for video production management. You can easily see your pending tasks and projects on a calendar, which can help you gauge the way your complex video project is coming together.Pros+ An attractive UI+ Lots of project viewsCons– Limited exporting options– Complications during the learning processSPECIALIZED PROJECT MANAGEMENT SOFTWARE FOR VIDEO PRODUCTIONNow that we’ve taken a look at a few general project management tools, let’s examine software that’s specialized for the project management of video production .14. StudioBinderStudioBinder is web-based software for production management that can be used for video, TV, and film projects. This specialized tool helps video teams produce better content and work in harmony.Thanks to its range of customizable solutions, this tool is a good fit for video projects.. Using StudioBinder, project managers can create and share call sheets, script breakdowns, storyboards, and much more.Pros+ It’s easy to use.+ It has an attractive, clear layout.Cons– It lacks weekend support.– It’s difficult to track your team’s engagement.16. DramatifyDramatify is a mobile platform for production management that helps creative teams collaborate on a wide range of media, such as TV, film, scripted VR, and more. This tool offers a range of tools that make production smarter, faster, and more streamlined.Dramatify helps project managers complete complex tasks like team communication, cue card creation, screenplay sharing, script breakdown, and much more. This tool also includes cast scheduling and reports, in order to make logistics move more smoothly.Pros+ It has comprehensive offerings.+ It has robust features.Cons– It can be overwhelming.– Its design is somewhat dated.To take a closer look at more solutions for your corporate video projects, read this article: 20+ Video Production Management Software Solutions to Streamline Your Video Projects | The Project Success Blog
Why does it take forever to build a 40 km metro line in Bangalore?
A very short answer:The route alignment and TBMs (Tunnel Boring Machine) breakdown.Long answer:Let us begin with inspecting the network of Namma Metro (NM)/ Bengaluru Metro.The 42.3 km phase 1 consists of 2 routes, the Mysuru/Mysore Road-Baiyyappanahalli terminal East-West corridor (EW) corridor and Nagasandra-Puttenahalli North-South corridor(NS). (The northern and southern ends of this map are wrong. The route was extended beyond Peenya till Nagasandra in the north and beyond RV Road terminal till Puttenahalli in the south. This is an older map). The two routes intersect at Majestic/Kempegowda interchange.The parts in blue are elevated and the parts in red are underground. Observe that the underground portions are around the intersection at Majestic. This is a critical aspect which has lead to the delay. (Due to the clear distinction of elevated and underground portions, I'm illustrating using a slightly inaccurate map)In NS, underground part starts at Swastik (Mantri Mall) and ends at KR Road (near KIMS). The length is 4 km. In EW, underground part starts at Cricket stadium (between MG Road and Minsk Square stations) and ends slightly beyond City Railway station (at intersection of Magadi Road and Tank Bund Road). The length is 4.8 km.The depot for NS is situated at CMTI (Peenya, beside KSRTC satellite bus stand) and that for EW is at Baiyyappanahalli. A depot is compulsory for a route to be functional as it caters to regular operation and maintenance of the trains. The depot is along northern and eastern stretches of the network.The elevated part is constructed by joining viaduct to viaduct, as visible to all of us. The underground part is bored using TBM (Tunnel Boring Machine). The 5 TBMs being used drill 4+4.8 = 8.8 km of the 42.3 km network. There are two tunnels, one for 'up' and another for 'down'. So total distance is twice 8.8, that is 17.6 km. (The actual distance bored is less than 17.6 as the stations are constructed using cut and cover technology and those distances are not bored. I am not providing that split up in order to provide only those numbers that are crucial and preventing the answer from having too much data).The media reports that work on elevated stretch started in April 2007. Here are some dates as much important as April 2007.Work on eastern elevated stretch started in April 2007, northern elevated stretch in 2008, western and southern elevated stretches in 2009. (Only April 2007 is factual here. Others are a result of recollection from memory and might be wrong). The point is construction of all of them did not commence together. There is 1-2 years gap. In fact, the northern and southern extensions were approved in 2007, till which the above map was the proposed route.The elevated stretches are easier and faster to construct and underground stretches are more unpredictable and slower to construct. Since the depots are present in the northern and eastern reaches, those stretches were the first ones to begin with construction and operations have been started as and when the construction is finished. The eastern part was inaugurated on 20 October 2011 and northern part on 1 March 2014, with 2.5 km extension on 1 May 2015.Even though the western and southern elevated stretches could have been completed by 2013, they couldn't have been started as the small underground stretch was incomplete and the depots cannot be used to support the operation. Thus, the western and southern stretches are dependent on the underground portions to get access to depot. Since 2013, those two stretches have been proceeding very slowly. Even if they had proceeded quick they could not have started.Thus construction of all the stretches not commencing simultaneously and the underground portions not complete have caused delay.Why is the opening of underground section delayed?The tunneling works in EW started in July 2011 (note that MG Road- Baiyyappanahalli commenced in October 2011). Totally 3 TBMs were used to drill the underground portions of EW corridor. In March 2014, the 4.8 km EW underground work was completed. After the tunnel boring is complete, they have to clear the tunnel and prepare for the trains to roll.Below is a photo of the tunnel when TBMs have completed tunneling. (Source: The Hindu)Below is the photo of a completed tunnel in which trains can run. One difference, along with others, compared to previous photo is the concrete bed at the bottom. Source : BMRCL news letter shared on TMRG websiteOnce the tunnels were ready, the trains were pushed through the tunnels and the western stretch commenced operations in November 2015. As of now (7th February 2016), the elevated portions of EW are operating without underground section. The underground stations work are nearing completion and the complete 18.1 km is set to operate in few months time.The construction of Majestic interchange started in 2011 second half, few months after tunnel work in EW started.Now coming to the NS underground part.The following is the timeline. Source: Your gateway to the international tunnelling industry on the web (Kaveri, Krishna, Godavari and Margarita are the names of the TBMs)The TBMs started from South ramp in October and November 2012. From north ramp, it started in June 2013.Starting in June 2013, Godavari drilled 352 m by July 2014, out of the planned 970 m from North Ramp to Majestic. It had broken down and new cutter heads had to be installed for it to resume operation. Cutter heads are blades in front of the TBM that do the drilling. It resumed operations from July 2015, after 1 year of inactivity.For Krishna and Kaveri, South Ramp to City market station was a breeze. Kaveri suffered a minor glitch from City Market to Chickpet. But Krishna was affected by a major drawback. It also had to be fixed and it did not move an inch for an year. Thus it took 22 months for what should have been around 10 months. (The TBMs had to drill below Mysuru Road flyover and there they had to be slowed down).From Chickpet to Majestic, the TBMs are forced to go slow because of topography. The land above the tunnels have houses built in 1950s with very weak foundations. If the TBMs speed up, the houses will collapse. In fact, some houses have developed large cracks. So they have to strengthen each foundation and proceed. Also, BMRCL encountered open borewells. Though they had closed all registered borewells, the existence of the ones not registered were known only when the tunneling began. This again has hampered the progress. Though BMRCL knew the progress in this stretch would be slow, they are forced to go slower than they had planned to due to these setbacks.TBMs are like a mini factory. Whenever one part stops functioning, it causes a large amount of time delay. For Godavari, it took 1 year for new cutter heads to arrive because they had to be manufactured (in Italy) based on soil conditions they drill through and TBM configurations. It is not that one can go to a shop and buy spare parts. After manufacturing, they had to be shipped here which again took 1 to 1.5 months.Due to above reasons, more than 2 years was lost due to inactivity. The original plan was Godavari had to drill both tunnels from North Ramp to Majestic. Once the EW tunnels were complete, one of the TBMs, Margarita, was roped in to drill the other tunnel meant for Godavari. In EW, there were no periods of inactivity.Also, many experts have agreed Bengaluru underground portion is the toughest in the country to construct. The reason is varying types of soil condition. As tunnel progresses, the nature varies from hard rock to soft soil with varying extents of rock. If the soil condition remains as any one type throughout, tunneling will be quick. Once the nature changes, then tunneling has to be temporarily stalled, cutter heads changed (which again is a long process) and continued. This causes delay which cannot be avoided.Apart from these, delay in land acquisitions at North Ramp and Majestic also played a role. If there were no hassles there, then we might have been 1 year ahead. Still, the TBMs breakdown are the major cause of delay.As said before, underground stretch is unpredictable. They have the data as to what is expected next. But one should be prepared for unpleasant scenarios to prop up any time. Only once the tunneling is complete, one can heave a sigh. As given in the photo, still around 1300 m has to be drilled and we has to hope we don't see any more idle time. Three breakthroughs determine the eventual completion of phase 1.Once Kaveri and Godavari complete tunneling, other activities in the tunnel can be taken up to enable trains to be pushed along the tunnel to commence the start of the elevated southern stretch. The irony is the southern part has been the fastest to complete among the rest. Yet, it is forced to lay idle. The stations along the southern part are more than 90% complete. Yet, they might not see trains at least till June 2016. The opening of underground section of NS will be later than the elevated part, after Krishna breakthroughs at Majestic and tunnels are readied. That will mark the completion of phase 1.What could have been done to avoid these? Start the construction of underground portions simultaneously, if not before, with elevated stretch. The reason it was late was because tenders were called late. Underground being complex, various types of data have to be collected to estimate the types of machinery and process to be deployed. The pre-construction activities are more and time consuming compared to elevated. Thus elevated portions began early. The tenders for underground were floated by 2009-2010, 1 year before first deadline set in 2007. From then on, deadlines have been pushed each instance by 6 months only, giving everyone the impression it is simply getting delayed. Though underground portion is just 20.41% in terms of length, the amount of time and effort is way more than that. If not for the time period TBMs were idle (which is huge), the time taken is normal, neither slow nor fast.As stated above, only once the tunneling is complete, realistic dates can be estimated. Till then, the dates will be assumed to be the ones having highest probability of being realistic ones, with assumptions of TBMs having same speed as they are currently in.Below is the correct route map, with operational network as on 7th May 2016. Source: BMRCLEdit:On May 5th, an event was organized by BMRCL where few people who headed the project shared their experiences with public. Below is part of what they spoke. Source: They worked 60 feet under when city was fast asleepKris Reeves, project manager of CECSoma-CICI, the joint venture of three contractors that undertook the underground tunnelling work, said, “We had to face freaky operating conditions to tunnel through the challenging underbelly of Bengaluru. Deccan Plateau has some of the hardest rock formations in the world and this city has complex geological and hydrological conditions which we could not estimate even after soil tests. There was a challenge at every step. Perhaps for the first time we were tunnelling under a huge railway station but the soil underneath was soft.Here is an article from another newspaper which reports the average tunnelling they could achieveHe said it was difficult to dig even 18 metre a day while the same contractors were able to tunnel 33.6 metre a day in Delhi.The deadline for the project was set based on the Delhi model but Bengaluru's geology delayed opening of the underground section.
- Home >
- Catalog >
- Business >
- Project Template >
- Work Breakdown Structure Template >
- Article-International Project Work Breakdown